Производство деталей из порошковых материалов
В начальном периоде развития методом порошковой металлургии изготовлялись такие материалы и детали из них, для получения которых этот метод был монопольным: твёрдые сплавы, пористые и тугоплавкие материалы, медно-графитовые и др. По мере развития порошковой металлургии её методы стали конкурировать с традиционными в получении деталей из чёрных и цветных металлов.
Порошковая металлургия позволяет наладить массовое производство деталей с жёсткими ограничениями по размерам. При этом они не будут требовать существенной дополнительной механической обработки. Или даже позволит отказаться от неё. Что приводит к резкому снижению трудоёмкости производственного процесса и металлоёмкости получаемых изделий.
Материалы для изготовления порошковых конструкционных деталей можно подразделить на две группы; материалы, заменяющие обычные углеродистые и легированные стали, чугуны и цветные металлы, то есть машиностроительные и приборостроительные общего назначения, и материалы со специальными свойствами: Высокой износостойкостью, твёрдостью, жаропрочностью, коррозионной стойкостью, со специальными магнитными и электрическими характеристиками, с большим удельным весом и т. п.
Основной особенностью порошковых конструкционных деталей является их высокая плотность и прочность, приближающаяся к плотности и прочности деталей из проката или литья.
Для возможности изготовления конкретной детали из порошка она должна соответствовать требованиям к прочности спеченного порошкового материала, целесообразность такого шага определяется серийностью.
Прочность спеченных материалов во многом зависит от их пористости. Обычное холодное прессование может обеспечить максимальную плотность 84-85 % и прочность после спекания около 50 % от прочности кованого материала того же сплава. Высокоскоростное холодное прессование (6-20 м/с) позволяет достичь относительной плотности 94-95 % и относительной прочности порядка 75 %. Достигнуть прочности близкой к 100 % удаётся только при высокотемпературном прессовании или импульсных методах уплотнения. В этих случаях прочность порошкового материала сравнивается с прочностью литого или кованого соответствующего состава и структуры.
При подборе необходимой степени уплотнения для изготовления деталей необходимо иметь в виду, что присутствие определённого процента пор может быть полезным. Так, пропитка пор маслом позволяет уменьшить трение и износ детали, улучшить прирабатываемость и уменьшить шум во время работы. Спеченную деталь практически всегда можно сделать более износостойкой при трении металла по металлу, чем деталь из проката. Кроме того, равномерно распределённая мелкая пористость резко уменьшает чувствительность материала к концентрации напряжений. Поэтому, несмотря на обычно пониженные по сравнению с металлопрокатом пластичность и ударную вязкость, материалы, выполненные по технологии спекания, активно используют для производства большого количества высоконагруженных деталей.
Эффективным способом получения высокопрочных порошковых деталей является пропитка пористых прессовок из железа, железографита или железомарганца жидкой медью или латунью. Прочность таких деталей достигает 100 кг/мм2. Особенность технологии состоит в том, что применяются взаимно насыщенные порошки. Заготовка из железного порошка содержит до 5 % меди. Пропитка производится медно-железным сплавом, содержащим до 8 % железа. Это даёт возможность избежать разъедания поверхности изделия в местах его контакта с пропитывающим брикетом. Преимуществом данной технологии является также то, что формование производится при сравнительно низких давлениях, а пропитка — при низкой усадке. Это дает возможность увеличить стойкость пресс-форм и получать детали точных размеров. Метод пропитки позволяет соединить отдельные детали простой конфигурации в деталь сложной формы.
В настоящее время экономически выгоднее производить спеченные детали с остаточной пористостью 5-20 %, а не совершенно плотные, хотя прочность пористых деталей ниже. Достигаемый при этом уровень прочностных характеристик достаточен для мало- и средненагруженных изделий. Высоконагруженные пористые детали приходится дополнительно уплотнять — либо повторным прессованием и спеканием, либо горячей штамповкой. Чаще практикуют штамповку за один переход в закрытых штампах.
Экономическая эффективность изготовления деталей из порошков тем больше, чем больше серийность, так как стоимость пресс-форм и оборудования (прессов, печей) достаточно велика. Поэтому основным потребителем спеченных конструкционных деталей является автомобилестроение, где производство массовое.
Типовыми порошковыми деталями общего назначения являются кулачки, храповики, шаровые вставки, корпуса подшипников, ролики, звёздочки распределительных валов, детали вычислительных машин, офисной, бытовой техники и многое другое. Обычно такие детали являются слабонагруженными, которые целесообразно изготавливать из железного порошка и графита однократным прессованием и спеканием. Средненагруженные детали могут быть изготовлены либо двукратным прессованием — спеканием, либо пропиткой пористой спеченной детали медью или латунью.
Для производства подобных деталей, вместе со смесями железографит, используются и смеси железо-медь-графит или железо-чугун, а также железо-графит-легирующие элементы. При получении изделий из порошковой углеродистой стали введением графита в железный порошок науглероживание железа проходит во время спекания. Диффузия углерода не успевает пройти достаточно полно и углерод в полученных изделиях распределяется неравномерно, что может привести к аномальности структуры. Применение смесей, содержащих порошок чугуна, а не графит, снижает прессуемость смеси, но обеспечивает более стабильные свойства.
Марки и характеристики прочности ряда спеченных материалов на основе железного порошка приведены в таблице. Маркировка расшифровывается следующим образом: цифры после буквы Ж — содержание углерода в сотых долях процента, далее указаны легирующие элементы и их количество, как в марках стали, и после дефиса — умноженная на десять плотность изделия в г/см3. Например, марка Ж20Д5Н3Х-60 означает: материал на основе железа с 0,20 % углерода, 5 % меди, 3 % никеля, ориентировочно 1 % хрома при плотности 6,0 г/см3. Малонагруженные детали изготавливают из материалов с временным сопротивлением до 250 МПа, средненагруженные — 300-500 МПа, сильно нагруженные — 500-800 МПа и более.
Особое место в числе деталей, изготавливаемых из порошков, занимают поршневые кольца и шестерни. В зависимости от условий работы шестерни производятся из железографита или из железографита с включением меди и легирующих элементов. При применении технологии производства шестерён с помощью спекания порошка, вместо нарезки зубьев из цельнометаллической заготовки, можно добиться экономии денежных затрат на 30-80%, а трудозатрат на 50 %. Чтобы добиться большей точности, изделия после спекания подвергают калиброванию и доводке.
После спекания можно прибегнуть к пропитке пор в заготовке маслом, что обеспечивает самосмазываемость шестерни в процессе работы, а также уменьшает износ и снижает шум.
При применении же порошковой технологии при производстве поршневых колец снижается расход материала, что снижает денежные затраты на производство на 30-40%. Кроме этого, поршневые кольца, произведённые методом порошкового спекания, примерно в 1,5-2 раза прочнее обычных чугунных, более износостойкие (в 1,5-3 раза), более упругие.
Методом спекания поршневые кольца производятся из смеси железного порошка с 1,1 % графита, 2 % меди и до 4 % сульфида цинка (применяется для уменьшения трения, так называемая, твёрдая смазка). Чтобы повысить износостойкость колец их делают двухслойными: во внешний слой вводят 6 % хрома и увеличивают содержание графита до 3,5 %.
Применение таких поршневых колец уменьшает износ двигателя и расход масла почти в 1,5 раза, что неминуемо продлевает его срок службы.
- На главную
-
Категории
-
Пластины твердосплавные
-
Пластины токарные
-
Пластины для внутреннего и наружного точения
-
Пластины резьбовые
-
Пластины резьбовые ISO
-
Пластины резьбовые трапецеидального профиля, угол 30 град.
-
Пластины резьбовые неполного профиля, угол 55 или 60 град.
-
Пластины резьбовые для нарезания трубной резьбы Whitworth, правые
-
Пластины резьбовые NPT (дюймовая коническая резьба c углом профиля 60 град. и конус 1:16)
-
Пластины резьбовые BSPT (Британский стандарт) полного профиля, угол 55 град.
-
Пластины резьбовые треугольного закругленного профиля
-
Пластины резьбовые UN (Американский стандарт) полного профиля, угол 60 град.
- Пластины резьбовые UN (Американский стандарт) полного профиля, угол 60 град.
- Панцирная трубная резьба Pg 80 град.
- Пластины резьбовые трапецеидального профиля, угол 30 град.
- Пластины резьбовые BSPT (Британский стандарт) полного профиля, угол 55 град.
- Пластины резьбовые NPT (дюймовая коническая резьба c углом профиля 60 град. и конус 1:16)
- Пластины резьбовые неполного профиля, угол 55 или 60 град.
- Упорная резьба SAGE 30 град.
-
-
Пластины отрезные и канавочные
-
TGF32
-
SP
-
MRMN
-
MG...N
- GER-C
- SP для стали
- SP для нержавеющей стали
-
QCMB
-
QPMB
- MGMN для стали
- MGMN для нержавеющей стали
- QPMB для стали
- QPMB для нержавеющей стали
- MRMN для стали
- ZP_S для нержавеющей стали
-
ZP_S
- QCMB для нержавеющей стали
- ZT_D для нержавеющей стали
-
ZT_D
- ZT_D для стали
- QCMB для стали
- TDC для нержавеющей стали
-
TDC
- QC_ для нержавеющей стали
-
QC
- QC_
- ZP_D для нержавеющей стали
-
ZP_D
- ZR_D для нержавеющей стали
-
ZR_D
- ZT_S для нержавеющей стали
-
ZT_S
- ZQMX для стали
-
ZQMX
- CTPA для нержавеющей стали
-
CTPA
- MGMN для чугуна
- MRMN для нержавеющей стали
- MRMN для чугуна
-
GEL-A/B
- GEL-A
-
GEL-A/B-R
-
GEL-C/D/E
- GEL-C
-
GEL-C/D/E-R
-
GER-A/B
- GER-A
-
GER-A/B-R
-
GER-C/D/E
-
GER-C/D/E-R
- MGMN
- MGGN
- MB
- ZTKS
- JRMN
- GK-R
- ZRFD
- KTMD
- KGT
- JSMN
- SPDR
-
-
-
Пластины фрезерные
-
Пластины для сверл
-
Лезвия для резьбофрез
-
Пластины со вставками PCBN
- Пластины для червячного зуба 40°
-
-
Фрезы
-
Метчики
-
Сверла
-
Ленточные пилы
-
Новое поступление (NEW!)
-
Державки токарные
-
Державки расточные
-
S...-SVJCR/S...-SVJCL
-
S...-DCLNR/S...-DCLNL
-
S...-DDUNR/S...-DDUNL
-
S...-DWLNR/S...-DWLNL
-
S...-MCKNR/S...-MCKNL
-
S...-MCLNR/S...-MCLNL
-
S...-MDQNR/S...-MDQNL
-
S...-MDUNR/S...-MDUNL
-
S...-MSKNR/S-...MSKNL
-
S...-MTJNR/S...-MTJNL
-
S...-MTQNR/S...-MTQNL
-
S...-MTUNR/S...-MTUNL
-
S...-MTFNR/S...-MTFNL
-
S...-MTWNR/S...-MTWNL
-
S...-MVQNR/S-...MVQNL
-
S...-MVUNR/S-...MVUNL
-
S...-MVWNR/S...-MVWNL
-
S...-MVXNR/S...-MVXNL
-
S...-MWLNR/S...-MWLNL
-
S...-PCLNR/S...-PCLNL
-
S...-PDSNR/S...-PDSNL
-
S...-PDUNR/S...-PDUNL
-
S...-PSKNR/S...-PSKNL
-
S...-PWLNR/S...-PWLNL
-
S...-PTFNR/S...-PTFNL
-
S...-SCKCR/S...-SCKCL
-
S...-SCLCR/S...-SCLCL
-
S...-SCLPR/S...-SCLPL
-
S...-SDQCR/S...-SDQCL
-
S...-SDUCR/S...-SDUCL
-
S...-SDZCR/S...-SDZCL
-
S...-SSSCR/S...-SSSCL
-
S...-SSKCR/S...-SSKCL
-
S...-STFCR/S-...STFCL
-
S...-STUCR/S-...STUCL
-
S...-SVUCR/S-...SVUCL
-
S...-SVUBR/S...-SVUBL
-
-
Державки проходные
-
CCLNR/CCLNL
-
CRDNN
-
CSDNN
-
CSKNR/CSKNL
-
CTJNR/CTJNL
-
DCBNR/DCBNL
-
DCKNR/DCKNL
-
DCLNR/DCLNL
-
DCMNN
-
DDJNR/DDJNL
-
DDPNN
-
DSSNR/DSSNL
-
DDQNR/DDQNL
-
DSBNR/DSBNL
-
DSDNN
-
DSKNR/DSKNL
-
DTFNR/DTFNL
-
DTGNR/DTGNL
-
DVJNR/DVJNL
-
DVVNN
-
DWLNR/DWLNL
-
ECLNR/ECLNL
-
EDJNR/EDJNL
-
EVJNR/EVJNL
-
EWLNR/EWLNL
-
MCBNR/MCBNL
-
MCKNR/MCKNL
-
MCLNR/MCLNL
-
MCMNN
-
MDJNR/MDJNL
-
MDPNN
-
MDQNR/MDQNL
-
MRDNN
-
MRGNR/MRGNL
-
MSBNR/MSBNL
-
MSDNN
-
MSKNR/MSKNL
-
MSSNR/MSSNL
-
MTENN
-
MTFNR/MTFNL
-
MTGNR/MTGNL
-
MTJNR/MTJNL
-
MTQNR/MTQNL
-
MVJNR/MVJNL
-
MVQNR/MVQNL
-
MVUNR/MVUNL
-
MVVNN
-
MWLNR/MWLNL
-
PWLNR/PWLNL
-
PCLNR/PCLNL
-
PDJNR/PDJNL
-
PRACR/PRACL
-
PRDCN
-
PCBNR/PCBNL
-
PRGCR/PRGCL
-
PSBNR/PSBNL
-
PSDNN
-
PSSNR/PSSNL
-
PTGNR/PTGNL
-
PTTNR/PTTNL
-
SCLCR/SCLCL
-
SDJCR/SDJCL
-
SDNCN
-
SRACR/SRACL
-
SRDCN
-
SSDCN
-
SSSCR/SSSCL
-
STFCR/STFCL
-
SVACR/SVACL
-
SVJBR/SVJBL
-
SVJCR/SVJCL
-
SVVBN
-
SVVCN
-
WTENN
-
WTJNR/WTJNL
-
WWLNR/WWLNL
-
PDNNR/PDNNL
-
SVHBR/SVHBL
-
PDNNN
-
PTFNR/PTFNL
-
SCACR/SCACL
-
SDACR/SDACL
-
SSBCR/SSBCL
-
SRGCR/SRGCL
-
SSKCR/SSKCL
-
STGCR/STGCL
-
SVABR/SVABL
-
SVQCR/SVQCL
-
SWACR/SWACL
-
WTQNR/WTQNL
-
-
Державки резьбовые
-
Державки отрезные, канавочные
-
Держатели отрезного лезвия
-
Лезвия отрезные
-
Мини-резцы твердосплавные
-
-
Оснастка для фрезерных станков
-
Фрезерные патроны
-
BT
-
BT-ER (для цанг ER)
-
BT-FMB (для насадных фрез)
-
BT-SCA (для дисковых фрез)
-
BT-D (тестовые оправки)
-
BT-SLN Weldon
-
BT-MTA (конус Морзе с лапкой)
-
BT-MTB (конус Морзе с резьбовым отверстием)
-
BT-DC (высокоскоростные патроны для цанг DC)
-
BT-APU
-
BT-SC (для цилиндрических цанг SC)
-
BT-GT (для резьбовых цанг GT12/24/42)
-
BT-TER (патроны с осевой компенсацией по длине для цанг ER)
-
BT-OZ(EOC) (для силовых цанг OZ)
-
BT-PHC (гидропластовые патроны)
-
-
Конус Морзе MTA/MTB
-
HSK
-
Цилиндрический хвостовик
-
NT
-
SK
-
SK-FMB (для насадных фрез)
-
SK-SLN (Weldon)
-
SK-TER (патроны с осевой компенсацией по длине для цанг ER)
-
SK-SC (для цилиндрических цанг SC)
-
SK-MTB (конус Морзе с резьбовым отверстием)
-
SK-MTA (конус Морзе с лапкой)
-
SK-ER (для цанг ER)
-
SK-GT (для резьбовых цанг GT12/24/42)
-
SK-OZ(EOC) (для силовых цанг OZ)
-
SK-APU (сверлильные быстрозажимные патроны)
-
SK-PHC (гидропластовые патроны)
-
-
-
Прихваты, прижимы, упоры
-
Цанги
-
Штревели
-
3D тестеры
-
Тиски станочные
-
Аксессуары и запчасти
- Силовые высокоточные VQC
-
640 Multitasking
-
Трехкулачковые NBK
-
Гидравлические DCV
-
Модульные двойные ZQ83
-
С регулируемым усилием зажима HPAC
-
Самоцентрирующиеся SC-I
-
Модульные GT
-
Глобусные HHY
-
Лекальные QGG
-
Лекальные QKG
-
Модульные составные ZQ84
-
Гидравлические CHV
-
Самоцентрирующиеся двойные SMC
-
-
Кромкоискатели
-
Магнитные плиты
-
Центроискатели
-
Гайки для цанг
-
Ключи гаечные
-
Приспособления для оправок
-
Наборы прижимов
-
Расточные системы
-
Система нулевого базирования
-
Магнитные захваты
-
Поворотные столы
-
Аксессуары для станочной оснастки
-
Привязка по оси Z
-
Защитные вставки
-
-
Оснастка для токарных станков
-
Кулачки токарные
- Инструментальные блоки BOT
-
Токарные патроны
-
Центры токарные вращающиеся
- Центры вращающиеся
- Центры вращающиеся усиленные M11
- Центры вращающиеся облегченные
- Центры вращающиеся со сменными вставками
- Центры вращающиеся высокоскоростные
- Центры вращающиеся с твердосплавной вставкой
- Центры вращающиеся с удлиненной вершиной
- Центры вращающиеся усиленные
- Центры вращающиеся высокоточные
- Центры вращающиеся грибковые
-
Держатели осевого инструмента
-
Переходные втулки
-
Приспособления для расточки кулачков
-
Инструментальные блоки BMT
-
Центры токарные упорные
-
Сухари для токарных патронов
-
Инструментальные блоки VDI
-
Патроны цанговые
-
Цанги токарные
-
-
Измерительный инструмент
-
Станки
-
Станки ленточные по металлу
-
Лазерные граверы (маркировщики) по металлу
-
Токарные станки
-
Фрезерные станки
-
Заточные станки
-
Резьбонарезные манипуляторы
-
Электроэрозионные станки
-
Промышленные роботы
-
-
Мерч CNC66
-
Проволока, СОЖ, запчасти для электроэрозионных станков
-
Промышленная мебель
-
Запасные части для державок, резцов и фрез
-
Развертки
-
Упаковка
-
Зенковки
-
Плашки
-
Инструмент для снятия заусенцев
-
Корзина пуста
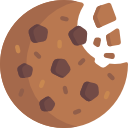
Мы используем файлы cookie для улучшения работы сайта и персонализации. Продолжая использовать сайт, вы соглашаетесь на сбор, обработку cookie-файлов и пользовательских данных с помощью Яндекс.Метрика, в соответствии с нашей Политикой конфиденциальности.