Закалка металла
Первые из дошедших до нас закаленных стальных предметов датируются началом I тысячелетия н.э. Но, по косвенным данным, можно предположить, что технология каления была известна намного ранее: на территории современной Португалии найдены отёсанные каменные столбы с гравировкой, датируемые 3800 г. до н.э. Провести такую работу незакаленным инструментом было попросту невозможно, из-за твёрдости камня долото приходилось бы затачивать через каждые несколько ударов.
Сами по себе изделия из металла мягки, плохо поддаются заточке материал как бы «плывёт» за абразивным инструментом. Поэтому неудивительно, что кузнецы, стремясь быстрее охладить деталь, погружали её в воду, после чего изделие приобретало улучшенные свойства. Отметим, что вплоть до Средневековья бытовало ошибочное представление, что прочность стали зависит от качества охлаждающей жидкости – использовали молоко, кровь, даже мочу. Хотя некоторый смысл в этом есть: в отличие от чистой воды, растворы менее теплопроводны, остывание происходит плавно, что сказывается на качестве металла. Известно, что дамасские мастера остужали клинки после закалки на северном ветру.
Что происходит с металлом при закалке
Закалка, как вид термической обработки, предполагает нагрев металла до определенной температуры (800-900оС) и последующего резкого охлаждения в воде, воздухе, масле, водяном тумане. При разогреве меняется тип кристаллической решетки, который не успевает вернуться к первоначальному из-за быстрой скорости остывания. Закалить можно только металлы с полиморфизмом, то есть такие, которые меняют кристаллическую структуру со сменой температуры.
После охлаждения в процессе закалки металл становится твёрже, особенно в наружном слое, но при этом увеличивается хрупкость. Чтобы сделать изделие менее хрупким, производится дополнительная термическая обработка.
Если температура при закалке была настолько высока, что произошло полное полиморфное превращение решетки, то выполняют отпуск. Изделие нагревают до средневысокой температуры (в зависимости от температуры плавления материала) до 150-650оС, и затем медленно остужают, зачастую вместе с печью.
При закалке с температурой ниже полиморфного превращения, достаточно просто дать металлу отлежаться. Такое старение в обычных условиях может затянуться на месяцы и годы, существенно сократить этот срок можно нагревом до 50-150оС.
Повышение прочности при закалке объясняется тем, что в массе железа формируются участки чрезвычайно твёрдого перенасыщенного углеродного раствора. Эти участки называются мартенситом, в честь описавшего их природу немецкого физика А.Мартенса.
Закалка также оптимизирует пластичность на изгиб, позволяет делать более лёгкие детали: ведь с повышением прочности требуется меньшая толщина изделий для достижения нужных параметров.
Закалённую сталь в обязательном порядке используют при изготовлении режущего инструмента: ножей, резцов, фрез. В промышленности широко используются высоконагруженные детали из закалённой стали, такие как подшипники, колёса, шестерни, втулки.
Металлы, которые можно закалить
Закалить можно не каждый материал, даже среди металлов и сплавов есть исключения. При этом, изменение свойств может быть как в сторону упрочнения, так и в сторону приобретения мягкости и пластичности.
Можно подвергать закалке:
Стали (углеродистые, легированные) с содержанием углерода не менее 0,4%. Именно из него образуется мартенсит, рассмотренный ранее. Закаливать сталь с меньшим содержанием углерода бессмысленно.
Чугуны, которые включают карбид, а также инструментальные марки.
Титан и сплавы на его основе. Будучи очень прочным и в обычном состоянии, титан улучшает свои характеристики при закалке, правда, для этого требуется точное соблюдение технологии.
Алюминиевые сплавы. Чистый алюминий не закаливают – он чересчур мягкий и пластичный даже в полиморфных состояниях, для образования легирующих компонентов нужны посторонние компоненты.
Нержавеющие стали требуют при закаливании более высоких температур и длительных сроков нагрева, так как содержат легирующие добавки, повышающие температуру плавления (многие из нержавсталей также огнеупорны). В зависимости от состава, некоторые сплавы могут становиться критически хрупкими, вплоть до саморазрушения.
Из цветных металлов можно закалить медь, латунь, бронзу. Но на практике это производится нечасто, из-за требований к точному (вплоть до 5оС) соблюдению температурного режима.
Способы закалки
При закалке в одной среде изделие после нагрева до нужного состояния помещается в воду (для высоколегированных сплавов – масло), где и остывает до комнатной температуры. При этом важно использовать подогретую до 60оС воду, так как иначе, при контакте с раскаленной заготовкой, образуется паровая рубашка, которая замедлит остывание. Минус способа – сохранение остаточных напряжений, необходимость дополнительного отпуска.
Ступенчатое закаливание требует больше времени, при этом заготовка погружается в масло с температурой выше формирования мартенсита на срок, достаточный для полного выравнивания температуры в толще металла. Затем производится постепенное охлаждение до обычной температуры.
Изотермическое закаливание предполагает очень плавное понижение температуры на протяжении всего процесса остывания. Цель – получение однородности металла, его меньшая хрупкость (отпуск после закалки не требуется).
Светлое закаливание производится в вакуумных печах (или в инертном газе: аргоне, азоте). Применяется для изделий, материал которых подвержен окислению, или же технические требования устанавливают лимит на содержание углерода в поверхностном слое.
Закаливание с самоотпуском – самый сложный процесс. Используется при изготовлении ударных инструментов, сочетающих твёрдость поверхности с внутренней пластичностью. Заключается способ в погружении разогретой детали на очень короткое время в охлаждающую среду, для формирования твёрдости внешнего слоя, и последующего медленного остывания, для придания мягкости основной толще металла.
- На главную
-
Категории
-
Пластины твердосплавные
-
Пластины токарные
-
Пластины для внутреннего и наружного точения
-
Пластины резьбовые
-
Пластины резьбовые ISO
-
Пластины резьбовые трапецеидального профиля, угол 30 град.
-
Пластины резьбовые неполного профиля, угол 55 или 60 град.
-
Пластины резьбовые для нарезания трубной резьбы Whitworth, правые
-
Пластины резьбовые NPT (дюймовая коническая резьба c углом профиля 60 град. и конус 1:16)
-
Пластины резьбовые BSPT (Британский стандарт) полного профиля, угол 55 град.
-
Пластины резьбовые треугольного закругленного профиля
-
Пластины резьбовые UN (Американский стандарт) полного профиля, угол 60 град.
- Пластины резьбовые UN (Американский стандарт) полного профиля, угол 60 град.
- Панцирная трубная резьба Pg 80 град.
- Пластины резьбовые трапецеидального профиля, угол 30 град.
- Пластины резьбовые BSPT (Британский стандарт) полного профиля, угол 55 град.
- Пластины резьбовые NPT (дюймовая коническая резьба c углом профиля 60 град. и конус 1:16)
- Пластины резьбовые неполного профиля, угол 55 или 60 град.
- Упорная резьба SAGE 30 град.
-
-
Пластины отрезные и канавочные
-
TGF32
-
SP
-
MRMN
-
MG...N
- GER-C
- SP для стали
- SP для нержавеющей стали
-
QCMB
-
QPMB
- MGMN для стали
- MGMN для нержавеющей стали
- QPMB для стали
- QPMB для нержавеющей стали
- MRMN для стали
- ZP_S для нержавеющей стали
-
ZP_S
- QCMB для нержавеющей стали
- ZT_D для нержавеющей стали
-
ZT_D
- ZT_D для стали
- QCMB для стали
- TDC для нержавеющей стали
-
TDC
- QC_ для нержавеющей стали
-
QC
- QC_
- ZP_D для нержавеющей стали
-
ZP_D
- ZR_D для нержавеющей стали
-
ZR_D
- ZT_S для нержавеющей стали
-
ZT_S
- ZQMX для стали
-
ZQMX
- CTPA для нержавеющей стали
-
CTPA
- MGMN для чугуна
- MRMN для нержавеющей стали
- MRMN для чугуна
-
GEL-A/B
- GEL-A
-
GEL-A/B-R
-
GEL-C/D/E
- GEL-C
-
GEL-C/D/E-R
-
GER-A/B
- GER-A
-
GER-A/B-R
-
GER-C/D/E
-
GER-C/D/E-R
- MGMN
- MGGN
- MB
- ZTKS
- JRMN
- GK-R
- ZRFD
- KTMD
- KGT
- JSMN
- SPDR
-
-
-
Пластины фрезерные
-
Пластины для сверл
-
Лезвия для резьбофрез
-
Пластины со вставками PCBN
- Пластины для червячного зуба 40°
-
-
Фрезы
-
Фрезы монолитные
-
Концевые
-
HRC72
- HRC45
- HRC55
- HRC60
- HRC65
- HRC66
- HRC70
- HRC45
- HRC55
- HRC60
- HRC65
- HRC66
- HRC70
- HRC45
- HRC55
- HRC60
- HRC65
- HRC66
- HRC70
- HRC45
- HRC55
- HRC60
- HRC65
- HRC66
- HRC70
- HRC45
- HRC55
- HRC60
- HRC65
- HRC66
- HRC70
- HRC45
- HRC55
- HRC60
- HRC65
- HRC66
- HRC70
- HRC45
- HRC55
- HRC60
- HRC65
- HRC66
- HRC70
- HRC55
- HRC65
- HRC70
- HRC60
- HRC45
- HRC66
- HRC45
- HRC55
- HRC60
- HRC65
- HRC66
- HRC70
- HRC45
- HRC55
- HRC60
- HRC65
- HRC66
- HRC70
- HRC45
- HRC55
- HRC60
- HRC65
- HRC66
- HRC70
- HRC45
- HRC55
- HRC60
- HRC65
- HRC66
- HRC70
-
-
Радиусные
-
Сферические
-
Фасочные
-
Граверы
-
Дисковые
- Резьбофрезы
-
-
Фрезы со сменными пластинами
-
Фрезы дисковые
-
Фрезы концевые
-
ASM
-
BAP
- BMR
-
EMR
-
PE03
-
RB02
-
RB03
-
TEBL
-
ХК01
- ХК02
- SSM390
- EMP01
- AF06
- BAP
- EMR
- EMRW
- EXN03
- PE01
- PE02
- PE05
- R217.96
- RF01
- AF06
- BAP
- EMR
- EMRW
- EXN03
- PE01
- PE02
- PE05
- R217.96
- RF01
- AF06
- BAP
- EMR
- EMRW
- EXN03
- PE01
- PE02
- PE05
- R217.96
- RF01
- AF06
- BAP
- EMR
- EMRW
- EXN03
- PE01
- PE02
- PE05
- R217.96
- RF01
- AF06
- BAP
- EMR
- EMRW
- EXN03
- PE01
- PE02
- PE05
- R217.96
- RF01
- AF06
- BAP
- EMR
- EMRW
- EXN03
- PE01
- PE02
- PE05
- R217.96
- RF01
- AF06
- BAP
- EMR
- EMRW
- EXN03
- PE01
- PE02
- PE05
- R217.96
- RF01
- RF01
- EXN03
- PE02
- AF06
- R217.96
- EMRW
- EMR
- BAP
- PE01
- PE05
- AF06
- BAP
- EMR
- EMRW
- EXN03
- PE01
- PE02
- PE05
- R217.96
- RF01
- AF06
- BAP
- EMR
- EMRW
- EXN03
- PE01
- PE02
- PE05
- R217.96
- RF01
- AF06
- BAP
- EMR
- EMRW
- EXN03
- PE01
- PE02
- PE05
- R217.96
- RF01
- AF06
- BAP
- EMR
- EMRW
- EXN03
- PE01
- PE02
- PE05
- R217.96
- RF01
-
-
Фрезы резьбонарезные
-
Фрезы торцевые насадные
-
Фрезы фасочные
-
-
Фрезы со сменными головками
-
-
Метчики
-
Сверла
-
Ленточные пилы
-
Новое поступление (NEW!)
-
Державки токарные
-
Державки расточные
-
S...-SVJCR/S...-SVJCL
-
S...-DCLNR/S...-DCLNL
-
S...-DDUNR/S...-DDUNL
-
S...-DWLNR/S...-DWLNL
-
S...-MCKNR/S...-MCKNL
-
S...-MCLNR/S...-MCLNL
-
S...-MDQNR/S...-MDQNL
-
S...-MDUNR/S...-MDUNL
-
S...-MSKNR/S-...MSKNL
-
S...-MTJNR/S...-MTJNL
-
S...-MTQNR/S...-MTQNL
-
S...-MTUNR/S...-MTUNL
-
S...-MTFNR/S...-MTFNL
-
S...-MTWNR/S...-MTWNL
-
S...-MVQNR/S-...MVQNL
-
S...-MVUNR/S-...MVUNL
-
S...-MVWNR/S...-MVWNL
-
S...-MVXNR/S...-MVXNL
-
S...-MWLNR/S...-MWLNL
-
S...-PCLNR/S...-PCLNL
-
S...-PDSNR/S...-PDSNL
-
S...-PDUNR/S...-PDUNL
-
S...-PSKNR/S...-PSKNL
-
S...-PWLNR/S...-PWLNL
-
S...-PTFNR/S...-PTFNL
-
S...-SCKCR/S...-SCKCL
-
S...-SCLCR/S...-SCLCL
-
S...-SCLPR/S...-SCLPL
-
S...-SDQCR/S...-SDQCL
-
S...-SDUCR/S...-SDUCL
-
S...-SDZCR/S...-SDZCL
-
S...-SSSCR/S...-SSSCL
-
S...-SSKCR/S...-SSKCL
-
S...-STFCR/S-...STFCL
-
S...-STUCR/S-...STUCL
-
S...-SVUCR/S-...SVUCL
-
S...-SVUBR/S...-SVUBL
-
-
Державки проходные
-
CCLNR/CCLNL
-
CRDNN
-
CSDNN
-
CSKNR/CSKNL
-
CTJNR/CTJNL
-
DCBNR/DCBNL
-
DCKNR/DCKNL
-
DCLNR/DCLNL
-
DCMNN
-
DDJNR/DDJNL
-
DDPNN
-
DSSNR/DSSNL
-
DDQNR/DDQNL
-
DSBNR/DSBNL
-
DSDNN
-
DSKNR/DSKNL
-
DTFNR/DTFNL
-
DTGNR/DTGNL
-
DVJNR/DVJNL
-
DVVNN
-
DWLNR/DWLNL
-
ECLNR/ECLNL
-
EDJNR/EDJNL
-
EVJNR/EVJNL
-
EWLNR/EWLNL
-
MCBNR/MCBNL
-
MCKNR/MCKNL
-
MCLNR/MCLNL
-
MCMNN
-
MDJNR/MDJNL
-
MDPNN
-
MDQNR/MDQNL
-
MRDNN
-
MRGNR/MRGNL
-
MSBNR/MSBNL
-
MSDNN
-
MSKNR/MSKNL
-
MSSNR/MSSNL
-
MTENN
-
MTFNR/MTFNL
-
MTGNR/MTGNL
-
MTJNR/MTJNL
-
MTQNR/MTQNL
-
MVJNR/MVJNL
-
MVQNR/MVQNL
-
MVUNR/MVUNL
-
MVVNN
-
MWLNR/MWLNL
-
PWLNR/PWLNL
-
PCLNR/PCLNL
-
PDJNR/PDJNL
-
PRACR/PRACL
-
PRDCN
-
PCBNR/PCBNL
-
PRGCR/PRGCL
-
PSBNR/PSBNL
-
PSDNN
-
PSSNR/PSSNL
-
PTGNR/PTGNL
-
PTTNR/PTTNL
-
SCLCR/SCLCL
-
SDJCR/SDJCL
-
SDNCN
-
SRACR/SRACL
-
SRDCN
-
SSDCN
-
SSSCR/SSSCL
-
STFCR/STFCL
-
SVACR/SVACL
-
SVJBR/SVJBL
-
SVJCR/SVJCL
-
SVVBN
-
SVVCN
-
WTENN
-
WTJNR/WTJNL
-
WWLNR/WWLNL
-
PDNNR/PDNNL
-
SVHBR/SVHBL
-
PDNNN
-
PTFNR/PTFNL
-
SCACR/SCACL
-
SDACR/SDACL
-
SSBCR/SSBCL
-
SRGCR/SRGCL
-
SSKCR/SSKCL
-
STGCR/STGCL
-
SVABR/SVABL
-
SVQCR/SVQCL
-
SWACR/SWACL
-
WTQNR/WTQNL
-
-
Державки резьбовые
-
Державки отрезные, канавочные
-
Держатели отрезного лезвия
-
Лезвия отрезные
-
Мини-резцы твердосплавные
-
-
Оснастка для фрезерных станков
-
Фрезерные патроны
-
BT
-
BT-ER (для цанг ER)
-
BT-FMB (для насадных фрез)
-
BT-SCA (для дисковых фрез)
-
BT-D (тестовые оправки)
-
BT-SLN Weldon
-
BT-MTA (конус Морзе с лапкой)
-
BT-MTB (конус Морзе с резьбовым отверстием)
-
BT-DC (высокоскоростные патроны для цанг DC)
-
BT-APU
-
BT-SC (для цилиндрических цанг SC)
-
BT-GT (для резьбовых цанг GT12/24/42)
-
BT-TER (патроны с осевой компенсацией по длине для цанг ER)
-
BT-OZ(EOC) (для силовых цанг OZ)
-
BT-PHC (гидропластовые патроны)
-
-
Конус Морзе MTA/MTB
-
HSK
-
Цилиндрический хвостовик
-
NT
-
SK
-
SK-FMB (для насадных фрез)
-
SK-SLN (Weldon)
-
SK-TER (патроны с осевой компенсацией по длине для цанг ER)
-
SK-SC (для цилиндрических цанг SC)
-
SK-MTB (конус Морзе с резьбовым отверстием)
-
SK-MTA (конус Морзе с лапкой)
-
SK-ER (для цанг ER)
-
SK-GT (для резьбовых цанг GT12/24/42)
-
SK-OZ(EOC) (для силовых цанг OZ)
-
SK-APU (сверлильные быстрозажимные патроны)
-
SK-PHC (гидропластовые патроны)
-
-
-
Прихваты, прижимы, упоры
-
Цанги
-
Штревели
-
3D тестеры
-
Тиски станочные
-
Аксессуары и запчасти
- Силовые высокоточные VQC
-
640 Multitasking
-
Трехкулачковые NBK
-
Гидравлические DCV
-
Модульные двойные ZQ83
-
С регулируемым усилием зажима HPAC
-
Самоцентрирующиеся SC-I
-
Модульные GT
-
Глобусные HHY
-
Лекальные QGG
-
Лекальные QKG
-
Модульные составные ZQ84
-
Гидравлические CHV
-
Самоцентрирующиеся двойные SMC
-
-
Кромкоискатели
-
Магнитные плиты
-
Центроискатели
-
Гайки для цанг
-
Ключи гаечные
-
Приспособления для оправок
-
Наборы прижимов
-
Расточные системы
-
Система нулевого базирования
-
Магнитные захваты
-
Поворотные столы
-
Аксессуары для станочной оснастки
-
Привязка по оси Z
-
Защитные вставки
-
-
Оснастка для токарных станков
-
Кулачки токарные
- Инструментальные блоки BOT
-
Токарные патроны
-
Центры токарные вращающиеся
- Центры вращающиеся
- Центры вращающиеся усиленные M11
- Центры вращающиеся облегченные
- Центры вращающиеся со сменными вставками
- Центры вращающиеся высокоскоростные
- Центры вращающиеся с твердосплавной вставкой
- Центры вращающиеся с удлиненной вершиной
- Центры вращающиеся усиленные
- Центры вращающиеся высокоточные
- Центры вращающиеся грибковые
-
Держатели осевого инструмента
-
Переходные втулки
-
Приспособления для расточки кулачков
-
Инструментальные блоки BMT
-
Центры токарные упорные
-
Сухари для токарных патронов
-
Инструментальные блоки VDI
-
Патроны цанговые
-
Цанги токарные
-
-
Измерительный инструмент
-
Станки
-
Станки ленточные по металлу
-
Лазерные граверы (маркировщики) по металлу
-
Токарные станки
-
Фрезерные станки
-
Заточные станки
-
Резьбонарезные манипуляторы
-
Электроэрозионные станки
-
Промышленные роботы
-
-
Мерч CNC66
-
Проволока, СОЖ, запчасти для электроэрозионных станков
-
Промышленная мебель
-
Запасные части для державок, резцов и фрез
-
Развертки
-
Упаковка
-
Зенковки
-
Плашки
-
Инструмент для снятия заусенцев
-
Корзина пуста
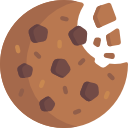
Мы используем файлы cookie для улучшения работы сайта и персонализации. Продолжая использовать сайт, вы соглашаетесь на сбор, обработку cookie-файлов и пользовательских данных с помощью Яндекс.Метрика, в соответствии с нашей Политикой конфиденциальности.