- Главная
- Статьи
- Использование медных подкладок при сварке нержавеющей стали для улучшения качества шва
Использование медных подкладок при сварке нержавеющей стали для улучшения качества шва
При сварке деталей из коррозионностойких сталей, особенно в корневой зоне, часто возникает трудность с формированием обратной поверхности соединения. Применение медных подкладок позволяет стабилизировать процесс, обеспечить симметрию проплавления и снизить вероятность прожога.
Такие подкладки особенно эффективны в ручной аргонодуговой и автоматической сварке неплавящимся электродом с подачей присадки.
Медь применяется за счёт высокой теплопроводности, превышающей 390 Вт/м·К. Это позволяет эффективно отводить тепло от зоны сваривания и предотвращает перегрев и деформацию краёв. Контакт должен быть плотным, чтобы не допускать прогаров и минимизировать провисание капли расплава. Поверхность подкладки необходимо зачищать абразивом зернистостью не крупнее Р120 и обезжиривать ацетоном.
Теплоёмкость меди при 20 °C составляет около 0,39 Дж/г·К. Это обуславливает её устойчивость к перегреву и позволяет использовать подкладку без дополнительного охлаждения при кратковременной сварке.
При длительном прогреве в многопроходной сварке может потребоваться водяное охлаждение, реализуемое через проточные каналы в теле подкладки.
Толщина медного листа должна быть не менее 5 мм при длине шва до 200 мм и не менее 10 мм при протяжённых соединениях. Применение тонких пластин приводит к прогибу и снижению теплоотвода. При сборке конструкций подкладка плотно прижимается к нижней кромке либо магнитами, либо механическим прижимом. Для вертикальных швов применяются фиксирующие лапки или винтовые опоры.
Для уменьшения прилипания капель металла и облегчения удаления окислов, рабочую поверхность покрывают графитовой смазкой, допустимо использовать составы на основе дисульфида молибдена.
Это не ухудшает контакт и сохраняет форму после многократного применения. Допускается использование вкладышей из фольги между подкладкой и изделием при сварке тонколистовых деталей.
В случае соединения трубопроводов, при невозможности установки массивной опоры, используют вставные вкладыши из медного прутка диаметром 12–20 мм. Такие элементы прижимаются за счёт распорной системы, или временной струбцины. После выполнения корня шва вкладыш удаляется, повторное использование возможно после зачистки.
В аргонодуговой сварке при применении тока до 160 А и вольфрамового электрода диаметром 2,4 мм медная подкладка позволяет уменьшить обратный валик до 1,5 мм при толщине металла 3 мм.
Это существенно упрощает последующую зачистку шва и снижает внутреннее напряжение в зоне соединения. При сварке листов толщиной от 6 мм подкладка способствует равномерному распределению теплового пятна и формированию симметричного корня.
Для автоматизированной сварки под флюсом или в защитной среде важно обеспечить стабильный зазор между изделием и подкладкой не более 0,3 мм. При большем зазоре возникает неравномерность теплового режима и возможен прожог. В серийном производстве применяются водоохлаждаемые опоры, выполненные из меди М1 или М2 с температурным расширением не выше 17 мкм/(м·°C).
Перед началом работ необходимо проконтролировать чистоту поверхности подкладки и отсутствие задиров, способных повредить основную деталь. Для зачистки не допускается применение угловых шлифмашин с лепестковыми кругами крупнее Р80, так как это увеличивает шероховатость. Грубая обработка вызывает перегрев и нарушает равномерность теплоотвода.
Допустимая температура рабочей поверхности медной пластины при сварке нержавейки толщиной до 4 мм не должна превышать 120 °C. При превышении этого значения возрастает риск деформации детали. Для контроля температуры используют контактные термодатчики, либо цветную термоиндикаторную ленту.
В производственных условиях длина подкладки выбирается на 20 мм больше длины предполагаемого шва с каждой стороны. Это исключает крайние перегревы и обеспечивает стабилизацию в начале и конце прохода. При сварке внахлёст применяются подкладки с выемкой под стыковую зону глубиной до 1,2 мм и шириной до 10 мм.
На практике, при сварке листов AISI 304 толщиной 2,5 мм с использованием аргона чистотой 99,995% и вольфрамового электрода с добавлением циркония, медная подкладка обеспечивает уменьшение ширины зоны термического влияния до 3 мм. Это положительно влияет на структуру стали и минимизирует риск межкристаллитной коррозии.
Если сварка выполняется без присадочного материала, подкладка особенно необходима для сохранения формы шва и предупреждения его провисания. В случае с изделиями толщиной менее 1,5 мм допускается использование гибких медных полос, которые формуются под нужную конфигурацию перед установкой. Важно следить за равномерностью давления и отсутствием перекосов.
При сварке труб с наружным диаметром до 76 мм используют разъёмные подкладки с секторным прижатием. В конструкции предусматриваются упоры, не позволяющие подкладке смещаться при нагреве. Места соприкосновения с изделием притираются вручную по шаблону. В случае отклонений более 0,1 мм возникает неравномерность теплоотвода.
Часто применяются медные охлаждаемые стержни с диаметром до 25 мм, используемые в вертикальной сварке тонкостенных сосудов. В теле стержня предусмотрен спиральный канал для протока воды с температурой 18–20 °C и скоростью до 1,2 л/мин. Это позволяет поддерживать стабильную температуру в зоне обратного валика.
Рекомендуется не применять подкладки из окисленной меди, так как наличие поверхностной плёнки снижает теплопроводность. При визуальном контроле должна отсутствовать побежалость, цветовые разводы и следы окисей. Восстановление поверхности проводится травлением в растворе серной кислоты с последующей нейтрализацией.
В массовом производстве изделий из стали AISI 316 с толщиной до 5 мм медные подкладки входят в состав стационарных сборочных приспособлений. Они оснащаются системой прижима с усилием не менее 100 Н, обеспечивающим равномерный контакт. При сварке с импульсной подачей тока подкладка снижает ширину зоны термического влияния на 30%.
Медные элементы применяются многократно, при условии отсутствия эрозии более 0,3 мм от первоначальной геометрии. После каждой операции производится зачистка и контроль плоскостности. При появлении выработки глубиной более 0,5 мм элемент заменяется новым. Допускается локальное восстановление формы наплавкой с последующей механической обработкой.
- На главную
-
Категории
-
Пластины
-
Пластины токарные
-
Пластины для внутреннего и наружного точения
-
Пластины резьбовые
-
Пластины резьбовые ISO
-
Пластины резьбовые трапецеидального профиля, угол 30 град.
-
Пластины резьбовые неполного профиля, угол 55 или 60 град.
-
Пластины резьбовые для нарезания трубной резьбы Whitworth, правые
-
Пластины резьбовые NPT (дюймовая коническая резьба c углом профиля 60 град. и конус 1:16)
-
Пластины резьбовые BSPT (Британский стандарт) полного профиля, угол 55 град.
-
Пластины резьбовые треугольного закругленного профиля
-
Пластины резьбовые UN (Американский стандарт) полного профиля, угол 60 град.
-
-
Пластины отрезные и канавочные
-
TGF32
-
SP
-
MRMN
-
MG...N
- GER-C
- SP для стали
- SP для нержавеющей стали
-
QCMB
-
QPMB
- MGMN для стали
- MGMN для нержавеющей стали
- QPMB для стали
- QPMB для нержавеющей стали
- MRMN для стали
- ZP_S для нержавеющей стали
-
ZP_S
- QCMB для нержавеющей стали
- ZT_D для нержавеющей стали
-
ZT_D
- ZT_D для стали
- QCMB для стали
- TDC для нержавеющей стали
-
TDC
- QC_ для нержавеющей стали
-
QC
- QC_
- ZP_D для нержавеющей стали
-
ZP_D
- ZR_D для нержавеющей стали
-
ZR_D
- ZT_S для нержавеющей стали
-
ZT_S
- ZQMX для стали
-
ZQMX
- CTPA для нержавеющей стали
-
CTPA
- MGMN для чугуна
- MRMN для нержавеющей стали
- MRMN для чугуна
-
GEL-A/B
- GEL-A
-
GEL-A/B-R
-
GEL-C/D/E
- GEL-C
-
GEL-C/D/E-R
-
GER-A/B
- GER-A
-
GER-A/B-R
-
GER-C/D/E
-
GER-C/D/E-R
-
-
-
Пластины фрезерные
-
Пластины для свёрл
-
Лезвия для резьбофрез
-
Пластины со вставками PCBN
-
-
Фрезы
-
Метчики
-
Сверла
-
Ленточные пилы
-
Новое поступление (NEW!)
-
Державки токарные
-
Державки расточные
-
S...-SVJCR/S...-SVJCL
-
S...-DCLNR/S...-DCLNL
-
S...-DDUNR/S...-DDUNL
-
S...-DWLNR/S...-DWLNL
-
S...-MCKNR/S...-MCKNL
-
S...-MCLNR/S...-MCLNL
-
S...-MDQNR/S...-MDQNL
-
S...-MDUNR/S...-MDUNL
-
S...-MSKNR/S-...MSKNL
-
S...-MTJNR/S...-MTJNL
-
S...-MTQNR/S...-MTQNL
-
S...-MTUNR/S...-MTUNL
-
S...-MTFNR/S...-MTFNL
-
S...-MTWNR/S...-MTWNL
-
S...-MVQNR/S-...MVQNL
-
S...-MVUNR/S-...MVUNL
-
S...-MVWNR/S...-MVWNL
-
S...-MVXNR/S...-MVXNL
-
S...-MWLNR/S...-MWLNL
-
S...-PCLNR/S...-PCLNL
-
S...-PDSNR/S...-PDSNL
-
S...-PDUNR/S...-PDUNL
-
S...-PSKNR/S...-PSKNL
-
S...-PWLNR/S...-PWLNL
-
S...-PTFNR/S...-PTFNL
-
S...-SCKCR/S...-SCKCL
-
S...-SCLCR/S...-SCLCL
-
S...-SCLPR/S...-SCLPL
-
S...-SDQCR/S...-SDQCL
-
S...-SDUCR/S...-SDUCL
-
S...-SDZCR/S...-SDZCL
-
S...-SSSCR/S...-SSSCL
-
S...-SSKCR/S...-SSKCL
-
S...-STFCR/S-...STFCL
-
S...-STUCR/S-...STUCL
-
S...-SVUCR/S-...SVUCL
-
S...-SVUBR/S...-SVUBL
-
-
Державки проходные
-
CCLNR/CCLNL
-
CRDNN
-
CSDNN
-
CSKNR/CSKNL
-
CTJNR/CTJNL
-
DCBNR/DCBNL
-
DCKNR/DCKNL
-
DCLNR/DCLNL
-
DCMNN
-
DDJNR/DDJNL
-
DDPNN
-
DSSNR/DSSNL
-
DDQNR/DDQNL
-
DSBNR/DSBNL
-
DSDNN
-
DSKNR/DSKNL
-
DTFNR/DTFNL
-
DTGNR/DTGNL
-
DVJNR/DVJNL
-
DVVNN
-
DWLNR/DWLNL
-
ECLNR/ECLNL
-
EDJNR/EDJNL
-
EVJNR/EVJNL
-
EWLNR/EWLNL
-
MCBNR/MCBNL
-
MCKNR/MCKNL
-
MCLNR/MCLNL
-
MCMNN
-
MDJNR/MDJNL
-
MDPNN
-
MDQNR/MDQNL
-
MRDNN
-
MRGNR/MRGNL
-
MSBNR/MSBNL
-
MSDNN
-
MSKNR/MSKNL
-
MSSNR/MSSNL
-
MTENN
-
MTFNR/MTFNL
-
MTGNR/MTGNL
-
MTJNR/MTJNL
-
MTQNR/MTQNL
-
MVJNR/MVJNL
-
MVQNR/MVQNL
-
MVUNR/MVUNL
-
MVVNN
-
MWLNR/MWLNL
-
PWLNR/PWLNL
-
PCLNR/PCLNL
-
PDJNR/PDJNL
-
PRACR/PRACL
-
PRDCN
-
PCBNR/PCBNL
-
PRGCR/PRGCL
-
PSBNR/PSBNL
-
PSDNN
-
PSSNR/PSSNL
-
PTGNR/PTGNL
-
PTTNR/PTTNL
-
SCLCR/SCLCL
-
SDJCR/SDJCL
-
SDNCN
-
SRACR/SRACL
-
SRDCN
-
SSDCN
-
SSSCR/SSSCL
-
STFCR/STFCL
-
SVACR/SVACL
-
SVJBR/SVJBL
-
SVJCR/SVJCL
-
SVVBN
-
SVVCN
-
WTENN
-
WTJNR/WTJNL
-
WWLNR/WWLNL
-
PDNNR/PDNNL
-
SVHBR/SVHBL
-
PDNNN
-
PTFNR/PTFNL
-
SCACR/SCACL
-
SDACR/SDACL
-
SSBCR/SSBCL
-
SRGCR/SRGCL
-
SSKCR/SSKCL
-
STGCR/STGCL
-
SVABR/SVABL
-
SVQCR/SVQCL
-
SWACR/SWACL
-
WTQNR/WTQNL
-
-
Державки резьбовые
-
Державки отрезные, канавочные
-
Держатели отрезного лезвия
-
Лезвия отрезные
-
Мини-резцы твердосплавные
-
-
Оснастка для фрезерных станков
-
Фрезерные патроны
-
BT
-
BT-ER (для цанг ER)
-
BT-FMB (для насадных фрез)
-
BT-SCA (для дисковых фрез)
-
BT-D (тестовые оправки)
-
BT-SLN Weldon
-
BT-MTA (конус Морзе с лапкой)
-
BT-MTB (конус Морзе с резьбовым отверстием)
-
BT-DC (высокоскоростные патроны для цанг DC)
-
BT-APU
-
BT-SC (для цилиндрических цанг SC)
-
BT-GT (для резьбовых цанг GT12/24/42)
-
BT-TER (патроны с осевой компенсацией по длине для цанг ER)
-
BT-OZ(EOC) (для силовых цанг OZ)
-
BT-PHC (гидропластовые патроны)
-
-
Конус Морзе MTA/MTB
-
HSK
-
Цилиндрический хвостовик
-
NT
-
SK
-
SK-FMB (для насадных фрез)
-
SK-SLN (Weldon)
-
SK-TER (патроны с осевой компенсацией по длине для цанг ER)
-
SK-SC (для цилиндрических цанг SC)
-
SK-MTB (конус Морзе с резьбовым отверстием)
-
SK-MTA (конус Морзе с лапкой)
-
SK-ER (для цанг ER)
-
SK-GT (для резьбовых цанг GT12/24/42)
-
SK-OZ(EOC) (для силовых цанг OZ)
-
SK-APU (сверлильные быстрозажимные патроны)
-
SK-PHC (гидропластовые патроны)
-
-
-
Прихваты, прижимы, упоры
-
Цанги
-
Штревели
-
3D тестеры
-
Тиски станочные
-
Аксессуары и запчасти
- Силовые высокоточные VQC
-
640 Multitasking
-
Трехкулачковые NBK
-
Гидравлические DCV
-
Модульные двойные ZQ83
-
С регулируемым усилием зажима HPAC
-
Самоцентрирующиеся SC-I
-
Модульные GT
-
Глобусные HHY
-
Лекальные QGG
-
Лекальные QKG
-
Модульные составные ZQ84
-
Гидравлические CHV
-
Самоцентрирующиеся двойные SMC
-
-
Кромкоискатели
-
Магнитные плиты
-
Центроискатели
-
Гайки для цанг
-
Ключи гаечные
-
Приспособления для оправок
-
Наборы прижимов
-
Расточные системы
-
Система нулевого базирования
-
Магнитные захваты
-
Поворотные столы
-
Аксессуары для станочной оснастки
-
Привязка по оси Z
-
-
Оснастка для токарных станков
-
Кулачки токарные
- Инструментальные блоки BOT
-
Токарные патроны
-
Центры токарные вращающиеся
- Центры вращающиеся
- Центры вращающиеся усиленные M11
- Центры вращающиеся облегченные
- Центры вращающиеся со сменными вставками
- Центры вращающиеся высокоскоростные
- Центры вращающиеся с твердосплавной вставкой
- Центры вращающиеся с удлиненной вершиной
- Центры вращающиеся усиленные
- Центры вращающиеся высокоточные
- Центры вращающиеся грибковые
-
Держатели осевого инструмента
-
Переходные втулки
-
Приспособления для расточки кулачков
-
Инструментальные блоки BMT
-
Центры токарные упорные
-
Сухари для токарных патронов
-
Инструментальные блоки VDI
-
Патроны цанговые
-
Цанги токарные
-
-
Измерительный инструмент
-
Станки
-
Станки ленточные по металлу
-
Лазерные граверы (маркировщики) по металлу
-
Токарные станки
-
Фрезерные станки
-
Заточные станки
-
Резьбонарезные манипуляторы
-
Электроэрозионные станки
-
Промышленные роботы
-
-
Мерч CNC66
-
Проволока, СОЖ, запчасти для электроэрозионных станков
-
Промышленная мебель
-
Запасные части для державок, резцов и фрез
-
Развертки
-
Упаковка
-
Зенковки
-
Плашки
-
Инструмент для снятия заусенцев
- выгрузка
-
Корзина пуста
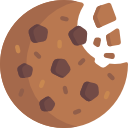
Мы используем файлы cookie для улучшения работы сайта и персонализации. Продолжая использовать сайт, вы соглашаетесь на сбор, обработку cookie-файлов и пользовательских данных с помощью Яндекс.Метрика, в соответствии с нашей Политикой конфиденциальности.