Шабрение металлических поверхностей вручную: когда оно нужно и как делать правильно
Ручное шабрение остается незаменимым при доводке ответственных поверхностей, где требуется высокая плоскостность и плотность прилегания. В отличие от шлифовки или фрезерования, этот способ позволяет добиться точности до 0,003 мм на длине 1 м, что критично для станин прецизионных станков или направляющих скольжения.
Для работы применяют шаберы с твердостью режущей кромки HRC 58-62. Угол заточки зависит от материала: 60-70° для чугуна, 40-50° для мягких сталей. Ширина лезвия обычно составляет 10-25 мм, а длина рабочей части – 150-300 мм. Инструмент изготавливают из инструментальных марок стали У10А или ХВГ.
Перед началом обработки поверхность покрывают тонким слоем синьки или сухой краски. Контрольную плиту или проверяемую деталь притирают к окрашенной плоскости, после чего выступающие участки становятся видны по пятнам красителя. Основная задача – последовательно снимать металл именно с этих отметин.
При черновом проходе снимают стружку толщиной 0,01-0,02 мм, двигая инструмент под углом 30-45° к направлению движения. Чистовое шабрение выполняют короткими штрихами длиной 5-10 мм с уменьшенным давлением. Критерием качества служит равномерное распределение 12-16 пятен на квадратном дюйме (25×25 мм) для поверхностей общего назначения.
В точном машиностроении требования жестче – здесь нормой считается 20-25 пятен в той же площади. Для достижения такого результата применяют трехгранные или ложкообразные шаберы, оставляющие узкую стружку шириной 2-3 мм. Усилие нажатия не должно превышать 5-7 кг, иначе вместо аккуратного срезания вершин микронеровностей произойдет задир материала.
Температура в цехе влияет на процесс – при нагреве свыше 22°C стальные детали начинают расширяться, что искажает результаты проверки. В таких случаях используют чугунные контрольные плиты, чей коэффициент теплового расширения ближе к обрабатываемой заготовке.
Особое внимание уделяют подготовке рабочего места. Верстак оборудуют деревянными подкладками, гасящими вибрации. Освещенность должна быть не менее 500 люкс, причем свет направляют под острым углом к плоскости – так лучше видны малейшие неровности.
Для алюминиевых сплавов применяют шаберы с отрицательным передним углом (-5°), предотвращающим залипание стружки. Чугун обрабатывают инструментом с радиусной заточкой, которая дробит стружку вместо образования длинных завитков.
После каждого прохода поверхность очищают щеткой с латунным ворсом, не оставляющим царапин. Окончательную проверку проводят через 2-3 часа, когда деталь стабилизирует свою геометрию после механического воздействия.
В ремонтных мастерских шабрение используют для восстановления посадочных мест под подшипники или направляющих суппортов. При износе до 0,1 мм применяют предварительное прошабривание с последующей обработкой пастой ГОИ. Более серьезные дефекты требуют механической обработки перед финишной доводкой.
Современные производственные стандарты допускают комбинирование ручного и механизированного шабрения. Пневматические или электрические шаберы с частотой ударов 2000-3000 в минуту ускоряют черновую стадию, но финишные операции все равно выполняют вручную.
Срок службы шабера до переточки составляет около 4-5 часов непрерывной работы. Для продления ресурса режущую кромку периодически правят на бруске из карбида кремния зернистостью М20-М40. Полную заточку делают на алмазном круге с охлаждением, чтобы избежать отпуска металла.
В метрологических лабораториях метод применяют для притирки поверочных плит класса 0 и 1. Здесь используют шаберы с шириной лезвия всего 3-5 мм, что обеспечивает локальное воздействие на микронеровности. Контроль ведут при помощи интерферометров, фиксирующих отклонения в доли микрона.
Опытные слесари определяют готовность поверхности на слух – при правильном шабрении инструмент издает короткий скрежещущий звук. Длинный визг означает чрезмерное давление, а глухой шум свидетельствует о затуплении кромки.
Для обучения новичков используют тренировочные плиты из мягкого чугуна СЧ20. На них отрабатывают базовые движения: "от себя" с постепенным увеличением нажима и "на себя" с ослаблением давления. Угол наклона инструмента меняют в пределах 15-75° в зависимости от требуемого характера стружки.
Восстановление геометрии станин протяженностью более 2 м требует применения длинных шаберов с рукоятками на обоих концах. Два работника синхронно обрабатывают поверхность, двигаясь от середины к краям. Такой способ исключает образование "прогиба" в центральной части.
При доводке ответственных соединений типа "ласточкин хвост" применяют фигурные шаберы, повторяющие профиль сопрягаемых деталей. Их изготавливают индивидуально для каждого узла, затачивая по шаблону из закаленной стали.
Сохранение традиционной технологии оправдано в случаях, где современные методы не обеспечивают нужной точности. Ручное шабрение по-прежнему остается эталоном при изготовлении прецизионных узлов, от которых зависит работа всего оборудования.
- На главную
-
Категории
-
Пластины твердосплавные
-
Пластины токарные
-
Пластины для внутреннего и наружного точения
-
Пластины резьбовые
-
Пластины резьбовые ISO
-
Пластины резьбовые трапецеидального профиля, угол 30 град.
-
Пластины резьбовые неполного профиля, угол 55 или 60 град.
-
Пластины резьбовые для нарезания трубной резьбы Whitworth, правые
-
Пластины резьбовые NPT (дюймовая коническая резьба c углом профиля 60 град. и конус 1:16)
-
Пластины резьбовые BSPT (Британский стандарт) полного профиля, угол 55 град.
-
Пластины резьбовые треугольного закругленного профиля
-
Пластины резьбовые UN (Американский стандарт) полного профиля, угол 60 град.
- Пластины резьбовые UN (Американский стандарт) полного профиля, угол 60 град.
- Панцирная трубная резьба Pg 80 град.
- Пластины резьбовые трапецеидального профиля, угол 30 град.
- Пластины резьбовые BSPT (Британский стандарт) полного профиля, угол 55 град.
- Пластины резьбовые NPT (дюймовая коническая резьба c углом профиля 60 град. и конус 1:16)
- Пластины резьбовые неполного профиля, угол 55 или 60 град.
- Упорная резьба SAGE 30 град.
-
-
Пластины отрезные и канавочные
-
TGF32
-
SP
-
MRMN
-
MG...N
- GER-C
- SP для стали
- SP для нержавеющей стали
-
QCMB
-
QPMB
- MGMN для стали
- MGMN для нержавеющей стали
- QPMB для стали
- QPMB для нержавеющей стали
- MRMN для стали
- ZP_S для нержавеющей стали
-
ZP_S
- QCMB для нержавеющей стали
- ZT_D для нержавеющей стали
-
ZT_D
- ZT_D для стали
- QCMB для стали
- TDC для нержавеющей стали
-
TDC
- QC_ для нержавеющей стали
-
QC
- QC_
- ZP_D для нержавеющей стали
-
ZP_D
- ZR_D для нержавеющей стали
-
ZR_D
- ZT_S для нержавеющей стали
-
ZT_S
- ZQMX для стали
-
ZQMX
- CTPA для нержавеющей стали
-
CTPA
- MGMN для чугуна
- MRMN для нержавеющей стали
- MRMN для чугуна
-
GEL-A/B
- GEL-A
-
GEL-A/B-R
-
GEL-C/D/E
- GEL-C
-
GEL-C/D/E-R
-
GER-A/B
- GER-A
-
GER-A/B-R
-
GER-C/D/E
-
GER-C/D/E-R
- MGMN
- MGGN
- MB
- ZTKS
- JRMN
- GK-R
- ZRFD
- KTMD
- KGT
- JSMN
- SPDR
-
-
-
Пластины фрезерные
-
Пластины для сверл
-
Лезвия для резьбофрез
-
Пластины со вставками PCBN
- Пластины для червячного зуба 40°
-
-
Фрезы
-
Метчики
-
Сверла
-
Ленточные пилы
-
Новое поступление (NEW!)
-
Державки токарные
-
Державки расточные
-
S...-SVJCR/S...-SVJCL
-
S...-DCLNR/S...-DCLNL
-
S...-DDUNR/S...-DDUNL
-
S...-DWLNR/S...-DWLNL
-
S...-MCKNR/S...-MCKNL
-
S...-MCLNR/S...-MCLNL
-
S...-MDQNR/S...-MDQNL
-
S...-MDUNR/S...-MDUNL
-
S...-MSKNR/S-...MSKNL
-
S...-MTJNR/S...-MTJNL
-
S...-MTQNR/S...-MTQNL
-
S...-MTUNR/S...-MTUNL
-
S...-MTFNR/S...-MTFNL
-
S...-MTWNR/S...-MTWNL
-
S...-MVQNR/S-...MVQNL
-
S...-MVUNR/S-...MVUNL
-
S...-MVWNR/S...-MVWNL
-
S...-MVXNR/S...-MVXNL
-
S...-MWLNR/S...-MWLNL
-
S...-PCLNR/S...-PCLNL
-
S...-PDSNR/S...-PDSNL
-
S...-PDUNR/S...-PDUNL
-
S...-PSKNR/S...-PSKNL
-
S...-PWLNR/S...-PWLNL
-
S...-PTFNR/S...-PTFNL
-
S...-SCKCR/S...-SCKCL
-
S...-SCLCR/S...-SCLCL
-
S...-SCLPR/S...-SCLPL
-
S...-SDQCR/S...-SDQCL
-
S...-SDUCR/S...-SDUCL
-
S...-SDZCR/S...-SDZCL
-
S...-SSSCR/S...-SSSCL
-
S...-SSKCR/S...-SSKCL
-
S...-STFCR/S-...STFCL
-
S...-STUCR/S-...STUCL
-
S...-SVUCR/S-...SVUCL
-
S...-SVUBR/S...-SVUBL
-
-
Державки проходные
-
CCLNR/CCLNL
-
CRDNN
-
CSDNN
-
CSKNR/CSKNL
-
CTJNR/CTJNL
-
DCBNR/DCBNL
-
DCKNR/DCKNL
-
DCLNR/DCLNL
-
DCMNN
-
DDJNR/DDJNL
-
DDPNN
-
DSSNR/DSSNL
-
DDQNR/DDQNL
-
DSBNR/DSBNL
-
DSDNN
-
DSKNR/DSKNL
-
DTFNR/DTFNL
-
DTGNR/DTGNL
-
DVJNR/DVJNL
-
DVVNN
-
DWLNR/DWLNL
-
ECLNR/ECLNL
-
EDJNR/EDJNL
-
EVJNR/EVJNL
-
EWLNR/EWLNL
-
MCBNR/MCBNL
-
MCKNR/MCKNL
-
MCLNR/MCLNL
-
MCMNN
-
MDJNR/MDJNL
-
MDPNN
-
MDQNR/MDQNL
-
MRDNN
-
MRGNR/MRGNL
-
MSBNR/MSBNL
-
MSDNN
-
MSKNR/MSKNL
-
MSSNR/MSSNL
-
MTENN
-
MTFNR/MTFNL
-
MTGNR/MTGNL
-
MTJNR/MTJNL
-
MTQNR/MTQNL
-
MVJNR/MVJNL
-
MVQNR/MVQNL
-
MVUNR/MVUNL
-
MVVNN
-
MWLNR/MWLNL
-
PWLNR/PWLNL
-
PCLNR/PCLNL
-
PDJNR/PDJNL
-
PRACR/PRACL
-
PRDCN
-
PCBNR/PCBNL
-
PRGCR/PRGCL
-
PSBNR/PSBNL
-
PSDNN
-
PSSNR/PSSNL
-
PTGNR/PTGNL
-
PTTNR/PTTNL
-
SCLCR/SCLCL
-
SDJCR/SDJCL
-
SDNCN
-
SRACR/SRACL
-
SRDCN
-
SSDCN
-
SSSCR/SSSCL
-
STFCR/STFCL
-
SVACR/SVACL
-
SVJBR/SVJBL
-
SVJCR/SVJCL
-
SVVBN
-
SVVCN
-
WTENN
-
WTJNR/WTJNL
-
WWLNR/WWLNL
-
PDNNR/PDNNL
-
SVHBR/SVHBL
-
PDNNN
-
PTFNR/PTFNL
-
SCACR/SCACL
-
SDACR/SDACL
-
SSBCR/SSBCL
-
SRGCR/SRGCL
-
SSKCR/SSKCL
-
STGCR/STGCL
-
SVABR/SVABL
-
SVQCR/SVQCL
-
SWACR/SWACL
-
WTQNR/WTQNL
-
-
Державки резьбовые
-
Державки отрезные, канавочные
-
Держатели отрезного лезвия
-
Лезвия отрезные
-
Мини-резцы твердосплавные
-
-
Оснастка для фрезерных станков
-
Фрезерные патроны
-
BT
-
BT-ER (для цанг ER)
-
BT-FMB (для насадных фрез)
-
BT-SCA (для дисковых фрез)
-
BT-D (тестовые оправки)
-
BT-SLN Weldon
-
BT-MTA (конус Морзе с лапкой)
-
BT-MTB (конус Морзе с резьбовым отверстием)
-
BT-DC (высокоскоростные патроны для цанг DC)
-
BT-APU
-
BT-SC (для цилиндрических цанг SC)
-
BT-GT (для резьбовых цанг GT12/24/42)
-
BT-TER (патроны с осевой компенсацией по длине для цанг ER)
-
BT-OZ(EOC) (для силовых цанг OZ)
-
BT-PHC (гидропластовые патроны)
-
-
Конус Морзе MTA/MTB
-
HSK
-
Цилиндрический хвостовик
-
NT
-
SK
-
SK-FMB (для насадных фрез)
-
SK-SLN (Weldon)
-
SK-TER (патроны с осевой компенсацией по длине для цанг ER)
-
SK-SC (для цилиндрических цанг SC)
-
SK-MTB (конус Морзе с резьбовым отверстием)
-
SK-MTA (конус Морзе с лапкой)
-
SK-ER (для цанг ER)
-
SK-GT (для резьбовых цанг GT12/24/42)
-
SK-OZ(EOC) (для силовых цанг OZ)
-
SK-APU (сверлильные быстрозажимные патроны)
-
SK-PHC (гидропластовые патроны)
-
-
-
Прихваты, прижимы, упоры
-
Цанги
-
Штревели
-
3D тестеры
-
Тиски станочные
-
Аксессуары и запчасти
- Силовые высокоточные VQC
-
640 Multitasking
-
Трехкулачковые NBK
-
Гидравлические DCV
-
Модульные двойные ZQ83
-
С регулируемым усилием зажима HPAC
-
Самоцентрирующиеся SC-I
-
Модульные GT
-
Глобусные HHY
-
Лекальные QGG
-
Лекальные QKG
-
Модульные составные ZQ84
-
Гидравлические CHV
-
Самоцентрирующиеся двойные SMC
-
-
Кромкоискатели
-
Магнитные плиты
-
Центроискатели
-
Гайки для цанг
-
Ключи гаечные
-
Приспособления для оправок
-
Наборы прижимов
-
Расточные системы
-
Система нулевого базирования
-
Магнитные захваты
-
Поворотные столы
-
Аксессуары для станочной оснастки
-
Привязка по оси Z
-
Защитные вставки
-
-
Оснастка для токарных станков
-
Кулачки токарные
- Инструментальные блоки BOT
-
Токарные патроны
-
Центры токарные вращающиеся
- Центры вращающиеся
- Центры вращающиеся усиленные M11
- Центры вращающиеся облегченные
- Центры вращающиеся со сменными вставками
- Центры вращающиеся высокоскоростные
- Центры вращающиеся с твердосплавной вставкой
- Центры вращающиеся с удлиненной вершиной
- Центры вращающиеся усиленные
- Центры вращающиеся высокоточные
- Центры вращающиеся грибковые
-
Держатели осевого инструмента
-
Переходные втулки
-
Приспособления для расточки кулачков
-
Инструментальные блоки BMT
-
Центры токарные упорные
-
Сухари для токарных патронов
-
Инструментальные блоки VDI
-
Патроны цанговые
-
Цанги токарные
-
-
Измерительный инструмент
-
Станки
-
Станки ленточные по металлу
-
Лазерные граверы (маркировщики) по металлу
-
Токарные станки
-
Фрезерные станки
-
Заточные станки
-
Резьбонарезные манипуляторы
-
Электроэрозионные станки
-
Промышленные роботы
-
-
Мерч CNC66
-
Проволока, СОЖ, запчасти для электроэрозионных станков
-
Промышленная мебель
-
Запасные части для державок, резцов и фрез
-
Развертки
-
Упаковка
-
Зенковки
-
Плашки
-
Инструмент для снятия заусенцев
-
Корзина пуста
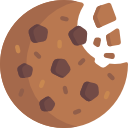
Мы используем файлы cookie для улучшения работы сайта и персонализации. Продолжая использовать сайт, вы соглашаетесь на сбор, обработку cookie-файлов и пользовательских данных с помощью Яндекс.Метрика, в соответствии с нашей Политикой конфиденциальности.