Послепечное рафинирование стали
Сталь, произведенная на обычных сталеплавильных агрегатах, не всегда обладает требуемыми свойствами. Она может иметь неоднородный химический состав, содержать газы и неметаллические включения.
Чтобы улучшить качество стали, ее необходимо рафинировать. Чаще всего применяют три метода рафинирования стали: вакуумную дегазацию, рафинирование инертными газами и рафинирование синтетическим шлаком.
В производственной практике возможно использование всех вышеперечисленных методов одновременно.
Ковшевое шлакование
Очень важную роль играют ковшовые шлаки, используемые в послепечной металлургии. Их задача:
- десульфурация стали;
- раскисление стали;
- очистка от оксидных неметаллических включений;
- обеспечение соответствующего состава оксидных включений в готовой стали;
- защита от атмосферных воздействий;
- тепловая изоляция.
Масса шлака при послепечном рафинировании составляет примерно 1/4 массы жидкого металла.
Рафинирование аргоном
Рафинирование стали в ковше со шлаком с использованием обработки аргоном – один из самых простых способов получения материала желаемого качества. Этот метод требует использования шлака хорошего качества, который ассимилирует нежелательные компоненты, и соответствующих параметров впрыскиваемого инертного газа.
Шлак должен иметь соответствующую щелочность, плотность, вязкость и свойства поверхности. Эти параметры определяются химическим составом шлака.
В свою очередь, продувку аргона следует вводить с такой интенсивностью, которая обеспечит перемешивание жидкой стали во всем объеме металлической ванны. Однако при этом важно, чтобы газовый поток не разрушал слой шлака.
Аргон — инертный газ, то есть он не вступает в химическую реакцию с другими элементами. Поэтому его широко используют в металлургических процессах, главным образом для перемешивания ванны металла.
Смешивая жидкую сталь в процессе аргонизирования, она гомогенизируется по химическому составу и температуре.
Продувка стали аргоном через штуцер, расположенный на дне ковша – самый часто используемый процесс рафинирования стали аргоном. Это подтверждается невысокой стоимостью монтажа и высоким качеством получаемой продукции.
Этот метод чаще всего используется одновременно с другими методами рафинирования, например рафинированием стали синтетическим шлаком или применением вакуума.
Аргон подается к жидкому металлу в ковше под давлением, чаще всего через огнеупорную пористую газопроницаемую форму, расположенную на дне чана. Газ к арматуре подается по трубам, содержащим регулирующие устройства.
Другой способ ввести аргон в ванну — использовать погружную трубку. Рафинирование стали с использованием погружной фурмы применяется редко из-за ее меньшей эффективности.
Пузырьки аргона обтекают фурму, а поток выходящего газа имеет меньший радиус действия в объеме металла, что приводит к ухудшению перемешивания по сравнению с использованием газопроницаемого штуцера на дне ковша.
Ковшовую обработку с нагревом стали чаще всего проводят в устройстве, называемом печью-ковшом. Она состоит из ковша, помещенного на специальную тележку, крышки с электродами, автоматической системы дозирования легирующих добавок и машины для ввода стержней.
Еще одним важным нюансом при рафинировании является то, что для нагрева жидкой стали используется электрическая дуга, поэтому ток не такой высокий, как в дуговых печах.
После выпуска стали из дуговой печи в ковш ее транспортируют мостовым краном или тележкой на станцию ковшовой печи. После помещения его под крышку к газопроницаемому штуцеру, расположенному на дне ковша, подключают аргон, а затем включают ток, нагревающий жидкую сталь дугой.
Поскольку жидкая сталь нагревается, ее постоянно продувают аргоном. Рафинировочный шлак в ковше образуется из извести, доломитовой извести, боксита, а также из оксидов металлов, находящихся в стали, например при окислении алюминия.
Образующийся шлак защищает щелочную природу огнеупорной футеровки ковша от излучения электрической дуги и необходим для процесса обессеривания стали и усвоения в ней неметаллических включений. Целью является получение высокой основности шлака, высокой текучести и хорошего усвоения серы и оксидных неметаллических включений.
После достижения необходимой температуры стали в печи-ковше и сигнализации момента передачи стали в устройство КОС проводится последний этап рафинирования стали, заключающийся в анализе химического состава металла и на основании этого, за счет системы введения добавок сплава дополняется его конечный химический состав.
После окончательного анализа химического состава и измерения контрольной температуры ковш с металлом передается на разливочный участок.
Дегазация стали
Газы в стали вызывают ее хрупкость, образование пустот и неметаллических включений. В жидкой стали газы поступают из шихты и поглощаются из атмосферы печи.
Газы, которые необходимо удалить из стали, — это водород, кислород и азот. Существует три типа устройств вакуумной дегазации: струйные, вакуумные в ванне и циркуляционные.
Струйную дегазацию производят при заливке жидкой стали в ковш под вакуумом. В этом методе стальная струя физически разбивается, что эффективно увеличивает площадь поверхности жидкости и, таким образом, обеспечивает эффективную дегазацию.
Дегазация стали в вакуумной камере является наиболее простым, но и наименее эффективным методом. Выделение газов начинается, когда чан помещают в камеру и создают вакуум.
Процесс ВД (вакуумной дегазации) — стационарный процесс, заключающийся в дегазации металла в ковше с использованием смешивания инертных газов. Целью использования вакуумного процесса является раскисление и глубокое обезуглероживание металла.
Его возникновение возможно из-за зависимости реакции обезуглероживания от давления, создаваемого окисью углерода. В процессе ВД дегазация происходит в разливочном ковше путем помещения его в отдельную камеру. Для интенсификации реакции необходима интенсивная продувка аргоном.
Метод циркулярной дегазации предполагает помещение небольших порций жидкого металла в вакуум.
Одним из таких типов методов является метод RH (Ruhrstahl Heraus).
Это непрерывный циркуляционный метод дегазации, отличающийся возможностью получения необходимого химического состава стали.
Дегазация стали в устройстве RH осуществляется следующим образом: после установки ковша со сталью на подъемное устройство его поднимают вверх до погружения заглушек в сталь на соответствующую глубину. Затем через сопло подается аргон под давлением, который нагнетает находящуюся в патрубке сталь в камеру и одновременно путем впрыска засасывает сталь из ковша в патрубок.
Подбирая давление аргона и скорость его подачи, можно регулировать скорость течения стали через вакуумную камеру. После поступления в камеру сталь подвергается интенсивной дегазации в результате диффузии газов в объем камеры и протекания через нее пузырьков аргона.
На поверхности этих пузырьков также возможна реакция раскисления стали углеродом. По окончании дегазации в вакуумную камеру вносят легирующие добавки и раскислители. После добавления этих материалов принудительная циркуляция должна поддерживаться в течение дополнительного периода.
Для гомогенизации состава стали, ковш опускается вниз, остатки стали перетекают из камеры в ковш, который затем транспортируется к месту разливки.
В процессе циркуляционной дегазации происходит интенсивное выделение газовых пузырьков, поскольку инертный газ способствует быстрому зарождению пузырьков других газов, например угарного газа, водорода или азота.
Количество транспортируемого газа и высота, на которой он вводится во всасывающее отверстие, также оказывают существенное влияние на степень дегидрирования. Чем ниже расположен вход инертного газа, тем большей степени дегазации можно достичь.
Добавление материалов
Для дополнения химического состава или внесении раскисляющих и шлакообразующих веществ применяют различные способы дозирования. Это можно сделать, добавляя материалы порциями, продувая погружным патрубком или вводя материалы в виде проволоки.
Весьма эффективным методом дополнения химического состава стали является введение легирующих добавок в виде проволоки. Такая проволока может содержать порошкообразные добавки в сердечнике, завернутом в тонкий стальной лист. Алюминиевую проволоку также можно подавать этим методом.
Этот метод является весьма эффективным способом пополнения химического состава стали, так как обеспечивает получение запланированного содержания компонентов сплава с высокой точностью, а сама машина позволяет автоматизировать процесс контроля и учета количества вносимых компонентов.
- На главную
-
Категории
-
Пластины твердосплавные
-
Пластины токарные
-
Пластины для внутреннего и наружного точения
-
Пластины резьбовые
-
Пластины резьбовые ISO
-
Пластины резьбовые трапецеидального профиля, угол 30 град.
-
Пластины резьбовые неполного профиля, угол 55 или 60 град.
-
Пластины резьбовые для нарезания трубной резьбы Whitworth, правые
-
Пластины резьбовые NPT (дюймовая коническая резьба c углом профиля 60 град. и конус 1:16)
-
Пластины резьбовые BSPT (Британский стандарт) полного профиля, угол 55 град.
-
Пластины резьбовые треугольного закругленного профиля
-
Пластины резьбовые UN (Американский стандарт) полного профиля, угол 60 град.
- Пластины резьбовые UN (Американский стандарт) полного профиля, угол 60 град.
- Панцирная трубная резьба Pg 80 град.
- Пластины резьбовые трапецеидального профиля, угол 30 град.
- Пластины резьбовые BSPT (Британский стандарт) полного профиля, угол 55 град.
- Пластины резьбовые NPT (дюймовая коническая резьба c углом профиля 60 град. и конус 1:16)
- Пластины резьбовые неполного профиля, угол 55 или 60 град.
- Упорная резьба SAGE 30 град.
-
-
Пластины отрезные и канавочные
-
TGF32
-
SP
-
MRMN
-
MG...N
- GER-C
- SP для стали
- SP для нержавеющей стали
-
QCMB
-
QPMB
- MGMN для стали
- MGMN для нержавеющей стали
- QPMB для стали
- QPMB для нержавеющей стали
- MRMN для стали
- ZP_S для нержавеющей стали
-
ZP_S
- QCMB для нержавеющей стали
- ZT_D для нержавеющей стали
-
ZT_D
- ZT_D для стали
- QCMB для стали
- TDC для нержавеющей стали
-
TDC
- QC_ для нержавеющей стали
-
QC
- QC_
- ZP_D для нержавеющей стали
-
ZP_D
- ZR_D для нержавеющей стали
-
ZR_D
- ZT_S для нержавеющей стали
-
ZT_S
- ZQMX для стали
-
ZQMX
- CTPA для нержавеющей стали
-
CTPA
- MGMN для чугуна
- MRMN для нержавеющей стали
- MRMN для чугуна
-
GEL-A/B
- GEL-A
-
GEL-A/B-R
-
GEL-C/D/E
- GEL-C
-
GEL-C/D/E-R
-
GER-A/B
- GER-A
-
GER-A/B-R
-
GER-C/D/E
-
GER-C/D/E-R
- MGMN
- MGGN
- MB
- ZTKS
- JRMN
- GK-R
- ZRFD
- KTMD
- KGT
- JSMN
- SPDR
-
-
-
Пластины фрезерные
-
Пластины для сверл
-
Лезвия для резьбофрез
-
Пластины со вставками PCBN
- Пластины для червячного зуба 40°
-
-
Фрезы
-
Фрезы монолитные
-
Фрезы со сменными пластинами
-
Фрезы дисковые
-
Фрезы концевые
-
ASM
-
BAP
- BMR
-
EMR
-
PE03
-
RB02
-
RB03
-
TEBL
-
ХК01
- ХК02
- SSM390
- EMP01
- AF06
- BAP
- EMR
- EMRW
- EXN03
- PE01
- PE02
- PE05
- R217.96
- RF01
- AF06
- BAP
- EMR
- EMRW
- EXN03
- PE01
- PE02
- PE05
- R217.96
- RF01
- AF06
- BAP
- EMR
- EMRW
- EXN03
- PE01
- PE02
- PE05
- R217.96
- RF01
- AF06
- BAP
- EMR
- EMRW
- EXN03
- PE01
- PE02
- PE05
- R217.96
- RF01
- AF06
- BAP
- EMR
- EMRW
- EXN03
- PE01
- PE02
- PE05
- R217.96
- RF01
- AF06
- BAP
- EMR
- EMRW
- EXN03
- PE01
- PE02
- PE05
- R217.96
- RF01
- AF06
- BAP
- EMR
- EMRW
- EXN03
- PE01
- PE02
- PE05
- R217.96
- RF01
- RF01
- EXN03
- PE02
- AF06
- R217.96
- EMRW
- EMR
- BAP
- PE01
- PE05
- AF06
- BAP
- EMR
- EMRW
- EXN03
- PE01
- PE02
- PE05
- R217.96
- RF01
- AF06
- BAP
- EMR
- EMRW
- EXN03
- PE01
- PE02
- PE05
- R217.96
- RF01
- AF06
- BAP
- EMR
- EMRW
- EXN03
- PE01
- PE02
- PE05
- R217.96
- RF01
- AF06
- BAP
- EMR
- EMRW
- EXN03
- PE01
- PE02
- PE05
- R217.96
- RF01
- AF06
- BAP
- EMR
- EMRW
- EXN03
- PE01
- PE02
- PE05
- R217.96
- RF01
- AF06
- BAP
- EMR
- EMRW
- EXN03
- PE01
- PE02
- PE05
- R217.96
- RF01
- AF06
- BAP
- EMR
- EMRW
- EXN03
- PE01
- PE02
- PE05
- R217.96
- RF01
- AF06
- BAP
- EMR
- EMRW
- EXN03
- PE01
- PE02
- PE05
- R217.96
- RF01
- AF06
- BAP
- EMR
- EMRW
- EXN03
- PE01
- PE02
- PE05
- R217.96
- RF01
- AF06
- BAP
- EMR
- EMRW
- EXN03
- PE01
- PE02
- PE05
- R217.96
- RF01
- AF06
- BAP
- EMR
- EMRW
- EXN03
- PE01
- PE02
- PE05
- R217.96
- RF01
- AF06
- BAP
- EMR
- EMRW
- EXN03
- PE01
- PE02
- PE05
- R217.96
- RF01
- AF06
- BAP
- EMR
- EMRW
- EXN03
- PE01
- PE02
- PE05
- R217.96
- RF01
- AF06
- BAP
- EMR
- EMRW
- EXN03
- PE01
- PE02
- PE05
- R217.96
- RF01
- AF06
- BAP
- EMR
- EMRW
- EXN03
- PE01
- PE02
- PE05
- R217.96
- RF01
- AF06
- BAP
- EMR
- EMRW
- EXN03
- PE01
- PE02
- PE05
- R217.96
- RF01
- AF06
- BAP
- EMR
- EMRW
- EXN03
- PE01
- PE02
- PE05
- R217.96
- RF01
- AF06
- BAP
- EMR
- EMRW
- EXN03
- PE01
- PE02
- PE05
- R217.96
- RF01
- AF06
- BAP
- EMR
- EMRW
- EXN03
- PE01
- PE02
- PE05
- R217.96
- RF01
- AF06
- BAP
- EMR
- EMRW
- EXN03
- PE01
- PE02
- PE05
- R217.96
- RF01
- AF06
- BAP
- EMR
- EMRW
- EXN03
- PE01
- PE02
- PE05
- R217.96
- RF01
- AF06
- BAP
- EMR
- EMRW
- EXN03
- PE01
- PE02
- PE05
- R217.96
- RF01
- AF06
- BAP
- EMR
- EMRW
- EXN03
- PE01
- PE02
- PE05
- R217.96
- RF01
- AF06
- BAP
- EMR
- EMRW
- EXN03
- PE01
- PE02
- PE05
- R217.96
- RF01
- AF06
- BAP
- EMR
- EMRW
- EXN03
- PE01
- PE02
- PE05
- R217.96
- RF01
- AF06
- BAP
- EMR
- EMRW
- EXN03
- PE01
- PE02
- PE05
- R217.96
- RF01
- AF06
- BAP
- EMR
- EMRW
- EXN03
- PE01
- PE02
- PE05
- R217.96
- RF01
- AF06
- BAP
- EMR
- EMRW
- EXN03
- PE01
- PE02
- PE05
- R217.96
- RF01
- AF06
- BAP
- EMR
- EMRW
- EXN03
- PE01
- PE02
- PE05
- R217.96
- RF01
- AF06
- BAP
- EMR
- EMRW
- EXN03
- PE01
- PE02
- PE05
- R217.96
- RF01
- AF06
- BAP
- EMR
- EMRW
- EXN03
- PE01
- PE02
- PE05
- R217.96
- RF01
- AF06
- BAP
- EMR
- EMRW
- EXN03
- PE01
- PE02
- PE05
- R217.96
- RF01
- AF06
- BAP
- EMR
- EMRW
- EXN03
- PE01
- PE02
- PE05
- R217.96
- RF01
- RF01
- EXN03
- PE02
- AF06
- R217.96
- EMRW
- EMR
- BAP
- PE01
- PE05
- RF01
- EXN03
- PE02
- AF06
- R217.96
- EMRW
- EMR
- BAP
- PE01
- PE05
-
-
Фрезы резьбонарезные
-
Фрезы торцевые насадные
-
Фрезы фасочные
-
-
Фрезы со сменными головками
-
-
Метчики
-
Сверла
-
Ленточные пилы
-
Новое поступление (NEW!)
-
Державки токарные
-
Державки расточные
-
S...-SVJCR/S...-SVJCL
-
S...-DCLNR/S...-DCLNL
-
S...-DDUNR/S...-DDUNL
-
S...-DWLNR/S...-DWLNL
-
S...-MCKNR/S...-MCKNL
-
S...-MCLNR/S...-MCLNL
-
S...-MDQNR/S...-MDQNL
-
S...-MDUNR/S...-MDUNL
-
S...-MSKNR/S-...MSKNL
-
S...-MTJNR/S...-MTJNL
-
S...-MTQNR/S...-MTQNL
-
S...-MTUNR/S...-MTUNL
-
S...-MTFNR/S...-MTFNL
-
S...-MTWNR/S...-MTWNL
-
S...-MVQNR/S-...MVQNL
-
S...-MVUNR/S-...MVUNL
-
S...-MVWNR/S...-MVWNL
-
S...-MVXNR/S...-MVXNL
-
S...-MWLNR/S...-MWLNL
-
S...-PCLNR/S...-PCLNL
-
S...-PDSNR/S...-PDSNL
-
S...-PDUNR/S...-PDUNL
-
S...-PSKNR/S...-PSKNL
-
S...-PWLNR/S...-PWLNL
-
S...-PTFNR/S...-PTFNL
-
S...-SCKCR/S...-SCKCL
-
S...-SCLCR/S...-SCLCL
-
S...-SCLPR/S...-SCLPL
-
S...-SDQCR/S...-SDQCL
-
S...-SDUCR/S...-SDUCL
-
S...-SDZCR/S...-SDZCL
-
S...-SSSCR/S...-SSSCL
-
S...-SSKCR/S...-SSKCL
-
S...-STFCR/S-...STFCL
-
S...-STUCR/S-...STUCL
-
S...-SVUCR/S-...SVUCL
-
S...-SVUBR/S...-SVUBL
-
-
Державки проходные
-
CCLNR/CCLNL
-
CRDNN
-
CSDNN
-
CSKNR/CSKNL
-
CTJNR/CTJNL
-
DCBNR/DCBNL
-
DCKNR/DCKNL
-
DCLNR/DCLNL
-
DCMNN
-
DDJNR/DDJNL
-
DDPNN
-
DSSNR/DSSNL
-
DDQNR/DDQNL
-
DSBNR/DSBNL
-
DSDNN
-
DSKNR/DSKNL
-
DTFNR/DTFNL
-
DTGNR/DTGNL
-
DVJNR/DVJNL
-
DVVNN
-
DWLNR/DWLNL
-
ECLNR/ECLNL
-
EDJNR/EDJNL
-
EVJNR/EVJNL
-
EWLNR/EWLNL
-
MCBNR/MCBNL
-
MCKNR/MCKNL
-
MCLNR/MCLNL
-
MCMNN
-
MDJNR/MDJNL
-
MDPNN
-
MDQNR/MDQNL
-
MRDNN
-
MRGNR/MRGNL
-
MSBNR/MSBNL
-
MSDNN
-
MSKNR/MSKNL
-
MSSNR/MSSNL
-
MTENN
-
MTFNR/MTFNL
-
MTGNR/MTGNL
-
MTJNR/MTJNL
-
MTQNR/MTQNL
-
MVJNR/MVJNL
-
MVQNR/MVQNL
-
MVUNR/MVUNL
-
MVVNN
-
MWLNR/MWLNL
-
PWLNR/PWLNL
-
PCLNR/PCLNL
-
PDJNR/PDJNL
-
PRACR/PRACL
-
PRDCN
-
PCBNR/PCBNL
-
PRGCR/PRGCL
-
PSBNR/PSBNL
-
PSDNN
-
PSSNR/PSSNL
-
PTGNR/PTGNL
-
PTTNR/PTTNL
-
SCLCR/SCLCL
-
SDJCR/SDJCL
-
SDNCN
-
SRACR/SRACL
-
SRDCN
-
SSDCN
-
SSSCR/SSSCL
-
STFCR/STFCL
-
SVACR/SVACL
-
SVJBR/SVJBL
-
SVJCR/SVJCL
-
SVVBN
-
SVVCN
-
WTENN
-
WTJNR/WTJNL
-
WWLNR/WWLNL
-
PDNNR/PDNNL
-
SVHBR/SVHBL
-
PDNNN
-
PTFNR/PTFNL
-
SCACR/SCACL
-
SDACR/SDACL
-
SSBCR/SSBCL
-
SRGCR/SRGCL
-
SSKCR/SSKCL
-
STGCR/STGCL
-
SVABR/SVABL
-
SVQCR/SVQCL
-
SWACR/SWACL
-
WTQNR/WTQNL
-
-
Державки резьбовые
-
Державки отрезные, канавочные
-
Держатели отрезного лезвия
-
Лезвия отрезные
-
Мини-резцы твердосплавные
-
-
Оснастка для фрезерных станков
-
Фрезерные патроны
-
BT
-
BT-ER (для цанг ER)
-
BT-FMB (для насадных фрез)
-
BT-SCA (для дисковых фрез)
-
BT-D (тестовые оправки)
-
BT-SLN Weldon
-
BT-MTA (конус Морзе с лапкой)
-
BT-MTB (конус Морзе с резьбовым отверстием)
-
BT-DC (высокоскоростные патроны для цанг DC)
-
BT-APU
-
BT-SC (для цилиндрических цанг SC)
-
BT-GT (для резьбовых цанг GT12/24/42)
-
BT-TER (патроны с осевой компенсацией по длине для цанг ER)
-
BT-OZ(EOC) (для силовых цанг OZ)
-
BT-PHC (гидропластовые патроны)
-
-
Конус Морзе MTA/MTB
-
HSK
-
Цилиндрический хвостовик
-
NT
-
SK
-
SK-FMB (для насадных фрез)
-
SK-SLN (Weldon)
-
SK-TER (патроны с осевой компенсацией по длине для цанг ER)
-
SK-SC (для цилиндрических цанг SC)
-
SK-MTB (конус Морзе с резьбовым отверстием)
-
SK-MTA (конус Морзе с лапкой)
-
SK-ER (для цанг ER)
-
SK-GT (для резьбовых цанг GT12/24/42)
-
SK-OZ(EOC) (для силовых цанг OZ)
-
SK-APU (сверлильные быстрозажимные патроны)
-
SK-PHC (гидропластовые патроны)
-
-
-
Прихваты, прижимы, упоры
-
Цанги
-
Штревели
-
3D тестеры
-
Тиски станочные
-
Аксессуары и запчасти
- Силовые высокоточные VQC
-
640 Multitasking
-
Трехкулачковые NBK
-
Гидравлические DCV
-
Модульные двойные ZQ83
-
С регулируемым усилием зажима HPAC
-
Самоцентрирующиеся SC-I
-
Модульные GT
-
Глобусные HHY
-
Лекальные QGG
-
Лекальные QKG
-
Модульные составные ZQ84
-
Гидравлические CHV
-
Самоцентрирующиеся двойные SMC
-
-
Кромкоискатели
-
Магнитные плиты
-
Центроискатели
-
Гайки для цанг
-
Ключи гаечные
-
Приспособления для оправок
-
Наборы прижимов
-
Расточные системы
-
Система нулевого базирования
-
Магнитные захваты
-
Поворотные столы
-
Аксессуары для станочной оснастки
-
Привязка по оси Z
-
Защитные вставки
-
-
Оснастка для токарных станков
-
Кулачки токарные
- Инструментальные блоки BOT
-
Токарные патроны
-
Центры токарные вращающиеся
- Центры вращающиеся
- Центры вращающиеся усиленные M11
- Центры вращающиеся облегченные
- Центры вращающиеся со сменными вставками
- Центры вращающиеся высокоскоростные
- Центры вращающиеся с твердосплавной вставкой
- Центры вращающиеся с удлиненной вершиной
- Центры вращающиеся усиленные
- Центры вращающиеся высокоточные
- Центры вращающиеся грибковые
-
Держатели осевого инструмента
-
Переходные втулки
-
Приспособления для расточки кулачков
-
Инструментальные блоки BMT
-
Центры токарные упорные
-
Сухари для токарных патронов
-
Инструментальные блоки VDI
-
Патроны цанговые
-
Цанги токарные
-
-
Измерительный инструмент
-
Станки
-
Станки ленточные по металлу
-
Лазерные граверы (маркировщики) по металлу
-
Токарные станки
-
Фрезерные станки
-
Заточные станки
-
Резьбонарезные манипуляторы
-
Электроэрозионные станки
-
Промышленные роботы
-
-
Мерч CNC66
-
Проволока, СОЖ, запчасти для электроэрозионных станков
-
Промышленная мебель
-
Запасные части для державок, резцов и фрез
-
Развертки
-
Упаковка
-
Зенковки
-
Плашки
-
Инструмент для снятия заусенцев
-
Корзина пуста
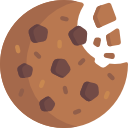
Мы используем файлы cookie для улучшения работы сайта и персонализации. Продолжая использовать сайт, вы соглашаетесь на сбор, обработку cookie-файлов и пользовательских данных с помощью Яндекс.Метрика, в соответствии с нашей Политикой конфиденциальности.