Производство стали в дуговых печах
В процессе производства стали в электродуговых печах в качестве основного исходного материала используется лом. В производстве могут быть использованы и другие железосодержащие материалы, чаще всего чугун и восстановленное железо.
Тип используемого материала существенно не влияет на ход плавки стали в электродуговой печи, однако химический состав перерабатываемого лома оказывает существенное влияние на технологию выплавки.
При переработке лома в дуговых печах используются три основные группы технологий:
- переработка нелегированного лома с одновременной плавкой и освежением газообразным кислородом;
- переработка лома сплавов восстановительными методами, без освежения газообразным кислородом или с ограниченным освежением;
- переработка высокохромистого лома восстановительными методами или с ограниченным освежением газообразным кислородом.
Независимо от типа используемой технологии производства стали, процесс производства в электродуговой печи включает в себя следующие этапы:
- послесливной ремонт печи;
- сборка, подготовка и загрузка партии;
- расплавление шихты;
- слив.
Сразу после выпуска металла из предыдущей плавки наступает этап, называемый послевыпускным ремонтом. Послевыпускной ремонт предназначен для подготовки всего печного оборудования к безопасной и экономичной плавке.
Такой ремонт включает в себя оценку технического состояния всех элементов конструкции, особенно состояние огнеупорной футеровки активной зоны, стенок, свода и выхода печи, графитовых электродов и устранение повреждений.
Независимо от восстановительного последренажного ремонта, для увеличения срока службы огнеупорной футеровки стен применяют так называемое торкретирование, т. е. напыление стен агрегата огнеупорными массами.
Состав и подготовка сырья
Металлошихта для плавки в электродуговой печи состоит из лома углеродистой и низколегированной стали и науглероживающих материалов. Материалом для цементации может быть чугун или кокс, уголь или электродный лом.
Биодоступность углерода в металлической ванне из чугуна составляет 100%. Чугун для шихты дуговых печей можно использовать не только для получения соответствующего содержания углерода в ванне, но и для снижения содержания неокисляющих компонентов в выпускаемой стали.
Металлическая ванна должна содержать металлолом после полного расплавления углерода. Соответствующее содержание углерода в металлической ванне необходимо для правильного проведения процесса освежения.
Благодаря процессу выплавки стали и получению соответствующего шлака необходимо оптимальное содержание ингредиентов в шихте. Особое внимание следует обратить на содержание кремния, марганца, хрома, фосфора и серы.
В шихте в количествах, не превышающих их допустимое содержание в выплавляемой марке стали, могут присутствовать компоненты, не окисляющиеся в процессе выплавки стали, такие как медь, никель, молибден, кобальт.
В шихту не следует добавлять другие компоненты стальных сплавов, подверженные в большей или меньшей степени окислению, особенно вольфрам, ванадий и титан. Эти элементы, так же как марганец и хром, в процессе выплавки стали окисляются, вызывая ухудшение физико-химических свойств шлака.
Следовательно, такие ингредиенты следует вводить в ванну металла при рафинировании стали, на заключительном этапе плавки в печи или вне печи – в процессах ковшовой металлургии. Шихта для электродуговой печи должна содержать также шлакообразующие материалы, например негашеную известь.
Помимо химического состава, большое значение для правильного проведения процесса плавки шихты имеет объемная масса лома и его расположение в печи. Наиболее благоприятные условия обеспечивает комплексная нагрузка из легкого лома, уложенного в корзину так, чтобы защитить активную зону печи от механических повреждений толстым и средним ломом, падающим при загрузке. Кроме того, загрузка должна содержать толстый лом, помещаемый непосредственно под электроды. Остаток должен составлять средний лом, размещенный у стенок печи.
Подготовленную с учетом вышеперечисленных критериев шихту загружают в печь с помощью специальных саморазгрузочных корзин. Корзины, предназначенные для загрузки печей малой и средней мощности, чаще всего закрываются снизу навесом, состоящим из шарнирных сегментов. Лом загружается из бункеров в корзину с помощью грейферов, подвешенных на мостовых кранах.
Плавка
После загрузки шихты и закрытия печи сводом включается электропитание и активируется система автоматического контроля положения электродов. Затем электроды опускаются, и при их соприкосновении с шихтой зажигается электрическая дуга и начинается процесс плавления лома.
Начальная фаза происходит с момента включения электричества до расплавления кратеров в металлоломе. Вторая фаза процесса включает плавление большей части лома и продолжается до тех пор, пока он не достигнет уровня металлической ванны.
Третий этап предполагает плавку лома, расположенного на периферии котла.
Завершающий этап – расплавление оставшихся нерасплавленных кусков лома у стенок котла и так называемый нагрев металлической ванны до соответствующей температуры.
С целью сокращения срока плавки лома с момента включения печного трансформатора на максимальную мощность приступают к приемам, интенсифицирующим этот процесс: вдуванию газообразного кислорода с помощью фурм и использованию газовых горелок.
С образованием металлической ванны в объем жидкого металла начинает вдуваться кислород. Тогда компоненты ванны, в том числе углерод, окисляются. Углерод – единственный элемент в ванне жидкого металла, который в результате реакции окисления образует газ – окись углерода.
Формирование пузырьков и их всплывание вызывает перемешивание ванны металла. Это явление очень полезно для выравнивания температуры в объеме ванны, ускорения процесса плавления лома, находящегося в холодных зонах.
В современной дуговой печи очень важную роль также играет химическая энергия, образующаяся при сгорании природного газа в результате реакции окисления железа из лома, окисления компонентов металлической ванны, таких как кремний и углерод, и дожигания окиси углерода.
Одновременно с плавлением шихты начинается процесс создания металлической ванны, растворяющий внесенный с кусковой шихтой углерод, окисляющий примеси ванны и образующий шлак. Шлак – это раствор оксидов, возникающий в результате реакций окисления неметаллических примесей лома, извести и износа огнеупорной футеровки.
Выпуск стали
Последним технологическим этапом производства стали в дуговой печи является выпуск металлической ванны, которая уже имеет химический состав готовой стали. Разливка производится в литейный ковш, расположенный под печью. На практике применяют два способа дренажа: через желоб или шахтное дренажное отверстие.
В случае желоба операцию выпуска начинают с размещения под печью разливочного ковша, подвешиваемого на мостовом кране. В случае шахтной летки разливочный ковш размещают на транспортной платформе, перемещающейся по направляющим, проложенным под печью, перпендикулярно длинной стороне печного зала.
Независимо от способа, необходимо следить за тем, чтобы при выпуске плавки в ковш не попал печной шлак. Эта операция непростая, поскольку при сливе жидкости из бака возникает явление завихрения.
После окончания выпуска стали печь наклоняют к рабочему окну и выпускают шлак. Шлак вывозится на свалки для дальнейшего использования, например, для нужд строительной и цементной промышленности.
При выпуске в ковш добавляют часть материалов для окончательного раскисления металлической ванны и шлакообразующих материалов. После выпуска ковш с жидким металлом транспортируют в литейный цех или на послепечной металлургический участок.
- На главную
-
Категории
-
Пластины
-
Пластины токарные
-
Пластины для внутреннего и наружного точения
-
Пластины резьбовые
-
Пластины резьбовые ISO
-
Пластины резьбовые трапецеидального профиля, угол 30 град.
-
Пластины резьбовые неполного профиля, угол 55 или 60 град.
-
Пластины резьбовые для нарезания трубной резьбы Whitworth, правые
-
Пластины резьбовые NPT (дюймовая коническая резьба c углом профиля 60 град. и конус 1:16)
-
Пластины резьбовые BSPT (Британский стандарт) полного профиля, угол 55 град.
-
Пластины резьбовые треугольного закругленного профиля
-
Пластины резьбовые UN (Американский стандарт) полного профиля, угол 60 град.
-
-
Пластины отрезные и канавочные
-
TGF32
-
SP
-
MRMN
-
MG...N
- GER-C
- SP для стали
- SP для нержавеющей стали
-
QCMB
-
QPMB
- MGMN для стали
- MGMN для нержавеющей стали
- QPMB для стали
- QPMB для нержавеющей стали
- MRMN для стали
- ZP_S для нержавеющей стали
-
ZP_S
- QCMB для нержавеющей стали
- ZT_D для нержавеющей стали
-
ZT_D
- ZT_D для стали
- QCMB для стали
- TDC для нержавеющей стали
-
TDC
- QC_ для нержавеющей стали
-
QC
- QC_
- ZP_D для нержавеющей стали
-
ZP_D
- ZR_D для нержавеющей стали
-
ZR_D
- ZT_S для нержавеющей стали
-
ZT_S
- ZQMX для стали
-
ZQMX
- CTPA для нержавеющей стали
-
CTPA
- MGMN для чугуна
- MRMN для нержавеющей стали
- MRMN для чугуна
-
GEL-A/B
- GEL-A
-
GEL-A/B-R
-
GEL-C/D/E
- GEL-C
-
GEL-C/D/E-R
-
GER-A/B
- GER-A
-
GER-A/B-R
-
GER-C/D/E
-
GER-C/D/E-R
-
-
-
Пластины фрезерные
-
Пластины для свёрл
-
Лезвия для резьбофрез
-
Пластины со вставками PCBN
-
-
Фрезы
-
Метчики
-
Сверла
-
Ленточные пилы
-
Новое поступление (NEW!)
-
Державки токарные
-
Державки расточные
-
S...-SVJCR/S...-SVJCL
-
S...-DCLNR/S...-DCLNL
-
S...-DDUNR/S...-DDUNL
-
S...-DWLNR/S...-DWLNL
-
S...-MCKNR/S...-MCKNL
-
S...-MCLNR/S...-MCLNL
-
S...-MDQNR/S...-MDQNL
-
S...-MDUNR/S...-MDUNL
-
S...-MSKNR/S-...MSKNL
-
S...-MTJNR/S...-MTJNL
-
S...-MTQNR/S...-MTQNL
-
S...-MTUNR/S...-MTUNL
-
S...-MTFNR/S...-MTFNL
-
S...-MTWNR/S...-MTWNL
-
S...-MVQNR/S-...MVQNL
-
S...-MVUNR/S-...MVUNL
-
S...-MVWNR/S...-MVWNL
-
S...-MVXNR/S...-MVXNL
-
S...-MWLNR/S...-MWLNL
-
S...-PCLNR/S...-PCLNL
-
S...-PDSNR/S...-PDSNL
-
S...-PDUNR/S...-PDUNL
-
S...-PSKNR/S...-PSKNL
-
S...-PWLNR/S...-PWLNL
-
S...-PTFNR/S...-PTFNL
-
S...-SCKCR/S...-SCKCL
-
S...-SCLCR/S...-SCLCL
-
S...-SCLPR/S...-SCLPL
-
S...-SDQCR/S...-SDQCL
-
S...-SDUCR/S...-SDUCL
-
S...-SDZCR/S...-SDZCL
-
S...-SSSCR/S...-SSSCL
-
S...-SSKCR/S...-SSKCL
-
S...-STFCR/S-...STFCL
-
S...-STUCR/S-...STUCL
-
S...-SVUCR/S-...SVUCL
-
S...-SVUBR/S...-SVUBL
-
-
Державки проходные
-
CCLNR/CCLNL
-
CRDNN
-
CSDNN
-
CSKNR/CSKNL
-
CTJNR/CTJNL
-
DCBNR/DCBNL
-
DCKNR/DCKNL
-
DCLNR/DCLNL
-
DCMNN
-
DDJNR/DDJNL
-
DDPNN
-
DSSNR/DSSNL
-
DDQNR/DDQNL
-
DSBNR/DSBNL
-
DSDNN
-
DSKNR/DSKNL
-
DTFNR/DTFNL
-
DTGNR/DTGNL
-
DVJNR/DVJNL
-
DVVNN
-
DWLNR/DWLNL
-
ECLNR/ECLNL
-
EDJNR/EDJNL
-
EVJNR/EVJNL
-
EWLNR/EWLNL
-
MCBNR/MCBNL
-
MCKNR/MCKNL
-
MCLNR/MCLNL
-
MCMNN
-
MDJNR/MDJNL
-
MDPNN
-
MDQNR/MDQNL
-
MRDNN
-
MRGNR/MRGNL
-
MSBNR/MSBNL
-
MSDNN
-
MSKNR/MSKNL
-
MSSNR/MSSNL
-
MTENN
-
MTFNR/MTFNL
-
MTGNR/MTGNL
-
MTJNR/MTJNL
-
MTQNR/MTQNL
-
MVJNR/MVJNL
-
MVQNR/MVQNL
-
MVUNR/MVUNL
-
MVVNN
-
MWLNR/MWLNL
-
PWLNR/PWLNL
-
PCLNR/PCLNL
-
PDJNR/PDJNL
-
PRACR/PRACL
-
PRDCN
-
PCBNR/PCBNL
-
PRGCR/PRGCL
-
PSBNR/PSBNL
-
PSDNN
-
PSSNR/PSSNL
-
PTGNR/PTGNL
-
PTTNR/PTTNL
-
SCLCR/SCLCL
-
SDJCR/SDJCL
-
SDNCN
-
SRACR/SRACL
-
SRDCN
-
SSDCN
-
SSSCR/SSSCL
-
STFCR/STFCL
-
SVACR/SVACL
-
SVJBR/SVJBL
-
SVJCR/SVJCL
-
SVVBN
-
SVVCN
-
WTENN
-
WTJNR/WTJNL
-
WWLNR/WWLNL
-
PDNNR/PDNNL
-
SVHBR/SVHBL
-
PDNNN
-
PTFNR/PTFNL
-
SCACR/SCACL
-
SDACR/SDACL
-
SSBCR/SSBCL
-
SRGCR/SRGCL
-
SSKCR/SSKCL
-
STGCR/STGCL
-
SVABR/SVABL
-
SVQCR/SVQCL
-
SWACR/SWACL
-
WTQNR/WTQNL
-
-
Державки резьбовые
-
Державки отрезные, канавочные
-
Держатели отрезного лезвия
-
Лезвия отрезные
-
Мини-резцы твердосплавные
-
-
Оснастка для фрезерных станков
-
Фрезерные патроны
-
BT
-
BT-ER (для цанг ER)
-
BT-FMB (для насадных фрез)
-
BT-SCA (для дисковых фрез)
-
BT-D (тестовые оправки)
-
BT-SLN Weldon
-
BT-MTA (конус Морзе с лапкой)
-
BT-MTB (конус Морзе с резьбовым отверстием)
-
BT-DC (высокоскоростные патроны для цанг DC)
-
BT-APU
-
BT-SC (для цилиндрических цанг SC)
-
BT-GT (для резьбовых цанг GT12/24/42)
-
BT-TER (патроны с осевой компенсацией по длине для цанг ER)
-
BT-OZ(EOC) (для силовых цанг OZ)
-
BT-PHC (гидропластовые патроны)
-
-
Конус Морзе MTA/MTB
-
HSK
-
Цилиндрический хвостовик
-
NT
-
SK
-
SK-FMB (для насадных фрез)
-
SK-SLN (Weldon)
-
SK-TER (патроны с осевой компенсацией по длине для цанг ER)
-
SK-SC (для цилиндрических цанг SC)
-
SK-MTB (конус Морзе с резьбовым отверстием)
-
SK-MTA (конус Морзе с лапкой)
-
SK-ER (для цанг ER)
-
SK-GT (для резьбовых цанг GT12/24/42)
-
SK-OZ(EOC) (для силовых цанг OZ)
-
SK-APU (сверлильные быстрозажимные патроны)
-
SK-PHC (гидропластовые патроны)
-
-
-
Прихваты, прижимы, упоры
-
Цанги
-
Штревели
-
3D тестеры
-
Тиски станочные
-
Аксессуары и запчасти
- Силовые высокоточные VQC
-
640 Multitasking
-
Трехкулачковые NBK
-
Гидравлические DCV
-
Модульные двойные ZQ83
-
С регулируемым усилием зажима HPAC
-
Самоцентрирующиеся SC-I
-
Модульные GT
-
Глобусные HHY
-
Лекальные QGG
-
Лекальные QKG
-
Модульные составные ZQ84
-
Гидравлические CHV
-
Самоцентрирующиеся двойные SMC
-
-
Кромкоискатели
-
Магнитные плиты
-
Центроискатели
-
Гайки для цанг
-
Ключи гаечные
-
Приспособления для оправок
-
Наборы прижимов
-
Расточные системы
-
Система нулевого базирования
-
Магнитные захваты
-
Поворотные столы
-
Аксессуары для станочной оснастки
-
Привязка по оси Z
-
-
Оснастка для токарных станков
-
Кулачки токарные
- Инструментальные блоки BOT
-
Токарные патроны
-
Центры токарные вращающиеся
- Центры вращающиеся
- Центры вращающиеся усиленные M11
- Центры вращающиеся облегченные
- Центры вращающиеся со сменными вставками
- Центры вращающиеся высокоскоростные
- Центры вращающиеся с твердосплавной вставкой
- Центры вращающиеся с удлиненной вершиной
- Центры вращающиеся усиленные
- Центры вращающиеся высокоточные
- Центры вращающиеся грибковые
-
Держатели осевого инструмента
-
Переходные втулки
-
Приспособления для расточки кулачков
-
Инструментальные блоки BMT
-
Центры токарные упорные
-
Сухари для токарных патронов
-
Инструментальные блоки VDI
-
Патроны цанговые
-
Цанги токарные
-
-
Измерительный инструмент
-
Станки
-
Станки ленточные по металлу
-
Лазерные граверы (маркировщики) по металлу
-
Токарные станки
-
Фрезерные станки
-
Заточные станки
-
Резьбонарезные манипуляторы
-
Электроэрозионные станки
-
Промышленные роботы
-
-
Мерч CNC66
-
Проволока, СОЖ, запчасти для электроэрозионных станков
-
Промышленная мебель
-
Запасные части для державок, резцов и фрез
-
Развертки
-
Упаковка
-
Зенковки
-
Плашки
-
Инструмент для снятия заусенцев
- выгрузка
-
Корзина пуста
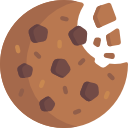
Мы используем файлы cookie для улучшения работы сайта и персонализации. Продолжая использовать сайт, вы соглашаетесь на сбор, обработку cookie-файлов и пользовательских данных с помощью Яндекс.Метрика, в соответствии с нашей Политикой конфиденциальности.