Особенности обработки порошковых металлов: предотвращение сколов и выбор инструмента
Порошковые металлы, полученные методом металлургии из порошков, обладают уникальными свойствами, которые требуют особого подхода при механической обработке. Их структура, состоящая из спеченных частиц, часто содержит поры, что делает материал менее плотным по сравнению с литыми или кованными аналогами.
Это влияет на выбор инструмента и режимов резания, так как неправильная обработка может привести к сколам, выкрашиванию кромок и снижению качества поверхности.
Для работы с такими материалами рекомендуется использовать твердосплавные инструменты с износостойкими покрытиями, такими как TiAlN или AlCrN. Эти покрытия повышают стойкость режущей кромки к абразивному износу, который часто возникает из-за наличия в материале оксидов и карбидов.
Угол заточки инструмента должен быть в пределах 85-90 градусов, что позволяет минимизировать риск сколов и обеспечить стабильное резание.
Скорость резания при обработке порошковых металлов обычно ниже, чем для традиционных сталей, и составляет 60-120 м/мин. Подача должна быть умеренной, в диапазоне 0,05-0,15 мм/об, чтобы избежать излишнего давления на заготовку.
При этом глубина резания не должна превышать 0,5 мм, так как большие нагрузки могут вызвать разрушение пористой структуры материала.
Охлаждение играет значительную роль в процессе обработки. Рекомендуется использовать смазочно-охлаждающие жидкости (СОЖ) на основе минеральных масел или эмульсий с добавлением противозадирных присадок. Это помогает снизить температуру в зоне резания и уменьшить износ инструмента. В случае с сухой обработкой, что иногда применяется для уменьшения загрязнения поверхности, необходимо обеспечить эффективное удаление стружки, чтобы избежать ее налипания на режущую кромку.
При фрезеровании деталей из порошковых металлов предпочтение стоит отдавать инструментам с переменным шагом зубьев. Это снижает вибрации и улучшает качество обработки. Диаметр фрезы должен быть на 10-15% меньше ширины обрабатываемой поверхности, чтобы минимизировать боковые нагрузки. Частота вращения шпинделя обычно составляет 800-1500 об/мин, а подача на зуб — 0,02-0,08 мм.
Для сверления отверстий в таких материалах лучше использовать спиральные сверла с углом при вершине 118-135 градусов. Это позволяет равномерно распределять нагрузку и избегать перегрева.
Скорость резания при сверлении должна быть в пределах 20-40 м/мин, а подача — 0,05-0,1 мм/об. При обработке глубоких отверстий рекомендуется периодически выводить сверло для удаления стружки и охлаждения.
Шлифование порошковых металлов требует особого внимания к выбору абразивного инструмента. Лучше всего подходят круги на керамической связке с зернистостью 46-80. Скорость вращения круга должна быть в диапазоне 25-35 м/с, а продольная подача — 0,5-1,5 м/мин. Это позволяет добиться высокой точности и минимизировать риск появления микротрещин на поверхности.
При токарной обработке важно правильно настроить геометрию резца. Угол в плане должен быть 45-60 градусов, а радиус при вершине — 0,4-0,8 мм. Это обеспечивает плавное врезание и снижает вероятность сколов. Для черновой обработки можно использовать резцы с отрицательным передним углом, а для чистовой — с положительным, чтобы улучшить качество поверхности.
В случае с тонкостенными деталями из порошковых металлов необходимо использовать минимальные усилия зажима, чтобы избежать деформации. Для этого подойдут мягкие кулачки патрона или специальные оправки.
При обработке таких заготовок рекомендуется снижать скорость резания на 20-30% по сравнению с обычными режимами.
Для повышения точности обработки стоит учитывать, что порошковые металлы могут иметь неоднородную плотность. Это требует тщательной настройки оборудования и контроля размеров на каждом этапе. Использование измерительных приборов с точностью до 0,01 мм поможет избежать брака.
При работе с деталями сложной формы, изготовленными методом порошковой металлургии, важно учитывать направление резания. Оно должно совпадать с направлением прессования порошка, чтобы минимизировать риск разрушения структуры материала. Это особенно актуально при обработке пазов, канавок и фасонных поверхностей.
Для повышения стойкости инструмента и улучшения качества обработки можно применять виброгасящие оправки и державки. Они снижают уровень вибраций, что особенно важно при работе с пористыми материалами.
Также стоит обратить внимание на балансировку инструмента, так как дисбаланс может привести к ускоренному износу и ухудшению качества поверхности.
При обработке порошковых металлов с высокой твердостью, таких как быстрорежущие стали или сплавы на основе карбидов, рекомендуется использовать инструменты с поликристаллическим алмазным (PCD) или кубическим нитридом бора (CBN) покрытием. Эти материалы обладают высокой износостойкостью и позволяют работать на повышенных скоростях резания.
Для контроля качества поверхности после обработки можно использовать профилометры или микроскопы. Среднее значение шероховатости Ra должно быть в пределах 0,8-1,6 мкм для большинства деталей.
Если требуется более высокая чистота поверхности, можно применить финишную обработку полировальными кругами с мелкозернистым абразивом.
При выборе режимов обработки стоит учитывать, что порошковые металлы могут иметь различную пористость — от 5 до 20%. Это влияет на теплопроводность материала и его способность рассеивать тепло, выделяемое в процессе резания.
Для материалов с высокой пористостью рекомендуется снижать скорость резания на 10-15% по сравнению с обычными режимами.
Для повышения эффективности обработки можно использовать ЧПУ-станки с адаптивным управлением. Они позволяют автоматически корректировать режимы резания в зависимости от нагрузки на инструмент, что особенно полезно при работе с неоднородными материалами. Это также помогает снизить риск поломки инструмента и повысить стабильность процесса.
При обработке порошковых металлов с добавлением меди или алюминия стоит учитывать, что эти материалы могут вызывать налипание стружки на режущую кромку. Для предотвращения этого можно использовать инструменты с полированными передними поверхностями или применять СОЖ с повышенной смазывающей способностью.
Для достижения высокой точности при обработке деталей из порошковых металлов рекомендуется использовать прецизионные станки с жесткой конструкцией. Это позволяет минимизировать вибрации и обеспечить стабильность размеров.
Также стоит обратить внимание на температурный режим в цеху, так как перепады температуры могут вызвать деформацию заготовок.
При работе с порошковыми металлами, содержащими твердые включения, такие как карбиды или нитриды, стоит использовать инструменты с повышенной ударной вязкостью. Это позволяет избежать выкрашивания режущей кромки и продлить срок службы инструмента.
Также рекомендуется применять инструменты с большим радиусом при вершине, чтобы распределить нагрузку более равномерно.
Для обработки деталей с высокой точностью размеров можно использовать шлифовальные круги с алмазным напылением. Они позволяют добиться шероховатости поверхности Ra до 0,2 мкм и обеспечивают высокую геометрическую точность. При этом скорость вращения круга должна быть в пределах 20-25 м/с, а подача — 0,1-0,3 мм/ход.
При обработке порошковых металлов с низкой теплопроводностью, таких как титановые сплавы, стоит уделить особое внимание охлаждению. Это поможет избежать перегрева инструмента и заготовки, что может привести к изменению структуры материала и снижению его прочности. Также рекомендуется использовать инструменты с повышенной стойкостью к высоким температурам.
Для повышения производительности при обработке порошковых металлов можно использовать многолезвийные инструменты, такие как фрезы с несколькими зубьями или сверла с внутренним подводом СОЖ. Это позволяет увеличить скорость резания и снизить время обработки без ущерба для качества.
При работе с деталями, изготовленными методом порошковой металлургии, стоит учитывать, что их механические свойства могут отличаться от свойств литых или кованых аналогов. Это требует тщательного подбора режимов обработки и инструмента, чтобы избежать брака и обеспечить высокое качество готовых изделий.
- На главную
-
Категории
-
Пластины твердосплавные
-
Пластины токарные
-
Пластины для внутреннего и наружного точения
-
Пластины резьбовые
-
Пластины резьбовые ISO
-
Пластины резьбовые трапецеидального профиля, угол 30 град.
-
Пластины резьбовые неполного профиля, угол 55 или 60 град.
-
Пластины резьбовые для нарезания трубной резьбы Whitworth, правые
-
Пластины резьбовые NPT (дюймовая коническая резьба c углом профиля 60 град. и конус 1:16)
-
Пластины резьбовые BSPT (Британский стандарт) полного профиля, угол 55 град.
-
Пластины резьбовые треугольного закругленного профиля
-
Пластины резьбовые UN (Американский стандарт) полного профиля, угол 60 град.
- Пластины резьбовые UN (Американский стандарт) полного профиля, угол 60 град.
- Панцирная трубная резьба Pg 80 град.
- Пластины резьбовые трапецеидального профиля, угол 30 град.
- Пластины резьбовые BSPT (Британский стандарт) полного профиля, угол 55 град.
- Пластины резьбовые NPT (дюймовая коническая резьба c углом профиля 60 град. и конус 1:16)
- Пластины резьбовые неполного профиля, угол 55 или 60 град.
- Упорная резьба SAGE 30 град.
-
-
Пластины отрезные и канавочные
-
TGF32
-
SP
-
MRMN
-
MG...N
- GER-C
- SP для стали
- SP для нержавеющей стали
-
QCMB
-
QPMB
- MGMN для стали
- MGMN для нержавеющей стали
- QPMB для стали
- QPMB для нержавеющей стали
- MRMN для стали
- ZP_S для нержавеющей стали
-
ZP_S
- QCMB для нержавеющей стали
- ZT_D для нержавеющей стали
-
ZT_D
- ZT_D для стали
- QCMB для стали
- TDC для нержавеющей стали
-
TDC
- QC_ для нержавеющей стали
-
QC
- QC_
- ZP_D для нержавеющей стали
-
ZP_D
- ZR_D для нержавеющей стали
-
ZR_D
- ZT_S для нержавеющей стали
-
ZT_S
- ZQMX для стали
-
ZQMX
- CTPA для нержавеющей стали
-
CTPA
- MGMN для чугуна
- MRMN для нержавеющей стали
- MRMN для чугуна
-
GEL-A/B
- GEL-A
-
GEL-A/B-R
-
GEL-C/D/E
- GEL-C
-
GEL-C/D/E-R
-
GER-A/B
- GER-A
-
GER-A/B-R
-
GER-C/D/E
-
GER-C/D/E-R
- MGMN
- MGGN
- MB
- ZTKS
- JRMN
- GK-R
- ZRFD
- KTMD
- KGT
- JSMN
- SPDR
-
-
-
Пластины фрезерные
-
Пластины для сверл
-
Лезвия для резьбофрез
-
Пластины со вставками PCBN
- Пластины для червячного зуба 40°
-
-
Фрезы
-
Фрезы монолитные
-
Концевые
-
HRC72
- HRC45
- HRC55
- HRC60
- HRC65
- HRC66
- HRC70
- HRC45
- HRC55
- HRC60
- HRC65
- HRC66
- HRC70
- HRC45
- HRC55
- HRC60
- HRC65
- HRC66
- HRC70
- HRC45
- HRC55
- HRC60
- HRC65
- HRC66
- HRC70
- HRC45
- HRC55
- HRC60
- HRC65
- HRC66
- HRC70
- HRC45
- HRC55
- HRC60
- HRC65
- HRC66
- HRC70
- HRC45
- HRC55
- HRC60
- HRC65
- HRC66
- HRC70
- HRC55
- HRC65
- HRC70
- HRC60
- HRC45
- HRC66
- HRC45
- HRC55
- HRC60
- HRC65
- HRC66
- HRC70
- HRC45
- HRC55
- HRC60
- HRC65
- HRC66
- HRC70
- HRC45
- HRC55
- HRC60
- HRC65
- HRC66
- HRC70
- HRC45
- HRC55
- HRC60
- HRC65
- HRC66
- HRC70
-
-
Радиусные
-
Сферические
-
Фасочные
-
Граверы
-
Дисковые
- Резьбофрезы
-
-
Фрезы со сменными пластинами
-
Фрезы дисковые
-
Фрезы концевые
-
ASM
-
BAP
- BMR
-
EMR
-
PE03
-
RB02
-
RB03
-
TEBL
-
ХК01
- ХК02
- SSM390
- EMP01
- AF06
- BAP
- EMR
- EMRW
- EXN03
- PE01
- PE02
- PE05
- R217.96
- RF01
- AF06
- BAP
- EMR
- EMRW
- EXN03
- PE01
- PE02
- PE05
- R217.96
- RF01
- AF06
- BAP
- EMR
- EMRW
- EXN03
- PE01
- PE02
- PE05
- R217.96
- RF01
- AF06
- BAP
- EMR
- EMRW
- EXN03
- PE01
- PE02
- PE05
- R217.96
- RF01
- AF06
- BAP
- EMR
- EMRW
- EXN03
- PE01
- PE02
- PE05
- R217.96
- RF01
- AF06
- BAP
- EMR
- EMRW
- EXN03
- PE01
- PE02
- PE05
- R217.96
- RF01
- AF06
- BAP
- EMR
- EMRW
- EXN03
- PE01
- PE02
- PE05
- R217.96
- RF01
- RF01
- EXN03
- PE02
- AF06
- R217.96
- EMRW
- EMR
- BAP
- PE01
- PE05
- AF06
- BAP
- EMR
- EMRW
- EXN03
- PE01
- PE02
- PE05
- R217.96
- RF01
- AF06
- BAP
- EMR
- EMRW
- EXN03
- PE01
- PE02
- PE05
- R217.96
- RF01
- AF06
- BAP
- EMR
- EMRW
- EXN03
- PE01
- PE02
- PE05
- R217.96
- RF01
- AF06
- BAP
- EMR
- EMRW
- EXN03
- PE01
- PE02
- PE05
- R217.96
- RF01
-
-
Фрезы резьбонарезные
-
Фрезы торцевые насадные
-
Фрезы фасочные
-
-
Фрезы со сменными головками
-
-
Метчики
-
Сверла
-
Ленточные пилы
-
Новое поступление (NEW!)
-
Державки токарные
-
Державки расточные
-
S...-SVJCR/S...-SVJCL
-
S...-DCLNR/S...-DCLNL
-
S...-DDUNR/S...-DDUNL
-
S...-DWLNR/S...-DWLNL
-
S...-MCKNR/S...-MCKNL
-
S...-MCLNR/S...-MCLNL
-
S...-MDQNR/S...-MDQNL
-
S...-MDUNR/S...-MDUNL
-
S...-MSKNR/S-...MSKNL
-
S...-MTJNR/S...-MTJNL
-
S...-MTQNR/S...-MTQNL
-
S...-MTUNR/S...-MTUNL
-
S...-MTFNR/S...-MTFNL
-
S...-MTWNR/S...-MTWNL
-
S...-MVQNR/S-...MVQNL
-
S...-MVUNR/S-...MVUNL
-
S...-MVWNR/S...-MVWNL
-
S...-MVXNR/S...-MVXNL
-
S...-MWLNR/S...-MWLNL
-
S...-PCLNR/S...-PCLNL
-
S...-PDSNR/S...-PDSNL
-
S...-PDUNR/S...-PDUNL
-
S...-PSKNR/S...-PSKNL
-
S...-PWLNR/S...-PWLNL
-
S...-PTFNR/S...-PTFNL
-
S...-SCKCR/S...-SCKCL
-
S...-SCLCR/S...-SCLCL
-
S...-SCLPR/S...-SCLPL
-
S...-SDQCR/S...-SDQCL
-
S...-SDUCR/S...-SDUCL
-
S...-SDZCR/S...-SDZCL
-
S...-SSSCR/S...-SSSCL
-
S...-SSKCR/S...-SSKCL
-
S...-STFCR/S-...STFCL
-
S...-STUCR/S-...STUCL
-
S...-SVUCR/S-...SVUCL
-
S...-SVUBR/S...-SVUBL
-
-
Державки проходные
-
CCLNR/CCLNL
-
CRDNN
-
CSDNN
-
CSKNR/CSKNL
-
CTJNR/CTJNL
-
DCBNR/DCBNL
-
DCKNR/DCKNL
-
DCLNR/DCLNL
-
DCMNN
-
DDJNR/DDJNL
-
DDPNN
-
DSSNR/DSSNL
-
DDQNR/DDQNL
-
DSBNR/DSBNL
-
DSDNN
-
DSKNR/DSKNL
-
DTFNR/DTFNL
-
DTGNR/DTGNL
-
DVJNR/DVJNL
-
DVVNN
-
DWLNR/DWLNL
-
ECLNR/ECLNL
-
EDJNR/EDJNL
-
EVJNR/EVJNL
-
EWLNR/EWLNL
-
MCBNR/MCBNL
-
MCKNR/MCKNL
-
MCLNR/MCLNL
-
MCMNN
-
MDJNR/MDJNL
-
MDPNN
-
MDQNR/MDQNL
-
MRDNN
-
MRGNR/MRGNL
-
MSBNR/MSBNL
-
MSDNN
-
MSKNR/MSKNL
-
MSSNR/MSSNL
-
MTENN
-
MTFNR/MTFNL
-
MTGNR/MTGNL
-
MTJNR/MTJNL
-
MTQNR/MTQNL
-
MVJNR/MVJNL
-
MVQNR/MVQNL
-
MVUNR/MVUNL
-
MVVNN
-
MWLNR/MWLNL
-
PWLNR/PWLNL
-
PCLNR/PCLNL
-
PDJNR/PDJNL
-
PRACR/PRACL
-
PRDCN
-
PCBNR/PCBNL
-
PRGCR/PRGCL
-
PSBNR/PSBNL
-
PSDNN
-
PSSNR/PSSNL
-
PTGNR/PTGNL
-
PTTNR/PTTNL
-
SCLCR/SCLCL
-
SDJCR/SDJCL
-
SDNCN
-
SRACR/SRACL
-
SRDCN
-
SSDCN
-
SSSCR/SSSCL
-
STFCR/STFCL
-
SVACR/SVACL
-
SVJBR/SVJBL
-
SVJCR/SVJCL
-
SVVBN
-
SVVCN
-
WTENN
-
WTJNR/WTJNL
-
WWLNR/WWLNL
-
PDNNR/PDNNL
-
SVHBR/SVHBL
-
PDNNN
-
PTFNR/PTFNL
-
SCACR/SCACL
-
SDACR/SDACL
-
SSBCR/SSBCL
-
SRGCR/SRGCL
-
SSKCR/SSKCL
-
STGCR/STGCL
-
SVABR/SVABL
-
SVQCR/SVQCL
-
SWACR/SWACL
-
WTQNR/WTQNL
-
-
Державки резьбовые
-
Державки отрезные, канавочные
-
Держатели отрезного лезвия
-
Лезвия отрезные
-
Мини-резцы твердосплавные
-
-
Оснастка для фрезерных станков
-
Фрезерные патроны
-
BT
-
BT-ER (для цанг ER)
-
BT-FMB (для насадных фрез)
-
BT-SCA (для дисковых фрез)
-
BT-D (тестовые оправки)
-
BT-SLN Weldon
-
BT-MTA (конус Морзе с лапкой)
-
BT-MTB (конус Морзе с резьбовым отверстием)
-
BT-DC (высокоскоростные патроны для цанг DC)
-
BT-APU
-
BT-SC (для цилиндрических цанг SC)
-
BT-GT (для резьбовых цанг GT12/24/42)
-
BT-TER (патроны с осевой компенсацией по длине для цанг ER)
-
BT-OZ(EOC) (для силовых цанг OZ)
-
BT-PHC (гидропластовые патроны)
-
-
Конус Морзе MTA/MTB
-
HSK
-
Цилиндрический хвостовик
-
NT
-
SK
-
SK-FMB (для насадных фрез)
-
SK-SLN (Weldon)
-
SK-TER (патроны с осевой компенсацией по длине для цанг ER)
-
SK-SC (для цилиндрических цанг SC)
-
SK-MTB (конус Морзе с резьбовым отверстием)
-
SK-MTA (конус Морзе с лапкой)
-
SK-ER (для цанг ER)
-
SK-GT (для резьбовых цанг GT12/24/42)
-
SK-OZ(EOC) (для силовых цанг OZ)
-
SK-APU (сверлильные быстрозажимные патроны)
-
SK-PHC (гидропластовые патроны)
-
-
-
Прихваты, прижимы, упоры
-
Цанги
-
Штревели
-
3D тестеры
-
Тиски станочные
-
Аксессуары и запчасти
- Силовые высокоточные VQC
-
640 Multitasking
-
Трехкулачковые NBK
-
Гидравлические DCV
-
Модульные двойные ZQ83
-
С регулируемым усилием зажима HPAC
-
Самоцентрирующиеся SC-I
-
Модульные GT
-
Глобусные HHY
-
Лекальные QGG
-
Лекальные QKG
-
Модульные составные ZQ84
-
Гидравлические CHV
-
Самоцентрирующиеся двойные SMC
-
-
Кромкоискатели
-
Магнитные плиты
-
Центроискатели
-
Гайки для цанг
-
Ключи гаечные
-
Приспособления для оправок
-
Наборы прижимов
-
Расточные системы
-
Система нулевого базирования
-
Магнитные захваты
-
Поворотные столы
-
Аксессуары для станочной оснастки
-
Привязка по оси Z
-
Защитные вставки
-
-
Оснастка для токарных станков
-
Кулачки токарные
- Инструментальные блоки BOT
-
Токарные патроны
-
Центры токарные вращающиеся
- Центры вращающиеся
- Центры вращающиеся усиленные M11
- Центры вращающиеся облегченные
- Центры вращающиеся со сменными вставками
- Центры вращающиеся высокоскоростные
- Центры вращающиеся с твердосплавной вставкой
- Центры вращающиеся с удлиненной вершиной
- Центры вращающиеся усиленные
- Центры вращающиеся высокоточные
- Центры вращающиеся грибковые
-
Держатели осевого инструмента
-
Переходные втулки
-
Приспособления для расточки кулачков
-
Инструментальные блоки BMT
-
Центры токарные упорные
-
Сухари для токарных патронов
-
Инструментальные блоки VDI
-
Патроны цанговые
-
Цанги токарные
-
-
Измерительный инструмент
-
Станки
-
Станки ленточные по металлу
-
Лазерные граверы (маркировщики) по металлу
-
Токарные станки
-
Фрезерные станки
-
Заточные станки
-
Резьбонарезные манипуляторы
-
Электроэрозионные станки
-
Промышленные роботы
-
-
Мерч CNC66
-
Проволока, СОЖ, запчасти для электроэрозионных станков
-
Промышленная мебель
-
Запасные части для державок, резцов и фрез
-
Развертки
-
Упаковка
-
Зенковки
-
Плашки
-
Инструмент для снятия заусенцев
-
Корзина пуста
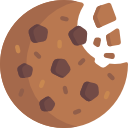
Мы используем файлы cookie для улучшения работы сайта и персонализации. Продолжая использовать сайт, вы соглашаетесь на сбор, обработку cookie-файлов и пользовательских данных с помощью Яндекс.Метрика, в соответствии с нашей Политикой конфиденциальности.