Технология ротационной вытяжки металла
Ротационная вытяжка металла - это метод обработки металлов давлением, позволяющий изготавливать осесимметричные полые детали сложной формы.
Данная технология была изобретена в начале 20 века и получила широкое распространение в промышленности благодаря своим уникальным возможностям.
Принцип ротационной вытяжки металла
Суть процесса ротационной вытяжки заключается в локальном пластическом деформировании вращающейся заготовки при помощи давящего ролика.
Заготовка в виде плоского диска или предварительно отформованной детали закрепляется на вращающейся оправке. К ней подводится давящий ролик, который постепенно обжимает металл по оправке, придавая ему требуемую форму. При этом толщина стенки детали уменьшается, а ее длина увеличивается.
Физической основой метода является локальная пластическая деформация металла в зоне контакта с роликом. Под действием сжимающих напряжений металл течет в радиальном направлении, утоняясь и удлиняясь.
Благодаря локальности деформации, усилия обработки относительно невелики, что позволяет изготавливать крупногабаритные тонкостенные детали.
Процесс ротационной вытяжки включает несколько этапов. Сначала производится подготовка заготовки - вырубка диска из листа или предварительная штамповка.
Затем заготовка закрепляется на оправке и начинается собственно процесс вытяжки. Ролик постепенно обжимает металл по оправке за несколько проходов. На финальном этапе производится калибровка детали для обеспечения требуемой точности.
Основным инструментом при ротационной вытяжке является давящий ролик. Он имеет специальный профиль рабочей поверхности, обеспечивающий оптимальное течение металла. Важную роль играет оправка, которая определяет внутреннюю форму детали. Для сложных изделий могут применяться составные или разборные оправки.
Ключевыми параметрами процесса являются скорость вращения заготовки, усилие давления ролика, подача ролика вдоль образующей детали, а также степень деформации за один проход. Их правильный выбор обеспечивает стабильное протекание процесса и получение качественных изделий.
Ротационной вытяжке поддаются практически все металлы и сплавы, обладающие достаточной пластичностью - алюминий, медь, латунь, низкоуглеродистые и нержавеющие стали, титан и др. Толщина обрабатываемых заготовок может составлять от долей миллиметра до нескольких сантиметров.
Для реализации технологии требуется специализированное оборудование - станки для ротационной вытяжки. Хотя они и универсальны, но все же достаточно дороги, что ограничивает применение метода на небольших предприятиях.
При неправильной настройке процесса возможно появление различных дефектов - гофр, волнистости, разрывов. Поэтому технология требует тщательной отработки режимов обработки для каждого нового изделия.
Данная технология нашла широкое применение в различных отраслях промышленности. В автомобилестроении методом ротационной вытяжки изготавливают детали выхлопных систем, топливные баки, декоративные колпаки колес. В аэрокосмической отрасли - обтекатели, сопла ракетных двигателей, топливные баки.
Производители бытовой техники используют ротационную вытяжку для изготовления корпусов стиральных машин, баков водонагревателей, кухонных вытяжек. В медицинской промышленности по этой технологии делают корпуса томографов, рентгеновских аппаратов и другого оборудования.
Преимущества ротационной вытяжки
Ротационная вытяжка обладает рядом важных преимуществ по сравнению с другими методами обработки металлов давлением. Одним из главных достоинств является высокая точность изготовления деталей.
Благодаря локальности деформации и отсутствию упругого последействия, обеспечивается точность формы и размеров на уровне 0,1-0,2 мм даже для крупногабаритных изделий.
Еще одно преимущество - существенная экономия материала. При ротационной вытяжке коэффициент использования металла достигает 0,9-0,95, тогда как при штамповке он редко превышает 0,6-0,7. Это особенно важно при работе с дорогостоящими материалами, например, титановыми сплавами.
Уникальной особенностью ротационной вытяжки является возможность изготовления тонкостенных деталей большого диаметра. Соотношение диаметра к толщине стенки может достигать 1000 и более. Такие изделия практически невозможно получить другими методами обработки давлением.
Производительность ротационной вытяжки также достаточно высока. Время изготовления одной детали составляет от нескольких секунд до нескольких минут в зависимости от сложности формы и размеров. При этом процесс легко поддается автоматизации, что позволяет организовать массовое производство.
Важным преимуществом является универсальность оборудования. На одном станке можно изготавливать широкую номенклатуру деталей, меняя только оправки и программу обработки. Это особенно ценно для мелкосерийного и опытного производства.
Однако у ротационной вытяжки есть и определенные ограничения. Главное из них - возможность изготовления только осесимметричных деталей. Хотя современные технологии позволяют получать и некоторые неосесимметричные формы, возможности здесь ограничены.
Еще одно ограничение связано со свойствами обрабатываемых материалов. Они должны обладать достаточной пластичностью, чтобы выдерживать значительные деформации без разрушения. Некоторые хрупкие материалы, например, чугун, не поддаются ротационной вытяжке.
Сравнение с другими технологиями формирования металла
Интересно сравнить ротационную вытяжку с другими методами обработки металлов давлением. По сравнению со штамповкой, ротационная вытяжка обеспечивает более высокую точность и качество поверхности, а также лучшую экономию материала. Однако штамповка более производительна при крупносерийном производстве.
Глубокая вытяжка позволяет получать детали более сложной формы, в том числе неосесимметричные. Но по точности и качеству поверхности она уступает ротационной вытяжке. Кроме того, для глубокой вытяжки требуется изготовление дорогостоящей штамповой оснастки.
Обработка давлением жидкостью или эластичной средой дает возможность изготавливать детали сложной формы из листовых заготовок. Однако этот метод менее производителен и требует более мощного оборудования по сравнению с ротационной вытяжкой.
Таким образом, ротационная вытяжка занимает свою уникальную нишу среди методов обработки металлов давлением. Она наиболее эффективна при изготовлении осесимметричных полых деталей сложной формы, особенно тонкостенных и крупногабаритных.
Развитие технологии ротационной вытяжки продолжается. Совершенствуются конструкции станков, появляются новые инструментальные материалы, разрабатываются методы компьютерного моделирования процесса. Это позволяет расширять технологические возможности метода, повышать точность и качество изделий.
Одним из перспективных направлений является сочетание ротационной вытяжки с другими методами обработки в рамках гибридных технологий. Например, комбинация ротационной вытяжки и лазерного нагрева позволяет обрабатывать труднодеформируемые материалы. А сочетание с ультразвуковым воздействием дает возможность повысить пластичность металла и снизить усилия деформирования.
Активно развиваются методы ротационной вытяжки с программным управлением. Они позволяют изготавливать детали сложной геометрии, в том числе с переменной толщиной стенки. Это открывает новые возможности для оптимизации конструкций изделий.
- На главную
-
Категории
-
Пластины твердосплавные
-
Пластины токарные
-
Пластины для внутреннего и наружного точения
-
Пластины резьбовые
-
Пластины резьбовые ISO
-
Пластины резьбовые трапецеидального профиля, угол 30 град.
-
Пластины резьбовые неполного профиля, угол 55 или 60 град.
-
Пластины резьбовые для нарезания трубной резьбы Whitworth, правые
-
Пластины резьбовые NPT (дюймовая коническая резьба c углом профиля 60 град. и конус 1:16)
-
Пластины резьбовые BSPT (Британский стандарт) полного профиля, угол 55 град.
-
Пластины резьбовые треугольного закругленного профиля
-
Пластины резьбовые UN (Американский стандарт) полного профиля, угол 60 град.
- Пластины резьбовые UN (Американский стандарт) полного профиля, угол 60 град.
- Панцирная трубная резьба Pg 80 град.
- Пластины резьбовые трапецеидального профиля, угол 30 град.
- Пластины резьбовые BSPT (Британский стандарт) полного профиля, угол 55 град.
- Пластины резьбовые NPT (дюймовая коническая резьба c углом профиля 60 град. и конус 1:16)
- Пластины резьбовые неполного профиля, угол 55 или 60 град.
- Упорная резьба SAGE 30 град.
-
-
Пластины отрезные и канавочные
-
TGF32
-
SP
-
MRMN
-
MG...N
- GER-C
- SP для стали
- SP для нержавеющей стали
-
QCMB
-
QPMB
- MGMN для стали
- MGMN для нержавеющей стали
- QPMB для стали
- QPMB для нержавеющей стали
- MRMN для стали
- ZP_S для нержавеющей стали
-
ZP_S
- QCMB для нержавеющей стали
- ZT_D для нержавеющей стали
-
ZT_D
- ZT_D для стали
- QCMB для стали
- TDC для нержавеющей стали
-
TDC
- QC_ для нержавеющей стали
-
QC
- QC_
- ZP_D для нержавеющей стали
-
ZP_D
- ZR_D для нержавеющей стали
-
ZR_D
- ZT_S для нержавеющей стали
-
ZT_S
- ZQMX для стали
-
ZQMX
- CTPA для нержавеющей стали
-
CTPA
- MGMN для чугуна
- MRMN для нержавеющей стали
- MRMN для чугуна
-
GEL-A/B
- GEL-A
-
GEL-A/B-R
-
GEL-C/D/E
- GEL-C
-
GEL-C/D/E-R
-
GER-A/B
- GER-A
-
GER-A/B-R
-
GER-C/D/E
-
GER-C/D/E-R
- MGMN
- MGGN
- MB
- ZTKS
- JRMN
- GK-R
- ZRFD
- KTMD
- KGT
- JSMN
- SPDR
-
-
-
Пластины фрезерные
-
Пластины для сверл
-
Лезвия для резьбофрез
-
Пластины со вставками PCBN
- Пластины для червячного зуба 40°
-
-
Фрезы
-
Метчики
-
Сверла
-
Ленточные пилы
-
Новое поступление (NEW!)
-
Державки токарные
-
Державки расточные
-
S...-SVJCR/S...-SVJCL
-
S...-DCLNR/S...-DCLNL
-
S...-DDUNR/S...-DDUNL
-
S...-DWLNR/S...-DWLNL
-
S...-MCKNR/S...-MCKNL
-
S...-MCLNR/S...-MCLNL
-
S...-MDQNR/S...-MDQNL
-
S...-MDUNR/S...-MDUNL
-
S...-MSKNR/S-...MSKNL
-
S...-MTJNR/S...-MTJNL
-
S...-MTQNR/S...-MTQNL
-
S...-MTUNR/S...-MTUNL
-
S...-MTFNR/S...-MTFNL
-
S...-MTWNR/S...-MTWNL
-
S...-MVQNR/S-...MVQNL
-
S...-MVUNR/S-...MVUNL
-
S...-MVWNR/S...-MVWNL
-
S...-MVXNR/S...-MVXNL
-
S...-MWLNR/S...-MWLNL
-
S...-PCLNR/S...-PCLNL
-
S...-PDSNR/S...-PDSNL
-
S...-PDUNR/S...-PDUNL
-
S...-PSKNR/S...-PSKNL
-
S...-PWLNR/S...-PWLNL
-
S...-PTFNR/S...-PTFNL
-
S...-SCKCR/S...-SCKCL
-
S...-SCLCR/S...-SCLCL
-
S...-SCLPR/S...-SCLPL
-
S...-SDQCR/S...-SDQCL
-
S...-SDUCR/S...-SDUCL
-
S...-SDZCR/S...-SDZCL
-
S...-SSSCR/S...-SSSCL
-
S...-SSKCR/S...-SSKCL
-
S...-STFCR/S-...STFCL
-
S...-STUCR/S-...STUCL
-
S...-SVUCR/S-...SVUCL
-
S...-SVUBR/S...-SVUBL
-
-
Державки проходные
-
CCLNR/CCLNL
-
CRDNN
-
CSDNN
-
CSKNR/CSKNL
-
CTJNR/CTJNL
-
DCBNR/DCBNL
-
DCKNR/DCKNL
-
DCLNR/DCLNL
-
DCMNN
-
DDJNR/DDJNL
-
DDPNN
-
DSSNR/DSSNL
-
DDQNR/DDQNL
-
DSBNR/DSBNL
-
DSDNN
-
DSKNR/DSKNL
-
DTFNR/DTFNL
-
DTGNR/DTGNL
-
DVJNR/DVJNL
-
DVVNN
-
DWLNR/DWLNL
-
ECLNR/ECLNL
-
EDJNR/EDJNL
-
EVJNR/EVJNL
-
EWLNR/EWLNL
-
MCBNR/MCBNL
-
MCKNR/MCKNL
-
MCLNR/MCLNL
-
MCMNN
-
MDJNR/MDJNL
-
MDPNN
-
MDQNR/MDQNL
-
MRDNN
-
MRGNR/MRGNL
-
MSBNR/MSBNL
-
MSDNN
-
MSKNR/MSKNL
-
MSSNR/MSSNL
-
MTENN
-
MTFNR/MTFNL
-
MTGNR/MTGNL
-
MTJNR/MTJNL
-
MTQNR/MTQNL
-
MVJNR/MVJNL
-
MVQNR/MVQNL
-
MVUNR/MVUNL
-
MVVNN
-
MWLNR/MWLNL
-
PWLNR/PWLNL
-
PCLNR/PCLNL
-
PDJNR/PDJNL
-
PRACR/PRACL
-
PRDCN
-
PCBNR/PCBNL
-
PRGCR/PRGCL
-
PSBNR/PSBNL
-
PSDNN
-
PSSNR/PSSNL
-
PTGNR/PTGNL
-
PTTNR/PTTNL
-
SCLCR/SCLCL
-
SDJCR/SDJCL
-
SDNCN
-
SRACR/SRACL
-
SRDCN
-
SSDCN
-
SSSCR/SSSCL
-
STFCR/STFCL
-
SVACR/SVACL
-
SVJBR/SVJBL
-
SVJCR/SVJCL
-
SVVBN
-
SVVCN
-
WTENN
-
WTJNR/WTJNL
-
WWLNR/WWLNL
-
PDNNR/PDNNL
-
SVHBR/SVHBL
-
PDNNN
-
PTFNR/PTFNL
-
SCACR/SCACL
-
SDACR/SDACL
-
SSBCR/SSBCL
-
SRGCR/SRGCL
-
SSKCR/SSKCL
-
STGCR/STGCL
-
SVABR/SVABL
-
SVQCR/SVQCL
-
SWACR/SWACL
-
WTQNR/WTQNL
-
-
Державки резьбовые
-
Державки отрезные, канавочные
-
Держатели отрезного лезвия
-
Лезвия отрезные
-
Мини-резцы твердосплавные
-
-
Оснастка для фрезерных станков
-
Фрезерные патроны
-
BT
-
BT-ER (для цанг ER)
-
BT-FMB (для насадных фрез)
-
BT-SCA (для дисковых фрез)
-
BT-D (тестовые оправки)
-
BT-SLN Weldon
-
BT-MTA (конус Морзе с лапкой)
-
BT-MTB (конус Морзе с резьбовым отверстием)
-
BT-DC (высокоскоростные патроны для цанг DC)
-
BT-APU
-
BT-SC (для цилиндрических цанг SC)
-
BT-GT (для резьбовых цанг GT12/24/42)
-
BT-TER (патроны с осевой компенсацией по длине для цанг ER)
-
BT-OZ(EOC) (для силовых цанг OZ)
-
BT-PHC (гидропластовые патроны)
-
-
Конус Морзе MTA/MTB
-
HSK
-
Цилиндрический хвостовик
-
NT
-
SK
-
SK-FMB (для насадных фрез)
-
SK-SLN (Weldon)
-
SK-TER (патроны с осевой компенсацией по длине для цанг ER)
-
SK-SC (для цилиндрических цанг SC)
-
SK-MTB (конус Морзе с резьбовым отверстием)
-
SK-MTA (конус Морзе с лапкой)
-
SK-ER (для цанг ER)
-
SK-GT (для резьбовых цанг GT12/24/42)
-
SK-OZ(EOC) (для силовых цанг OZ)
-
SK-APU (сверлильные быстрозажимные патроны)
-
SK-PHC (гидропластовые патроны)
-
-
-
Прихваты, прижимы, упоры
-
Цанги
-
Штревели
-
3D тестеры
-
Тиски станочные
-
Аксессуары и запчасти
- Силовые высокоточные VQC
-
640 Multitasking
-
Трехкулачковые NBK
-
Гидравлические DCV
-
Модульные двойные ZQ83
-
С регулируемым усилием зажима HPAC
-
Самоцентрирующиеся SC-I
-
Модульные GT
-
Глобусные HHY
-
Лекальные QGG
-
Лекальные QKG
-
Модульные составные ZQ84
-
Гидравлические CHV
-
Самоцентрирующиеся двойные SMC
-
-
Кромкоискатели
-
Магнитные плиты
-
Центроискатели
-
Гайки для цанг
-
Ключи гаечные
-
Приспособления для оправок
-
Наборы прижимов
-
Расточные системы
-
Система нулевого базирования
-
Магнитные захваты
-
Поворотные столы
-
Аксессуары для станочной оснастки
-
Привязка по оси Z
-
Защитные вставки
-
-
Оснастка для токарных станков
-
Кулачки токарные
- Инструментальные блоки BOT
-
Токарные патроны
-
Центры токарные вращающиеся
- Центры вращающиеся
- Центры вращающиеся усиленные M11
- Центры вращающиеся облегченные
- Центры вращающиеся со сменными вставками
- Центры вращающиеся высокоскоростные
- Центры вращающиеся с твердосплавной вставкой
- Центры вращающиеся с удлиненной вершиной
- Центры вращающиеся усиленные
- Центры вращающиеся высокоточные
- Центры вращающиеся грибковые
-
Держатели осевого инструмента
-
Переходные втулки
-
Приспособления для расточки кулачков
-
Инструментальные блоки BMT
-
Центры токарные упорные
-
Сухари для токарных патронов
-
Инструментальные блоки VDI
-
Патроны цанговые
-
Цанги токарные
-
-
Измерительный инструмент
-
Станки
-
Станки ленточные по металлу
-
Лазерные граверы (маркировщики) по металлу
-
Токарные станки
-
Фрезерные станки
-
Заточные станки
-
Резьбонарезные манипуляторы
-
Электроэрозионные станки
-
Промышленные роботы
-
-
Мерч CNC66
-
Проволока, СОЖ, запчасти для электроэрозионных станков
-
Промышленная мебель
-
Запасные части для державок, резцов и фрез
-
Развертки
-
Упаковка
-
Зенковки
-
Плашки
-
Инструмент для снятия заусенцев
-
Корзина пуста
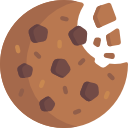
Мы используем файлы cookie для улучшения работы сайта и персонализации. Продолжая использовать сайт, вы соглашаетесь на сбор, обработку cookie-файлов и пользовательских данных с помощью Яндекс.Метрика, в соответствии с нашей Политикой конфиденциальности.