Техника безопасной рубки толстого листового металла зубилом
Работа с толстым металлом требует точного подбора инструмента. Для листов толщиной более 3 мм применяют зубило с шириной режущей кромки 16–25 мм и углом заточки 60–70°. Более твердые сплавы, такие как сталь 45 или 65Г, диктуют увеличение угла до 75–80° для снижения риска затупления.
Перед началом резки заготовку фиксируют в тисках с усилием не менее 150 Н·м, чтобы исключить вибрацию. Лист располагают так, чтобы место реза находилось на расстоянии 2–3 мм от губок – это предотвращает деформацию кромки. При отсутствии тисков используют струбцины, закрепляя деталь на массивной плите.
Угол наклона зубила влияет на эффективность рубки. Оптимальное положение – 5–10° от вертикали в сторону движения. Слишком острый наклон приводит к заклиниванию, а прямой удар снижает скорость работы. Для мягких металлов, таких как алюминий или медь, допустимо увеличение угла до 15°.
Сила удара подбирается в зависимости от толщины материала. При работе с листом 4–6 мм достаточно усилия 80–100 Дж, создаваемого молотком массой 400–600 г. Для сталей толщиной 8–10 мм требуется энергия 120–150 Дж, что достигается инструментом весом 800–1000 г. Частота ударов не должна превышать 60 в минуту – это позволяет контролировать процесс.
Траектория движения инструмента должна быть прямолинейной, без бокового смещения. Каждый последующий удар перекрывает предыдущую вырубку на 30–40% ширины кромки. В случае образования заусенцев их сразу удаляют напильником с зернистостью 100–120 мкм.
Охлаждение зоны реза продлевает срок службы зубила. Для этого используют эмульсии на основе минерального масла с концентрацией 5–7%. В домашних условиях подойдет обычная вода, но ее применение увеличивает риск коррозии.
Твердость рабочей части инструмента должна на 15–20% превышать аналогичный показатель металла. Для проверки используют напильник – он не должен оставлять следов на правильно закаленном зубиле. Заточку выполняют на абразивном круге с зернистостью 40–50 мкм, контролируя температуру, чтобы избежать отпуска стали.
При рубке длинных кромок делают насечки через каждые 20–30 мм, затем соединяют их сплошным резом. Это снижает нагрузку на инструмент и уменьшает вероятность сколов. Для криволинейных резов применяют зубила с радиусной кромкой шириной 6–10 мм.
Износ режущей части определяют по увеличению усилия при ударе на 25–30%. Своевременная заточка восстанавливает геометрию – ширина фаски не должна превышать 1,5 мм.
Работа с нержавеющими сталями требует особого подхода. Из-за высокой вязкости материала угол заточки увеличивают до 85°, а частоту ударов снижают вдвое. Для предотвращения наклепа используют охлаждающие пасты на основе графита.
Чугун рубится при температуре не ниже +15°С – в холодном состоянии он склонен к растрескиванию. Первые удары наносят с минимальной силой, постепенно увеличивая энергию. Угол наклона зубила поддерживают в пределах 3–5° для чистого скола.
Медь и ее сплавы требуют частой заточки инструмента – каждые 10–15 минут работы. Ширина режущей кромки не должна превышать 12 мм из-за высокой пластичности материала.
Для контроля глубины реза используют шаблоны из мягкой стали. Их устанавливают параллельно линии разметки с отступом 0,5 мм. Это позволяет сохранить геометрию при обработке ответственных деталей.
Вибрация – основной враг качественной рубки. Ее снижают, применяя резиновые прокладки под заготовку толщиной 8–10 мм. В производственных условиях используют магнитные плиты с силой притяжения не менее 0,5 МПа.
Скорость движения инструмента зависит от твердости металла. Для низкоуглеродистых сталей оптимально 0,3–0,5 м/мин, для инструментальных сплавов – не более 0,2 м/мин. Превышение этих значений ведет к перегреву кромки.
После завершения работ режущую часть покрывают тонким слоем консервационной смазки. Хранение инструмента в условиях влажности выше 70% требует применения силикагелевых осушителей.
Точность рубки проверяют щупом 0,1 мм – зазор между шаблоном и кромкой не должен превышать это значение. Для финишной доводки применяют бархатные напильники с насечкой №4–5.
Радиус скругления режущей кромки не должен превышать 0,2 мм. Контроль осуществляют с помощью радиусного шаблона. Превышение параметра ведет к увеличению усилия резания на 40–50%.
При обработке пакета листов их стягивают болтами М8–М10 с шагом 150–200 мм. Это предотвращает смещение слоев относительно друг друга. Смазка стыков графитовой пастой облегчает разделение деталей после рубки.
Термообработанные стали требуют предварительного отжига в зоне реза. Нагрев до 600–650°С снижает твердость на 30%, что значительно облегчает процесс. Температуру контролируют термокрасками, меняющими цвет при достижении заданных значений.
Для вырубки отверстий диаметром до 20 мм применяют зубила с выпуклой режущей частью. Первый удар наносят под углом 45° к поверхности, затем постепенно выводят инструмент в вертикальное положение.
Износостойкость повышают нанесением на рабочую часть тугоплавких покрытий. Карбид вольфрама толщиной 50–60 мкм увеличивает ресурс в 2–2,5 раза при работе с легированными сталями.
Остаточные напряжения в металле после рубки снимают локальным нагревом до 200–250°С с последующим медленным охлаждением. Это особенно актуально для деталей, подвергающихся динамическим нагрузкам.
Шум при работе достигает 110 дБ, поэтому используют противошумные вкладыши с коэффициентом поглощения не менее 25 дБ. Это соответствует требованиям ГОСТ Р 12.4.211–99.
Для маркировки линии реза применяют кернер с углом при вершине 90°. Глубина лунок должна составлять 0,3–0,5 мм при шаге 5–7 мм. Это предотвращает соскальзывание инструмента при первых ударах.
Стойкость зубила из инструментальной стали У8 составляет 3–4 часа непрерывной работы. Быстрорежущие марки Р6М5 увеличивают этот показатель до 6–8 часов при обработке конструкционных сталей.
При рубке под прессом усилие рассчитывают по формуле P=kSσ, где k=1,2–1,5 – коэффициент запаса, S – площадь сечения, σ – предел прочности. Для стали Ст3 усилие составляет 400–450 Н на 1 мм толщины.
Овальность отверстий после вырубки не должна превышать 0,05D, где D – номинальный диаметр. Контроль осуществляют нутромером с точностью 0,01 мм.
Для уменьшения припуска под механическую обработку применяют зубила с направляющими роликами. Они позволяют выдерживать допуск ±0,2 мм при толщине металла до 10 мм.
Антикоррозионную обработку кромок выполняют сразу после рубки. Фосфатирование в течение 15–20 минут создает защитный слой толщиной 5–7 мкм.
Твердомер Rockwell показывает значение HRC 58–62 для правильно закаленного инструмента. Падение показателя ниже HRC 52 свидетельствует о необходимости переточки.
Работа с хрупкими материалами, такими как серый чугун, требует уменьшения угла заточки до 50–55°. Это снижает вероятность образования трещин по линии реза.
Для контроля прямолинейности используют поверочную линейку класса 0. Зазор не должен превышать 0,1 мм на длине 300 мм.
Смазочно-охлаждающие жидкости подают со скоростью 0,5–0,8 л/мин. Это обеспечивает эффективное теплоотведение без разбрызгивания.
- На главную
-
Категории
-
Пластины твердосплавные
-
Пластины токарные
-
Пластины для внутреннего и наружного точения
-
Пластины резьбовые
-
Пластины резьбовые ISO
-
Пластины резьбовые трапецеидального профиля, угол 30 град.
-
Пластины резьбовые неполного профиля, угол 55 или 60 град.
-
Пластины резьбовые для нарезания трубной резьбы Whitworth, правые
-
Пластины резьбовые NPT (дюймовая коническая резьба c углом профиля 60 град. и конус 1:16)
-
Пластины резьбовые BSPT (Британский стандарт) полного профиля, угол 55 град.
-
Пластины резьбовые треугольного закругленного профиля
-
Пластины резьбовые UN (Американский стандарт) полного профиля, угол 60 град.
- Пластины резьбовые UN (Американский стандарт) полного профиля, угол 60 град.
- Панцирная трубная резьба Pg 80 град.
- Пластины резьбовые трапецеидального профиля, угол 30 град.
- Пластины резьбовые BSPT (Британский стандарт) полного профиля, угол 55 град.
- Пластины резьбовые NPT (дюймовая коническая резьба c углом профиля 60 град. и конус 1:16)
- Пластины резьбовые неполного профиля, угол 55 или 60 град.
- Упорная резьба SAGE 30 град.
-
-
Пластины отрезные и канавочные
-
TGF32
-
SP
-
MRMN
-
MG...N
- GER-C
- SP для стали
- SP для нержавеющей стали
-
QCMB
-
QPMB
- MGMN для стали
- MGMN для нержавеющей стали
- QPMB для стали
- QPMB для нержавеющей стали
- MRMN для стали
- ZP_S для нержавеющей стали
-
ZP_S
- QCMB для нержавеющей стали
- ZT_D для нержавеющей стали
-
ZT_D
- ZT_D для стали
- QCMB для стали
- TDC для нержавеющей стали
-
TDC
- QC_ для нержавеющей стали
-
QC
- QC_
- ZP_D для нержавеющей стали
-
ZP_D
- ZR_D для нержавеющей стали
-
ZR_D
- ZT_S для нержавеющей стали
-
ZT_S
- ZQMX для стали
-
ZQMX
- CTPA для нержавеющей стали
-
CTPA
- MGMN для чугуна
- MRMN для нержавеющей стали
- MRMN для чугуна
-
GEL-A/B
- GEL-A
-
GEL-A/B-R
-
GEL-C/D/E
- GEL-C
-
GEL-C/D/E-R
-
GER-A/B
- GER-A
-
GER-A/B-R
-
GER-C/D/E
-
GER-C/D/E-R
- MGMN
- MGGN
- MB
- ZTKS
- JRMN
- GK-R
- ZRFD
- KTMD
- KGT
- JSMN
- SPDR
-
-
-
Пластины фрезерные
-
Пластины для сверл
-
Лезвия для резьбофрез
-
Пластины со вставками PCBN
- Пластины для червячного зуба 40°
-
-
Фрезы
-
Метчики
-
Сверла
-
Ленточные пилы
-
Новое поступление (NEW!)
-
Державки токарные
-
Державки расточные
-
S...-SVJCR/S...-SVJCL
-
S...-DCLNR/S...-DCLNL
-
S...-DDUNR/S...-DDUNL
-
S...-DWLNR/S...-DWLNL
-
S...-MCKNR/S...-MCKNL
-
S...-MCLNR/S...-MCLNL
-
S...-MDQNR/S...-MDQNL
-
S...-MDUNR/S...-MDUNL
-
S...-MSKNR/S-...MSKNL
-
S...-MTJNR/S...-MTJNL
-
S...-MTQNR/S...-MTQNL
-
S...-MTUNR/S...-MTUNL
-
S...-MTFNR/S...-MTFNL
-
S...-MTWNR/S...-MTWNL
-
S...-MVQNR/S-...MVQNL
-
S...-MVUNR/S-...MVUNL
-
S...-MVWNR/S...-MVWNL
-
S...-MVXNR/S...-MVXNL
-
S...-MWLNR/S...-MWLNL
-
S...-PCLNR/S...-PCLNL
-
S...-PDSNR/S...-PDSNL
-
S...-PDUNR/S...-PDUNL
-
S...-PSKNR/S...-PSKNL
-
S...-PWLNR/S...-PWLNL
-
S...-PTFNR/S...-PTFNL
-
S...-SCKCR/S...-SCKCL
-
S...-SCLCR/S...-SCLCL
-
S...-SCLPR/S...-SCLPL
-
S...-SDQCR/S...-SDQCL
-
S...-SDUCR/S...-SDUCL
-
S...-SDZCR/S...-SDZCL
-
S...-SSSCR/S...-SSSCL
-
S...-SSKCR/S...-SSKCL
-
S...-STFCR/S-...STFCL
-
S...-STUCR/S-...STUCL
-
S...-SVUCR/S-...SVUCL
-
S...-SVUBR/S...-SVUBL
-
-
Державки проходные
-
CCLNR/CCLNL
-
CRDNN
-
CSDNN
-
CSKNR/CSKNL
-
CTJNR/CTJNL
-
DCBNR/DCBNL
-
DCKNR/DCKNL
-
DCLNR/DCLNL
-
DCMNN
-
DDJNR/DDJNL
-
DDPNN
-
DSSNR/DSSNL
-
DDQNR/DDQNL
-
DSBNR/DSBNL
-
DSDNN
-
DSKNR/DSKNL
-
DTFNR/DTFNL
-
DTGNR/DTGNL
-
DVJNR/DVJNL
-
DVVNN
-
DWLNR/DWLNL
-
ECLNR/ECLNL
-
EDJNR/EDJNL
-
EVJNR/EVJNL
-
EWLNR/EWLNL
-
MCBNR/MCBNL
-
MCKNR/MCKNL
-
MCLNR/MCLNL
-
MCMNN
-
MDJNR/MDJNL
-
MDPNN
-
MDQNR/MDQNL
-
MRDNN
-
MRGNR/MRGNL
-
MSBNR/MSBNL
-
MSDNN
-
MSKNR/MSKNL
-
MSSNR/MSSNL
-
MTENN
-
MTFNR/MTFNL
-
MTGNR/MTGNL
-
MTJNR/MTJNL
-
MTQNR/MTQNL
-
MVJNR/MVJNL
-
MVQNR/MVQNL
-
MVUNR/MVUNL
-
MVVNN
-
MWLNR/MWLNL
-
PWLNR/PWLNL
-
PCLNR/PCLNL
-
PDJNR/PDJNL
-
PRACR/PRACL
-
PRDCN
-
PCBNR/PCBNL
-
PRGCR/PRGCL
-
PSBNR/PSBNL
-
PSDNN
-
PSSNR/PSSNL
-
PTGNR/PTGNL
-
PTTNR/PTTNL
-
SCLCR/SCLCL
-
SDJCR/SDJCL
-
SDNCN
-
SRACR/SRACL
-
SRDCN
-
SSDCN
-
SSSCR/SSSCL
-
STFCR/STFCL
-
SVACR/SVACL
-
SVJBR/SVJBL
-
SVJCR/SVJCL
-
SVVBN
-
SVVCN
-
WTENN
-
WTJNR/WTJNL
-
WWLNR/WWLNL
-
PDNNR/PDNNL
-
SVHBR/SVHBL
-
PDNNN
-
PTFNR/PTFNL
-
SCACR/SCACL
-
SDACR/SDACL
-
SSBCR/SSBCL
-
SRGCR/SRGCL
-
SSKCR/SSKCL
-
STGCR/STGCL
-
SVABR/SVABL
-
SVQCR/SVQCL
-
SWACR/SWACL
-
WTQNR/WTQNL
-
-
Державки резьбовые
-
Державки отрезные, канавочные
-
Держатели отрезного лезвия
-
Лезвия отрезные
-
Мини-резцы твердосплавные
-
-
Оснастка для фрезерных станков
-
Фрезерные патроны
-
BT
-
BT-ER (для цанг ER)
-
BT-FMB (для насадных фрез)
-
BT-SCA (для дисковых фрез)
-
BT-D (тестовые оправки)
-
BT-SLN Weldon
-
BT-MTA (конус Морзе с лапкой)
-
BT-MTB (конус Морзе с резьбовым отверстием)
-
BT-DC (высокоскоростные патроны для цанг DC)
-
BT-APU
-
BT-SC (для цилиндрических цанг SC)
-
BT-GT (для резьбовых цанг GT12/24/42)
-
BT-TER (патроны с осевой компенсацией по длине для цанг ER)
-
BT-OZ(EOC) (для силовых цанг OZ)
-
BT-PHC (гидропластовые патроны)
-
-
Конус Морзе MTA/MTB
-
HSK
-
Цилиндрический хвостовик
-
NT
-
SK
-
SK-FMB (для насадных фрез)
-
SK-SLN (Weldon)
-
SK-TER (патроны с осевой компенсацией по длине для цанг ER)
-
SK-SC (для цилиндрических цанг SC)
-
SK-MTB (конус Морзе с резьбовым отверстием)
-
SK-MTA (конус Морзе с лапкой)
-
SK-ER (для цанг ER)
-
SK-GT (для резьбовых цанг GT12/24/42)
-
SK-OZ(EOC) (для силовых цанг OZ)
-
SK-APU (сверлильные быстрозажимные патроны)
-
SK-PHC (гидропластовые патроны)
-
-
-
Прихваты, прижимы, упоры
-
Цанги
-
Штревели
-
3D тестеры
-
Тиски станочные
-
Аксессуары и запчасти
- Силовые высокоточные VQC
-
640 Multitasking
-
Трехкулачковые NBK
-
Гидравлические DCV
-
Модульные двойные ZQ83
-
С регулируемым усилием зажима HPAC
-
Самоцентрирующиеся SC-I
-
Модульные GT
-
Глобусные HHY
-
Лекальные QGG
-
Лекальные QKG
-
Модульные составные ZQ84
-
Гидравлические CHV
-
Самоцентрирующиеся двойные SMC
-
-
Кромкоискатели
-
Магнитные плиты
-
Центроискатели
-
Гайки для цанг
-
Ключи гаечные
-
Приспособления для оправок
-
Наборы прижимов
-
Расточные системы
-
Система нулевого базирования
-
Магнитные захваты
-
Поворотные столы
-
Аксессуары для станочной оснастки
-
Привязка по оси Z
-
Защитные вставки
-
-
Оснастка для токарных станков
-
Кулачки токарные
- Инструментальные блоки BOT
-
Токарные патроны
-
Центры токарные вращающиеся
- Центры вращающиеся
- Центры вращающиеся усиленные M11
- Центры вращающиеся облегченные
- Центры вращающиеся со сменными вставками
- Центры вращающиеся высокоскоростные
- Центры вращающиеся с твердосплавной вставкой
- Центры вращающиеся с удлиненной вершиной
- Центры вращающиеся усиленные
- Центры вращающиеся высокоточные
- Центры вращающиеся грибковые
-
Держатели осевого инструмента
-
Переходные втулки
-
Приспособления для расточки кулачков
-
Инструментальные блоки BMT
-
Центры токарные упорные
-
Сухари для токарных патронов
-
Инструментальные блоки VDI
-
Патроны цанговые
-
Цанги токарные
-
-
Измерительный инструмент
-
Станки
-
Станки ленточные по металлу
-
Лазерные граверы (маркировщики) по металлу
-
Токарные станки
-
Фрезерные станки
-
Заточные станки
-
Резьбонарезные манипуляторы
-
Электроэрозионные станки
-
Промышленные роботы
-
-
Мерч CNC66
-
Проволока, СОЖ, запчасти для электроэрозионных станков
-
Промышленная мебель
-
Запасные части для державок, резцов и фрез
-
Развертки
-
Упаковка
-
Зенковки
-
Плашки
-
Инструмент для снятия заусенцев
-
Корзина пуста
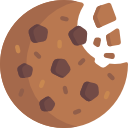
Мы используем файлы cookie для улучшения работы сайта и персонализации. Продолжая использовать сайт, вы соглашаетесь на сбор, обработку cookie-файлов и пользовательских данных с помощью Яндекс.Метрика, в соответствии с нашей Политикой конфиденциальности.