Стальные канаты и тросы: разновидности и технология производства
Стальной канат был запатентован в Германии в 1827 году инженером В.Альбертом. Первые канаты, за неимением специальных станков, сплетались вручную, что накладывало ограничения на количество и толщину жил – таким способом удавалось сплести канат из 12 проволок сечением по 3,5 мм каждая. Несмотря на это, полученные канаты намного превосходили по прочности и надежности существующие аналоги.
Спрос на проволочные канаты привел к появлению специальной производственной техники, в Словении в 1840 году запустили первую линию автоматического витья проволоки. Применение паровых двигателей позволило использовать все большее количество проволочных прядей из проволоки высокой прочности. В это время в Европе произошел всплеск популярности подвесных фуникулёров, применявшихся как в горнолыжном туризме, так и в качестве общественного транспорта в гористой местности. В основе доступности, надёжности и простоты реализации «подвесных дорог» лежало, конечно же, развитие технологии производства стальных канатов.
В 1870 году производители отказались от проволоки, перейдя на использование литой стали. Именно тогда появилось понятие «стальной канат», само изделие перешло из разряда такелажа в разряд несущих конструкций в строительстве. Стальные канаты, особенно в США, активно применялись (и применяются по сей день) для установки подвесных мостов. Трос для подвеса моста, состоящий более чем из семнадцати тысяч свитых проволок диаметром 0,3 мм каждая, может выдерживать около 95 тысяч тонн. При этом сталь, при надлежащем изготовлении и антикоррозионной обработке, может служить до сотни лет.
Этапы производства стальных тросов и канатов
Материалом для изготовления металлических тросов и канатов является проволока из высокоуглеродистых сортов нержавеющей стали. Сорт и марка стали влияют на самую главную характеристику каната – диапазон растяжения. Стандартом являются границы в 1570 – 2160 Н/мм2.
Проволока на производство поставляется в виде бухт весом до 2 тонн каждая. Диаметр проволоки-материала – от 0,6 до 8 мм. Проволока проходит предварительную обработку в ванне с соляной кислотой, для некоторой закалки и удаления посторонних фрагментов. После ополаскивания проволоку укрепляют волочением, то есть пропускают через ряд конусообразных отверстий, каждое из которых становится меньше в диаметре, проволока при этом спрессовывается, уменьшая диаметр на 30-200%.
Финальным этапом подготовки проволоки является горячее цинкование, для чего ее погружают в ванну с горячим, около 450оС, расплавом цинка. Цинковое покрытие защищает сталь от коррозии, механических повреждений, делая поверхность более гладкой, что снижает трение (и образование потертостей) между прядями каната. Кроме того, цинк инертен к большинству слабых электролитов, поэтому оцинкованная проволока не деградирует при контакте с подобными средами.
Далее формируют пряди, путём завивки (скрутки) нескольких проволок-нитей между собой в скруточном аппарате. В сильно нагруженных канатах, например, используемых в конструкции подвесных мостов, количество нитей в пряди достигает 60. На практике используются меньшие значения – от 19 до 30 нитей. Полученные пряди пропускаются через протяжно кольцо, где происходит нормализация степени скручивания, при этом прядь обильно смазывается, что способствует подвижности проволок внутри пучка, повышая его эластичность. Лишняя смазка затем снимается резиновыми валками. Последующий прогон прядей между роликами большого диаметра убирает внутренние напряжения, в то же время спрессовывая и закрепляя пучок, во избежание его раскручивания.
Для получения тросов и канатов пряди подаются в канатовьющую машину. Здесь пучки приобретают форму спирали, навиваясь на центральный такой же пучок – жилу, или на органический или металлический сердечник. В первом случае канат будет более гибким, во втором – более стойким на растяжение.
В зависимости от условий эксплуатации, канат может иметь защитную оболочку из двухслойного пластика. Полимер нагревают в экструдере и выдавливают на трос, пропускаемый через протяжное устройство. Чтобы пластик не успевал стечь с каната, его сразу же охлаждают в воде.
Виды канатов
Пряди являются тросами одинарной свивки, то есть состоящими из 1-3 слоев витой проволоки. Если при этом использовалась только круглая проволока, такие канаты называются обыкновенными. Иногда наружный слой проволоки имеет разную геометрию сечения (закрытая конструкция) для того, чтобы в случае обрыва внешние проволоки удерживались в составе каната соседними, не допуская его «разлохмачивания».
Канаты двойной свивки (стренги) включают в себя шесть и больше прядей, свитых в концентрический слой. Такие изделия, при противоположном направлении скрутки прядей, не только значительно прочнее того же количества прядей, но еще и менее склонны к закручиванию. Самые популярные канаты – именно шестипрядные, они используются как тросы подъёмных кранов, такелаж при строительстве, в горнодобывающей промышленности.
Для более нагруженных условий эксплуатации выпускают канаты тройной свивки, они точно также скручиваются из стренгов, причем диаметр и количество проволок во внешнем слое стренгов зачастую применяют больший, чем во внутренних слоях.
Способы свивки прядей и стренгов между собой позволяют добиться разных типов их касания между собой, что придает канату различные свойства. Различают:
Канаты с точечным касанием (тип ТК). Пряди изготавливаются за несколько приёмов, ха каждый проход свивается один слой с определенным шагом, меняющимся от слоя к слою; кроме того, слои навиваются под углом друг к другу. Это придает канату большую гибкость, однако повышает его изнашиваемость из-за внутренних контактных напряжений и подвижности слоев, приводит к увеличению толщины каната.
Пряди с линейным касанием (тип ЛК) имеют постоянный шаг скрутки во всех слоях, и изготавливаются за один приём. А вот диаметр проволок может быть различным – если наружные выполнены из проволоки большего диаметра, то они маркируются как ЛК-Р, в противном случае – ЛК-0. Если проволоки разного диаметра чередуются внутри слоев одной пряди, говорят о смешанном типе – ЛК-Р0. Канаты с линейным касанием значительно долговечнее, но из-за меньшей гибкости используются для удержания статичных нагрузок, редко применяясь, скажем для организации канатных дорог, подъёма клетей и вагонеток, строительных материалов и пр.
Пряди точечно-линейного касания (ТЛК-О) имеют повышенные некрутящиеся свойства и подходят для использования в конструкциях лебедок, талей, подъёмных кранов – там, где канат может висеть без нагрузки, и при её приложении не должен придавать вращение поднимаемому грузу. Канаты ТЛК-О получаются по той же технологии, что и ЛК, но центральная проволока в них заменена семипроволочной прядью с точечным касанием, которая и препятствует самодеформации изделия.
- На главную
-
Категории
-
Пластины твердосплавные
-
Пластины токарные
-
Пластины для внутреннего и наружного точения
-
Пластины резьбовые
-
Пластины резьбовые ISO
-
Пластины резьбовые трапецеидального профиля, угол 30 град.
-
Пластины резьбовые неполного профиля, угол 55 или 60 град.
-
Пластины резьбовые для нарезания трубной резьбы Whitworth, правые
-
Пластины резьбовые NPT (дюймовая коническая резьба c углом профиля 60 град. и конус 1:16)
-
Пластины резьбовые BSPT (Британский стандарт) полного профиля, угол 55 град.
-
Пластины резьбовые треугольного закругленного профиля
-
Пластины резьбовые UN (Американский стандарт) полного профиля, угол 60 град.
- Пластины резьбовые UN (Американский стандарт) полного профиля, угол 60 град.
- Панцирная трубная резьба Pg 80 град.
- Пластины резьбовые трапецеидального профиля, угол 30 град.
- Пластины резьбовые BSPT (Британский стандарт) полного профиля, угол 55 град.
- Пластины резьбовые NPT (дюймовая коническая резьба c углом профиля 60 град. и конус 1:16)
- Пластины резьбовые неполного профиля, угол 55 или 60 град.
- Упорная резьба SAGE 30 град.
-
-
Пластины отрезные и канавочные
-
TGF32
-
SP
-
MRMN
-
MG...N
- GER-C
- SP для стали
- SP для нержавеющей стали
-
QCMB
-
QPMB
- MGMN для стали
- MGMN для нержавеющей стали
- QPMB для стали
- QPMB для нержавеющей стали
- MRMN для стали
- ZP_S для нержавеющей стали
-
ZP_S
- QCMB для нержавеющей стали
- ZT_D для нержавеющей стали
-
ZT_D
- ZT_D для стали
- QCMB для стали
- TDC для нержавеющей стали
-
TDC
- QC_ для нержавеющей стали
-
QC
- QC_
- ZP_D для нержавеющей стали
-
ZP_D
- ZR_D для нержавеющей стали
-
ZR_D
- ZT_S для нержавеющей стали
-
ZT_S
- ZQMX для стали
-
ZQMX
- CTPA для нержавеющей стали
-
CTPA
- MGMN для чугуна
- MRMN для нержавеющей стали
- MRMN для чугуна
-
GEL-A/B
- GEL-A
-
GEL-A/B-R
-
GEL-C/D/E
- GEL-C
-
GEL-C/D/E-R
-
GER-A/B
- GER-A
-
GER-A/B-R
-
GER-C/D/E
-
GER-C/D/E-R
- MGMN
- MGGN
- MB
- ZTKS
- JRMN
- GK-R
- ZRFD
- KTMD
- KGT
- JSMN
- SPDR
-
-
-
Пластины фрезерные
-
Пластины для сверл
-
Лезвия для резьбофрез
-
Пластины со вставками PCBN
- Пластины для червячного зуба 40°
-
-
Фрезы
-
Метчики
-
Сверла
-
Ленточные пилы
-
Новое поступление (NEW!)
-
Державки токарные
-
Державки расточные
-
S...-SVJCR/S...-SVJCL
-
S...-DCLNR/S...-DCLNL
-
S...-DDUNR/S...-DDUNL
-
S...-DWLNR/S...-DWLNL
-
S...-MCKNR/S...-MCKNL
-
S...-MCLNR/S...-MCLNL
-
S...-MDQNR/S...-MDQNL
-
S...-MDUNR/S...-MDUNL
-
S...-MSKNR/S-...MSKNL
-
S...-MTJNR/S...-MTJNL
-
S...-MTQNR/S...-MTQNL
-
S...-MTUNR/S...-MTUNL
-
S...-MTFNR/S...-MTFNL
-
S...-MTWNR/S...-MTWNL
-
S...-MVQNR/S-...MVQNL
-
S...-MVUNR/S-...MVUNL
-
S...-MVWNR/S...-MVWNL
-
S...-MVXNR/S...-MVXNL
-
S...-MWLNR/S...-MWLNL
-
S...-PCLNR/S...-PCLNL
-
S...-PDSNR/S...-PDSNL
-
S...-PDUNR/S...-PDUNL
-
S...-PSKNR/S...-PSKNL
-
S...-PWLNR/S...-PWLNL
-
S...-PTFNR/S...-PTFNL
-
S...-SCKCR/S...-SCKCL
-
S...-SCLCR/S...-SCLCL
-
S...-SCLPR/S...-SCLPL
-
S...-SDQCR/S...-SDQCL
-
S...-SDUCR/S...-SDUCL
-
S...-SDZCR/S...-SDZCL
-
S...-SSSCR/S...-SSSCL
-
S...-SSKCR/S...-SSKCL
-
S...-STFCR/S-...STFCL
-
S...-STUCR/S-...STUCL
-
S...-SVUCR/S-...SVUCL
-
S...-SVUBR/S...-SVUBL
-
-
Державки проходные
-
CCLNR/CCLNL
-
CRDNN
-
CSDNN
-
CSKNR/CSKNL
-
CTJNR/CTJNL
-
DCBNR/DCBNL
-
DCKNR/DCKNL
-
DCLNR/DCLNL
-
DCMNN
-
DDJNR/DDJNL
-
DDPNN
-
DSSNR/DSSNL
-
DDQNR/DDQNL
-
DSBNR/DSBNL
-
DSDNN
-
DSKNR/DSKNL
-
DTFNR/DTFNL
-
DTGNR/DTGNL
-
DVJNR/DVJNL
-
DVVNN
-
DWLNR/DWLNL
-
ECLNR/ECLNL
-
EDJNR/EDJNL
-
EVJNR/EVJNL
-
EWLNR/EWLNL
-
MCBNR/MCBNL
-
MCKNR/MCKNL
-
MCLNR/MCLNL
-
MCMNN
-
MDJNR/MDJNL
-
MDPNN
-
MDQNR/MDQNL
-
MRDNN
-
MRGNR/MRGNL
-
MSBNR/MSBNL
-
MSDNN
-
MSKNR/MSKNL
-
MSSNR/MSSNL
-
MTENN
-
MTFNR/MTFNL
-
MTGNR/MTGNL
-
MTJNR/MTJNL
-
MTQNR/MTQNL
-
MVJNR/MVJNL
-
MVQNR/MVQNL
-
MVUNR/MVUNL
-
MVVNN
-
MWLNR/MWLNL
-
PWLNR/PWLNL
-
PCLNR/PCLNL
-
PDJNR/PDJNL
-
PRACR/PRACL
-
PRDCN
-
PCBNR/PCBNL
-
PRGCR/PRGCL
-
PSBNR/PSBNL
-
PSDNN
-
PSSNR/PSSNL
-
PTGNR/PTGNL
-
PTTNR/PTTNL
-
SCLCR/SCLCL
-
SDJCR/SDJCL
-
SDNCN
-
SRACR/SRACL
-
SRDCN
-
SSDCN
-
SSSCR/SSSCL
-
STFCR/STFCL
-
SVACR/SVACL
-
SVJBR/SVJBL
-
SVJCR/SVJCL
-
SVVBN
-
SVVCN
-
WTENN
-
WTJNR/WTJNL
-
WWLNR/WWLNL
-
PDNNR/PDNNL
-
SVHBR/SVHBL
-
PDNNN
-
PTFNR/PTFNL
-
SCACR/SCACL
-
SDACR/SDACL
-
SSBCR/SSBCL
-
SRGCR/SRGCL
-
SSKCR/SSKCL
-
STGCR/STGCL
-
SVABR/SVABL
-
SVQCR/SVQCL
-
SWACR/SWACL
-
WTQNR/WTQNL
-
-
Державки резьбовые
-
Державки отрезные, канавочные
-
Держатели отрезного лезвия
-
Лезвия отрезные
-
Мини-резцы твердосплавные
-
-
Оснастка для фрезерных станков
-
Фрезерные патроны
-
BT
-
BT-ER (для цанг ER)
-
BT-FMB (для насадных фрез)
-
BT-SCA (для дисковых фрез)
-
BT-D (тестовые оправки)
-
BT-SLN Weldon
-
BT-MTA (конус Морзе с лапкой)
-
BT-MTB (конус Морзе с резьбовым отверстием)
-
BT-DC (высокоскоростные патроны для цанг DC)
-
BT-APU
-
BT-SC (для цилиндрических цанг SC)
-
BT-GT (для резьбовых цанг GT12/24/42)
-
BT-TER (патроны с осевой компенсацией по длине для цанг ER)
-
BT-OZ(EOC) (для силовых цанг OZ)
-
BT-PHC (гидропластовые патроны)
-
-
Конус Морзе MTA/MTB
-
HSK
-
Цилиндрический хвостовик
-
NT
-
SK
-
SK-FMB (для насадных фрез)
-
SK-SLN (Weldon)
-
SK-TER (патроны с осевой компенсацией по длине для цанг ER)
-
SK-SC (для цилиндрических цанг SC)
-
SK-MTB (конус Морзе с резьбовым отверстием)
-
SK-MTA (конус Морзе с лапкой)
-
SK-ER (для цанг ER)
-
SK-GT (для резьбовых цанг GT12/24/42)
-
SK-OZ(EOC) (для силовых цанг OZ)
-
SK-APU (сверлильные быстрозажимные патроны)
-
SK-PHC (гидропластовые патроны)
-
-
-
Прихваты, прижимы, упоры
-
Цанги
-
Штревели
-
3D тестеры
-
Тиски станочные
-
Аксессуары и запчасти
- Силовые высокоточные VQC
-
640 Multitasking
-
Трехкулачковые NBK
-
Гидравлические DCV
-
Модульные двойные ZQ83
-
С регулируемым усилием зажима HPAC
-
Самоцентрирующиеся SC-I
-
Модульные GT
-
Глобусные HHY
-
Лекальные QGG
-
Лекальные QKG
-
Модульные составные ZQ84
-
Гидравлические CHV
-
Самоцентрирующиеся двойные SMC
-
-
Кромкоискатели
-
Магнитные плиты
-
Центроискатели
-
Гайки для цанг
-
Ключи гаечные
-
Приспособления для оправок
-
Наборы прижимов
-
Расточные системы
-
Система нулевого базирования
-
Магнитные захваты
-
Поворотные столы
-
Аксессуары для станочной оснастки
-
Привязка по оси Z
-
Защитные вставки
-
-
Оснастка для токарных станков
-
Кулачки токарные
- Инструментальные блоки BOT
-
Токарные патроны
-
Центры токарные вращающиеся
- Центры вращающиеся
- Центры вращающиеся усиленные M11
- Центры вращающиеся облегченные
- Центры вращающиеся со сменными вставками
- Центры вращающиеся высокоскоростные
- Центры вращающиеся с твердосплавной вставкой
- Центры вращающиеся с удлиненной вершиной
- Центры вращающиеся усиленные
- Центры вращающиеся высокоточные
- Центры вращающиеся грибковые
-
Держатели осевого инструмента
-
Переходные втулки
-
Приспособления для расточки кулачков
-
Инструментальные блоки BMT
-
Центры токарные упорные
-
Сухари для токарных патронов
-
Инструментальные блоки VDI
-
Патроны цанговые
-
Цанги токарные
-
-
Измерительный инструмент
-
Станки
-
Станки ленточные по металлу
-
Лазерные граверы (маркировщики) по металлу
-
Токарные станки
-
Фрезерные станки
-
Заточные станки
-
Резьбонарезные манипуляторы
-
Электроэрозионные станки
-
Промышленные роботы
-
-
Мерч CNC66
-
Проволока, СОЖ, запчасти для электроэрозионных станков
-
Промышленная мебель
-
Запасные части для державок, резцов и фрез
-
Развертки
-
Упаковка
-
Зенковки
-
Плашки
-
Инструмент для снятия заусенцев
-
Корзина пуста
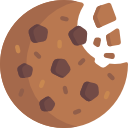
Мы используем файлы cookie для улучшения работы сайта и персонализации. Продолжая использовать сайт, вы соглашаетесь на сбор, обработку cookie-файлов и пользовательских данных с помощью Яндекс.Метрика, в соответствии с нашей Политикой конфиденциальности.