Зубофрезерование шестерен: выбор шага и углов для высокой точности
Зубофрезерование шестерен представляет собой процесс, требующий высокой точности и грамотного выбора параметров, таких как шаг зубьев и углы резания. Оптимальный подбор этих величин обеспечивает правильную передачу вращающего момента, уменьшает уровень шума и снижает износ механизмов. Для работы чаще всего применяют модульные фрезы, специально предназначенные для обработки профиля зуба, форма которого строго соответствует стандартам. Например, использование резцов по DIN 3972 или ISO 53 позволяет добиться высокой степени соответствия профиля шестерни нормативным требованиям.
Процесс начинается с анализа требований к конечной детали. Основным параметром, определяющим выбор шага, является модуль. Его рассчитывают по формуле, где модуль равен отношению диаметра делительного круга к числу зубьев. Для передачи с высоким КПД и минимальным уровнем вибрации выбирают модули от 1 до 6 мм, в зависимости от назначения. Например, шестерни для точных механизмов часто имеют модуль 1,25 или 1,5 мм, а для тяжелых приводов – от 4 до 6 мм. При этом важно учитывать материал заготовки. Чаще всего применяют углеродистые сплавы средней прочности, закаленные до твердости порядка 35–45 HRC. Для этих материалов фрезы из быстрорежущей стали или с твердосплавными напайками дают наиболее стабильный результат.
Угол наклона зуба зависит от типа передачи. Для прямозубых механизмов угол равен нулю, что упрощает изготовление, однако увеличивает вероятность возникновения ударных нагрузок. Для косозубых передач угол наклона обычно составляет от 15 до 25 градусов. Выбор конкретного значения зависит от требований к плавности работы и скорости вращения. Например, для высокоскоростных редукторов угол в 20 градусов позволяет добиться оптимального сочетания параметров. Важно учитывать, что при увеличении угла наклона возрастает сложность обработки, так как требуется соблюдать точность расположения резца относительно заготовки.
Выбор шага и углов фрезы влияет на установку станка. Настройка начинается с подбора зубофрезерного инструмента. Для стандартных передач применяют фрезы с прямыми зубьями, а для косозубых – с наклонными. Например, при модуле 2 мм и косом расположении зубьев угол наклона инструмента должен совпадать с углом зубьев заготовки. При настройке важно учитывать осевое смещение резца относительно центра заготовки. Даже минимальное отклонение приводит к увеличению вибраций и снижению точности передачи.
Важной составляющей процесса является подача и скорость вращения инструмента. Эти параметры выбирают в зависимости от материала заготовки и типа резца. Для заготовок из конструкционных сталей применяют скорости в пределах 60–80 м/мин, что соответствует частоте вращения фрезы от 100 до 200 об/мин при диаметре инструмента 100 мм. Подача на зуб обычно составляет 0,05–0,15 мм, что позволяет избежать перегрева инструмента и появления задиров на поверхности. Для твердых заготовок используют меньшую подачу, что обеспечивает стабильность обработки.
Контроль за качеством профиля осуществляется в процессе работы. При фрезеровании прямозубых передач измеряют шаг зубьев и радиальное биение. Допустимое отклонение по шагу для передач класса точности 6 составляет не более 0,01 мм на 100 мм длины окружности. Для косозубых передач дополнительно контролируют угол наклона зубьев, который не должен отклоняться от расчетного более чем на ±0,5 градуса. Например, при угле наклона 20 градусов допустимое отклонение составит 19,5–20,5 градусов.
Для повышения точности зубофрезерования применяют охлаждающую жидкость. Она снижает трение между резцом и заготовкой, предотвращает перегрев инструмента и улучшает качество поверхности. Наиболее распространены водосмешиваемые эмульсии с концентрацией масла 3–5%, которые эффективно охлаждают и смывают стружку. Для обработки твердосплавными фрезами используют более густые жидкости, обеспечивающие стабильное охлаждение даже при высоких скоростях.
Монтаж шестерен после фрезерования требует проверки посадочных размеров. Наиболее распространены валы с посадкой H7/h6 или H8/h7, что обеспечивает плотное соединение без люфтов. Контроль зазора между зубьями осуществляется с помощью щупов или индикаторов. Для передач класса точности 6 зазор должен составлять от 0,02 до 0,05 мм, при большем зазоре возможно появление вибраций, а меньший зазор приводит к повышенному износу. Для контроля за правильностью установки шестерен используют шаблоны или универсальные контрольно-измерительные приборы.
Финишная обработка включает удаление заусенцев и шлифовку боковых поверхностей зубьев. Для этого применяют абразивные круги с зернистостью от 60 до 120, что позволяет добиться шероховатости порядка Ra 0,8–1,2 мкм. Шлифовку проводят с минимальным давлением, чтобы избежать изменения геометрии зуба. После завершения обработки проверяют равномерность контакта зубьев, используя красящий состав. Правильное распределение пятна контакта вдоль всей длины зуба свидетельствует о высоком качестве передачи.
Использование зубофрезерных станков с ЧПУ позволяет значительно сократить время настройки и повысить точность обработки. Программы задаются на основе 3D-моделей, что исключает ошибки при расчете параметров. Современные станки способны автоматически подстраивать скорость и подачу в зависимости от нагрузки, что особенно важно при обработке твердых материалов. Для настройки таких систем важно правильно задавать координаты и параметры инструмента, чтобы избежать несоответствия с расчетным профилем.
При выборе фрезы особое внимание уделяют ее материалу. Для обработки мягких сплавов применяют инструменты из быстрорежущей стали, а для твердых – с твердосплавными пластинами. Например, фрезы из WC-Co обеспечивают стабильную работу при обработке заготовок твердостью до 55 HRC. Такие инструменты имеют повышенную стойкость к износу, что особенно важно при серийном производстве. Для увеличения срока службы фрез применяют покрытие PVD, которое снижает трение и защищает режущую кромку от перегрева.
При планировании зубофрезерования важно учитывать жесткость станка и системы крепления заготовки. Для снижения вибраций используют фиксирующие приспособления с гидравлическим или пневматическим зажимом. Это обеспечивает равномерное распределение усилия и предотвращает смещение заготовки во время обработки. Например, для заготовок диаметром до 200 мм применяют патроны с радиальным зажимом, а для более крупных деталей – специальные планшайбы.
Правильный выбор шага зубьев и углов фрезы позволяет добиться высокой точности передачи, что особенно важно для ответственных узлов. Соблюдение нормативных требований и рекомендаций по настройке оборудования гарантирует надежность работы механизмов даже в самых сложных условиях.
- На главную
-
Категории
-
Пластины
-
Пластины токарные
-
Пластины для внутреннего и наружного точения
-
Пластины резьбовые
-
Пластины резьбовые ISO
-
Пластины резьбовые трапецеидального профиля, угол 30 град.
-
Пластины резьбовые неполного профиля, угол 55 или 60 град.
-
Пластины резьбовые для нарезания трубной резьбы Whitworth, правые
-
Пластины резьбовые NPT (дюймовая коническая резьба c углом профиля 60 град. и конус 1:16)
-
Пластины резьбовые BSPT (Британский стандарт) полного профиля, угол 55 град.
-
Пластины резьбовые треугольного закругленного профиля
-
Пластины резьбовые UN (Американский стандарт) полного профиля, угол 60 град.
-
-
Пластины отрезные и канавочные
-
TGF32
-
SP
-
MRMN
-
MG...N
- GER-C
- SP для стали
- SP для нержавеющей стали
-
QCMB
-
QPMB
- MGMN для стали
- MGMN для нержавеющей стали
- QPMB для стали
- QPMB для нержавеющей стали
- MRMN для стали
- ZP_S для нержавеющей стали
-
ZP_S
- QCMB для нержавеющей стали
- ZT_D для нержавеющей стали
-
ZT_D
- ZT_D для стали
- QCMB для стали
- TDC для нержавеющей стали
-
TDC
- QC_ для нержавеющей стали
-
QC
- QC_
- ZP_D для нержавеющей стали
-
ZP_D
- ZR_D для нержавеющей стали
-
ZR_D
- ZT_S для нержавеющей стали
-
ZT_S
- ZQMX для стали
-
ZQMX
- CTPA для нержавеющей стали
-
CTPA
- MGMN для чугуна
- MRMN для нержавеющей стали
- MRMN для чугуна
-
GEL-A/B
- GEL-A
-
GEL-A/B-R
-
GEL-C/D/E
- GEL-C
-
GEL-C/D/E-R
-
GER-A/B
- GER-A
-
GER-A/B-R
-
GER-C/D/E
-
GER-C/D/E-R
-
-
-
Пластины фрезерные
-
Пластины для свёрл
-
Лезвия для резьбофрез
-
Пластины со вставками PCBN
-
-
Фрезы
-
Метчики
-
Сверла
-
Ленточные пилы
-
Новое поступление (NEW!)
-
Державки токарные
-
Державки расточные
-
S...-SVJCR/S...-SVJCL
-
S...-DCLNR/S...-DCLNL
-
S...-DDUNR/S...-DDUNL
-
S...-DWLNR/S...-DWLNL
-
S...-MCKNR/S...-MCKNL
-
S...-MCLNR/S...-MCLNL
-
S...-MDQNR/S...-MDQNL
-
S...-MDUNR/S...-MDUNL
-
S...-MSKNR/S-...MSKNL
-
S...-MTJNR/S...-MTJNL
-
S...-MTQNR/S...-MTQNL
-
S...-MTUNR/S...-MTUNL
-
S...-MTFNR/S...-MTFNL
-
S...-MTWNR/S...-MTWNL
-
S...-MVQNR/S-...MVQNL
-
S...-MVUNR/S-...MVUNL
-
S...-MVWNR/S...-MVWNL
-
S...-MVXNR/S...-MVXNL
-
S...-MWLNR/S...-MWLNL
-
S...-PCLNR/S...-PCLNL
-
S...-PDSNR/S...-PDSNL
-
S...-PDUNR/S...-PDUNL
-
S...-PSKNR/S...-PSKNL
-
S...-PWLNR/S...-PWLNL
-
S...-PTFNR/S...-PTFNL
-
S...-SCKCR/S...-SCKCL
-
S...-SCLCR/S...-SCLCL
-
S...-SCLPR/S...-SCLPL
-
S...-SDQCR/S...-SDQCL
-
S...-SDUCR/S...-SDUCL
-
S...-SDZCR/S...-SDZCL
-
S...-SSSCR/S...-SSSCL
-
S...-SSKCR/S...-SSKCL
-
S...-STFCR/S-...STFCL
-
S...-STUCR/S-...STUCL
-
S...-SVUCR/S-...SVUCL
-
S...-SVUBR/S...-SVUBL
-
-
Державки проходные
-
CCLNR/CCLNL
-
CRDNN
-
CSDNN
-
CSKNR/CSKNL
-
CTJNR/CTJNL
-
DCBNR/DCBNL
-
DCKNR/DCKNL
-
DCLNR/DCLNL
-
DCMNN
-
DDJNR/DDJNL
-
DDPNN
-
DSSNR/DSSNL
-
DDQNR/DDQNL
-
DSBNR/DSBNL
-
DSDNN
-
DSKNR/DSKNL
-
DTFNR/DTFNL
-
DTGNR/DTGNL
-
DVJNR/DVJNL
-
DVVNN
-
DWLNR/DWLNL
-
ECLNR/ECLNL
-
EDJNR/EDJNL
-
EVJNR/EVJNL
-
EWLNR/EWLNL
-
MCBNR/MCBNL
-
MCKNR/MCKNL
-
MCLNR/MCLNL
-
MCMNN
-
MDJNR/MDJNL
-
MDPNN
-
MDQNR/MDQNL
-
MRDNN
-
MRGNR/MRGNL
-
MSBNR/MSBNL
-
MSDNN
-
MSKNR/MSKNL
-
MSSNR/MSSNL
-
MTENN
-
MTFNR/MTFNL
-
MTGNR/MTGNL
-
MTJNR/MTJNL
-
MTQNR/MTQNL
-
MVJNR/MVJNL
-
MVQNR/MVQNL
-
MVUNR/MVUNL
-
MVVNN
-
MWLNR/MWLNL
-
PWLNR/PWLNL
-
PCLNR/PCLNL
-
PDJNR/PDJNL
-
PRACR/PRACL
-
PRDCN
-
PCBNR/PCBNL
-
PRGCR/PRGCL
-
PSBNR/PSBNL
-
PSDNN
-
PSSNR/PSSNL
-
PTGNR/PTGNL
-
PTTNR/PTTNL
-
SCLCR/SCLCL
-
SDJCR/SDJCL
-
SDNCN
-
SRACR/SRACL
-
SRDCN
-
SSDCN
-
SSSCR/SSSCL
-
STFCR/STFCL
-
SVACR/SVACL
-
SVJBR/SVJBL
-
SVJCR/SVJCL
-
SVVBN
-
SVVCN
-
WTENN
-
WTJNR/WTJNL
-
WWLNR/WWLNL
-
PDNNR/PDNNL
-
SVHBR/SVHBL
-
PDNNN
-
PTFNR/PTFNL
-
SCACR/SCACL
-
SDACR/SDACL
-
SSBCR/SSBCL
-
SRGCR/SRGCL
-
SSKCR/SSKCL
-
STGCR/STGCL
-
SVABR/SVABL
-
SVQCR/SVQCL
-
SWACR/SWACL
-
WTQNR/WTQNL
-
-
Державки резьбовые
-
Державки отрезные, канавочные
-
Держатели отрезного лезвия
-
Лезвия отрезные
-
Мини-резцы твердосплавные
-
-
Оснастка для фрезерных станков
-
Фрезерные патроны
-
BT
-
BT-ER (для цанг ER)
-
BT-FMB (для насадных фрез)
-
BT-SCA (для дисковых фрез)
-
BT-D (тестовые оправки)
-
BT-SLN Weldon
-
BT-MTA (конус Морзе с лапкой)
-
BT-MTB (конус Морзе с резьбовым отверстием)
-
BT-DC (высокоскоростные патроны для цанг DC)
-
BT-APU
-
BT-SC (для цилиндрических цанг SC)
-
BT-GT (для резьбовых цанг GT12/24/42)
-
BT-TER (патроны с осевой компенсацией по длине для цанг ER)
-
BT-OZ(EOC) (для силовых цанг OZ)
-
BT-PHC (гидропластовые патроны)
-
-
Конус Морзе MTA/MTB
-
HSK
-
Цилиндрический хвостовик
-
NT
-
SK
-
SK-FMB (для насадных фрез)
-
SK-SLN (Weldon)
-
SK-TER (патроны с осевой компенсацией по длине для цанг ER)
-
SK-SC (для цилиндрических цанг SC)
-
SK-MTB (конус Морзе с резьбовым отверстием)
-
SK-MTA (конус Морзе с лапкой)
-
SK-ER (для цанг ER)
-
SK-GT (для резьбовых цанг GT12/24/42)
-
SK-OZ(EOC) (для силовых цанг OZ)
-
SK-APU (сверлильные быстрозажимные патроны)
-
SK-PHC (гидропластовые патроны)
-
-
-
Прихваты, прижимы, упоры
-
Цанги
-
Штревели
-
3D тестеры
-
Тиски станочные
-
Аксессуары и запчасти
- Силовые высокоточные VQC
-
640 Multitasking
-
Трехкулачковые NBK
-
Гидравлические DCV
-
Модульные двойные ZQ83
-
С регулируемым усилием зажима HPAC
-
Самоцентрирующиеся SC-I
-
Модульные GT
-
Глобусные HHY
-
Лекальные QGG
-
Лекальные QKG
-
Модульные составные ZQ84
-
Гидравлические CHV
-
Самоцентрирующиеся двойные SMC
-
-
Кромкоискатели
-
Магнитные плиты
-
Центроискатели
-
Гайки для цанг
-
Ключи гаечные
-
Приспособления для оправок
-
Наборы прижимов
-
Расточные системы
-
Система нулевого базирования
-
Магнитные захваты
-
Поворотные столы
-
Аксессуары для станочной оснастки
-
Привязка по оси Z
-
-
Оснастка для токарных станков
-
Кулачки токарные
- Инструментальные блоки BOT
-
Токарные патроны
-
Центры токарные вращающиеся
- Центры вращающиеся
- Центры вращающиеся усиленные M11
- Центры вращающиеся облегченные
- Центры вращающиеся со сменными вставками
- Центры вращающиеся высокоскоростные
- Центры вращающиеся с твердосплавной вставкой
- Центры вращающиеся с удлиненной вершиной
- Центры вращающиеся усиленные
- Центры вращающиеся высокоточные
- Центры вращающиеся грибковые
-
Держатели осевого инструмента
-
Переходные втулки
-
Приспособления для расточки кулачков
-
Инструментальные блоки BMT
-
Центры токарные упорные
-
Сухари для токарных патронов
-
Инструментальные блоки VDI
-
Патроны цанговые
-
Цанги токарные
-
-
Измерительный инструмент
-
Станки
-
Станки ленточные по металлу
-
Лазерные граверы (маркировщики) по металлу
-
Токарные станки
-
Фрезерные станки
-
Заточные станки
-
Резьбонарезные манипуляторы
-
Электроэрозионные станки
-
Промышленные роботы
-
-
Мерч CNC66
-
Проволока, СОЖ, запчасти для электроэрозионных станков
-
Промышленная мебель
-
Запасные части для державок, резцов и фрез
-
Развертки
-
Упаковка
-
Зенковки
-
Плашки
-
Инструмент для снятия заусенцев
- выгрузка
-
Корзина пуста
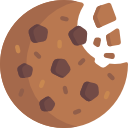
Мы используем файлы cookie для улучшения работы сайта и персонализации. Продолжая использовать сайт, вы соглашаетесь на сбор, обработку cookie-файлов и пользовательских данных с помощью Яндекс.Метрика, в соответствии с нашей Политикой конфиденциальности.