Соединение металлов методом электроконтактного спекания
Электроконтактное спекание объединяет принципы порошковой металлургии и электросварки. Истоки этой технологии уходят корнями в начало 20 века, когда ученые начали экспериментировать с использованием электрического тока для спекания металлических порошков.
Первые серьезные исследования в этой области были проведены в 1930-х годах советским ученым Г.А. Меерсоном, который заложил теоретические основы процесса.
В 1960-х годах японский ученый Кийоши Иноуэ разработал и запатентовал технологию искрового плазменного спекания (SPS). Эта технология стала основой для современных методов электроконтактного спекания.
Иноуэ обнаружил, что пропускание импульсного электрического тока через металлический порошок позволяет достичь очень быстрого и равномерного нагрева, что значительно улучшает качество спекания.
Как происходит контактное спекание
В процессе электроконтактного спекания металлический порошок или заготовки помещаются между двумя электродами в специальной пресс-форме. Через систему пропускается электрический ток высокой плотности, который вызывает локальный нагрев в точках контакта между частицами порошка.
Одновременно к заготовке прикладывается механическое давление. Комбинация высокой температуры и давления приводит к быстрому формированию прочных межчастичных связей и уплотнению материала.
Физические принципы, лежащие в основе электроконтактного спекания, включают в себя джоулев нагрев, электромиграцию и эффект электропластичности. Джоулев нагрев возникает при прохождении электрического тока через материал с электрическим сопротивлением.
Электромиграция способствует переносу атомов под действием электрического поля, что ускоряет диффузионные процессы. Эффект электропластичности заключается в повышении пластичности металла под воздействием электрического тока, что облегчает деформацию частиц и их сближение.
Оборудование для электроконтактного спекания обычно состоит из мощного источника тока, гидравлического пресса, системы охлаждения и вакуумной камеры. Ключевыми компонентами являются электроды, которые должны обладать высокой электро- и теплопроводностью, а также устойчивостью к высоким температурам. Часто используются графитовые или медные электроды с вольфрамовыми наконечниками.
Ключевыми факторами процесса являются сила тока, напряжение, длительность импульсов, давление прессования и скорость нагрева.
Для каждого материала и типа изделия существуют оптимальные режимы спекания, которые определяются экспериментально. Например, для спекания нанопорошка алюминия типичные параметры могут включать ток 1000-1500 А, напряжение 3-5 В, давление 50-100 МПа и время спекания 1-3 минуты.
Сфера применения электроконтактного спекания
Метод электроконтактного спекания позволяет работать с широким спектром металлов и сплавов, включая тугоплавкие материалы, такие как вольфрам, молибден и тантал.
Особенно эффективен этот метод для спекания нанопорошков и создания наноструктурных материалов. При этом важна тщательная подготовка исходных материалов - порошки должны быть очищены от оксидов и других примесей, иметь определенный гранулометрический состав.
Одним из интересных применений электроконтактного спекания является создание градиентных материалов, где свойства изделия плавно изменяются от одной части к другой. Например, можно получить деталь, одна сторона которой обладает высокой твердостью, а другая - повышенной пластичностью. Это достигается путем послойного спекания порошков различного состава.
В аэрокосмической отрасли метод электроконтактного спекания используется для изготовления деталей двигателей и теплозащитных экранов. Благодаря возможности работы с тугоплавкими материалами, удается создавать компоненты, способные выдерживать экстремальные температуры и нагрузки.
В медицине эта технология применяется для производства имплантатов с пористой структурой, которая способствует лучшей интеграции с костной тканью.
Электроконтактное спекание нашло широкое применение в производстве режущего инструмента. Метод позволяет создавать твердосплавные пластины с улучшенными характеристиками износостойкости и прочности.
Например, компания Sandvik Coromant использует эту технологию для изготовления инструментов с градиентной структурой, где внешний слой обладает высокой твердостью, а внутренний - повышенной вязкостью.
Основные преимущества технологии
Одним из главных преимуществ электроконтактного спекания является высокая скорость процесса. В отличие от традиционного спекания, которое может занимать часы или даже дни, электроконтактное спекание обычно завершается за несколько минут.
Это не только повышает производительность, но и позволяет сохранить исходную микроструктуру материала, что особенно важно при работе с наноматериалами.
Энергоэффективность - еще одно важное преимущество метода. Локальный нагрев в точках контакта между частицами позволяет достичь требуемой температуры спекания при значительно меньших затратах энергии по сравнению с нагревом всего объема материала в печи. Это особенно актуально при работе с тугоплавкими металлами, требующими высоких температур спекания.
Уникальной особенностью электроконтактного спекания является возможность соединения разнородных материалов, которые трудно или невозможно соединить другими методами.
Например, удается создавать композиты из металлов и керамики, что открывает новые возможности в материаловедении. Российские ученые из Института структурной макрокинетики и проблем материаловедения РАН успешно применили этот метод для создания композитов на основе титана и карбида кремния, обладающих высокой жаропрочностью.
Несмотря на множество преимуществ, электроконтактное спекание имеет ряд ограничений. Одним из основных является сложность контроля процесса, особенно при работе с крупногабаритными изделиями.
Неравномерное распределение тока и температуры может приводить к неоднородности структуры и свойств материала. Для решения этой проблемы разрабатываются сложные системы моделирования и управления процессом.
Другим ограничением является размер и форма изделий. Большинство установок для электроконтактного спекания позволяют работать с образцами диаметром до 100-150 мм. Создание более крупных деталей требует специального оборудования и сопряжено с техническими трудностями.
Кроме того, метод в основном подходит для изготовления изделий простой формы - дисков, цилиндров, пластин. Получение сложных геометрических форм затруднено.
По сравнению с традиционным спеканием в печах, электроконтактное спекание обеспечивает более высокую плотность и однородность структуры материала. Это достигается за счет быстрого нагрева и приложения давления непосредственно в процессе спекания. Однако традиционное спекание остается более универсальным методом, позволяющим работать с изделиями практически любых размеров и форм.
В отличие от сварки, электроконтактное спекание позволяет соединять материалы без их плавления, что особенно важно для сохранения структуры наноматериалов. Кроме того, этот метод обеспечивает более равномерное распределение свойств по объему изделия. Однако сварка остается незаменимой для соединения крупногабаритных деталей и конструкций.
По сравнению с пайкой, электроконтактное спекание обеспечивает более прочное соединение, так как оно происходит на атомарном уровне без использования промежуточных материалов. Однако пайка более универсальна с точки зрения соединяемых материалов и геометрии соединений.
- На главную
-
Категории
-
Пластины твердосплавные
-
Пластины токарные
-
Пластины для внутреннего и наружного точения
-
Пластины резьбовые
-
Пластины резьбовые ISO
-
Пластины резьбовые трапецеидального профиля, угол 30 град.
-
Пластины резьбовые неполного профиля, угол 55 или 60 град.
-
Пластины резьбовые для нарезания трубной резьбы Whitworth, правые
-
Пластины резьбовые NPT (дюймовая коническая резьба c углом профиля 60 град. и конус 1:16)
-
Пластины резьбовые BSPT (Британский стандарт) полного профиля, угол 55 град.
-
Пластины резьбовые треугольного закругленного профиля
-
Пластины резьбовые UN (Американский стандарт) полного профиля, угол 60 град.
- Пластины резьбовые UN (Американский стандарт) полного профиля, угол 60 град.
- Панцирная трубная резьба Pg 80 град.
- Пластины резьбовые трапецеидального профиля, угол 30 град.
- Пластины резьбовые BSPT (Британский стандарт) полного профиля, угол 55 град.
- Пластины резьбовые NPT (дюймовая коническая резьба c углом профиля 60 град. и конус 1:16)
- Пластины резьбовые неполного профиля, угол 55 или 60 град.
-
-
Пластины отрезные и канавочные
-
TGF32
-
SP
-
MRMN
-
MG...N
- GER-C
- SP для стали
- SP для нержавеющей стали
-
QCMB
-
QPMB
- MGMN для стали
- MGMN для нержавеющей стали
- QPMB для стали
- QPMB для нержавеющей стали
- MRMN для стали
- ZP_S для нержавеющей стали
-
ZP_S
- QCMB для нержавеющей стали
- ZT_D для нержавеющей стали
-
ZT_D
- ZT_D для стали
- QCMB для стали
- TDC для нержавеющей стали
-
TDC
- QC_ для нержавеющей стали
-
QC
- QC_
- ZP_D для нержавеющей стали
-
ZP_D
- ZR_D для нержавеющей стали
-
ZR_D
- ZT_S для нержавеющей стали
-
ZT_S
- ZQMX для стали
-
ZQMX
- CTPA для нержавеющей стали
-
CTPA
- MGMN для чугуна
- MRMN для нержавеющей стали
- MRMN для чугуна
-
GEL-A/B
- GEL-A
-
GEL-A/B-R
-
GEL-C/D/E
- GEL-C
-
GEL-C/D/E-R
-
GER-A/B
- GER-A
-
GER-A/B-R
-
GER-C/D/E
-
GER-C/D/E-R
- MGMN
- MGGN
- MB
- ZTKS
- JRMN
- GK-R
- ZRFD
- KTMD
- KGT
- JSMN
- SPDR
-
-
-
Пластины фрезерные
-
Пластины для сверл
-
Лезвия для резьбофрез
-
Пластины со вставками PCBN
- Пластины для червячного зуба 40°
-
-
Фрезы
-
Метчики
-
Сверла
-
Ленточные пилы
-
Новое поступление (NEW!)
-
Державки токарные
-
Державки расточные
-
S...-SVJCR/S...-SVJCL
-
S...-DCLNR/S...-DCLNL
-
S...-DDUNR/S...-DDUNL
-
S...-DWLNR/S...-DWLNL
-
S...-MCKNR/S...-MCKNL
-
S...-MCLNR/S...-MCLNL
-
S...-MDQNR/S...-MDQNL
-
S...-MDUNR/S...-MDUNL
-
S...-MSKNR/S-...MSKNL
-
S...-MTJNR/S...-MTJNL
-
S...-MTQNR/S...-MTQNL
-
S...-MTUNR/S...-MTUNL
-
S...-MTFNR/S...-MTFNL
-
S...-MTWNR/S...-MTWNL
-
S...-MVQNR/S-...MVQNL
-
S...-MVUNR/S-...MVUNL
-
S...-MVWNR/S...-MVWNL
-
S...-MVXNR/S...-MVXNL
-
S...-MWLNR/S...-MWLNL
-
S...-PCLNR/S...-PCLNL
-
S...-PDSNR/S...-PDSNL
-
S...-PDUNR/S...-PDUNL
-
S...-PSKNR/S...-PSKNL
-
S...-PWLNR/S...-PWLNL
-
S...-PTFNR/S...-PTFNL
-
S...-SCKCR/S...-SCKCL
-
S...-SCLCR/S...-SCLCL
-
S...-SCLPR/S...-SCLPL
-
S...-SDQCR/S...-SDQCL
-
S...-SDUCR/S...-SDUCL
-
S...-SDZCR/S...-SDZCL
-
S...-SSSCR/S...-SSSCL
-
S...-SSKCR/S...-SSKCL
-
S...-STFCR/S-...STFCL
-
S...-STUCR/S-...STUCL
-
S...-SVUCR/S-...SVUCL
-
S...-SVUBR/S...-SVUBL
-
-
Державки проходные
-
CCLNR/CCLNL
-
CRDNN
-
CSDNN
-
CSKNR/CSKNL
-
CTJNR/CTJNL
-
DCBNR/DCBNL
-
DCKNR/DCKNL
-
DCLNR/DCLNL
-
DCMNN
-
DDJNR/DDJNL
-
DDPNN
-
DSSNR/DSSNL
-
DDQNR/DDQNL
-
DSBNR/DSBNL
-
DSDNN
-
DSKNR/DSKNL
-
DTFNR/DTFNL
-
DTGNR/DTGNL
-
DVJNR/DVJNL
-
DVVNN
-
DWLNR/DWLNL
-
ECLNR/ECLNL
-
EDJNR/EDJNL
-
EVJNR/EVJNL
-
EWLNR/EWLNL
-
MCBNR/MCBNL
-
MCKNR/MCKNL
-
MCLNR/MCLNL
-
MCMNN
-
MDJNR/MDJNL
-
MDPNN
-
MDQNR/MDQNL
-
MRDNN
-
MRGNR/MRGNL
-
MSBNR/MSBNL
-
MSDNN
-
MSKNR/MSKNL
-
MSSNR/MSSNL
-
MTENN
-
MTFNR/MTFNL
-
MTGNR/MTGNL
-
MTJNR/MTJNL
-
MTQNR/MTQNL
-
MVJNR/MVJNL
-
MVQNR/MVQNL
-
MVUNR/MVUNL
-
MVVNN
-
MWLNR/MWLNL
-
PWLNR/PWLNL
-
PCLNR/PCLNL
-
PDJNR/PDJNL
-
PRACR/PRACL
-
PRDCN
-
PCBNR/PCBNL
-
PRGCR/PRGCL
-
PSBNR/PSBNL
-
PSDNN
-
PSSNR/PSSNL
-
PTGNR/PTGNL
-
PTTNR/PTTNL
-
SCLCR/SCLCL
-
SDJCR/SDJCL
-
SDNCN
-
SRACR/SRACL
-
SRDCN
-
SSDCN
-
SSSCR/SSSCL
-
STFCR/STFCL
-
SVACR/SVACL
-
SVJBR/SVJBL
-
SVJCR/SVJCL
-
SVVBN
-
SVVCN
-
WTENN
-
WTJNR/WTJNL
-
WWLNR/WWLNL
-
PDNNR/PDNNL
-
SVHBR/SVHBL
-
PDNNN
-
PTFNR/PTFNL
-
SCACR/SCACL
-
SDACR/SDACL
-
SSBCR/SSBCL
-
SRGCR/SRGCL
-
SSKCR/SSKCL
-
STGCR/STGCL
-
SVABR/SVABL
-
SVQCR/SVQCL
-
SWACR/SWACL
-
WTQNR/WTQNL
-
-
Державки резьбовые
-
Державки отрезные, канавочные
-
Держатели отрезного лезвия
-
Лезвия отрезные
-
Мини-резцы твердосплавные
-
-
Оснастка для фрезерных станков
-
Фрезерные патроны
-
BT
-
BT-ER (для цанг ER)
-
BT-FMB (для насадных фрез)
-
BT-SCA (для дисковых фрез)
-
BT-D (тестовые оправки)
-
BT-SLN Weldon
-
BT-MTA (конус Морзе с лапкой)
-
BT-MTB (конус Морзе с резьбовым отверстием)
-
BT-DC (высокоскоростные патроны для цанг DC)
-
BT-APU
-
BT-SC (для цилиндрических цанг SC)
-
BT-GT (для резьбовых цанг GT12/24/42)
-
BT-TER (патроны с осевой компенсацией по длине для цанг ER)
-
BT-OZ(EOC) (для силовых цанг OZ)
-
BT-PHC (гидропластовые патроны)
-
-
Конус Морзе MTA/MTB
-
HSK
-
Цилиндрический хвостовик
-
NT
-
SK
-
SK-FMB (для насадных фрез)
-
SK-SLN (Weldon)
-
SK-TER (патроны с осевой компенсацией по длине для цанг ER)
-
SK-SC (для цилиндрических цанг SC)
-
SK-MTB (конус Морзе с резьбовым отверстием)
-
SK-MTA (конус Морзе с лапкой)
-
SK-ER (для цанг ER)
-
SK-GT (для резьбовых цанг GT12/24/42)
-
SK-OZ(EOC) (для силовых цанг OZ)
-
SK-APU (сверлильные быстрозажимные патроны)
-
SK-PHC (гидропластовые патроны)
-
-
-
Прихваты, прижимы, упоры
-
Цанги
-
Штревели
-
3D тестеры
-
Тиски станочные
-
Аксессуары и запчасти
- Силовые высокоточные VQC
-
640 Multitasking
-
Трехкулачковые NBK
-
Гидравлические DCV
-
Модульные двойные ZQ83
-
С регулируемым усилием зажима HPAC
-
Самоцентрирующиеся SC-I
-
Модульные GT
-
Глобусные HHY
-
Лекальные QGG
-
Лекальные QKG
-
Модульные составные ZQ84
-
Гидравлические CHV
-
Самоцентрирующиеся двойные SMC
-
-
Кромкоискатели
-
Магнитные плиты
-
Центроискатели
-
Гайки для цанг
-
Ключи гаечные
-
Приспособления для оправок
-
Наборы прижимов
-
Расточные системы
-
Система нулевого базирования
-
Магнитные захваты
-
Поворотные столы
-
Аксессуары для станочной оснастки
-
Привязка по оси Z
- 3D-тестеры и щупы
-
-
Оснастка для токарных станков
-
Кулачки токарные
- Инструментальные блоки BOT
-
Токарные патроны
-
Центры токарные вращающиеся
- Центры вращающиеся
- Центры вращающиеся усиленные M11
- Центры вращающиеся облегченные
- Центры вращающиеся со сменными вставками
- Центры вращающиеся высокоскоростные
- Центры вращающиеся с твердосплавной вставкой
- Центры вращающиеся с удлиненной вершиной
- Центры вращающиеся усиленные
- Центры вращающиеся высокоточные
- Центры вращающиеся грибковые
-
Держатели осевого инструмента
-
Переходные втулки
-
Приспособления для расточки кулачков
-
Инструментальные блоки BMT
-
Центры токарные упорные
-
Сухари для токарных патронов
-
Инструментальные блоки VDI
-
Патроны цанговые
-
Цанги токарные
-
-
Измерительный инструмент
-
Станки
-
Станки ленточные по металлу
-
Лазерные граверы (маркировщики) по металлу
-
Токарные станки
-
Фрезерные станки
-
Заточные станки
-
Резьбонарезные манипуляторы
-
Электроэрозионные станки
-
Промышленные роботы
-
-
Мерч CNC66
-
Проволока, СОЖ, запчасти для электроэрозионных станков
-
Промышленная мебель
-
Запасные части для державок, резцов и фрез
-
Развертки
-
Упаковка
-
Зенковки
-
Плашки
-
Инструмент для снятия заусенцев
-
Корзина пуста
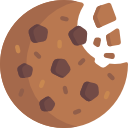
Мы используем файлы cookie для улучшения работы сайта и персонализации. Продолжая использовать сайт, вы соглашаетесь на сбор, обработку cookie-файлов и пользовательских данных с помощью Яндекс.Метрика, в соответствии с нашей Политикой конфиденциальности.