Как работает плазменная резка металлов
Плазменная резка металлов - метод термической обработки, позволяющий быстро и точно разделять металлические заготовки. Физический принцип данного процесса основан на использовании высокотемпературной плазменной струи, которая расплавляет и выдувает металл из зоны реза.
Плазма представляет собой ионизированный газ, нагретый до экстремально высоких температур (15000-30000°C). При таких температурах происходит разрушение межатомных связей и образование свободных электронов и ионов. Плазменная струя обладает высокой кинетической энергией и теплосодержанием, что позволяет ей эффективно прорезать металл.
Для получения плазмы используется электрическая дуга, горящая между электродом и обрабатываемой деталью. Через эту дугу продувается плазмообразующий газ (обычно воздух, азот или аргон), который ионизируется и превращается в плазму. Сжатая в сопле плазмотрона плазменная струя фокусируется и ускоряется, приобретая высокую режущую способность.
Виды плазменной резки
Существует несколько видов плазменной резки, различающихся по способу формирования плазменной струи и используемым газам. Основными являются плазменно-дуговая резка и резка плазменной струей.
При плазменно-дуговой резке электрическая дуга горит между электродом плазмотрона и разрезаемым металлом. Это обеспечивает высокую концентрацию энергии и хорошее качество реза. Данный метод применяется для резки токопроводящих металлов толщиной до 100-150 мм.
Резка плазменной струей использует косвенную дугу, горящую между электродами внутри плазмотрона. Плазменная струя в этом случае является нейтральной и может применяться для резки как проводящих, так и непроводящих материалов. Однако глубина реза и качество кромок при этом методе несколько ниже.
Плазменно-дуговая резка является наиболее распространенным видом плазменной обработки металлов. Она обеспечивает высокую скорость резки, хорошее качество кромок и возможность автоматизации процесса. При этом методе плазмообразующий газ (чаще всего воздух или азот) подается в сопло плазмотрона под давлением 0.4-0.6 МПа. Электрическая дуга, горящая между катодом плазмотрона и анодом-заготовкой, нагревает и ионизирует газ. Образующаяся плазменная струя фокусируется соплом и приобретает высокую кинетическую энергию.
При контакте с металлом плазменная струя мгновенно расплавляет его, а кинетическая энергия потока выдувает расплав из зоны реза. Благодаря высокой концентрации энергии в плазменной струе (до 10^9 Вт/м²) обеспечивается узкий рез с минимальной зоной термического влияния. Скорость резки может достигать 6-10 м/мин для тонколистового металла.
Раскрой плазменной струей применяется в основном для резки неэлектропроводных материалов или в случаях, когда невозможно использовать заготовку в качестве анода. При этом методе плазменная дуга горит между электродами внутри плазмотрона, а нейтральная плазменная струя выдувается наружу. Температура струи несколько ниже, чем при плазменно-дуговой резке, поэтому данный метод менее производителен. Однако он позволяет обрабатывать практически любые материалы.
Плюсы и минусы использования плазменной резки
Плазменная резка обладает рядом существенных преимуществ по сравнению с другими методами термической резки металлов. К ним относятся высокая скорость обработки, возможность резки практически любых металлов и сплавов, хорошее качество реза, узкая зона термического влияния, отсутствие механического воздействия на заготовку. Кроме того, плазменная резка легко поддается автоматизации и роботизации.
Однако у данного метода есть и некоторые недостатки. Основными из них являются высокая стоимость оборудования, значительное энергопотребление, необходимость использования сжатых газов, сильное ультрафиолетовое излучение и шум при работе. Кроме того, при плазменной резке образуются вредные аэрозоли, требующие эффективной вентиляции рабочего места.
Используемое оборудование
Для осуществления плазменной резки используется специализированное оборудование - плазморезы. Основными компонентами плазмореза являются источник питания, плазмотрон, система подачи газов и система охлаждения. Источник питания преобразует переменный ток сети в постоянный ток, необходимый для горения плазменной дуги. Современные инверторные источники обеспечивают стабильные параметры дуги и высокий КПД.
Плазмотрон является ключевым элементом установки, в котором происходит формирование плазменной струи. Он состоит из водоохлаждаемого корпуса, сменного электрода-катода, газового завихрителя и сопла. Конструкция плазмотрона во многом определяет качество и производительность резки. Важную роль играет правильный подбор расходных деталей - электродов и сопел.
Система подачи газов обеспечивает подачу плазмообразующего, защитного и охлаждающего газов в плазмотрон. Она включает в себя газовые баллоны или компрессор, редукторы, электромагнитные клапаны и расходомеры. Точность регулировки расхода и давления газов напрямую влияет на стабильность процесса резки.
Система охлаждения необходима для отвода тепла от нагруженных элементов плазмотрона. В маломощных установках используется воздушное охлаждение, в более мощных - замкнутый контур с жидкостным охлаждением. Эффективное охлаждение значительно увеличивает срок службы расходных деталей.
Работа на плазморезе
Принцип работы плазмореза заключается в следующем. При нажатии кнопки на плазмотроне включается подача газа и зажигается дежурная дуга между электродом и соплом. При поднесении плазмотрона к заготовке дежурная дуга переходит в режущую, горящую между электродом и металлом. Мощный поток плазмы прожигает начальное отверстие, после чего начинается процесс резки.
Оператор перемещает плазмотрон вдоль линии реза с определенной скоростью. Важно поддерживать постоянное расстояние между соплом и заготовкой (обычно 3-5 мм). Для этого часто используются специальные упоры или системы автоматического поддержания высоты. По окончании реза подача тока и газа автоматически прекращается.
Для эффективной и безопасной работы на плазморезе необходимо соблюдать ряд правил. Перед началом работы следует проверить исправность оборудования, наличие и состояние расходных деталей. Важно правильно выставить параметры резки - ток, давление газа, скорость перемещения - в зависимости от толщины и материала заготовки. Эти данные обычно приводятся в инструкции к оборудованию.
При работе необходимо использовать средства индивидуальной защиты - специальную маску со светофильтром, защитную одежду и обувь. Нельзя допускать попадания влаги на плазмотрон и заготовку. Рабочее место должно быть оборудовано эффективной вытяжной вентиляцией для удаления вредных аэрозолей. После окончания работы нужно продуть плазмотрон сжатым воздухом для удаления остатков шлака.
Техника безопасности при плазменной резке требует особого внимания. Основными факторами риска являются поражение электрическим током, ожоги от брызг расплавленного металла, повреждение глаз ультрафиолетовым излучением дуги. Категорически запрещается работать на неисправном оборудовании или при отсутствии заземления. Нельзя производить резку вблизи легковоспламеняющихся материалов или емкостей из-под горючих жидкостей.
Выбор плазмореза
На рынке представлен широкий ассортимент оборудования для плазменной резки от различных производителей. Выбор конкретной модели зависит от решаемых задач, толщины обрабатываемого металла и требуемой производительности. Для небольших мастерских и частного использования подойдут компактные инверторные плазморезы мощностью 30-60 А. Они позволяют резать металл толщиной до 10-15 мм.
Для промышленного применения используются более мощные установки на 80-120 А, способные резать металл толщиной до 25-30 мм. Крупные предприятия часто оснащаются автоматизированными комплексами плазменной резки с ЧПУ. Они обеспечивают высокую точность и производительность при раскрое листового металла.
При выборе плазмореза следует обращать внимание на такие характеристики, как максимальная толщина реза, продолжительность включения, наличие дополнительных функций (например, строжки). Важным фактором является доступность и стоимость расходных деталей. Некоторые производители предлагают универсальные плазмотроны, совместимые с электродами и соплами разных типов.
- На главную
-
Категории
-
Пластины твердосплавные
-
Пластины токарные
-
Пластины для внутреннего и наружного точения
-
Пластины резьбовые
-
Пластины резьбовые ISO
-
Пластины резьбовые трапецеидального профиля, угол 30 град.
-
Пластины резьбовые неполного профиля, угол 55 или 60 град.
-
Пластины резьбовые для нарезания трубной резьбы Whitworth, правые
-
Пластины резьбовые NPT (дюймовая коническая резьба c углом профиля 60 град. и конус 1:16)
-
Пластины резьбовые BSPT (Британский стандарт) полного профиля, угол 55 град.
-
Пластины резьбовые треугольного закругленного профиля
-
Пластины резьбовые UN (Американский стандарт) полного профиля, угол 60 град.
- Пластины резьбовые UN (Американский стандарт) полного профиля, угол 60 град.
- Панцирная трубная резьба Pg 80 град.
- Пластины резьбовые трапецеидального профиля, угол 30 град.
- Пластины резьбовые BSPT (Британский стандарт) полного профиля, угол 55 град.
- Пластины резьбовые NPT (дюймовая коническая резьба c углом профиля 60 град. и конус 1:16)
- Пластины резьбовые неполного профиля, угол 55 или 60 град.
- Упорная резьба SAGE 30 град.
-
-
Пластины отрезные и канавочные
-
TGF32
-
SP
-
MRMN
-
MG...N
- GER-C
- SP для стали
- SP для нержавеющей стали
-
QCMB
-
QPMB
- MGMN для стали
- MGMN для нержавеющей стали
- QPMB для стали
- QPMB для нержавеющей стали
- MRMN для стали
- ZP_S для нержавеющей стали
-
ZP_S
- QCMB для нержавеющей стали
- ZT_D для нержавеющей стали
-
ZT_D
- ZT_D для стали
- QCMB для стали
- TDC для нержавеющей стали
-
TDC
- QC_ для нержавеющей стали
-
QC
- QC_
- ZP_D для нержавеющей стали
-
ZP_D
- ZR_D для нержавеющей стали
-
ZR_D
- ZT_S для нержавеющей стали
-
ZT_S
- ZQMX для стали
-
ZQMX
- CTPA для нержавеющей стали
-
CTPA
- MGMN для чугуна
- MRMN для нержавеющей стали
- MRMN для чугуна
-
GEL-A/B
- GEL-A
-
GEL-A/B-R
-
GEL-C/D/E
- GEL-C
-
GEL-C/D/E-R
-
GER-A/B
- GER-A
-
GER-A/B-R
-
GER-C/D/E
-
GER-C/D/E-R
- MGMN
- MGGN
- MB
- ZTKS
- JRMN
- GK-R
- ZRFD
- KTMD
- KGT
- JSMN
- SPDR
-
-
-
Пластины фрезерные
-
Пластины для сверл
-
Лезвия для резьбофрез
-
Пластины со вставками PCBN
- Пластины для червячного зуба 40°
-
-
Фрезы
-
Метчики
-
Сверла
-
Ленточные пилы
-
Новое поступление (NEW!)
-
Державки токарные
-
Державки расточные
-
S...-SVJCR/S...-SVJCL
-
S...-DCLNR/S...-DCLNL
-
S...-DDUNR/S...-DDUNL
-
S...-DWLNR/S...-DWLNL
-
S...-MCKNR/S...-MCKNL
-
S...-MCLNR/S...-MCLNL
-
S...-MDQNR/S...-MDQNL
-
S...-MDUNR/S...-MDUNL
-
S...-MSKNR/S-...MSKNL
-
S...-MTJNR/S...-MTJNL
-
S...-MTQNR/S...-MTQNL
-
S...-MTUNR/S...-MTUNL
-
S...-MTFNR/S...-MTFNL
-
S...-MTWNR/S...-MTWNL
-
S...-MVQNR/S-...MVQNL
-
S...-MVUNR/S-...MVUNL
-
S...-MVWNR/S...-MVWNL
-
S...-MVXNR/S...-MVXNL
-
S...-MWLNR/S...-MWLNL
-
S...-PCLNR/S...-PCLNL
-
S...-PDSNR/S...-PDSNL
-
S...-PDUNR/S...-PDUNL
-
S...-PSKNR/S...-PSKNL
-
S...-PWLNR/S...-PWLNL
-
S...-PTFNR/S...-PTFNL
-
S...-SCKCR/S...-SCKCL
-
S...-SCLCR/S...-SCLCL
-
S...-SCLPR/S...-SCLPL
-
S...-SDQCR/S...-SDQCL
-
S...-SDUCR/S...-SDUCL
-
S...-SDZCR/S...-SDZCL
-
S...-SSSCR/S...-SSSCL
-
S...-SSKCR/S...-SSKCL
-
S...-STFCR/S-...STFCL
-
S...-STUCR/S-...STUCL
-
S...-SVUCR/S-...SVUCL
-
S...-SVUBR/S...-SVUBL
-
-
Державки проходные
-
CCLNR/CCLNL
-
CRDNN
-
CSDNN
-
CSKNR/CSKNL
-
CTJNR/CTJNL
-
DCBNR/DCBNL
-
DCKNR/DCKNL
-
DCLNR/DCLNL
-
DCMNN
-
DDJNR/DDJNL
-
DDPNN
-
DSSNR/DSSNL
-
DDQNR/DDQNL
-
DSBNR/DSBNL
-
DSDNN
-
DSKNR/DSKNL
-
DTFNR/DTFNL
-
DTGNR/DTGNL
-
DVJNR/DVJNL
-
DVVNN
-
DWLNR/DWLNL
-
ECLNR/ECLNL
-
EDJNR/EDJNL
-
EVJNR/EVJNL
-
EWLNR/EWLNL
-
MCBNR/MCBNL
-
MCKNR/MCKNL
-
MCLNR/MCLNL
-
MCMNN
-
MDJNR/MDJNL
-
MDPNN
-
MDQNR/MDQNL
-
MRDNN
-
MRGNR/MRGNL
-
MSBNR/MSBNL
-
MSDNN
-
MSKNR/MSKNL
-
MSSNR/MSSNL
-
MTENN
-
MTFNR/MTFNL
-
MTGNR/MTGNL
-
MTJNR/MTJNL
-
MTQNR/MTQNL
-
MVJNR/MVJNL
-
MVQNR/MVQNL
-
MVUNR/MVUNL
-
MVVNN
-
MWLNR/MWLNL
-
PWLNR/PWLNL
-
PCLNR/PCLNL
-
PDJNR/PDJNL
-
PRACR/PRACL
-
PRDCN
-
PCBNR/PCBNL
-
PRGCR/PRGCL
-
PSBNR/PSBNL
-
PSDNN
-
PSSNR/PSSNL
-
PTGNR/PTGNL
-
PTTNR/PTTNL
-
SCLCR/SCLCL
-
SDJCR/SDJCL
-
SDNCN
-
SRACR/SRACL
-
SRDCN
-
SSDCN
-
SSSCR/SSSCL
-
STFCR/STFCL
-
SVACR/SVACL
-
SVJBR/SVJBL
-
SVJCR/SVJCL
-
SVVBN
-
SVVCN
-
WTENN
-
WTJNR/WTJNL
-
WWLNR/WWLNL
-
PDNNR/PDNNL
-
SVHBR/SVHBL
-
PDNNN
-
PTFNR/PTFNL
-
SCACR/SCACL
-
SDACR/SDACL
-
SSBCR/SSBCL
-
SRGCR/SRGCL
-
SSKCR/SSKCL
-
STGCR/STGCL
-
SVABR/SVABL
-
SVQCR/SVQCL
-
SWACR/SWACL
-
WTQNR/WTQNL
-
-
Державки резьбовые
-
Державки отрезные, канавочные
-
Держатели отрезного лезвия
-
Лезвия отрезные
-
Мини-резцы твердосплавные
-
-
Оснастка для фрезерных станков
-
Фрезерные патроны
-
BT
-
BT-ER (для цанг ER)
-
BT-FMB (для насадных фрез)
-
BT-SCA (для дисковых фрез)
-
BT-D (тестовые оправки)
-
BT-SLN Weldon
-
BT-MTA (конус Морзе с лапкой)
-
BT-MTB (конус Морзе с резьбовым отверстием)
-
BT-DC (высокоскоростные патроны для цанг DC)
-
BT-APU
-
BT-SC (для цилиндрических цанг SC)
-
BT-GT (для резьбовых цанг GT12/24/42)
-
BT-TER (патроны с осевой компенсацией по длине для цанг ER)
-
BT-OZ(EOC) (для силовых цанг OZ)
-
BT-PHC (гидропластовые патроны)
-
-
Конус Морзе MTA/MTB
-
HSK
-
Цилиндрический хвостовик
-
NT
-
SK
-
SK-FMB (для насадных фрез)
-
SK-SLN (Weldon)
-
SK-TER (патроны с осевой компенсацией по длине для цанг ER)
-
SK-SC (для цилиндрических цанг SC)
-
SK-MTB (конус Морзе с резьбовым отверстием)
-
SK-MTA (конус Морзе с лапкой)
-
SK-ER (для цанг ER)
-
SK-GT (для резьбовых цанг GT12/24/42)
-
SK-OZ(EOC) (для силовых цанг OZ)
-
SK-APU (сверлильные быстрозажимные патроны)
-
SK-PHC (гидропластовые патроны)
-
-
-
Прихваты, прижимы, упоры
-
Цанги
-
Штревели
-
3D тестеры
-
Тиски станочные
-
Аксессуары и запчасти
- Силовые высокоточные VQC
-
640 Multitasking
-
Трехкулачковые NBK
-
Гидравлические DCV
-
Модульные двойные ZQ83
-
С регулируемым усилием зажима HPAC
-
Самоцентрирующиеся SC-I
-
Модульные GT
-
Глобусные HHY
-
Лекальные QGG
-
Лекальные QKG
-
Модульные составные ZQ84
-
Гидравлические CHV
-
Самоцентрирующиеся двойные SMC
-
-
Кромкоискатели
-
Магнитные плиты
-
Центроискатели
-
Гайки для цанг
-
Ключи гаечные
-
Приспособления для оправок
-
Наборы прижимов
-
Расточные системы
-
Система нулевого базирования
-
Магнитные захваты
-
Поворотные столы
-
Аксессуары для станочной оснастки
-
Привязка по оси Z
-
Защитные вставки
-
-
Оснастка для токарных станков
-
Кулачки токарные
- Инструментальные блоки BOT
-
Токарные патроны
-
Центры токарные вращающиеся
- Центры вращающиеся
- Центры вращающиеся усиленные M11
- Центры вращающиеся облегченные
- Центры вращающиеся со сменными вставками
- Центры вращающиеся высокоскоростные
- Центры вращающиеся с твердосплавной вставкой
- Центры вращающиеся с удлиненной вершиной
- Центры вращающиеся усиленные
- Центры вращающиеся высокоточные
- Центры вращающиеся грибковые
-
Держатели осевого инструмента
-
Переходные втулки
-
Приспособления для расточки кулачков
-
Инструментальные блоки BMT
-
Центры токарные упорные
-
Сухари для токарных патронов
-
Инструментальные блоки VDI
-
Патроны цанговые
-
Цанги токарные
-
-
Измерительный инструмент
-
Станки
-
Станки ленточные по металлу
-
Лазерные граверы (маркировщики) по металлу
-
Токарные станки
-
Фрезерные станки
-
Заточные станки
-
Резьбонарезные манипуляторы
-
Электроэрозионные станки
-
Промышленные роботы
-
-
Мерч CNC66
-
Проволока, СОЖ, запчасти для электроэрозионных станков
-
Промышленная мебель
-
Запасные части для державок, резцов и фрез
-
Развертки
-
Упаковка
-
Зенковки
-
Плашки
-
Инструмент для снятия заусенцев
-
Корзина пуста
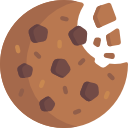
Мы используем файлы cookie для улучшения работы сайта и персонализации. Продолжая использовать сайт, вы соглашаетесь на сбор, обработку cookie-файлов и пользовательских данных с помощью Яндекс.Метрика, в соответствии с нашей Политикой конфиденциальности.