Сварка в воде: мифы и реальные способы
Погружение металлоконструкций под воду не делает невозможной работу с ними. В морской и речной инженерии применяются технологии, позволяющие соединять элементы в условиях полной или частичной затопленности.
Для выполнения соединений в жидкости применяют два основных способа: мокрый и сухой. Первый используется чаще из-за меньших затрат, однако требует особых навыков, иначе качество шва резко снижается.
В мокром методе сварщик работает в воде в специальном костюме с подачей кислорода. Используются электроды с покрытием, устойчивым к воздействию воды. На практике применяются типы УОНИИ-13/55, МР-3 и ОЗЛ-6. Для работы на глубине до 30 метров подойдут электроды диаметром 4 мм с рутиловым или основным покрытием.
При больших глубинах возможно применение электродов Ø 5 мм с повышенным содержанием легирующих элементов. Угол наклона электрода должен составлять 45–60 градусов к поверхности детали, иначе дуга будет нестабильной. При переменном токе длина дуги не должна превышать 3 мм.
В сухом варианте создаётся герметичная камера с подачей воздуха, вытесняющего воду. Такой метод применяется для точных соединений, когда необходимо обеспечить повышенную прочность. Камера оснащается осветительными приборами, вентиляцией, средствами наблюдения.
Внутри обеспечивают давление, соответствующее глубине. При превышении 10 метров давление внутри камеры составляет около 2 атмосферы. Сварку ведут в среде защитных газов или с использованием порошковой проволоки. Расход аргона достигает 10 литров в минуту при работе на режимах 180–200 ампер.
Наиболее распространённая ошибка – попытка использовать обычные электроды, предназначенные для сухих условий. При контакте с водой они разрушаются, а изоляция провода обугливается. Подходит только специально подготовленный инструмент. Класс защиты сварочного кабеля – не ниже IP68.
Питание подаётся через трансформатор с защитой от утечки. Сечение кабеля должно соответствовать мощности аппарата: при 200 амперах – не менее 25 мм². Прокладка кабеля осуществляется в герметичной изоляции с гидрофобной пропиткой.
В условиях полной затопленности часто возникают брызги расплавленного металла. Чтобы снизить их количество, сварку ведут короткой дугой, уменьшая напряжение на 10–15% от сухого режима. Если при обычной сварке ток устанавливается на уровне 120 ампер, то под водой – 100–105. Также желательно использовать устройства с плавной регулировкой, чтобы оперативно менять параметры без подъема к поверхности.
Стыковку трубопроводов под водой осуществляют кольцевыми швами. Диаметр свариваемых труб варьируется от 50 до 400 мм, стенка – от 5 до 12 мм. Перед работой торцы очищаются от загрязнений, ржавчины и морских отложений. Применяется абразивная обработка с помощью гидропескоструйного аппарата. Минимальный радиус кривизны при соединении труб – 1,5 диаметра. При меньших значениях возрастает риск образования трещин на переходах.
Для сварки металлических конструкций применяют полярность обратную, так как она даёт более глубокое проплавление. В случае прямой полярности увеличивается разбрызгивание и ухудшается формирование шва. Инверторы с цифровым управлением позволяют быстрее настраивать параметры, особенно в нестабильной среде. Влагозащищенные модели, такие как модели с IP67, допускаются к использованию до глубины 15 метров без изменения рабочих характеристик.
Работа с алюминием в подводных условиях затруднена из-за быстрого окисления поверхности. Применяют аргонодуговую сварку с использованием неплавящегося вольфрамового электрода. Для обеспечения стабильной дуги необходим постоянный ток и тщательная зачистка кромок. Ширина разделки – 2–3 мм, при толщине металла до 6 мм. Газ подаётся через узкое сопло под давлением до 1,5 атмосферы. Расход аргона при этом – 12–15 л/мин.
Чугун практически не соединяется под водой из-за пористой структуры и высокого содержания углерода. Даже при использовании специальных покрытий результат нестабилен. Лучше выполнить вставку или фланцевое соединение вне жидкости и погрузить уже собранный блок.
Оценка качества соединения под водой проводится визуально, по структуре наплавленного валика. При неравномерной форме и наличии кратеров работу повторяют. Наплывы и подрезы устраняются механически. Для зачистки шва используют подводные шлифмашины с гидроприводом. Диаметр круга – 125 мм, скорость вращения – до 9000 об/мин, давление в системе – от 6 до 10 МПа.
Для крепления пластин к корпусу судна применяют угловые соединения с прокладкой уплотнительных элементов. Толщина пластины – от 6 до 14 мм. Расстояние от края до шва – не менее 10 мм. Положение пластины фиксируется временными прихватками длиной до 25 мм через каждые 100 мм.
При температуре воды ниже +4°C снижается вязкость металла, что приводит к хрупкости соединения. Для стальных деталей толщиной 10–12 мм рекомендуется предварительный подогрев, если работа ведётся при глубине менее 5 м и открытом пространстве. Температура нагрева – до 80°C с последующей сваркой на токе до 140 ампер.
Часто возникает вопрос о применении полуавтоматических аппаратов. При наличии сухой камеры допускается использование проволоки диаметром 0,8–1,2 мм. Рекомендуемая скорость подачи – 6–10 м/мин. Положение горелки строго под углом 70° к плоскости детали, иначе проволока залипает на поверхности.
В случае ремонта свайного основания под мостом, швы наносят точечно, фиксируя основную арматуру через каждые 300 мм. Толщина арматурного стержня – 16–25 мм. Учитывается коррозийная стойкость – применяются нержавеющие стали марок 08Х18Н10Т и 10Х17Н13М2Т.
Монтаж элементов из низколегированных сталей допускается при толщине от 8 до 20 мм, при этом усилие фиксации перед сваркой – не менее 300 Н. Применение струбцин возможно при глубине до 12 метров, выше – только фиксирующие замки с антикоррозийным покрытием.
По мере увеличения глубины работа осложняется за счёт изменения давления, снижения освещённости и увеличения сопротивления среды. Поэтому часто применяются роботы-манипуляторы, особенно при монтаже трубопроводов на глубине свыше 30 метров. Механическое соединение выполняется при помощи гидравлических устройств, а провар осуществляется дистанционно через управляемую платформу.
Мифы об опасности сварки в воде безосновательны при соблюдении технологических параметров. Работы подобного рода выполняются десятилетиями в судостроении, при ремонте нефтяных платформ, обустройстве портовых сооружений. Главное – знание методики, точный подбор оборудования и строгое соблюдение режимов. Это трудоёмкий, но вполне реализуемый процесс, требующий высокой квалификации исполнителя и точного расчёта каждого действия.
- На главную
-
Категории
-
Пластины
-
Пластины токарные
-
Пластины для внутреннего и наружного точения
-
Пластины резьбовые
-
Пластины резьбовые ISO
-
Пластины резьбовые трапецеидального профиля, угол 30 град.
-
Пластины резьбовые неполного профиля, угол 55 или 60 град.
-
Пластины резьбовые для нарезания трубной резьбы Whitworth, правые
-
Пластины резьбовые NPT (дюймовая коническая резьба c углом профиля 60 град. и конус 1:16)
-
Пластины резьбовые BSPT (Британский стандарт) полного профиля, угол 55 град.
-
Пластины резьбовые треугольного закругленного профиля
-
Пластины резьбовые UN (Американский стандарт) полного профиля, угол 60 град.
-
-
Пластины отрезные и канавочные
-
TGF32
-
SP
-
MRMN
-
MG...N
- GER-C
- SP для стали
- SP для нержавеющей стали
-
QCMB
-
QPMB
- MGMN для стали
- MGMN для нержавеющей стали
- QPMB для стали
- QPMB для нержавеющей стали
- MRMN для стали
- ZP_S для нержавеющей стали
-
ZP_S
- QCMB для нержавеющей стали
- ZT_D для нержавеющей стали
-
ZT_D
- ZT_D для стали
- QCMB для стали
- TDC для нержавеющей стали
-
TDC
- QC_ для нержавеющей стали
-
QC
- QC_
- ZP_D для нержавеющей стали
-
ZP_D
- ZR_D для нержавеющей стали
-
ZR_D
- ZT_S для нержавеющей стали
-
ZT_S
- ZQMX для стали
-
ZQMX
- CTPA для нержавеющей стали
-
CTPA
- MGMN для чугуна
- MRMN для нержавеющей стали
- MRMN для чугуна
-
GEL-A/B
- GEL-A
-
GEL-A/B-R
-
GEL-C/D/E
- GEL-C
-
GEL-C/D/E-R
-
GER-A/B
- GER-A
-
GER-A/B-R
-
GER-C/D/E
-
GER-C/D/E-R
-
-
-
Пластины фрезерные
-
Пластины для свёрл
-
Лезвия для резьбофрез
-
Пластины со вставками PCBN
-
-
Фрезы
-
Метчики
-
Сверла
-
Ленточные пилы
-
Новое поступление (NEW!)
-
Державки токарные
-
Державки расточные
-
S...-SVJCR/S...-SVJCL
-
S...-DCLNR/S...-DCLNL
-
S...-DDUNR/S...-DDUNL
-
S...-DWLNR/S...-DWLNL
-
S...-MCKNR/S...-MCKNL
-
S...-MCLNR/S...-MCLNL
-
S...-MDQNR/S...-MDQNL
-
S...-MDUNR/S...-MDUNL
-
S...-MSKNR/S-...MSKNL
-
S...-MTJNR/S...-MTJNL
-
S...-MTQNR/S...-MTQNL
-
S...-MTUNR/S...-MTUNL
-
S...-MTFNR/S...-MTFNL
-
S...-MTWNR/S...-MTWNL
-
S...-MVQNR/S-...MVQNL
-
S...-MVUNR/S-...MVUNL
-
S...-MVWNR/S...-MVWNL
-
S...-MVXNR/S...-MVXNL
-
S...-MWLNR/S...-MWLNL
-
S...-PCLNR/S...-PCLNL
-
S...-PDSNR/S...-PDSNL
-
S...-PDUNR/S...-PDUNL
-
S...-PSKNR/S...-PSKNL
-
S...-PWLNR/S...-PWLNL
-
S...-PTFNR/S...-PTFNL
-
S...-SCKCR/S...-SCKCL
-
S...-SCLCR/S...-SCLCL
-
S...-SCLPR/S...-SCLPL
-
S...-SDQCR/S...-SDQCL
-
S...-SDUCR/S...-SDUCL
-
S...-SDZCR/S...-SDZCL
-
S...-SSSCR/S...-SSSCL
-
S...-SSKCR/S...-SSKCL
-
S...-STFCR/S-...STFCL
-
S...-STUCR/S-...STUCL
-
S...-SVUCR/S-...SVUCL
-
S...-SVUBR/S...-SVUBL
-
-
Державки проходные
-
CCLNR/CCLNL
-
CRDNN
-
CSDNN
-
CSKNR/CSKNL
-
CTJNR/CTJNL
-
DCBNR/DCBNL
-
DCKNR/DCKNL
-
DCLNR/DCLNL
-
DCMNN
-
DDJNR/DDJNL
-
DDPNN
-
DSSNR/DSSNL
-
DDQNR/DDQNL
-
DSBNR/DSBNL
-
DSDNN
-
DSKNR/DSKNL
-
DTFNR/DTFNL
-
DTGNR/DTGNL
-
DVJNR/DVJNL
-
DVVNN
-
DWLNR/DWLNL
-
ECLNR/ECLNL
-
EDJNR/EDJNL
-
EVJNR/EVJNL
-
EWLNR/EWLNL
-
MCBNR/MCBNL
-
MCKNR/MCKNL
-
MCLNR/MCLNL
-
MCMNN
-
MDJNR/MDJNL
-
MDPNN
-
MDQNR/MDQNL
-
MRDNN
-
MRGNR/MRGNL
-
MSBNR/MSBNL
-
MSDNN
-
MSKNR/MSKNL
-
MSSNR/MSSNL
-
MTENN
-
MTFNR/MTFNL
-
MTGNR/MTGNL
-
MTJNR/MTJNL
-
MTQNR/MTQNL
-
MVJNR/MVJNL
-
MVQNR/MVQNL
-
MVUNR/MVUNL
-
MVVNN
-
MWLNR/MWLNL
-
PWLNR/PWLNL
-
PCLNR/PCLNL
-
PDJNR/PDJNL
-
PRACR/PRACL
-
PRDCN
-
PCBNR/PCBNL
-
PRGCR/PRGCL
-
PSBNR/PSBNL
-
PSDNN
-
PSSNR/PSSNL
-
PTGNR/PTGNL
-
PTTNR/PTTNL
-
SCLCR/SCLCL
-
SDJCR/SDJCL
-
SDNCN
-
SRACR/SRACL
-
SRDCN
-
SSDCN
-
SSSCR/SSSCL
-
STFCR/STFCL
-
SVACR/SVACL
-
SVJBR/SVJBL
-
SVJCR/SVJCL
-
SVVBN
-
SVVCN
-
WTENN
-
WTJNR/WTJNL
-
WWLNR/WWLNL
-
PDNNR/PDNNL
-
SVHBR/SVHBL
-
PDNNN
-
PTFNR/PTFNL
-
SCACR/SCACL
-
SDACR/SDACL
-
SSBCR/SSBCL
-
SRGCR/SRGCL
-
SSKCR/SSKCL
-
STGCR/STGCL
-
SVABR/SVABL
-
SVQCR/SVQCL
-
SWACR/SWACL
-
WTQNR/WTQNL
-
-
Державки резьбовые
-
Державки отрезные, канавочные
-
Держатели отрезного лезвия
-
Лезвия отрезные
-
Мини-резцы твердосплавные
-
-
Оснастка для фрезерных станков
-
Фрезерные патроны
-
BT
-
BT-ER (для цанг ER)
-
BT-FMB (для насадных фрез)
-
BT-SCA (для дисковых фрез)
-
BT-D (тестовые оправки)
-
BT-SLN Weldon
-
BT-MTA (конус Морзе с лапкой)
-
BT-MTB (конус Морзе с резьбовым отверстием)
-
BT-DC (высокоскоростные патроны для цанг DC)
-
BT-APU
-
BT-SC (для цилиндрических цанг SC)
-
BT-GT (для резьбовых цанг GT12/24/42)
-
BT-TER (патроны с осевой компенсацией по длине для цанг ER)
-
BT-OZ(EOC) (для силовых цанг OZ)
-
BT-PHC (гидропластовые патроны)
-
-
Конус Морзе MTA/MTB
-
HSK
-
Цилиндрический хвостовик
-
NT
-
SK
-
SK-FMB (для насадных фрез)
-
SK-SLN (Weldon)
-
SK-TER (патроны с осевой компенсацией по длине для цанг ER)
-
SK-SC (для цилиндрических цанг SC)
-
SK-MTB (конус Морзе с резьбовым отверстием)
-
SK-MTA (конус Морзе с лапкой)
-
SK-ER (для цанг ER)
-
SK-GT (для резьбовых цанг GT12/24/42)
-
SK-OZ(EOC) (для силовых цанг OZ)
-
SK-APU (сверлильные быстрозажимные патроны)
-
SK-PHC (гидропластовые патроны)
-
-
-
Прихваты, прижимы, упоры
-
Цанги
-
Штревели
-
3D тестеры
-
Тиски станочные
-
Аксессуары и запчасти
- Силовые высокоточные VQC
-
640 Multitasking
-
Трехкулачковые NBK
-
Гидравлические DCV
-
Модульные двойные ZQ83
-
С регулируемым усилием зажима HPAC
-
Самоцентрирующиеся SC-I
-
Модульные GT
-
Глобусные HHY
-
Лекальные QGG
-
Лекальные QKG
-
Модульные составные ZQ84
-
Гидравлические CHV
-
Самоцентрирующиеся двойные SMC
-
-
Кромкоискатели
-
Магнитные плиты
-
Центроискатели
-
Гайки для цанг
-
Ключи гаечные
-
Приспособления для оправок
-
Наборы прижимов
-
Расточные системы
-
Система нулевого базирования
-
Магнитные захваты
-
Поворотные столы
-
Аксессуары для станочной оснастки
-
Привязка по оси Z
-
-
Оснастка для токарных станков
-
Кулачки токарные
- Инструментальные блоки BOT
-
Токарные патроны
-
Центры токарные вращающиеся
- Центры вращающиеся
- Центры вращающиеся усиленные M11
- Центры вращающиеся облегченные
- Центры вращающиеся со сменными вставками
- Центры вращающиеся высокоскоростные
- Центры вращающиеся с твердосплавной вставкой
- Центры вращающиеся с удлиненной вершиной
- Центры вращающиеся усиленные
- Центры вращающиеся высокоточные
- Центры вращающиеся грибковые
-
Держатели осевого инструмента
-
Переходные втулки
-
Приспособления для расточки кулачков
-
Инструментальные блоки BMT
-
Центры токарные упорные
-
Сухари для токарных патронов
-
Инструментальные блоки VDI
-
Патроны цанговые
-
Цанги токарные
-
-
Измерительный инструмент
-
Станки
-
Станки ленточные по металлу
-
Лазерные граверы (маркировщики) по металлу
-
Токарные станки
-
Фрезерные станки
-
Заточные станки
-
Резьбонарезные манипуляторы
-
Электроэрозионные станки
-
Промышленные роботы
-
-
Мерч CNC66
-
Проволока, СОЖ, запчасти для электроэрозионных станков
-
Промышленная мебель
-
Запасные части для державок, резцов и фрез
-
Развертки
-
Упаковка
-
Зенковки
-
Плашки
-
Инструмент для снятия заусенцев
- выгрузка
-
Корзина пуста
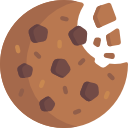
Мы используем файлы cookie для улучшения работы сайта и персонализации. Продолжая использовать сайт, вы соглашаетесь на сбор, обработку cookie-файлов и пользовательских данных с помощью Яндекс.Метрика, в соответствии с нашей Политикой конфиденциальности.