Рекомендации по выбору метода закалки для различных типов стали
Закалка металлов представляет собой один из важнейших процессов в металлургии и машиностроении, позволяющий значительно улучшить механические свойства изделий.
Для различных типов стали выбор метода закалки определяется их химическим составом, структурой, а также требованиями к конечным характеристикам материала. Чтобы избежать ошибок при подборе и реализации процесса, важно учитывать несколько ключевых факторов и применять проверенные рекомендации на практике.
Основное различие в подходах к закалке связано с содержанием углерода в стали. Низкоуглеродистые марки, содержащие менее 0,3% углерода, требуют применения методов, которые обеспечивают равномерное охлаждение, минимизируя риск деформаций.
Для таких сталей зачастую используется закалка в воде или водных растворах с добавками. Температура нагрева должна быть точно выдержана в пределах 880–900 °C, чтобы обеспечить полное растворение углерода в аустените.
Важно учитывать, что слишком быстрое охлаждение может привести к образованию закалочных трещин, поэтому стоит отдавать предпочтение менее агрессивным средам, таким как масляные ванны с температурой около 60–80 °C.
Для среднеуглеродистых сталей, с содержанием углерода от 0,3% до 0,6%, подходит более широкий спектр методов. Такие стали после закалки приобретают высокую твердость, однако требуют обязательного отпуска для снятия внутренних напряжений.
Процесс отпуска рекомендуется проводить при температуре 300–500 °C, в зависимости от необходимой прочности и пластичности. Использование соляных ванн для нагрева обеспечивает равномерность температуры, что особенно важно для крупных деталей.
Закалку этих сталей можно выполнять в масле или специально подготовленных растворах, таких как 10%-ный раствор каустической соды, который снижает вероятность перегрева поверхности.
Высокоуглеродистые марки, содержащие свыше 0,6% углерода, требуют особенно тщательного контроля температуры нагрева и времени выдержки. Оптимальная температура для закалки таких сталей составляет 780–820 °C. Перегрев или чрезмерно длительное удержание при высокой температуре может привести к зернистости, что ухудшает механические свойства.
Для охлаждения высокоуглеродистых сталей лучше всего подходит масло, обеспечивающее мягкое охлаждение, или расплавленные соли при температуре около 150 °C. Альтернативой могут служить воздух или инертные газы, если требуется минимизировать риск деформаций.
Сплавы инструментальной группы, такие как сталь У8 или У10, требуют особого подхода к закалке, учитывая их применение в условиях высоких нагрузок. Такие материалы часто обрабатываются методом ступенчатой закалки, при которой детали выдерживаются в жидкой среде с температурой около 250–300 °C, а затем охлаждаются до комнатной температуры.
Это позволяет избежать возникновения внутренних напряжений и обеспечивать равномерное распределение твердости по всей толщине изделия. При использовании вакуумных печей для нагрева можно достигнуть высокой чистоты поверхности, что особенно важно для режущего инструмента.
Нержавеющие стали, отличающиеся высоким содержанием хрома и никеля, закаливаются преимущественно методом термической обработки в инертных газах. Температура нагрева варьируется от 1000 до 1100 °C, что обеспечивает растворение карбидов и образование однородной структуры.
Охлаждение проводят в газовой среде под высоким давлением, что минимизирует риск окисления и сохраняет точные размеры изделия. Такой метод особенно эффективен для сталей аустенитного класса, которые применяются в химической промышленности и медицине.
Для деталей сложной формы и тонкостенных изделий предпочтительно применять изотермическую закалку. Этот метод включает постепенное охлаждение до температуры 250–300 °C, с последующей выдержкой до завершения фазовых превращений.
Изотермическая закалка позволяет существенно снизить деформации, что особенно важно при изготовлении компонентов, требующих высокой точности размеров. Для реализации процесса используются печи с контролируемой атмосферой и термостойкие жидкости, такие как масло с добавками полимеров.
Ошибки при выборе и выполнении закалки часто связаны с неправильной оценкой свойств материала или несоблюдением технологических режимов. Одной из распространенных проблем является недостаточный прогрев детали, который приводит к образованию мягких участков в структуре.
Чтобы этого избежать, необходимо использовать пирометры для контроля температуры в зоне нагрева. Также следует учитывать, что большие детали требуют более длительного времени выдержки, чтобы обеспечить равномерный прогрев по всей толщине.
Еще одной частой ошибкой является использование неподходящей охлаждающей среды. Применение воды вместо масла для среднеуглеродистых сталей может привести к образованию трещин из-за высокой скорости охлаждения.
Для выбора правильной среды необходимо учитывать размер и форму детали, а также наличие концентраторов напряжений, таких как резьбовые соединения или отверстия. В случае сложных форм целесообразно использовать полимерные растворы, обеспечивающие регулируемую скорость охлаждения.
Нарушение времени выдержки при нагреве — еще один фактор, способный негативно сказаться на свойствах металла. Слишком короткое время приводит к неравномерному распределению твердости, а избыточная выдержка вызывает рост зерна.
Оптимальное время рассчитывается исходя из толщины детали и коэффициента теплопроводности стали. Для тонкостенных изделий время выдержки обычно составляет 10–15 минут, в то время как для массивных деталей этот показатель может достигать 1–2 часов.
Рекомендации по выбору оборудования для закалки также играют важную роль в успешной обработке. Использование современных печей с микропроцессорным управлением позволяет точно регулировать температурные параметры и исключать ошибки, связанные с человеческим фактором.
Оборудование должно быть оснащено системой принудительного охлаждения, что особенно важно при работе с крупными деталями. Вакуумные и газовые печи подходят для закалки инструментальных и нержавеющих сталей, так как они обеспечивают минимальный уровень загрязнений поверхности и точное соблюдение температурных режимов.
Для повышения качества закалки рекомендуется проводить предварительную нормализацию стали. Этот процесс позволяет устранить остаточные напряжения и обеспечить равномерность структуры перед закалкой.
Нормализация выполняется при температуре 850–890 °C с медленным охлаждением на воздухе. После этого можно приступить к основному этапу, точно выдерживая параметры нагрева и охлаждения.
Закалка металлов — сложный процесс, требующий учета множества факторов. От правильного выбора метода зависит не только долговечность изделия, но и его эксплуатационные характеристики. Следуя описанным рекомендациям, можно минимизировать риски, связанные с деформациями, трещинами и несоответствием механических свойств стали.
Особое внимание следует уделять подбору оборудования, контролю температуры и использованию подходящих охлаждающих сред, чтобы достичь высокого качества обработки.
- На главную
-
Категории
-
Пластины твердосплавные
-
Пластины токарные
-
Пластины для внутреннего и наружного точения
-
Пластины резьбовые
-
Пластины резьбовые ISO
-
Пластины резьбовые трапецеидального профиля, угол 30 град.
-
Пластины резьбовые неполного профиля, угол 55 или 60 град.
-
Пластины резьбовые для нарезания трубной резьбы Whitworth, правые
-
Пластины резьбовые NPT (дюймовая коническая резьба c углом профиля 60 град. и конус 1:16)
-
Пластины резьбовые BSPT (Британский стандарт) полного профиля, угол 55 град.
-
Пластины резьбовые треугольного закругленного профиля
-
Пластины резьбовые UN (Американский стандарт) полного профиля, угол 60 град.
- Пластины резьбовые UN (Американский стандарт) полного профиля, угол 60 град.
- Панцирная трубная резьба Pg 80 град.
- Пластины резьбовые трапецеидального профиля, угол 30 град.
- Пластины резьбовые BSPT (Британский стандарт) полного профиля, угол 55 град.
- Пластины резьбовые NPT (дюймовая коническая резьба c углом профиля 60 град. и конус 1:16)
- Пластины резьбовые неполного профиля, угол 55 или 60 град.
- Упорная резьба SAGE 30 град.
-
-
Пластины отрезные и канавочные
-
TGF32
-
SP
-
MRMN
-
MG...N
- GER-C
- SP для стали
- SP для нержавеющей стали
-
QCMB
-
QPMB
- MGMN для стали
- MGMN для нержавеющей стали
- QPMB для стали
- QPMB для нержавеющей стали
- MRMN для стали
- ZP_S для нержавеющей стали
-
ZP_S
- QCMB для нержавеющей стали
- ZT_D для нержавеющей стали
-
ZT_D
- ZT_D для стали
- QCMB для стали
- TDC для нержавеющей стали
-
TDC
- QC_ для нержавеющей стали
-
QC
- QC_
- ZP_D для нержавеющей стали
-
ZP_D
- ZR_D для нержавеющей стали
-
ZR_D
- ZT_S для нержавеющей стали
-
ZT_S
- ZQMX для стали
-
ZQMX
- CTPA для нержавеющей стали
-
CTPA
- MGMN для чугуна
- MRMN для нержавеющей стали
- MRMN для чугуна
-
GEL-A/B
- GEL-A
-
GEL-A/B-R
-
GEL-C/D/E
- GEL-C
-
GEL-C/D/E-R
-
GER-A/B
- GER-A
-
GER-A/B-R
-
GER-C/D/E
-
GER-C/D/E-R
- MGMN
- MGGN
- MB
- ZTKS
- JRMN
- GK-R
- ZRFD
- KTMD
- KGT
- JSMN
- SPDR
-
-
-
Пластины фрезерные
-
Пластины для сверл
-
Лезвия для резьбофрез
-
Пластины со вставками PCBN
- Пластины для червячного зуба 40°
-
-
Фрезы
-
Метчики
-
Сверла
-
Ленточные пилы
-
Новое поступление (NEW!)
-
Державки токарные
-
Державки расточные
-
S...-SVJCR/S...-SVJCL
-
S...-DCLNR/S...-DCLNL
-
S...-DDUNR/S...-DDUNL
-
S...-DWLNR/S...-DWLNL
-
S...-MCKNR/S...-MCKNL
-
S...-MCLNR/S...-MCLNL
-
S...-MDQNR/S...-MDQNL
-
S...-MDUNR/S...-MDUNL
-
S...-MSKNR/S-...MSKNL
-
S...-MTJNR/S...-MTJNL
-
S...-MTQNR/S...-MTQNL
-
S...-MTUNR/S...-MTUNL
-
S...-MTFNR/S...-MTFNL
-
S...-MTWNR/S...-MTWNL
-
S...-MVQNR/S-...MVQNL
-
S...-MVUNR/S-...MVUNL
-
S...-MVWNR/S...-MVWNL
-
S...-MVXNR/S...-MVXNL
-
S...-MWLNR/S...-MWLNL
-
S...-PCLNR/S...-PCLNL
-
S...-PDSNR/S...-PDSNL
-
S...-PDUNR/S...-PDUNL
-
S...-PSKNR/S...-PSKNL
-
S...-PWLNR/S...-PWLNL
-
S...-PTFNR/S...-PTFNL
-
S...-SCKCR/S...-SCKCL
-
S...-SCLCR/S...-SCLCL
-
S...-SCLPR/S...-SCLPL
-
S...-SDQCR/S...-SDQCL
-
S...-SDUCR/S...-SDUCL
-
S...-SDZCR/S...-SDZCL
-
S...-SSSCR/S...-SSSCL
-
S...-SSKCR/S...-SSKCL
-
S...-STFCR/S-...STFCL
-
S...-STUCR/S-...STUCL
-
S...-SVUCR/S-...SVUCL
-
S...-SVUBR/S...-SVUBL
-
-
Державки проходные
-
CCLNR/CCLNL
-
CRDNN
-
CSDNN
-
CSKNR/CSKNL
-
CTJNR/CTJNL
-
DCBNR/DCBNL
-
DCKNR/DCKNL
-
DCLNR/DCLNL
-
DCMNN
-
DDJNR/DDJNL
-
DDPNN
-
DSSNR/DSSNL
-
DDQNR/DDQNL
-
DSBNR/DSBNL
-
DSDNN
-
DSKNR/DSKNL
-
DTFNR/DTFNL
-
DTGNR/DTGNL
-
DVJNR/DVJNL
-
DVVNN
-
DWLNR/DWLNL
-
ECLNR/ECLNL
-
EDJNR/EDJNL
-
EVJNR/EVJNL
-
EWLNR/EWLNL
-
MCBNR/MCBNL
-
MCKNR/MCKNL
-
MCLNR/MCLNL
-
MCMNN
-
MDJNR/MDJNL
-
MDPNN
-
MDQNR/MDQNL
-
MRDNN
-
MRGNR/MRGNL
-
MSBNR/MSBNL
-
MSDNN
-
MSKNR/MSKNL
-
MSSNR/MSSNL
-
MTENN
-
MTFNR/MTFNL
-
MTGNR/MTGNL
-
MTJNR/MTJNL
-
MTQNR/MTQNL
-
MVJNR/MVJNL
-
MVQNR/MVQNL
-
MVUNR/MVUNL
-
MVVNN
-
MWLNR/MWLNL
-
PWLNR/PWLNL
-
PCLNR/PCLNL
-
PDJNR/PDJNL
-
PRACR/PRACL
-
PRDCN
-
PCBNR/PCBNL
-
PRGCR/PRGCL
-
PSBNR/PSBNL
-
PSDNN
-
PSSNR/PSSNL
-
PTGNR/PTGNL
-
PTTNR/PTTNL
-
SCLCR/SCLCL
-
SDJCR/SDJCL
-
SDNCN
-
SRACR/SRACL
-
SRDCN
-
SSDCN
-
SSSCR/SSSCL
-
STFCR/STFCL
-
SVACR/SVACL
-
SVJBR/SVJBL
-
SVJCR/SVJCL
-
SVVBN
-
SVVCN
-
WTENN
-
WTJNR/WTJNL
-
WWLNR/WWLNL
-
PDNNR/PDNNL
-
SVHBR/SVHBL
-
PDNNN
-
PTFNR/PTFNL
-
SCACR/SCACL
-
SDACR/SDACL
-
SSBCR/SSBCL
-
SRGCR/SRGCL
-
SSKCR/SSKCL
-
STGCR/STGCL
-
SVABR/SVABL
-
SVQCR/SVQCL
-
SWACR/SWACL
-
WTQNR/WTQNL
-
-
Державки резьбовые
-
Державки отрезные, канавочные
-
Держатели отрезного лезвия
-
Лезвия отрезные
-
Мини-резцы твердосплавные
-
-
Оснастка для фрезерных станков
-
Фрезерные патроны
-
BT
-
BT-ER (для цанг ER)
-
BT-FMB (для насадных фрез)
-
BT-SCA (для дисковых фрез)
-
BT-D (тестовые оправки)
-
BT-SLN Weldon
-
BT-MTA (конус Морзе с лапкой)
-
BT-MTB (конус Морзе с резьбовым отверстием)
-
BT-DC (высокоскоростные патроны для цанг DC)
-
BT-APU
-
BT-SC (для цилиндрических цанг SC)
-
BT-GT (для резьбовых цанг GT12/24/42)
-
BT-TER (патроны с осевой компенсацией по длине для цанг ER)
-
BT-OZ(EOC) (для силовых цанг OZ)
-
BT-PHC (гидропластовые патроны)
-
-
Конус Морзе MTA/MTB
-
HSK
-
Цилиндрический хвостовик
-
NT
-
SK
-
SK-FMB (для насадных фрез)
-
SK-SLN (Weldon)
-
SK-TER (патроны с осевой компенсацией по длине для цанг ER)
-
SK-SC (для цилиндрических цанг SC)
-
SK-MTB (конус Морзе с резьбовым отверстием)
-
SK-MTA (конус Морзе с лапкой)
-
SK-ER (для цанг ER)
-
SK-GT (для резьбовых цанг GT12/24/42)
-
SK-OZ(EOC) (для силовых цанг OZ)
-
SK-APU (сверлильные быстрозажимные патроны)
-
SK-PHC (гидропластовые патроны)
-
-
-
Прихваты, прижимы, упоры
-
Цанги
-
Штревели
-
3D тестеры
-
Тиски станочные
-
Аксессуары и запчасти
- Силовые высокоточные VQC
-
640 Multitasking
-
Трехкулачковые NBK
-
Гидравлические DCV
-
Модульные двойные ZQ83
-
С регулируемым усилием зажима HPAC
-
Самоцентрирующиеся SC-I
-
Модульные GT
-
Глобусные HHY
-
Лекальные QGG
-
Лекальные QKG
-
Модульные составные ZQ84
-
Гидравлические CHV
-
Самоцентрирующиеся двойные SMC
-
-
Кромкоискатели
-
Магнитные плиты
-
Центроискатели
-
Гайки для цанг
-
Ключи гаечные
-
Приспособления для оправок
-
Наборы прижимов
-
Расточные системы
-
Система нулевого базирования
-
Магнитные захваты
-
Поворотные столы
-
Аксессуары для станочной оснастки
-
Привязка по оси Z
-
Защитные вставки
-
-
Оснастка для токарных станков
-
Кулачки токарные
- Инструментальные блоки BOT
-
Токарные патроны
-
Центры токарные вращающиеся
- Центры вращающиеся
- Центры вращающиеся усиленные M11
- Центры вращающиеся облегченные
- Центры вращающиеся со сменными вставками
- Центры вращающиеся высокоскоростные
- Центры вращающиеся с твердосплавной вставкой
- Центры вращающиеся с удлиненной вершиной
- Центры вращающиеся усиленные
- Центры вращающиеся высокоточные
- Центры вращающиеся грибковые
-
Держатели осевого инструмента
-
Переходные втулки
-
Приспособления для расточки кулачков
-
Инструментальные блоки BMT
-
Центры токарные упорные
-
Сухари для токарных патронов
-
Инструментальные блоки VDI
-
Патроны цанговые
-
Цанги токарные
-
-
Измерительный инструмент
-
Станки
-
Станки ленточные по металлу
-
Лазерные граверы (маркировщики) по металлу
-
Токарные станки
-
Фрезерные станки
-
Заточные станки
-
Резьбонарезные манипуляторы
-
Электроэрозионные станки
-
Промышленные роботы
-
-
Мерч CNC66
-
Проволока, СОЖ, запчасти для электроэрозионных станков
-
Промышленная мебель
-
Запасные части для державок, резцов и фрез
-
Развертки
-
Упаковка
-
Зенковки
-
Плашки
-
Инструмент для снятия заусенцев
-
Корзина пуста
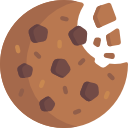
Мы используем файлы cookie для улучшения работы сайта и персонализации. Продолжая использовать сайт, вы соглашаетесь на сбор, обработку cookie-файлов и пользовательских данных с помощью Яндекс.Метрика, в соответствии с нашей Политикой конфиденциальности.