Основные ошибки при токарной обработке металлов и как их избежать
При выполнении токарной обработки металлов важно избегать ошибок, которые могут привести к ухудшению качества изделий, увеличению времени на выполнение операций или повышению износа инструмента. Одной из наиболее распространенных проблем является неправильный выбор параметров резания.
При обработке твердых сплавов, таких как сталь с высоким содержанием углерода, использование слишком высокой скорости резания приводит к быстрому износу режущих кромок и снижению точности обработки.
Чтобы избежать этого, следует учитывать рекомендации производителей инструмента, указывающих оптимальные значения скорости резания, подачи и глубины реза.
Для обработки стали марок 45 или 40Х с использованием твердосплавных пластин оптимальная скорость составляет 80-100 м/мин, глубина резания до 2 мм, а подача — 0,15-0,3 мм/об.
Еще одной частой ошибкой является неправильная установка заготовки в патроне токарного станка. Если заготовка зафиксирована недостаточно надежно, возникает биение, которое может повлиять на геометрию детали. Для устранения этой проблемы необходимо проверять усилие зажима и использовать качественные центровочные устройства.
Также важно убедиться, что торцевые поверхности заготовки тщательно обработаны перед установкой. В случае работы с длинными заготовками необходимо использовать задний центр или люнет, чтобы избежать прогиба и вибрации.
Некачественная подготовка режущего инструмента может стать причиной недостаточной чистоты поверхности или появления дефектов. Неправильный угол заточки приводит к перегреву материала, ухудшению режущих свойств и образованию заусенцев.
При работе с алюминием, например, угол заточки должен быть около 15-20 градусов, а при обработке жаропрочных сплавов он может достигать 5-10 градусов.
Регулярная проверка состояния инструмента и своевременная его замена — залог качественной обработки. Использование смазочно-охлаждающих жидкостей помогает снизить износ и улучшить состояние поверхности.
Применение неподходящих материалов для режущих кромок вызывает повышенный износ и потерю точности обработки. Для обработки мягких материалов, таких как медь или латунь, лучше использовать быстрорежущую сталь, тогда как для работы с твердыми материалами предпочтительнее твердосплавные пластины или керамические вставки.
Ошибки в настройке подачи и глубины резания часто приводят к снижению производительности и качественных характеристик деталей. Чрезмерная подача вызывает вибрации, которые не только ухудшают поверхность, но и увеличивают нагрузку на станок.
Чтобы избежать таких проблем, стоит придерживаться рекомендаций, указанных в паспорте станка, и корректировать параметры резания в зависимости от характеристик материала и задач. При черновой обработке подача может составлять 0,3-0,5 мм/об, а при чистовой — 0,05-0,1 мм/об. Глубина резания при чистовой обработке редко превышает 0,5 мм.
Одним из значительных затруднений в токарной обработке является возникновение вибрации, особенно при работе с длинными заготовками или при использовании инструментов с большой вылетной частью. Вибрации возникают из-за недостаточной жесткости системы станок-заготовка-инструмент.
Для устранения этого необходимо использовать режущие инструменты с минимально возможным вылетом и обеспечивать дополнительную поддержку длинных деталей с помощью подручников или люнетов. Применение демпфирующих держателей может значительно снизить вибрации и улучшить качество обработки.
Неправильный выбор смазочно-охлаждающей жидкости также приводит к появлению различных дефектов и быстрому износу инструмента. При работе с различными материалами важно подбирать состав, соответствующий условиям обработки.
Для стали и жаропрочных сплавов подойдут жидкости на основе минеральных масел, тогда как для алюминия предпочтительнее использовать водорастворимые эмульсии с высокой охлаждающей способностью. Регулярная замена и фильтрация жидкости помогают поддерживать стабильные условия резания и продлевают срок службы режущего инструмента.
Невнимательное отношение к чертежам и несоблюдение допусков на размеры — одна из частых причин брака. Тщательная проверка настроек станка и постоянный контроль размеров детали во время обработки позволяют избежать проблем.
Использование микрометров, штангенциркулей и других измерительных приборов высокого класса точности помогает исключить отклонения от заданных параметров. Важно помнить, что температурные изменения могут влиять на размеры деталей, поэтому в условиях интенсивного резания необходимо учитывать коэффициенты температурного расширения материалов.
Недостаточное внимание к состоянию станка также становится причиной проблем при обработке. Износ направляющих, люфты в узлах подачи или недостаточная жесткость конструкции вызывают отклонения в геометрии деталей.
Регулярное техническое обслуживание, проверка состояния станка и своевременная замена изношенных частей обеспечивают стабильное качество обработки. Кроме того, правильная установка и балансировка резцедержателя способствуют снижению вибраций и увеличению точности.
Несоблюдение порядка обработки сложных поверхностей или элементов, таких как резьбы, канавки и фаски, приводит к неточностям и увеличению времени на выполнение операций. Для выполнения резьбы необходимо использовать специализированные резцы с точным профилем, а подача должна быть синхронизирована с вращением шпинделя.
Обработка канавок требует применения узкоспециализированных резцов с повышенной жесткостью, а при выполнении фасок важно соблюдать угол наклона инструмента и глубину реза, чтобы избежать заусенцев.
Еще одной ошибкой является использование неподходящих режимов работы при обработке заготовок из композитных материалов или сплавов с высокой абразивностью. Такие материалы, как стеклопластик или титановый сплав, требуют применения инструментов с покрытием из нитрида титана или алмазного напыления, которые обеспечивают высокую износостойкость.
Оптимальный режим обработки для этих материалов включает низкие скорости резания, небольшую подачу и использование мощных систем охлаждения.
Для предотвращения ошибок важно обучать персонал правильным методам работы с оборудованием и материалами. Знание характеристик обрабатываемого материала, оптимальных параметров резания и способов устранения дефектов помогает не только повысить качество продукции, но и снизить затраты на инструмент и время обработки.
Постоянное повышение квалификации сотрудников позволяет исключить большинство ошибок и улучшить производственные показатели.
- На главную
-
Категории
-
Пластины твердосплавные
-
Пластины токарные
-
Пластины для внутреннего и наружного точения
-
Пластины резьбовые
-
Пластины резьбовые ISO
-
Пластины резьбовые трапецеидального профиля, угол 30 град.
-
Пластины резьбовые неполного профиля, угол 55 или 60 град.
-
Пластины резьбовые для нарезания трубной резьбы Whitworth, правые
-
Пластины резьбовые NPT (дюймовая коническая резьба c углом профиля 60 град. и конус 1:16)
-
Пластины резьбовые BSPT (Британский стандарт) полного профиля, угол 55 град.
-
Пластины резьбовые треугольного закругленного профиля
-
Пластины резьбовые UN (Американский стандарт) полного профиля, угол 60 град.
- Пластины резьбовые UN (Американский стандарт) полного профиля, угол 60 град.
- Панцирная трубная резьба Pg 80 град.
- Пластины резьбовые трапецеидального профиля, угол 30 град.
- Пластины резьбовые BSPT (Британский стандарт) полного профиля, угол 55 град.
- Пластины резьбовые NPT (дюймовая коническая резьба c углом профиля 60 град. и конус 1:16)
- Пластины резьбовые неполного профиля, угол 55 или 60 град.
- Упорная резьба SAGE 30 град.
-
-
Пластины отрезные и канавочные
-
TGF32
-
SP
-
MRMN
-
MG...N
- GER-C
- SP для стали
- SP для нержавеющей стали
-
QCMB
-
QPMB
- MGMN для стали
- MGMN для нержавеющей стали
- QPMB для стали
- QPMB для нержавеющей стали
- MRMN для стали
- ZP_S для нержавеющей стали
-
ZP_S
- QCMB для нержавеющей стали
- ZT_D для нержавеющей стали
-
ZT_D
- ZT_D для стали
- QCMB для стали
- TDC для нержавеющей стали
-
TDC
- QC_ для нержавеющей стали
-
QC
- QC_
- ZP_D для нержавеющей стали
-
ZP_D
- ZR_D для нержавеющей стали
-
ZR_D
- ZT_S для нержавеющей стали
-
ZT_S
- ZQMX для стали
-
ZQMX
- CTPA для нержавеющей стали
-
CTPA
- MGMN для чугуна
- MRMN для нержавеющей стали
- MRMN для чугуна
-
GEL-A/B
- GEL-A
-
GEL-A/B-R
-
GEL-C/D/E
- GEL-C
-
GEL-C/D/E-R
-
GER-A/B
- GER-A
-
GER-A/B-R
-
GER-C/D/E
-
GER-C/D/E-R
- MGMN
- MGGN
- MB
- ZTKS
- JRMN
- GK-R
- ZRFD
- KTMD
- KGT
- JSMN
- SPDR
-
-
-
Пластины фрезерные
-
Пластины для сверл
-
Лезвия для резьбофрез
-
Пластины со вставками PCBN
- Пластины для червячного зуба 40°
-
-
Фрезы
-
Фрезы монолитные
-
Концевые
-
HRC72
- HRC45
- HRC55
- HRC60
- HRC65
- HRC66
- HRC70
- HRC45
- HRC55
- HRC60
- HRC65
- HRC66
- HRC70
- HRC45
- HRC55
- HRC60
- HRC65
- HRC66
- HRC70
- HRC45
- HRC55
- HRC60
- HRC65
- HRC66
- HRC70
- HRC45
- HRC55
- HRC60
- HRC65
- HRC66
- HRC70
- HRC45
- HRC55
- HRC60
- HRC65
- HRC66
- HRC70
- HRC45
- HRC55
- HRC60
- HRC65
- HRC66
- HRC70
- HRC55
- HRC65
- HRC70
- HRC60
- HRC45
- HRC66
- HRC45
- HRC55
- HRC60
- HRC65
- HRC66
- HRC70
- HRC45
- HRC55
- HRC60
- HRC65
- HRC66
- HRC70
- HRC45
- HRC55
- HRC60
- HRC65
- HRC66
- HRC70
-
-
Радиусные
-
Сферические
-
Фасочные
-
Граверы
-
Дисковые
- Резьбофрезы
-
-
Фрезы со сменными пластинами
-
Фрезы дисковые
-
Фрезы концевые
-
ASM
-
BAP
- BMR
-
EMR
-
PE03
-
RB02
-
RB03
-
TEBL
-
ХК01
- ХК02
- SSM390
- EMP01
- AF06
- BAP
- EMR
- EMRW
- EXN03
- PE01
- PE02
- PE05
- R217.96
- RF01
- AF06
- BAP
- EMR
- EMRW
- EXN03
- PE01
- PE02
- PE05
- R217.96
- RF01
- AF06
- BAP
- EMR
- EMRW
- EXN03
- PE01
- PE02
- PE05
- R217.96
- RF01
- AF06
- BAP
- EMR
- EMRW
- EXN03
- PE01
- PE02
- PE05
- R217.96
- RF01
- AF06
- BAP
- EMR
- EMRW
- EXN03
- PE01
- PE02
- PE05
- R217.96
- RF01
- AF06
- BAP
- EMR
- EMRW
- EXN03
- PE01
- PE02
- PE05
- R217.96
- RF01
- AF06
- BAP
- EMR
- EMRW
- EXN03
- PE01
- PE02
- PE05
- R217.96
- RF01
- RF01
- EXN03
- PE02
- AF06
- R217.96
- EMRW
- EMR
- BAP
- PE01
- PE05
- AF06
- BAP
- EMR
- EMRW
- EXN03
- PE01
- PE02
- PE05
- R217.96
- RF01
- AF06
- BAP
- EMR
- EMRW
- EXN03
- PE01
- PE02
- PE05
- R217.96
- RF01
- AF06
- BAP
- EMR
- EMRW
- EXN03
- PE01
- PE02
- PE05
- R217.96
- RF01
-
-
Фрезы резьбонарезные
-
Фрезы торцевые насадные
-
Фрезы фасочные
-
-
Фрезы со сменными головками
-
-
Метчики
-
Сверла
-
Ленточные пилы
-
Новое поступление (NEW!)
-
Державки токарные
-
Державки расточные
-
S...-SVJCR/S...-SVJCL
-
S...-DCLNR/S...-DCLNL
-
S...-DDUNR/S...-DDUNL
-
S...-DWLNR/S...-DWLNL
-
S...-MCKNR/S...-MCKNL
-
S...-MCLNR/S...-MCLNL
-
S...-MDQNR/S...-MDQNL
-
S...-MDUNR/S...-MDUNL
-
S...-MSKNR/S-...MSKNL
-
S...-MTJNR/S...-MTJNL
-
S...-MTQNR/S...-MTQNL
-
S...-MTUNR/S...-MTUNL
-
S...-MTFNR/S...-MTFNL
-
S...-MTWNR/S...-MTWNL
-
S...-MVQNR/S-...MVQNL
-
S...-MVUNR/S-...MVUNL
-
S...-MVWNR/S...-MVWNL
-
S...-MVXNR/S...-MVXNL
-
S...-MWLNR/S...-MWLNL
-
S...-PCLNR/S...-PCLNL
-
S...-PDSNR/S...-PDSNL
-
S...-PDUNR/S...-PDUNL
-
S...-PSKNR/S...-PSKNL
-
S...-PWLNR/S...-PWLNL
-
S...-PTFNR/S...-PTFNL
-
S...-SCKCR/S...-SCKCL
-
S...-SCLCR/S...-SCLCL
-
S...-SCLPR/S...-SCLPL
-
S...-SDQCR/S...-SDQCL
-
S...-SDUCR/S...-SDUCL
-
S...-SDZCR/S...-SDZCL
-
S...-SSSCR/S...-SSSCL
-
S...-SSKCR/S...-SSKCL
-
S...-STFCR/S-...STFCL
-
S...-STUCR/S-...STUCL
-
S...-SVUCR/S-...SVUCL
-
S...-SVUBR/S...-SVUBL
-
-
Державки проходные
-
CCLNR/CCLNL
-
CRDNN
-
CSDNN
-
CSKNR/CSKNL
-
CTJNR/CTJNL
-
DCBNR/DCBNL
-
DCKNR/DCKNL
-
DCLNR/DCLNL
-
DCMNN
-
DDJNR/DDJNL
-
DDPNN
-
DSSNR/DSSNL
-
DDQNR/DDQNL
-
DSBNR/DSBNL
-
DSDNN
-
DSKNR/DSKNL
-
DTFNR/DTFNL
-
DTGNR/DTGNL
-
DVJNR/DVJNL
-
DVVNN
-
DWLNR/DWLNL
-
ECLNR/ECLNL
-
EDJNR/EDJNL
-
EVJNR/EVJNL
-
EWLNR/EWLNL
-
MCBNR/MCBNL
-
MCKNR/MCKNL
-
MCLNR/MCLNL
-
MCMNN
-
MDJNR/MDJNL
-
MDPNN
-
MDQNR/MDQNL
-
MRDNN
-
MRGNR/MRGNL
-
MSBNR/MSBNL
-
MSDNN
-
MSKNR/MSKNL
-
MSSNR/MSSNL
-
MTENN
-
MTFNR/MTFNL
-
MTGNR/MTGNL
-
MTJNR/MTJNL
-
MTQNR/MTQNL
-
MVJNR/MVJNL
-
MVQNR/MVQNL
-
MVUNR/MVUNL
-
MVVNN
-
MWLNR/MWLNL
-
PWLNR/PWLNL
-
PCLNR/PCLNL
-
PDJNR/PDJNL
-
PRACR/PRACL
-
PRDCN
-
PCBNR/PCBNL
-
PRGCR/PRGCL
-
PSBNR/PSBNL
-
PSDNN
-
PSSNR/PSSNL
-
PTGNR/PTGNL
-
PTTNR/PTTNL
-
SCLCR/SCLCL
-
SDJCR/SDJCL
-
SDNCN
-
SRACR/SRACL
-
SRDCN
-
SSDCN
-
SSSCR/SSSCL
-
STFCR/STFCL
-
SVACR/SVACL
-
SVJBR/SVJBL
-
SVJCR/SVJCL
-
SVVBN
-
SVVCN
-
WTENN
-
WTJNR/WTJNL
-
WWLNR/WWLNL
-
PDNNR/PDNNL
-
SVHBR/SVHBL
-
PDNNN
-
PTFNR/PTFNL
-
SCACR/SCACL
-
SDACR/SDACL
-
SSBCR/SSBCL
-
SRGCR/SRGCL
-
SSKCR/SSKCL
-
STGCR/STGCL
-
SVABR/SVABL
-
SVQCR/SVQCL
-
SWACR/SWACL
-
WTQNR/WTQNL
-
-
Державки резьбовые
-
Державки отрезные, канавочные
-
Держатели отрезного лезвия
-
Лезвия отрезные
-
Мини-резцы твердосплавные
-
-
Оснастка для фрезерных станков
-
Фрезерные патроны
-
BT
-
BT-ER (для цанг ER)
-
BT-FMB (для насадных фрез)
-
BT-SCA (для дисковых фрез)
-
BT-D (тестовые оправки)
-
BT-SLN Weldon
-
BT-MTA (конус Морзе с лапкой)
-
BT-MTB (конус Морзе с резьбовым отверстием)
-
BT-DC (высокоскоростные патроны для цанг DC)
-
BT-APU
-
BT-SC (для цилиндрических цанг SC)
-
BT-GT (для резьбовых цанг GT12/24/42)
-
BT-TER (патроны с осевой компенсацией по длине для цанг ER)
-
BT-OZ(EOC) (для силовых цанг OZ)
-
BT-PHC (гидропластовые патроны)
-
-
Конус Морзе MTA/MTB
-
HSK
-
Цилиндрический хвостовик
-
NT
-
SK
-
SK-FMB (для насадных фрез)
-
SK-SLN (Weldon)
-
SK-TER (патроны с осевой компенсацией по длине для цанг ER)
-
SK-SC (для цилиндрических цанг SC)
-
SK-MTB (конус Морзе с резьбовым отверстием)
-
SK-MTA (конус Морзе с лапкой)
-
SK-ER (для цанг ER)
-
SK-GT (для резьбовых цанг GT12/24/42)
-
SK-OZ(EOC) (для силовых цанг OZ)
-
SK-APU (сверлильные быстрозажимные патроны)
-
SK-PHC (гидропластовые патроны)
-
-
-
Прихваты, прижимы, упоры
-
Цанги
-
Штревели
-
3D тестеры
-
Тиски станочные
-
Аксессуары и запчасти
- Силовые высокоточные VQC
-
640 Multitasking
-
Трехкулачковые NBK
-
Гидравлические DCV
-
Модульные двойные ZQ83
-
С регулируемым усилием зажима HPAC
-
Самоцентрирующиеся SC-I
-
Модульные GT
-
Глобусные HHY
-
Лекальные QGG
-
Лекальные QKG
-
Модульные составные ZQ84
-
Гидравлические CHV
-
Самоцентрирующиеся двойные SMC
-
-
Кромкоискатели
-
Магнитные плиты
-
Центроискатели
-
Гайки для цанг
-
Ключи гаечные
-
Приспособления для оправок
-
Наборы прижимов
-
Расточные системы
-
Система нулевого базирования
-
Магнитные захваты
-
Поворотные столы
-
Аксессуары для станочной оснастки
-
Привязка по оси Z
-
Защитные вставки
-
-
Оснастка для токарных станков
-
Кулачки токарные
- Инструментальные блоки BOT
-
Токарные патроны
-
Центры токарные вращающиеся
- Центры вращающиеся
- Центры вращающиеся усиленные M11
- Центры вращающиеся облегченные
- Центры вращающиеся со сменными вставками
- Центры вращающиеся высокоскоростные
- Центры вращающиеся с твердосплавной вставкой
- Центры вращающиеся с удлиненной вершиной
- Центры вращающиеся усиленные
- Центры вращающиеся высокоточные
- Центры вращающиеся грибковые
-
Держатели осевого инструмента
-
Переходные втулки
-
Приспособления для расточки кулачков
-
Инструментальные блоки BMT
-
Центры токарные упорные
-
Сухари для токарных патронов
-
Инструментальные блоки VDI
-
Патроны цанговые
-
Цанги токарные
-
-
Измерительный инструмент
-
Станки
-
Станки ленточные по металлу
-
Лазерные граверы (маркировщики) по металлу
-
Токарные станки
-
Фрезерные станки
-
Заточные станки
-
Резьбонарезные манипуляторы
-
Электроэрозионные станки
-
Промышленные роботы
-
-
Мерч CNC66
-
Проволока, СОЖ, запчасти для электроэрозионных станков
-
Промышленная мебель
-
Запасные части для державок, резцов и фрез
-
Развертки
-
Упаковка
-
Зенковки
-
Плашки
-
Инструмент для снятия заусенцев
-
Корзина пуста
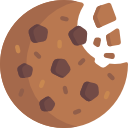
Мы используем файлы cookie для улучшения работы сайта и персонализации. Продолжая использовать сайт, вы соглашаетесь на сбор, обработку cookie-файлов и пользовательских данных с помощью Яндекс.Метрика, в соответствии с нашей Политикой конфиденциальности.