Карбидные инструменты для обработки металла
Карбидные инструменты представляют собой режущие и абразивные приспособления, изготовленные из твердых сплавов на основе карбидов тугоплавких металлов.
Основными компонентами этих сплавов являются карбиды вольфрама, титана, тантала и ниобия, связанные кобальтовой матрицей. Благодаря уникальному сочетанию свойств, карбидные инструменты обладают значительными преимуществами по сравнению с традиционными стальными аналогами.
Ключевые отличия карбидного инструмента
Одним из ключевых достоинств карбидных инструментов является их исключительная долговечность. В среднем, срок службы карбидного инструмента в 10-15 раз превышает срок службы инструмента из быстрорежущей стали при работе в аналогичных условиях.
Это обусловлено высокой твердостью карбидных сплавов, которая сохраняется даже при повышенных температурах, возникающих в процессе резания. Твердость карбидных инструментов по шкале Роквелла достигает 90-92 HRC, что значительно превосходит показатели быстрорежущих сталей (62-65 HRC).
Устойчивость к износу карбидных инструментов объясняется особенностями их микроструктуры. Твердые частицы карбидов, равномерно распределенные в более мягкой кобальтовой связке, образуют своеобразный каркас, который эффективно противостоит абразивному воздействию обрабатываемого материала. При этом кобальтовая матрица обеспечивает необходимую вязкость, предотвращая хрупкое разрушение инструмента.
Высокая твердость карбидных инструментов позволяет достигать исключительного качества обработки поверхности. При правильно подобранных режимах резания, карбидные инструменты способны обеспечивать шероховатость поверхности Ra 0,8-0,4 мкм и ниже, что соответствует 7-8 классу чистоты по ГОСТ 2789-73. Это особенно важно при изготовлении прецизионных деталей в аэрокосмической и автомобильной промышленности.
Стабильность свойств карбидных инструментов при высоких температурах является их неоспоримым преимуществом при высокоскоростной обработке. В то время как инструменты из быстрорежущей стали начинают терять свою твердость уже при температурах около 600°C, карбидные инструменты сохраняют работоспособность до температур порядка 900-1000°C. Это позволяет значительно увеличить скорость резания и, как следствие, повысить производительность обработки.
При сравнении карбидных инструментов с инструментами из быстрорежущей стали (HSS) становится очевидным, что карбидные инструменты обладают значительными преимуществами в плане производительности и стойкости. Однако они также имеют более высокую стоимость и требуют более тщательного обращения.
Инструменты из быстрорежущей стали остаются востребованными в случаях, когда требуется высокая вязкость инструментального материала, например, при обработке с большими ударными нагрузками или при изготовлении инструментов сложной формы.
Сравнение карбидных и керамических инструментов показывает, что каждый тип имеет свою область применения. Керамические инструменты превосходят карбидные по твердости и теплостойкости, что позволяет использовать еще более высокие скорости резания.
Однако они уступают карбидным инструментам по вязкости и более чувствительны к ударным нагрузкам. Керамические инструменты наиболее эффективны при обработке чугунов и жаропрочных сплавов в условиях стабильного резания, в то время как карбидные инструменты обеспечивают более универсальное применение.
Применение карбидных инструментов
Карбидные инструменты особенно эффективны при обработке труднообрабатываемых материалов, таких как нержавеющие стали, титановые сплавы и жаропрочные никелевые сплавы. При обработке нержавеющей стали AISI 316L карбидные инструменты позволяют увеличить скорость резания в 2-3 раза по сравнению с инструментами из быстрорежущей стали, обеспечивая при этом более высокое качество обработанной поверхности и меньший износ инструмента.
В токарной обработке карбидные инструменты широко применяются для черновых и чистовых операций. Они особенно эффективны при непрерывном резании, когда требуется высокая стойкость инструмента.
При фрезеровании карбидные инструменты позволяют достигать высоких скоростей резания, что особенно важно при обработке крупногабаритных деталей. В области сверления карбидные сверла обеспечивают высокую точность и качество отверстий, особенно при работе с труднообрабатываемыми материалами.
При изготовлении сложных деталей, требующих высокой точности и качества поверхности, карбидные инструменты становятся незаменимыми. Например, при производстве турбинных лопаток для авиационных двигателей, где допуски на размеры могут составлять всего несколько микрон, использование карбидных фрез позволяет достичь требуемой точности и обеспечить необходимую шероховатость поверхности.
Выбор подходящего карбидного инструмента зависит от множества факторов, включая тип обрабатываемого материала, вид операции, требуемую точность и качество поверхности. При выборе инструмента следует учитывать марку твердого сплава, геометрию режущей кромки, наличие и тип покрытия. Например, для обработки стали часто используются сплавы группы P по ISO, в то время как для обработки чугуна предпочтительны сплавы группы K.
Настройка станка для работы с карбидными инструментами требует особого внимания. Оптимальные параметры резания, такие как скорость резания, подача и глубина резания, зависят от конкретной комбинации инструмента и обрабатываемого материала.
В общем случае, карбидные инструменты позволяют использовать более высокие скорости резания по сравнению с инструментами из быстрорежущей стали. Например, при точении конструкционной стали скорость резания для карбидного инструмента может достигать 200-300 м/мин, в то время как для инструмента из быстрорежущей стали она обычно не превышает 30-50 м/мин.
При работе с карбидными инструментами важно обеспечить жесткость системы станок-приспособление-инструмент-деталь. Высокая твердость карбидных инструментов делает их более чувствительными к вибрациям и ударным нагрузкам. Поэтому необходимо минимизировать вылет инструмента, использовать надежные зажимные приспособления и обеспечивать правильную балансировку вращающихся частей.
Для достижения максимальной эффективности при работе с карбидными инструментами важно правильно выбирать условия резания. Это включает в себя не только скорость, подачу и глубину резания, но и использование соответствующей смазочно-охлаждающей жидкости (СОЖ).
Применение СОЖ помогает снизить температуру в зоне резания, улучшить отвод стружки и продлить срок службы инструмента. При высокоскоростной обработке эффективным может быть использование минимального количества смазки (MQL) или обработка без применения СОЖ.
Эксплуатация карбидного инструмента
Уход за карбидными инструментами играет важную роль в обеспечении их долговечности. После использования инструменты следует тщательно очистить от стружки и СОЖ, высушить и хранить в сухом месте, защищенном от механических повреждений. Для предотвращения коррозии кобальтовой связки рекомендуется использовать специальные антикоррозионные составы.
Профилактические меры по предотвращению повреждений карбидных инструментов включают в себя регулярный контроль состояния режущих кромок, проверку биения инструмента в шпинделе станка, а также соблюдение рекомендованных режимов резания. Особое внимание следует уделять предотвращению ударных нагрузок на инструмент, которые могут привести к выкрашиванию или сколам режущей кромки.
Ремонт и заточка карбидных инструментов требуют специального оборудования и навыков. В отличие от инструментов из быстрорежущей стали, которые можно затачивать на обычных заточных станках, карбидные инструменты требуют использования алмазных шлифовальных кругов и прецизионного оборудования.
Заточку следует проводить при первых признаках износа режущей кромки, не допуская критического износа, который может привести к необратимым повреждениям инструмента.
- На главную
-
Категории
-
Пластины
-
Пластины токарные
-
Пластины для внутреннего и наружного точения
-
Пластины резьбовые
-
Пластины резьбовые ISO
-
Пластины резьбовые трапецеидального профиля, угол 30 град.
-
Пластины резьбовые неполного профиля, угол 55 или 60 град.
-
Пластины резьбовые для нарезания трубной резьбы Whitworth, правые
-
Пластины резьбовые NPT (дюймовая коническая резьба c углом профиля 60 град. и конус 1:16)
-
Пластины резьбовые BSPT (Британский стандарт) полного профиля, угол 55 град.
-
Пластины резьбовые треугольного закругленного профиля
-
Пластины резьбовые UN (Американский стандарт) полного профиля, угол 60 град.
-
-
Пластины отрезные и канавочные
-
TGF32
-
SP
-
MRMN
-
MG...N
- GER-C
- SP для стали
- SP для нержавеющей стали
-
QCMB
-
QPMB
- MGMN для стали
- MGMN для нержавеющей стали
- QPMB для стали
- QPMB для нержавеющей стали
- MRMN для стали
- ZP_S для нержавеющей стали
-
ZP_S
- QCMB для нержавеющей стали
- ZT_D для нержавеющей стали
-
ZT_D
- ZT_D для стали
- QCMB для стали
- TDC для нержавеющей стали
-
TDC
- QC_ для нержавеющей стали
-
QC
- QC_
- ZP_D для нержавеющей стали
-
ZP_D
- ZR_D для нержавеющей стали
-
ZR_D
- ZT_S для нержавеющей стали
-
ZT_S
- ZQMX для стали
-
ZQMX
- CTPA для нержавеющей стали
-
CTPA
- MGMN для чугуна
- MRMN для нержавеющей стали
- MRMN для чугуна
-
GEL-A/B
- GEL-A
-
GEL-A/B-R
-
GEL-C/D/E
- GEL-C
-
GEL-C/D/E-R
-
GER-A/B
- GER-A
-
GER-A/B-R
-
GER-C/D/E
-
GER-C/D/E-R
-
-
-
Пластины фрезерные
-
Пластины для свёрл
-
Лезвия для резьбофрез
-
Пластины со вставками PCBN
-
-
Фрезы
-
Метчики
-
Сверла
-
Ленточные пилы
-
Новое поступление (NEW!)
-
Державки токарные
-
Державки расточные
-
S...-SVJCR/S...-SVJCL
-
S...-DCLNR/S...-DCLNL
-
S...-DDUNR/S...-DDUNL
-
S...-DWLNR/S...-DWLNL
-
S...-MCKNR/S...-MCKNL
-
S...-MCLNR/S...-MCLNL
-
S...-MDQNR/S...-MDQNL
-
S...-MDUNR/S...-MDUNL
-
S...-MSKNR/S-...MSKNL
-
S...-MTJNR/S...-MTJNL
-
S...-MTQNR/S...-MTQNL
-
S...-MTUNR/S...-MTUNL
-
S...-MTFNR/S...-MTFNL
-
S...-MTWNR/S...-MTWNL
-
S...-MVQNR/S-...MVQNL
-
S...-MVUNR/S-...MVUNL
-
S...-MVWNR/S...-MVWNL
-
S...-MVXNR/S...-MVXNL
-
S...-MWLNR/S...-MWLNL
-
S...-PCLNR/S...-PCLNL
-
S...-PDSNR/S...-PDSNL
-
S...-PDUNR/S...-PDUNL
-
S...-PSKNR/S...-PSKNL
-
S...-PWLNR/S...-PWLNL
-
S...-PTFNR/S...-PTFNL
-
S...-SCKCR/S...-SCKCL
-
S...-SCLCR/S...-SCLCL
-
S...-SCLPR/S...-SCLPL
-
S...-SDQCR/S...-SDQCL
-
S...-SDUCR/S...-SDUCL
-
S...-SDZCR/S...-SDZCL
-
S...-SSSCR/S...-SSSCL
-
S...-SSKCR/S...-SSKCL
-
S...-STFCR/S-...STFCL
-
S...-STUCR/S-...STUCL
-
S...-SVUCR/S-...SVUCL
-
S...-SVUBR/S...-SVUBL
-
-
Державки проходные
-
CCLNR/CCLNL
-
CRDNN
-
CSDNN
-
CSKNR/CSKNL
-
CTJNR/CTJNL
-
DCBNR/DCBNL
-
DCKNR/DCKNL
-
DCLNR/DCLNL
-
DCMNN
-
DDJNR/DDJNL
-
DDPNN
-
DSSNR/DSSNL
-
DDQNR/DDQNL
-
DSBNR/DSBNL
-
DSDNN
-
DSKNR/DSKNL
-
DTFNR/DTFNL
-
DTGNR/DTGNL
-
DVJNR/DVJNL
-
DVVNN
-
DWLNR/DWLNL
-
ECLNR/ECLNL
-
EDJNR/EDJNL
-
EVJNR/EVJNL
-
EWLNR/EWLNL
-
MCBNR/MCBNL
-
MCKNR/MCKNL
-
MCLNR/MCLNL
-
MCMNN
-
MDJNR/MDJNL
-
MDPNN
-
MDQNR/MDQNL
-
MRDNN
-
MRGNR/MRGNL
-
MSBNR/MSBNL
-
MSDNN
-
MSKNR/MSKNL
-
MSSNR/MSSNL
-
MTENN
-
MTFNR/MTFNL
-
MTGNR/MTGNL
-
MTJNR/MTJNL
-
MTQNR/MTQNL
-
MVJNR/MVJNL
-
MVQNR/MVQNL
-
MVUNR/MVUNL
-
MVVNN
-
MWLNR/MWLNL
-
PWLNR/PWLNL
-
PCLNR/PCLNL
-
PDJNR/PDJNL
-
PRACR/PRACL
-
PRDCN
-
PCBNR/PCBNL
-
PRGCR/PRGCL
-
PSBNR/PSBNL
-
PSDNN
-
PSSNR/PSSNL
-
PTGNR/PTGNL
-
PTTNR/PTTNL
-
SCLCR/SCLCL
-
SDJCR/SDJCL
-
SDNCN
-
SRACR/SRACL
-
SRDCN
-
SSDCN
-
SSSCR/SSSCL
-
STFCR/STFCL
-
SVACR/SVACL
-
SVJBR/SVJBL
-
SVJCR/SVJCL
-
SVVBN
-
SVVCN
-
WTENN
-
WTJNR/WTJNL
-
WWLNR/WWLNL
-
PDNNR/PDNNL
-
SVHBR/SVHBL
-
PDNNN
-
PTFNR/PTFNL
-
SCACR/SCACL
-
SDACR/SDACL
-
SSBCR/SSBCL
-
SRGCR/SRGCL
-
SSKCR/SSKCL
-
STGCR/STGCL
-
SVABR/SVABL
-
SVQCR/SVQCL
-
SWACR/SWACL
-
WTQNR/WTQNL
-
-
Державки резьбовые
-
Державки отрезные, канавочные
-
Держатели отрезного лезвия
-
Лезвия отрезные
-
Мини-резцы твердосплавные
-
-
Оснастка для фрезерных станков
-
Фрезерные патроны
-
BT
-
BT-ER (для цанг ER)
-
BT-FMB (для насадных фрез)
-
BT-SCA (для дисковых фрез)
-
BT-D (тестовые оправки)
-
BT-SLN Weldon
-
BT-MTA (конус Морзе с лапкой)
-
BT-MTB (конус Морзе с резьбовым отверстием)
-
BT-DC (высокоскоростные патроны для цанг DC)
-
BT-APU
-
BT-SC (для цилиндрических цанг SC)
-
BT-GT (для резьбовых цанг GT12/24/42)
-
BT-TER (патроны с осевой компенсацией по длине для цанг ER)
-
BT-OZ(EOC) (для силовых цанг OZ)
-
BT-PHC (гидропластовые патроны)
-
-
Конус Морзе MTA/MTB
-
HSK
-
Цилиндрический хвостовик
-
NT
-
SK
-
SK-FMB (для насадных фрез)
-
SK-SLN (Weldon)
-
SK-TER (патроны с осевой компенсацией по длине для цанг ER)
-
SK-SC (для цилиндрических цанг SC)
-
SK-MTB (конус Морзе с резьбовым отверстием)
-
SK-MTA (конус Морзе с лапкой)
-
SK-ER (для цанг ER)
-
SK-GT (для резьбовых цанг GT12/24/42)
-
SK-OZ(EOC) (для силовых цанг OZ)
-
SK-APU (сверлильные быстрозажимные патроны)
-
SK-PHC (гидропластовые патроны)
-
-
-
Прихваты, прижимы, упоры
-
Цанги
-
Штревели
-
3D тестеры
-
Тиски станочные
-
Аксессуары и запчасти
- Силовые высокоточные VQC
-
640 Multitasking
-
Трехкулачковые NBK
-
Гидравлические DCV
-
Модульные двойные ZQ83
-
С регулируемым усилием зажима HPAC
-
Самоцентрирующиеся SC-I
-
Модульные GT
-
Глобусные HHY
-
Лекальные QGG
-
Лекальные QKG
-
Модульные составные ZQ84
-
Гидравлические CHV
-
Самоцентрирующиеся двойные SMC
-
-
Кромкоискатели
-
Магнитные плиты
-
Центроискатели
-
Гайки для цанг
-
Ключи гаечные
-
Приспособления для оправок
-
Наборы прижимов
-
Расточные системы
-
Система нулевого базирования
-
Магнитные захваты
-
Поворотные столы
-
Аксессуары для станочной оснастки
-
Привязка по оси Z
-
-
Оснастка для токарных станков
-
Кулачки токарные
- Инструментальные блоки BOT
-
Токарные патроны
-
Центры токарные вращающиеся
- Центры вращающиеся
- Центры вращающиеся усиленные M11
- Центры вращающиеся облегченные
- Центры вращающиеся со сменными вставками
- Центры вращающиеся высокоскоростные
- Центры вращающиеся с твердосплавной вставкой
- Центры вращающиеся с удлиненной вершиной
- Центры вращающиеся усиленные
- Центры вращающиеся высокоточные
- Центры вращающиеся грибковые
-
Держатели осевого инструмента
-
Переходные втулки
-
Приспособления для расточки кулачков
-
Инструментальные блоки BMT
-
Центры токарные упорные
-
Сухари для токарных патронов
-
Инструментальные блоки VDI
-
Патроны цанговые
-
Цанги токарные
-
-
Измерительный инструмент
-
Станки
-
Станки ленточные по металлу
-
Лазерные граверы (маркировщики) по металлу
-
Токарные станки
-
Фрезерные станки
-
Заточные станки
-
Резьбонарезные манипуляторы
-
Электроэрозионные станки
-
Промышленные роботы
-
-
Мерч CNC66
-
Проволока, СОЖ, запчасти для электроэрозионных станков
-
Промышленная мебель
-
Запасные части для державок, резцов и фрез
-
Развертки
-
Упаковка
-
Зенковки
-
Плашки
-
Инструмент для снятия заусенцев
- выгрузка
-
Корзина пуста
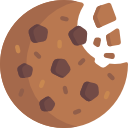
Мы используем файлы cookie для улучшения работы сайта и персонализации. Продолжая использовать сайт, вы соглашаетесь на сбор, обработку cookie-файлов и пользовательских данных с помощью Яндекс.Метрика, в соответствии с нашей Политикой конфиденциальности.