Электронно-лучевая сварка в металлообработке
Электронно-лучевая сварка (ЭЛС) была изобретена в 1950-х годах немецким физиком Карлом-Хайнцем Штайгервальдом.
Он обнаружил, что сфокусированный пучок электронов способен плавить и соединять металлы в вакууме. Первые промышленные установки для ЭЛС появились в 1960-х годах и сразу нашли применение в аэрокосмической отрасли для сварки титановых сплавов.
Физические основы процесса
Сущность процесса ЭЛС заключается в использовании кинетической энергии ускоренных электронов для нагрева и плавления свариваемых металлов. Электроны генерируются электронной пушкой и ускоряются в электрическом поле до скоростей, составляющих 30-70% скорости света.
При столкновении с металлом кинетическая энергия электронов преобразуется в тепловую, вызывая локальный нагрев и плавление. Процесс происходит в вакуумной камере для предотвращения рассеивания электронного пучка.
Техника ЭЛС включает несколько ключевых этапов. Сначала детали тщательно очищаются и обезжириваются, затем помещаются в вакуумную камеру. После откачки воздуха из камеры включается электронная пушка, генерирующая пучок электронов.
С помощью электромагнитных линз пучок фокусируется в точку диаметром 0,2-0,5 мм. Перемещение пучка вдоль линии сварки осуществляется либо движением самих деталей, либо отклонением пучка магнитным полем. Глубина проплавления регулируется мощностью пучка и скоростью сварки.
Основными параметрами режима ЭЛС являются ускоряющее напряжение (обычно 30-200 кВ), ток пучка (10-1000 мА), скорость сварки (до 50 м/мин), фокусировка пучка. От правильного выбора этих параметров зависит качество сварного соединения.
Например, повышение ускоряющего напряжения увеличивает глубину проплавления, но может вызвать образование пор. Увеличение тока пучка повышает производительность, но может привести к перегреву металла. Оптимальные режимы подбираются экспериментально для каждого конкретного случая.
При ЭЛС возможно получение различных типов сварных соединений: стыковых, угловых, тавровых, нахлесточных. Наиболее распространены стыковые соединения, обеспечивающие максимальную прочность шва.
Для их получения кромки деталей должны быть подготовлены с высокой точностью, зазор не должен превышать 0,1 мм. Угловые и тавровые соединения требуют точного позиционирования электронного пучка относительно стыка. Нахлесточные соединения применяются реже из-за сложности контроля глубины проплавления.
Особенности электронно-лучевой сварки
Особенностью ЭЛС является формирование узкого и глубокого шва с соотношением глубины к ширине до 20:1. Это позволяет сваривать за один проход металл толщиной до 200 мм. Высокая концентрация энергии в пучке (до 108 Вт/см2) обеспечивает минимальное тепловложение в металл.
Зона термического влияния при ЭЛС в 3-5 раз меньше, чем при дуговой сварке. Это особенно важно при сварке термически упрочненных и закаленных сталей, когда требуется сохранить исходную структуру и свойства металла.
К достоинствам ЭЛС относятся высокая производительность, возможность сварки тугоплавких и активных металлов, отсутствие необходимости в присадочном материале, высокая чистота процесса.
Сварные швы, полученные ЭЛС, отличаются высоким качеством, отсутствием пор и шлаковых включений. Возможность программирования траектории пучка позволяет автоматизировать процесс и получать швы сложной конфигурации.
Однако ЭЛС имеет и ряд недостатков. Главный из них - необходимость в вакуумной камере, что ограничивает размеры свариваемых изделий. Высокая стоимость оборудования и сложность его обслуживания также сдерживают широкое распространение технологии.
Кроме того, при ЭЛС возможно образование дефектов в виде подрезов, корневых пустот, выплесков металла. Для их предотвращения требуется тщательный подбор режимов сварки и высокая квалификация персонала.
Сравнение с другими технологиями сварки
По сравнению с лазерной сваркой, ЭЛС обладает рядом преимуществ. Коэффициент полезного действия электронного пучка (до 90%) значительно выше, чем у лазерного луча (10-20%). Это обеспечивает более высокую производительность и меньшее энергопотребление.
ЭЛС позволяет получать более глубокие швы - до 200 мм за один проход против 20-30 мм у лазерной сварки. Кроме того, электронный пучок легче фокусируется и отклоняется, что упрощает автоматизацию процесса.
В сравнении с дуговой сваркой ЭЛС обеспечивает значительно меньшее тепловложение в металл. Это позволяет сваривать материалы, чувствительные к перегреву, например, высокопрочные алюминиевые сплавы.
Отсутствие газовой среды и флюсов исключает загрязнение металла шва примесями. Швы, полученные ЭЛС, не требуют механической обработки, что снижает трудоемкость изготовления изделий.
Сферы и перспективы применения ЭЛС
ЭЛС нашла широкое применение в авиакосмической промышленности для сварки корпусов двигателей, топливных баков, элементов конструкции летательных аппаратов. В атомной энергетике эта технология используется для изготовления тепловыделяющих элементов и сварки трубопроводов.
В автомобилестроении ЭЛС применяется для сварки коробок передач, карданных валов, элементов кузова. Электронно-лучевая сварка позволяет получать высококачественные соединения в приборостроении, электронике, медицинской технике.
Развитие ЭЛС идет по пути создания многолучевых систем, позволяющих одновременно сваривать несколько швов. Ведутся работы по совмещению ЭЛС с другими технологиями, например, с ультразвуковой обработкой для улучшения структуры шва. Разрабатываются методы неразрушающего контроля качества сварных соединений непосредственно в процессе сварки.
Важным направлением является создание мобильных установок ЭЛС для работы вне вакуумной камеры. Это позволит расширить область применения технологии на крупногабаритные изделия и ремонтные работы. Ведутся исследования по использованию плазменных источников электронов, которые могут работать при более высоком остаточном давлении, чем традиционные термокатодные пушки.
Электронно-лучевая сварка продолжает оставаться одной из наиболее перспективных технологий соединения металлов. Ее дальнейшее развитие связано с совершенствованием систем управления пучком, разработкой новых типов электронных пушек, созданием гибридных технологий. Все это позволит расширить возможности ЭЛС и сделать ее более доступной для широкого круга предприятий.
- На главную
-
Категории
-
Пластины
-
Пластины токарные
-
Пластины для внутреннего и наружного точения
-
Пластины резьбовые
-
Пластины резьбовые ISO
-
Пластины резьбовые трапецеидального профиля, угол 30 град.
-
Пластины резьбовые неполного профиля, угол 55 или 60 град.
-
Пластины резьбовые для нарезания трубной резьбы Whitworth, правые
-
Пластины резьбовые NPT (дюймовая коническая резьба c углом профиля 60 град. и конус 1:16)
-
Пластины резьбовые BSPT (Британский стандарт) полного профиля, угол 55 град.
-
Пластины резьбовые треугольного закругленного профиля
-
Пластины резьбовые UN (Американский стандарт) полного профиля, угол 60 град.
-
-
Пластины отрезные и канавочные
-
TGF32
-
SP
-
MRMN
-
MG...N
- GER-C
- SP для стали
- SP для нержавеющей стали
-
QCMB
-
QPMB
- MGMN для стали
- MGMN для нержавеющей стали
- QPMB для стали
- QPMB для нержавеющей стали
- MRMN для стали
- ZP_S для нержавеющей стали
-
ZP_S
- QCMB для нержавеющей стали
- ZT_D для нержавеющей стали
-
ZT_D
- ZT_D для стали
- QCMB для стали
- TDC для нержавеющей стали
-
TDC
- QC_ для нержавеющей стали
-
QC
- QC_
- ZP_D для нержавеющей стали
-
ZP_D
- ZR_D для нержавеющей стали
-
ZR_D
- ZT_S для нержавеющей стали
-
ZT_S
- ZQMX для стали
-
ZQMX
- CTPA для нержавеющей стали
-
CTPA
- MGMN для чугуна
- MRMN для нержавеющей стали
- MRMN для чугуна
-
GEL-A/B
- GEL-A
-
GEL-A/B-R
-
GEL-C/D/E
- GEL-C
-
GEL-C/D/E-R
-
GER-A/B
- GER-A
-
GER-A/B-R
-
GER-C/D/E
-
GER-C/D/E-R
-
-
-
Пластины фрезерные
-
Пластины для свёрл
-
Лезвия для резьбофрез
-
Пластины со вставками PCBN
-
-
Фрезы
-
Метчики
-
Сверла
-
Ленточные пилы
-
Новое поступление (NEW!)
-
Державки токарные
-
Державки расточные
-
S...-SVJCR/S...-SVJCL
-
S...-DCLNR/S...-DCLNL
-
S...-DDUNR/S...-DDUNL
-
S...-DWLNR/S...-DWLNL
-
S...-MCKNR/S...-MCKNL
-
S...-MCLNR/S...-MCLNL
-
S...-MDQNR/S...-MDQNL
-
S...-MDUNR/S...-MDUNL
-
S...-MSKNR/S-...MSKNL
-
S...-MTJNR/S...-MTJNL
-
S...-MTQNR/S...-MTQNL
-
S...-MTUNR/S...-MTUNL
-
S...-MTFNR/S...-MTFNL
-
S...-MTWNR/S...-MTWNL
-
S...-MVQNR/S-...MVQNL
-
S...-MVUNR/S-...MVUNL
-
S...-MVWNR/S...-MVWNL
-
S...-MVXNR/S...-MVXNL
-
S...-MWLNR/S...-MWLNL
-
S...-PCLNR/S...-PCLNL
-
S...-PDSNR/S...-PDSNL
-
S...-PDUNR/S...-PDUNL
-
S...-PSKNR/S...-PSKNL
-
S...-PWLNR/S...-PWLNL
-
S...-PTFNR/S...-PTFNL
-
S...-SCKCR/S...-SCKCL
-
S...-SCLCR/S...-SCLCL
-
S...-SCLPR/S...-SCLPL
-
S...-SDQCR/S...-SDQCL
-
S...-SDUCR/S...-SDUCL
-
S...-SDZCR/S...-SDZCL
-
S...-SSSCR/S...-SSSCL
-
S...-SSKCR/S...-SSKCL
-
S...-STFCR/S-...STFCL
-
S...-STUCR/S-...STUCL
-
S...-SVUCR/S-...SVUCL
-
S...-SVUBR/S...-SVUBL
-
-
Державки проходные
-
CCLNR/CCLNL
-
CRDNN
-
CSDNN
-
CSKNR/CSKNL
-
CTJNR/CTJNL
-
DCBNR/DCBNL
-
DCKNR/DCKNL
-
DCLNR/DCLNL
-
DCMNN
-
DDJNR/DDJNL
-
DDPNN
-
DSSNR/DSSNL
-
DDQNR/DDQNL
-
DSBNR/DSBNL
-
DSDNN
-
DSKNR/DSKNL
-
DTFNR/DTFNL
-
DTGNR/DTGNL
-
DVJNR/DVJNL
-
DVVNN
-
DWLNR/DWLNL
-
ECLNR/ECLNL
-
EDJNR/EDJNL
-
EVJNR/EVJNL
-
EWLNR/EWLNL
-
MCBNR/MCBNL
-
MCKNR/MCKNL
-
MCLNR/MCLNL
-
MCMNN
-
MDJNR/MDJNL
-
MDPNN
-
MDQNR/MDQNL
-
MRDNN
-
MRGNR/MRGNL
-
MSBNR/MSBNL
-
MSDNN
-
MSKNR/MSKNL
-
MSSNR/MSSNL
-
MTENN
-
MTFNR/MTFNL
-
MTGNR/MTGNL
-
MTJNR/MTJNL
-
MTQNR/MTQNL
-
MVJNR/MVJNL
-
MVQNR/MVQNL
-
MVUNR/MVUNL
-
MVVNN
-
MWLNR/MWLNL
-
PWLNR/PWLNL
-
PCLNR/PCLNL
-
PDJNR/PDJNL
-
PRACR/PRACL
-
PRDCN
-
PCBNR/PCBNL
-
PRGCR/PRGCL
-
PSBNR/PSBNL
-
PSDNN
-
PSSNR/PSSNL
-
PTGNR/PTGNL
-
PTTNR/PTTNL
-
SCLCR/SCLCL
-
SDJCR/SDJCL
-
SDNCN
-
SRACR/SRACL
-
SRDCN
-
SSDCN
-
SSSCR/SSSCL
-
STFCR/STFCL
-
SVACR/SVACL
-
SVJBR/SVJBL
-
SVJCR/SVJCL
-
SVVBN
-
SVVCN
-
WTENN
-
WTJNR/WTJNL
-
WWLNR/WWLNL
-
PDNNR/PDNNL
-
SVHBR/SVHBL
-
PDNNN
-
PTFNR/PTFNL
-
SCACR/SCACL
-
SDACR/SDACL
-
SSBCR/SSBCL
-
SRGCR/SRGCL
-
SSKCR/SSKCL
-
STGCR/STGCL
-
SVABR/SVABL
-
SVQCR/SVQCL
-
SWACR/SWACL
-
WTQNR/WTQNL
-
-
Державки резьбовые
-
Державки отрезные, канавочные
-
Держатели отрезного лезвия
-
Лезвия отрезные
-
Мини-резцы твердосплавные
-
-
Оснастка для фрезерных станков
-
Фрезерные патроны
-
BT
-
BT-ER (для цанг ER)
-
BT-FMB (для насадных фрез)
-
BT-SCA (для дисковых фрез)
-
BT-D (тестовые оправки)
-
BT-SLN Weldon
-
BT-MTA (конус Морзе с лапкой)
-
BT-MTB (конус Морзе с резьбовым отверстием)
-
BT-DC (высокоскоростные патроны для цанг DC)
-
BT-APU
-
BT-SC (для цилиндрических цанг SC)
-
BT-GT (для резьбовых цанг GT12/24/42)
-
BT-TER (патроны с осевой компенсацией по длине для цанг ER)
-
BT-OZ(EOC) (для силовых цанг OZ)
-
BT-PHC (гидропластовые патроны)
-
-
Конус Морзе MTA/MTB
-
HSK
-
Цилиндрический хвостовик
-
NT
-
SK
-
SK-FMB (для насадных фрез)
-
SK-SLN (Weldon)
-
SK-TER (патроны с осевой компенсацией по длине для цанг ER)
-
SK-SC (для цилиндрических цанг SC)
-
SK-MTB (конус Морзе с резьбовым отверстием)
-
SK-MTA (конус Морзе с лапкой)
-
SK-ER (для цанг ER)
-
SK-GT (для резьбовых цанг GT12/24/42)
-
SK-OZ(EOC) (для силовых цанг OZ)
-
SK-APU (сверлильные быстрозажимные патроны)
-
SK-PHC (гидропластовые патроны)
-
-
-
Прихваты, прижимы, упоры
-
Цанги
-
Штревели
-
3D тестеры
-
Тиски станочные
-
Аксессуары и запчасти
- Силовые высокоточные VQC
-
640 Multitasking
-
Трехкулачковые NBK
-
Гидравлические DCV
-
Модульные двойные ZQ83
-
С регулируемым усилием зажима HPAC
-
Самоцентрирующиеся SC-I
-
Модульные GT
-
Глобусные HHY
-
Лекальные QGG
-
Лекальные QKG
-
Модульные составные ZQ84
-
Гидравлические CHV
-
Самоцентрирующиеся двойные SMC
-
-
Кромкоискатели
-
Магнитные плиты
-
Центроискатели
-
Гайки для цанг
-
Ключи гаечные
-
Приспособления для оправок
-
Наборы прижимов
-
Расточные системы
-
Система нулевого базирования
-
Магнитные захваты
-
Поворотные столы
-
Аксессуары для станочной оснастки
-
Привязка по оси Z
-
-
Оснастка для токарных станков
-
Кулачки токарные
- Инструментальные блоки BOT
-
Токарные патроны
-
Центры токарные вращающиеся
- Центры вращающиеся
- Центры вращающиеся усиленные M11
- Центры вращающиеся облегченные
- Центры вращающиеся со сменными вставками
- Центры вращающиеся высокоскоростные
- Центры вращающиеся с твердосплавной вставкой
- Центры вращающиеся с удлиненной вершиной
- Центры вращающиеся усиленные
- Центры вращающиеся высокоточные
- Центры вращающиеся грибковые
-
Держатели осевого инструмента
-
Переходные втулки
-
Приспособления для расточки кулачков
-
Инструментальные блоки BMT
-
Центры токарные упорные
-
Сухари для токарных патронов
-
Инструментальные блоки VDI
-
Патроны цанговые
-
Цанги токарные
-
-
Измерительный инструмент
-
Станки
-
Станки ленточные по металлу
-
Лазерные граверы (маркировщики) по металлу
-
Токарные станки
-
Фрезерные станки
-
Заточные станки
-
Резьбонарезные манипуляторы
-
Электроэрозионные станки
-
Промышленные роботы
-
-
Мерч CNC66
-
Проволока, СОЖ, запчасти для электроэрозионных станков
-
Промышленная мебель
-
Запасные части для державок, резцов и фрез
-
Развертки
-
Упаковка
-
Зенковки
-
Плашки
-
Инструмент для снятия заусенцев
- выгрузка
-
Корзина пуста
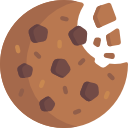
Мы используем файлы cookie для улучшения работы сайта и персонализации. Продолжая использовать сайт, вы соглашаетесь на сбор, обработку cookie-файлов и пользовательских данных с помощью Яндекс.Метрика, в соответствии с нашей Политикой конфиденциальности.