Тонкости притирки стальных деталей с абразивными пастами
Притирка — завершающий метод доводки сопрягаемых поверхностей, при котором снимаются микронные слои металла для получения точной геометрии и плотного прилегания. Чаще всего она применяется для посадки по классу H5 и выше, когда требуется минимальный зазор, например, в прецизионных парах скольжения.
Суть процесса — перемещение одной детали по другой с наличием мелкодисперсного твердого вещества между ними, служащего режущей микросредой.
Чаще всего используют составы на основе карбида кремния (SiC) или оксида алюминия (Al₂O₃). Первый тип применяют для твердых сталей, таких как ШХ15, Х12МФ, Р6М5, с твердостью выше 60 HRC.
Оксидные пасты чаще используют для среднеуглеродистых конструкционных сталей — 40Х, У8, Ст45. Размер зерна подбирается в зависимости от степени обработки: при начальной притирке берут зерно F100–F150 (100–150 мкм), а для доводки — не крупнее F400 (15 мкм). При необходимости финишной доводки сопряжений, зернистость снижают до F800–F1000 (3–5 мкм).
Базовый состав абразивной пасты включает не только зерна, но и связующее, часто на основе технического вазелина, солидола, или минерального масла. Жидкие связующие применяют при интенсивной подаче, когда важна равномерность распределения зерен и снижение локального перегрева.
В случае с ручной притиркой практичнее использовать пасты средней вязкости. Они обеспечивают хорошее удержание зерна между поверхностями и равномерный износ.
Притираемые поверхности предварительно шлифуют с точностью не ниже IT7. Риски от шлифования не должны быть ориентированы в направлении движения при притирке — иначе увеличится вероятность появления задиров.
Шероховатость базовой поверхности перед началом должна быть в пределах Ra 0,4–0,8 мкм. Если превышать эти значения, паста будет залипать в рисках, а движение детали станет неравномерным.
Для стальных деталей часто применяют притирочные плиты из чугуна СЧ20 или меди. Чугун удобен благодаря своей пористой структуре — абразив частично вдавливается в материал и создает рабочий слой.
Поверхность притира должна быть плоской, с отклонением не более 2 мкм на 100 мм. При необходимости точной геометрии используют метод наладки притира по контрольному калибру. Медь применяется в случае, когда нужно исключить риск повреждения деликатной геометрии детали.
Скорость перемещения при ручной обработке держат на уровне 20–40 мм/с. При машинной доводке — до 120 мм/с.
Усилие нажатия должно быть постоянным — порядка 20–50 Н, в зависимости от размера контактной зоны. При избыточной нагрузке абразивы могут врезаться в поверхность, образуя риски. Недостаточная сила прижатия приведет к неравномерной работе и снижению производительности.
Для деталей цилиндрической формы часто используют метод круговой притирки с перемещением по оси. Такая техника позволяет избежать зон перегрева и уменьшает вероятность локального износа.
При работе с фланцами или плоскими деталями лучше применять восьмеркообразное движение. Оно обеспечивает равномерную выработку, особенно на торцевых участках.
После каждого цикла притиранную поверхность промывают керосином или уайт-спиритом и просушивают. Повторное нанесение пасты на загрязненную поверхность снижает эффективность обработки.
Частицы металла, выработанные в процессе, образуют вторичные абразивные очаги, способные повредить геометрию. Поэтому использовать свежий состав предпочтительнее каждые 5–7 минут интенсивной работы.
Температурный режим влияет на вязкость пасты. При температурах выше +30 °C она становится слишком текучей, зерна соскальзывают, а эффективность резко падает.
В условиях повышенной температуры можно применять загущенные варианты на основе ЦИАТИМ-221 или аналогичных термостойких смазок. В прохладных помещениях оптимальны мягкие составы с низкой температурой застывания.
При точной доводке сопряжений с натягом 0,01–0,02 мм важно учитывать форму микроизноса. Поверхности должны быть притерты с сохранением микровпадин, которые удерживают масло.
Полностью гладкая поверхность снижает маслоудерживающую способность, что снижает срок службы соединения. Рекомендуется финишная обработка с зерном F1000 при доводке плунжеров, золотников и втулок.
Перед началом работы важно контролировать параметры шероховатости обеих поверхностей. Если одна из них будет иметь Ra более чем в два раза выше другой, износ будет происходить неравномерно, возможен увод геометрии.
Контрольный притир на тестовой пластине позволяет определить скорость съема металла. По опыту, при использовании пасты с зерном F320 скорость удаления составляет около 0,4 мкм/мин на стали 45 при усилии 30 Н.
Расход пасты зависит от геометрии и площади сопряжения. Для обработки контактной площади 10 см² в течение 10 минут при стандартной притирке потребуется около 1,5 г состава.
При механической обработке этот показатель выше — до 3 г за тот же период, особенно при работе на вращающемся притире. При доводке вала диаметром 20 мм на длине 30 мм типичный расход составляет 2 г пасты за 8 минут.
При шлифовке предварительно нужно выдерживать форму в допуске IT7–IT8, чтобы не было перекосов и пятен контакта. После притирки контролируют пятно контакта по краске.
Оно должно занимать не менее 80% рабочей поверхности при равномерной окраске без просветов. В случае, если контактная зона покрыта точками, это признак избыточной зернистости либо неправильного движения.
Инструменты для нанесения состава — шпатели, тампоны, кисти. В условиях мастерской практично использовать кусок фетра или войлока для распределения массы по поверхности.
Для небольших деталей можно воспользоваться деревянной палочкой, предварительно смоченной в масле. Это позволяет равномерно вводить состав в зону притирки, не перегружая контактную часть.
Часто встречается метод чередования зернистости: сначала используют F150, затем переходят на F320 и заканчивают F800. Промежуточная промывка между сменой состава обязательна — частицы крупного зерна могут повредить слой при доводке мелким.
В случае притирки клапанов или конусных соединений финишная стадия выполняется вручную, без дополнительного усилия, только под весом детали.
Контроль равномерности съема ведется по равномерности зеркального блеска. При наличии матовых пятен в краях зоны — необходимо повторное движение по той же траектории с меньшим количеством состава.
Повторное нанесение выполняется только после удаления старого слоя, иначе увеличится вероятность появления микрозадиров.
При обработке нержавеющих марок стали AISI 304, 316 и аналогичных необходимо учитывать склонность поверхности к наклепу. В таких случаях применяют минимальное давление и составы на масляной основе.
Повышенная вязкость смазки снижает микропластическую деформацию, улучшая финишную структуру. Абразив при этом выбирают только белый оксид алюминия с зерном F600 и выше.
- На главную
-
Категории
-
Пластины твердосплавные
-
Пластины токарные
-
Пластины для внутреннего и наружного точения
-
Пластины резьбовые
-
Пластины резьбовые ISO
-
Пластины резьбовые трапецеидального профиля, угол 30 град.
-
Пластины резьбовые неполного профиля, угол 55 или 60 град.
-
Пластины резьбовые для нарезания трубной резьбы Whitworth, правые
-
Пластины резьбовые NPT (дюймовая коническая резьба c углом профиля 60 град. и конус 1:16)
-
Пластины резьбовые BSPT (Британский стандарт) полного профиля, угол 55 град.
-
Пластины резьбовые треугольного закругленного профиля
-
Пластины резьбовые UN (Американский стандарт) полного профиля, угол 60 град.
- Пластины резьбовые UN (Американский стандарт) полного профиля, угол 60 град.
- Панцирная трубная резьба Pg 80 град.
- Пластины резьбовые трапецеидального профиля, угол 30 град.
- Пластины резьбовые BSPT (Британский стандарт) полного профиля, угол 55 град.
- Пластины резьбовые NPT (дюймовая коническая резьба c углом профиля 60 град. и конус 1:16)
- Пластины резьбовые неполного профиля, угол 55 или 60 град.
- Упорная резьба SAGE 30 град.
-
-
Пластины отрезные и канавочные
-
TGF32
-
SP
-
MRMN
-
MG...N
- GER-C
- SP для стали
- SP для нержавеющей стали
-
QCMB
-
QPMB
- MGMN для стали
- MGMN для нержавеющей стали
- QPMB для стали
- QPMB для нержавеющей стали
- MRMN для стали
- ZP_S для нержавеющей стали
-
ZP_S
- QCMB для нержавеющей стали
- ZT_D для нержавеющей стали
-
ZT_D
- ZT_D для стали
- QCMB для стали
- TDC для нержавеющей стали
-
TDC
- QC_ для нержавеющей стали
-
QC
- QC_
- ZP_D для нержавеющей стали
-
ZP_D
- ZR_D для нержавеющей стали
-
ZR_D
- ZT_S для нержавеющей стали
-
ZT_S
- ZQMX для стали
-
ZQMX
- CTPA для нержавеющей стали
-
CTPA
- MGMN для чугуна
- MRMN для нержавеющей стали
- MRMN для чугуна
-
GEL-A/B
- GEL-A
-
GEL-A/B-R
-
GEL-C/D/E
- GEL-C
-
GEL-C/D/E-R
-
GER-A/B
- GER-A
-
GER-A/B-R
-
GER-C/D/E
-
GER-C/D/E-R
- MGMN
- MGGN
- MB
- ZTKS
- JRMN
- GK-R
- ZRFD
- KTMD
- KGT
- JSMN
- SPDR
-
-
-
Пластины фрезерные
-
Пластины для сверл
-
Лезвия для резьбофрез
-
Пластины со вставками PCBN
- Пластины для червячного зуба 40°
-
-
Фрезы
-
Метчики
-
Сверла
-
Ленточные пилы
-
Новое поступление (NEW!)
-
Державки токарные
-
Державки расточные
-
S...-SVJCR/S...-SVJCL
-
S...-DCLNR/S...-DCLNL
-
S...-DDUNR/S...-DDUNL
-
S...-DWLNR/S...-DWLNL
-
S...-MCKNR/S...-MCKNL
-
S...-MCLNR/S...-MCLNL
-
S...-MDQNR/S...-MDQNL
-
S...-MDUNR/S...-MDUNL
-
S...-MSKNR/S-...MSKNL
-
S...-MTJNR/S...-MTJNL
-
S...-MTQNR/S...-MTQNL
-
S...-MTUNR/S...-MTUNL
-
S...-MTFNR/S...-MTFNL
-
S...-MTWNR/S...-MTWNL
-
S...-MVQNR/S-...MVQNL
-
S...-MVUNR/S-...MVUNL
-
S...-MVWNR/S...-MVWNL
-
S...-MVXNR/S...-MVXNL
-
S...-MWLNR/S...-MWLNL
-
S...-PCLNR/S...-PCLNL
-
S...-PDSNR/S...-PDSNL
-
S...-PDUNR/S...-PDUNL
-
S...-PSKNR/S...-PSKNL
-
S...-PWLNR/S...-PWLNL
-
S...-PTFNR/S...-PTFNL
-
S...-SCKCR/S...-SCKCL
-
S...-SCLCR/S...-SCLCL
-
S...-SCLPR/S...-SCLPL
-
S...-SDQCR/S...-SDQCL
-
S...-SDUCR/S...-SDUCL
-
S...-SDZCR/S...-SDZCL
-
S...-SSSCR/S...-SSSCL
-
S...-SSKCR/S...-SSKCL
-
S...-STFCR/S-...STFCL
-
S...-STUCR/S-...STUCL
-
S...-SVUCR/S-...SVUCL
-
S...-SVUBR/S...-SVUBL
-
-
Державки проходные
-
CCLNR/CCLNL
-
CRDNN
-
CSDNN
-
CSKNR/CSKNL
-
CTJNR/CTJNL
-
DCBNR/DCBNL
-
DCKNR/DCKNL
-
DCLNR/DCLNL
-
DCMNN
-
DDJNR/DDJNL
-
DDPNN
-
DSSNR/DSSNL
-
DDQNR/DDQNL
-
DSBNR/DSBNL
-
DSDNN
-
DSKNR/DSKNL
-
DTFNR/DTFNL
-
DTGNR/DTGNL
-
DVJNR/DVJNL
-
DVVNN
-
DWLNR/DWLNL
-
ECLNR/ECLNL
-
EDJNR/EDJNL
-
EVJNR/EVJNL
-
EWLNR/EWLNL
-
MCBNR/MCBNL
-
MCKNR/MCKNL
-
MCLNR/MCLNL
-
MCMNN
-
MDJNR/MDJNL
-
MDPNN
-
MDQNR/MDQNL
-
MRDNN
-
MRGNR/MRGNL
-
MSBNR/MSBNL
-
MSDNN
-
MSKNR/MSKNL
-
MSSNR/MSSNL
-
MTENN
-
MTFNR/MTFNL
-
MTGNR/MTGNL
-
MTJNR/MTJNL
-
MTQNR/MTQNL
-
MVJNR/MVJNL
-
MVQNR/MVQNL
-
MVUNR/MVUNL
-
MVVNN
-
MWLNR/MWLNL
-
PWLNR/PWLNL
-
PCLNR/PCLNL
-
PDJNR/PDJNL
-
PRACR/PRACL
-
PRDCN
-
PCBNR/PCBNL
-
PRGCR/PRGCL
-
PSBNR/PSBNL
-
PSDNN
-
PSSNR/PSSNL
-
PTGNR/PTGNL
-
PTTNR/PTTNL
-
SCLCR/SCLCL
-
SDJCR/SDJCL
-
SDNCN
-
SRACR/SRACL
-
SRDCN
-
SSDCN
-
SSSCR/SSSCL
-
STFCR/STFCL
-
SVACR/SVACL
-
SVJBR/SVJBL
-
SVJCR/SVJCL
-
SVVBN
-
SVVCN
-
WTENN
-
WTJNR/WTJNL
-
WWLNR/WWLNL
-
PDNNR/PDNNL
-
SVHBR/SVHBL
-
PDNNN
-
PTFNR/PTFNL
-
SCACR/SCACL
-
SDACR/SDACL
-
SSBCR/SSBCL
-
SRGCR/SRGCL
-
SSKCR/SSKCL
-
STGCR/STGCL
-
SVABR/SVABL
-
SVQCR/SVQCL
-
SWACR/SWACL
-
WTQNR/WTQNL
-
-
Державки резьбовые
-
Державки отрезные, канавочные
-
Держатели отрезного лезвия
-
Лезвия отрезные
-
Мини-резцы твердосплавные
-
-
Оснастка для фрезерных станков
-
Фрезерные патроны
-
BT
-
BT-ER (для цанг ER)
-
BT-FMB (для насадных фрез)
-
BT-SCA (для дисковых фрез)
-
BT-D (тестовые оправки)
-
BT-SLN Weldon
-
BT-MTA (конус Морзе с лапкой)
-
BT-MTB (конус Морзе с резьбовым отверстием)
-
BT-DC (высокоскоростные патроны для цанг DC)
-
BT-APU
-
BT-SC (для цилиндрических цанг SC)
-
BT-GT (для резьбовых цанг GT12/24/42)
-
BT-TER (патроны с осевой компенсацией по длине для цанг ER)
-
BT-OZ(EOC) (для силовых цанг OZ)
-
BT-PHC (гидропластовые патроны)
-
-
Конус Морзе MTA/MTB
-
HSK
-
Цилиндрический хвостовик
-
NT
-
SK
-
SK-FMB (для насадных фрез)
-
SK-SLN (Weldon)
-
SK-TER (патроны с осевой компенсацией по длине для цанг ER)
-
SK-SC (для цилиндрических цанг SC)
-
SK-MTB (конус Морзе с резьбовым отверстием)
-
SK-MTA (конус Морзе с лапкой)
-
SK-ER (для цанг ER)
-
SK-GT (для резьбовых цанг GT12/24/42)
-
SK-OZ(EOC) (для силовых цанг OZ)
-
SK-APU (сверлильные быстрозажимные патроны)
-
SK-PHC (гидропластовые патроны)
-
-
-
Прихваты, прижимы, упоры
-
Цанги
-
Штревели
-
3D тестеры
-
Тиски станочные
-
Аксессуары и запчасти
- Силовые высокоточные VQC
-
640 Multitasking
-
Трехкулачковые NBK
-
Гидравлические DCV
-
Модульные двойные ZQ83
-
С регулируемым усилием зажима HPAC
-
Самоцентрирующиеся SC-I
-
Модульные GT
-
Глобусные HHY
-
Лекальные QGG
-
Лекальные QKG
-
Модульные составные ZQ84
-
Гидравлические CHV
-
Самоцентрирующиеся двойные SMC
-
-
Кромкоискатели
-
Магнитные плиты
-
Центроискатели
-
Гайки для цанг
-
Ключи гаечные
-
Приспособления для оправок
-
Наборы прижимов
-
Расточные системы
-
Система нулевого базирования
-
Магнитные захваты
-
Поворотные столы
-
Аксессуары для станочной оснастки
-
Привязка по оси Z
-
Защитные вставки
-
-
Оснастка для токарных станков
-
Кулачки токарные
- Инструментальные блоки BOT
-
Токарные патроны
-
Центры токарные вращающиеся
- Центры вращающиеся
- Центры вращающиеся усиленные M11
- Центры вращающиеся облегченные
- Центры вращающиеся со сменными вставками
- Центры вращающиеся высокоскоростные
- Центры вращающиеся с твердосплавной вставкой
- Центры вращающиеся с удлиненной вершиной
- Центры вращающиеся усиленные
- Центры вращающиеся высокоточные
- Центры вращающиеся грибковые
-
Держатели осевого инструмента
-
Переходные втулки
-
Приспособления для расточки кулачков
-
Инструментальные блоки BMT
-
Центры токарные упорные
-
Сухари для токарных патронов
-
Инструментальные блоки VDI
-
Патроны цанговые
-
Цанги токарные
-
-
Измерительный инструмент
-
Станки
-
Станки ленточные по металлу
-
Лазерные граверы (маркировщики) по металлу
-
Токарные станки
-
Фрезерные станки
-
Заточные станки
-
Резьбонарезные манипуляторы
-
Электроэрозионные станки
-
Промышленные роботы
-
-
Мерч CNC66
-
Проволока, СОЖ, запчасти для электроэрозионных станков
-
Промышленная мебель
-
Запасные части для державок, резцов и фрез
-
Развертки
-
Упаковка
-
Зенковки
-
Плашки
-
Инструмент для снятия заусенцев
-
Корзина пуста
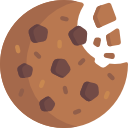
Мы используем файлы cookie для улучшения работы сайта и персонализации. Продолжая использовать сайт, вы соглашаетесь на сбор, обработку cookie-файлов и пользовательских данных с помощью Яндекс.Метрика, в соответствии с нашей Политикой конфиденциальности.