- Главная
- Статьи
- Сверление глубинных отверстий в металле: выбор свёрл и смазочно-охлаждающих жидкостей
Сверление глубинных отверстий в металле: выбор свёрл и смазочно-охлаждающих жидкостей
Создание глубоких отверстий в металлах требует не только точного выбора инструмента, но и тщательного подбора смазочно-охлаждающих жидкостей (СОЖ), которые обеспечивают стабильное качество обработки.
В металлургии и машиностроении важно понимать характеристики материала и физические условия, чтобы избежать дефектов и чрезмерного износа инструмента. При этом следует учитывать, что для глубоких отверстий (глубина которых превышает их диаметр более чем в 5 раз) требования к оборудованию и условиям охлаждения будут особенно высоки.
Существует несколько типов режущих инструментов для глубоких отверстий, которые можно применять в зависимости от условий и материала заготовки. Спиральные сверла используются чаще всего, когда необходимо обработать мягкие стали или легкие сплавы, так как они создают стабильный выход стружки, а острые углы режущей кромки обеспечивают ровное отверстие.
Рекомендуется выбирать инструмент с углом наклона режущей кромки в пределах 135-140 градусов для повышения точности и уменьшения нагрева. Однако при обработке твердосплавных и закаленных сталей такой инструмент может оказаться недостаточно прочным, и лучше применять более специализированные варианты, такие как пушечные сверла, которые имеют прямолинейные каналы для выведения стружки. У этих вариантов угол наклона обычно меньше – около 100-110 градусов, что уменьшает нагрузку на режущую часть и способствует экстракции стружки.
Пушечные сверла считаются наиболее эффективными для создания глубоких отверстий в твердых и хрупких материалах. Этот тип инструмента, который возник еще в XIX веке и изначально использовался в оружейной промышленности, отличается особой прочностью и способностью к устойчивому поддержанию направления при высокой глубине бурения.
Они обычно имеют меньший угол наклона режущей кромки и канал для подачи СОЖ под давлением, что снижает вероятность перегрева и уменьшает трение. Современные образцы пушечных сверл могут работать с подачей жидкости под давлением от 50 до 100 бар, что позволяет эффективно вымывать стружку из отверстия и предупреждать заедание.
Для создания глубоких отверстий в таких материалах, как высокопрочные стали или титановые сплавы, также используются многозубые сверла, где режущая поверхность разбита на несколько сегментов. Каждый сегмент удаляет небольшое количество материала, что уменьшает нагрузку на инструмент и снижает нагрев, делая многозубые сверла идеальными для твердых заготовок. Диаметр этих инструментов варьируется от 1,5 до 30 мм, а длина может достигать 600 мм, что позволяет работать с глубокими отверстиями без потери точности.
При выборе СОЖ для глубинной обработки важно учитывать состав и температуру заготовки, так как перегрев металла может привести к изменениям его структуры и быстрому износу инструмента. СОЖ должны иметь высокие показатели теплопроводности и смазывающей способности, чтобы обеспечить постоянное охлаждение и уменьшение трения между инструментом и заготовкой. Состав жидкости обычно включает масла и эмульсии на водной основе, в которые добавляют антикоррозионные присадки и стабилизаторы.
Применение синтетических СОЖ с высоким содержанием смазывающих компонентов, таких как полиэтиленгликоли или хлорированные парафины, позволяет снизить трение и уменьшить температуру в зоне обработки на 15-20%. Это особенно важно при глубинной обработке сталей, подверженных закалке, где перегрев может вызвать необратимые изменения структуры и привести к дефектам.
Не менее важна подача СОЖ. Давление жидкости должно поддерживаться на уровне не менее 20 бар для легких сплавов и не менее 50 бар для высокопрочных материалов. Система подачи жидкости может включать специальные каналы в инструменте или использовать внешние сопла, направленные прямо в зону контакта.
При использовании пушечных сверл подача СОЖ через внутренние каналы позволяет эффективно охлаждать рабочую область и предотвращает скопление стружки. Такие системы часто применяются на станках с ЧПУ, где управление подачей жидкости точно поддерживает температурный режим.
Важно учитывать и качество самой стружки, так как неправильный выбор инструмента или СОЖ может привести к ее скоплению и перегреву. Оптимальные размеры варьируются от 0,5 до 2 мм в зависимости от материала и типа инструмента. Слишком длинные элементы могут блокировать канал и создавать дополнительное давление, вызывая перегрев.
Для быстрого удаления стружки используются спиральные и внутренние каналы для подачи жидкости. При этом их диаметр должен составлять не менее 1,5 диаметра стружки, чтобы избежать заедания. В некоторых случаях применяются воздушные потоки для удаления стружки, однако такая техника эффективна только при малой глубине отверстий.
Для получения высокого качества обработки необходимо также соблюдать точные режимы подачи и скорости вращения. При глубинной обработке скорость вращения обычно снижается на 20-30% по сравнению со стандартными режимами, чтобы уменьшить нагрев и улучшить контроль над стружкой. Так, для высокопрочных сталей скорость не должна превышать 600-800 оборотов в минуту, а подача должна находиться в пределах 0,1-0,2 мм на оборот.
- На главную
-
Категории
-
Пластины твердосплавные
-
Пластины токарные
-
Пластины для внутреннего и наружного точения
-
Пластины резьбовые
-
Пластины резьбовые ISO
-
Пластины резьбовые трапецеидального профиля, угол 30 град.
-
Пластины резьбовые неполного профиля, угол 55 или 60 град.
-
Пластины резьбовые для нарезания трубной резьбы Whitworth, правые
-
Пластины резьбовые NPT (дюймовая коническая резьба c углом профиля 60 град. и конус 1:16)
-
Пластины резьбовые BSPT (Британский стандарт) полного профиля, угол 55 град.
-
Пластины резьбовые треугольного закругленного профиля
-
Пластины резьбовые UN (Американский стандарт) полного профиля, угол 60 град.
- Пластины резьбовые UN (Американский стандарт) полного профиля, угол 60 град.
- Панцирная трубная резьба Pg 80 град.
- Пластины резьбовые трапецеидального профиля, угол 30 град.
- Пластины резьбовые BSPT (Британский стандарт) полного профиля, угол 55 град.
- Пластины резьбовые NPT (дюймовая коническая резьба c углом профиля 60 град. и конус 1:16)
- Пластины резьбовые неполного профиля, угол 55 или 60 град.
- Упорная резьба SAGE 30 град.
-
-
Пластины отрезные и канавочные
-
TGF32
-
SP
-
MRMN
-
MG...N
- GER-C
- SP для стали
- SP для нержавеющей стали
-
QCMB
-
QPMB
- MGMN для стали
- MGMN для нержавеющей стали
- QPMB для стали
- QPMB для нержавеющей стали
- MRMN для стали
- ZP_S для нержавеющей стали
-
ZP_S
- QCMB для нержавеющей стали
- ZT_D для нержавеющей стали
-
ZT_D
- ZT_D для стали
- QCMB для стали
- TDC для нержавеющей стали
-
TDC
- QC_ для нержавеющей стали
-
QC
- QC_
- ZP_D для нержавеющей стали
-
ZP_D
- ZR_D для нержавеющей стали
-
ZR_D
- ZT_S для нержавеющей стали
-
ZT_S
- ZQMX для стали
-
ZQMX
- CTPA для нержавеющей стали
-
CTPA
- MGMN для чугуна
- MRMN для нержавеющей стали
- MRMN для чугуна
-
GEL-A/B
- GEL-A
-
GEL-A/B-R
-
GEL-C/D/E
- GEL-C
-
GEL-C/D/E-R
-
GER-A/B
- GER-A
-
GER-A/B-R
-
GER-C/D/E
-
GER-C/D/E-R
- MGMN
- MGGN
- MB
- ZTKS
- JRMN
- GK-R
- ZRFD
- KTMD
- KGT
- JSMN
- SPDR
-
-
-
Пластины фрезерные
-
Пластины для сверл
-
Лезвия для резьбофрез
-
Пластины со вставками PCBN
- Пластины для червячного зуба 40°
-
-
Фрезы
-
Фрезы монолитные
-
Концевые
-
HRC72
- HRC45
- HRC55
- HRC60
- HRC65
- HRC66
- HRC70
- HRC45
- HRC55
- HRC60
- HRC65
- HRC66
- HRC70
- HRC45
- HRC55
- HRC60
- HRC65
- HRC66
- HRC70
- HRC45
- HRC55
- HRC60
- HRC65
- HRC66
- HRC70
- HRC45
- HRC55
- HRC60
- HRC65
- HRC66
- HRC70
- HRC45
- HRC55
- HRC60
- HRC65
- HRC66
- HRC70
- HRC45
- HRC55
- HRC60
- HRC65
- HRC66
- HRC70
- HRC55
- HRC65
- HRC70
- HRC60
- HRC45
- HRC66
- HRC45
- HRC55
- HRC60
- HRC65
- HRC66
- HRC70
- HRC45
- HRC55
- HRC60
- HRC65
- HRC66
- HRC70
- HRC45
- HRC55
- HRC60
- HRC65
- HRC66
- HRC70
-
-
Радиусные
-
Сферические
-
Фасочные
-
Граверы
-
Дисковые
- Резьбофрезы
-
-
Фрезы со сменными пластинами
-
Фрезы дисковые
-
Фрезы концевые
-
ASM
-
BAP
- BMR
-
EMR
-
PE03
-
RB02
-
RB03
-
TEBL
-
ХК01
- ХК02
- SSM390
- EMP01
- AF06
- BAP
- EMR
- EMRW
- EXN03
- PE01
- PE02
- PE05
- R217.96
- RF01
- AF06
- BAP
- EMR
- EMRW
- EXN03
- PE01
- PE02
- PE05
- R217.96
- RF01
- AF06
- BAP
- EMR
- EMRW
- EXN03
- PE01
- PE02
- PE05
- R217.96
- RF01
- AF06
- BAP
- EMR
- EMRW
- EXN03
- PE01
- PE02
- PE05
- R217.96
- RF01
- AF06
- BAP
- EMR
- EMRW
- EXN03
- PE01
- PE02
- PE05
- R217.96
- RF01
- AF06
- BAP
- EMR
- EMRW
- EXN03
- PE01
- PE02
- PE05
- R217.96
- RF01
- AF06
- BAP
- EMR
- EMRW
- EXN03
- PE01
- PE02
- PE05
- R217.96
- RF01
- RF01
- EXN03
- PE02
- AF06
- R217.96
- EMRW
- EMR
- BAP
- PE01
- PE05
- AF06
- BAP
- EMR
- EMRW
- EXN03
- PE01
- PE02
- PE05
- R217.96
- RF01
- AF06
- BAP
- EMR
- EMRW
- EXN03
- PE01
- PE02
- PE05
- R217.96
- RF01
- AF06
- BAP
- EMR
- EMRW
- EXN03
- PE01
- PE02
- PE05
- R217.96
- RF01
-
-
Фрезы резьбонарезные
-
Фрезы торцевые насадные
-
Фрезы фасочные
-
-
Фрезы со сменными головками
-
-
Метчики
-
Сверла
-
Ленточные пилы
-
Новое поступление (NEW!)
-
Державки токарные
-
Державки расточные
-
S...-SVJCR/S...-SVJCL
-
S...-DCLNR/S...-DCLNL
-
S...-DDUNR/S...-DDUNL
-
S...-DWLNR/S...-DWLNL
-
S...-MCKNR/S...-MCKNL
-
S...-MCLNR/S...-MCLNL
-
S...-MDQNR/S...-MDQNL
-
S...-MDUNR/S...-MDUNL
-
S...-MSKNR/S-...MSKNL
-
S...-MTJNR/S...-MTJNL
-
S...-MTQNR/S...-MTQNL
-
S...-MTUNR/S...-MTUNL
-
S...-MTFNR/S...-MTFNL
-
S...-MTWNR/S...-MTWNL
-
S...-MVQNR/S-...MVQNL
-
S...-MVUNR/S-...MVUNL
-
S...-MVWNR/S...-MVWNL
-
S...-MVXNR/S...-MVXNL
-
S...-MWLNR/S...-MWLNL
-
S...-PCLNR/S...-PCLNL
-
S...-PDSNR/S...-PDSNL
-
S...-PDUNR/S...-PDUNL
-
S...-PSKNR/S...-PSKNL
-
S...-PWLNR/S...-PWLNL
-
S...-PTFNR/S...-PTFNL
-
S...-SCKCR/S...-SCKCL
-
S...-SCLCR/S...-SCLCL
-
S...-SCLPR/S...-SCLPL
-
S...-SDQCR/S...-SDQCL
-
S...-SDUCR/S...-SDUCL
-
S...-SDZCR/S...-SDZCL
-
S...-SSSCR/S...-SSSCL
-
S...-SSKCR/S...-SSKCL
-
S...-STFCR/S-...STFCL
-
S...-STUCR/S-...STUCL
-
S...-SVUCR/S-...SVUCL
-
S...-SVUBR/S...-SVUBL
-
-
Державки проходные
-
CCLNR/CCLNL
-
CRDNN
-
CSDNN
-
CSKNR/CSKNL
-
CTJNR/CTJNL
-
DCBNR/DCBNL
-
DCKNR/DCKNL
-
DCLNR/DCLNL
-
DCMNN
-
DDJNR/DDJNL
-
DDPNN
-
DSSNR/DSSNL
-
DDQNR/DDQNL
-
DSBNR/DSBNL
-
DSDNN
-
DSKNR/DSKNL
-
DTFNR/DTFNL
-
DTGNR/DTGNL
-
DVJNR/DVJNL
-
DVVNN
-
DWLNR/DWLNL
-
ECLNR/ECLNL
-
EDJNR/EDJNL
-
EVJNR/EVJNL
-
EWLNR/EWLNL
-
MCBNR/MCBNL
-
MCKNR/MCKNL
-
MCLNR/MCLNL
-
MCMNN
-
MDJNR/MDJNL
-
MDPNN
-
MDQNR/MDQNL
-
MRDNN
-
MRGNR/MRGNL
-
MSBNR/MSBNL
-
MSDNN
-
MSKNR/MSKNL
-
MSSNR/MSSNL
-
MTENN
-
MTFNR/MTFNL
-
MTGNR/MTGNL
-
MTJNR/MTJNL
-
MTQNR/MTQNL
-
MVJNR/MVJNL
-
MVQNR/MVQNL
-
MVUNR/MVUNL
-
MVVNN
-
MWLNR/MWLNL
-
PWLNR/PWLNL
-
PCLNR/PCLNL
-
PDJNR/PDJNL
-
PRACR/PRACL
-
PRDCN
-
PCBNR/PCBNL
-
PRGCR/PRGCL
-
PSBNR/PSBNL
-
PSDNN
-
PSSNR/PSSNL
-
PTGNR/PTGNL
-
PTTNR/PTTNL
-
SCLCR/SCLCL
-
SDJCR/SDJCL
-
SDNCN
-
SRACR/SRACL
-
SRDCN
-
SSDCN
-
SSSCR/SSSCL
-
STFCR/STFCL
-
SVACR/SVACL
-
SVJBR/SVJBL
-
SVJCR/SVJCL
-
SVVBN
-
SVVCN
-
WTENN
-
WTJNR/WTJNL
-
WWLNR/WWLNL
-
PDNNR/PDNNL
-
SVHBR/SVHBL
-
PDNNN
-
PTFNR/PTFNL
-
SCACR/SCACL
-
SDACR/SDACL
-
SSBCR/SSBCL
-
SRGCR/SRGCL
-
SSKCR/SSKCL
-
STGCR/STGCL
-
SVABR/SVABL
-
SVQCR/SVQCL
-
SWACR/SWACL
-
WTQNR/WTQNL
-
-
Державки резьбовые
-
Державки отрезные, канавочные
-
Держатели отрезного лезвия
-
Лезвия отрезные
-
Мини-резцы твердосплавные
-
-
Оснастка для фрезерных станков
-
Фрезерные патроны
-
BT
-
BT-ER (для цанг ER)
-
BT-FMB (для насадных фрез)
-
BT-SCA (для дисковых фрез)
-
BT-D (тестовые оправки)
-
BT-SLN Weldon
-
BT-MTA (конус Морзе с лапкой)
-
BT-MTB (конус Морзе с резьбовым отверстием)
-
BT-DC (высокоскоростные патроны для цанг DC)
-
BT-APU
-
BT-SC (для цилиндрических цанг SC)
-
BT-GT (для резьбовых цанг GT12/24/42)
-
BT-TER (патроны с осевой компенсацией по длине для цанг ER)
-
BT-OZ(EOC) (для силовых цанг OZ)
-
BT-PHC (гидропластовые патроны)
-
-
Конус Морзе MTA/MTB
-
HSK
-
Цилиндрический хвостовик
-
NT
-
SK
-
SK-FMB (для насадных фрез)
-
SK-SLN (Weldon)
-
SK-TER (патроны с осевой компенсацией по длине для цанг ER)
-
SK-SC (для цилиндрических цанг SC)
-
SK-MTB (конус Морзе с резьбовым отверстием)
-
SK-MTA (конус Морзе с лапкой)
-
SK-ER (для цанг ER)
-
SK-GT (для резьбовых цанг GT12/24/42)
-
SK-OZ(EOC) (для силовых цанг OZ)
-
SK-APU (сверлильные быстрозажимные патроны)
-
SK-PHC (гидропластовые патроны)
-
-
-
Прихваты, прижимы, упоры
-
Цанги
-
Штревели
-
3D тестеры
-
Тиски станочные
-
Аксессуары и запчасти
- Силовые высокоточные VQC
-
640 Multitasking
-
Трехкулачковые NBK
-
Гидравлические DCV
-
Модульные двойные ZQ83
-
С регулируемым усилием зажима HPAC
-
Самоцентрирующиеся SC-I
-
Модульные GT
-
Глобусные HHY
-
Лекальные QGG
-
Лекальные QKG
-
Модульные составные ZQ84
-
Гидравлические CHV
-
Самоцентрирующиеся двойные SMC
-
-
Кромкоискатели
-
Магнитные плиты
-
Центроискатели
-
Гайки для цанг
-
Ключи гаечные
-
Приспособления для оправок
-
Наборы прижимов
-
Расточные системы
-
Система нулевого базирования
-
Магнитные захваты
-
Поворотные столы
-
Аксессуары для станочной оснастки
-
Привязка по оси Z
-
Защитные вставки
-
-
Оснастка для токарных станков
-
Кулачки токарные
- Инструментальные блоки BOT
-
Токарные патроны
-
Центры токарные вращающиеся
- Центры вращающиеся
- Центры вращающиеся усиленные M11
- Центры вращающиеся облегченные
- Центры вращающиеся со сменными вставками
- Центры вращающиеся высокоскоростные
- Центры вращающиеся с твердосплавной вставкой
- Центры вращающиеся с удлиненной вершиной
- Центры вращающиеся усиленные
- Центры вращающиеся высокоточные
- Центры вращающиеся грибковые
-
Держатели осевого инструмента
-
Переходные втулки
-
Приспособления для расточки кулачков
-
Инструментальные блоки BMT
-
Центры токарные упорные
-
Сухари для токарных патронов
-
Инструментальные блоки VDI
-
Патроны цанговые
-
Цанги токарные
-
-
Измерительный инструмент
-
Станки
-
Станки ленточные по металлу
-
Лазерные граверы (маркировщики) по металлу
-
Токарные станки
-
Фрезерные станки
-
Заточные станки
-
Резьбонарезные манипуляторы
-
Электроэрозионные станки
-
Промышленные роботы
-
-
Мерч CNC66
-
Проволока, СОЖ, запчасти для электроэрозионных станков
-
Промышленная мебель
-
Запасные части для державок, резцов и фрез
-
Развертки
-
Упаковка
-
Зенковки
-
Плашки
-
Инструмент для снятия заусенцев
-
Корзина пуста
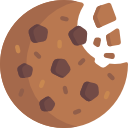
Мы используем файлы cookie для улучшения работы сайта и персонализации. Продолжая использовать сайт, вы соглашаетесь на сбор, обработку cookie-файлов и пользовательских данных с помощью Яндекс.Метрика, в соответствии с нашей Политикой конфиденциальности.