Как измерить твердость металла без твердомера
Оценка сопротивления материала без использования специального прибора требует не только аккуратности, но и знания характерных признаков поведения сплава при различных воздействиях. Первым способом можно назвать метод царапания. Суть его в том, что путем проведения острым предметом по поверхности заготовки определяется относительная устойчивость к повреждению.
Для этой цели удобно брать надфиль с твердостью около 60 HRC, либо напильник с крупной насечкой. В случае с углеродистой сталью царапины остаются при показателях менее 50 HRC, если напильник скользит без следа — изделие выше 60 HRC.
Полезно помнить, что медь царапается ногтем, латунь — легко ножом, а конструкционная сталь — только острым инструментом. На практике для оценки пригоден комплект эталонных образцов, их можно изготовить самостоятельно из заранее проверенных сплавов.
Второй метод — сверление. Этот прием позволяет судить о прочностных свойствах по усилию, требуемому для прохождения сверла через материал. Для испытаний берется сверло диаметром 3 мм из быстрорежущей стали Р6М5. При скорости 500 об/мин на мягкой стали углеродистого типа отверстие получается за 3-5 секунд при среднем давлении руки.
Если сверление идет с трудом, заготовка закалена и имеет показатели свыше 40 HRC. На алюминии такого диаметра отверстие формируется за доли секунды. Практическое сравнение показывает, что нержавеющая сталь AISI 304 дает сопротивление, схожее с конструкционной Ст3, однако сверло греется быстрее. При этом в случае с твердым чугуном сверло оставляет лишь вмятину, без образования отверстия.
Третий способ — сравнение с эталонными деталями. Для оценки подбирается образец, свойства которого заранее известны. Распространена практика использовать ножовочное полотно по металлу с твердостью около 62 HRC. Если режущая кромка скользит по поверхности, не оставляя следов, значит тестируемая заготовка имеет аналогичные или более высокие показатели.
В случае с кусачками или бокорезами — стандартные образцы имеют закалку 55–58 HRC. Попытка перекусить проволоку из исследуемого материала позволяет оценить прочность: если кусачки не справляются, металл тверже. Практическая рекомендация — держать под рукой небольшой набор фрагментов проволоки из стали, латуни, меди, алюминия и использовать их для механического теста.
Важно учитывать структуру материала. Так, ковкий чугун содержит графитовые включения, что снижает общее сопротивление, а высокоуглеродистая сталь отличается повышенной хрупкостью после закалки.
При применении метода царапания заметно, что высокопрочная инструментальная сталь при воздействии надфилем крошится по краям царапины, а низкоуглеродистая лишь пластически деформируется. Полезно применять увеличительное стекло кратностью 10х для оценки характера следа.
В случае сверления ключевым параметром служит тип стружки. При обработке мягкой стали выходит длинная, витая стружка; при работе с закаленным сплавом — короткая, ломающаяся. Нержавеющая сталь дает вязкую, плохо отделяемую стружку. Это дает дополнительную информацию.
При практическом использовании сверла диаметром 2 мм, частота вращения 800 об/мин, подача 0,02 мм/об, мягкая углеродистая сталь позволяет проходить 1 мм за 5 секунд. Если за то же время сверло проникает лишь на 0,3 мм, материал закален.
Для метода сравнения удобно применять испытание на удар. Если молоток с закаленным бойком при легком ударе оставляет четкий отпечаток на поверхности — сплав имеет невысокие показатели сопротивления.
В случае с твердой сталью отпечаток не формируется, зато возможно появление трещин по краю зоны удара. При практическом применении молотка массой 200 г, падение с высоты 20 см на образец меди дает вмятину глубиной 0,3 мм, а на углеродистой стали той же толщины — 0,1 мм.
Дополнительный прием — оценка искр при шлифовании. На точильном круге при обработке мягкой стали искры длинные, разветвленные; высокоуглеродистая дает короткие, яркие пучки. В случае с легированной инструментальной сталью появляется характерная метелка с множественными разветвлениями.
Это позволяет отличить сталь 45 от У8 или Р18. Практически полезно шлифовать небольшую зону при скорости круга 30 м/с, нажим легкий. При этом стандартный круг из электрокорунда зернистостью 40 дает наиболее показательный рисунок искр.
Если оценка требуется для цветных металлов, используется метод сжатия. Медная пластина толщиной 2 мм при сжатии между губками тисков с усилием 500 Н деформируется на 1 мм. Алюминиевая при тех же условиях — на 1,5 мм.
Это позволяет отличить алюминиевые сплавы от медных или латунных. При практическом использовании настольных тисков с шириной губок 100 мм усилие создается при моменте затяжки рукоятки порядка 25 Н·м.
При работе со сварными швами оценка сопротивления производится по поведению при зачистке. Если зачистной круг зернистостью 60 удаляет металл быстро и образуется ровная поверхность — шов выполнен из мягкого сплава.
Если круг стачивается быстрее, чем металл, и поверхность остается шероховатой — применен более прочный материал. Полезно учитывать, что при зачистке шва из стали 09Г2С скорость съема выше на 20% по сравнению с нержавеющей 08Х18Н10.
Для тонкостенных элементов оценка производится методом сгибания. Полоса толщиной 1 мм и шириной 20 мм изгибается на угол 90° с радиусом 5 мм. Если после изгиба образуются трещины на внешнем радиусе, материал хрупок.
В случае с низкоуглеродистой сталью такого не наблюдается. Практическая рекомендация — при сгибе вручную с помощью тисков и оправки из стали диаметром 10 мм наблюдать наличие трещин вдоль линии сгиба.
Если оценка производится в полевых условиях, удобно применять метод удара керном. Если при ударе керна массой 150 г с высоты 10 см образуется углубление диаметром 1 мм — материал имеет сравнительно низкие показатели прочности. Если углубление менее 0,3 мм — высокие. Полезно контролировать глубину с помощью штихмасс-масштабной лупы кратностью 8х.
- На главную
-
Категории
-
Пластины
-
Пластины токарные
-
Пластины для внутреннего и наружного точения
-
Пластины резьбовые
-
Пластины резьбовые ISO
-
Пластины резьбовые трапецеидального профиля, угол 30 град.
-
Пластины резьбовые неполного профиля, угол 55 или 60 град.
-
Пластины резьбовые для нарезания трубной резьбы Whitworth, правые
-
Пластины резьбовые NPT (дюймовая коническая резьба c углом профиля 60 град. и конус 1:16)
-
Пластины резьбовые BSPT (Британский стандарт) полного профиля, угол 55 град.
-
Пластины резьбовые треугольного закругленного профиля
-
Пластины резьбовые UN (Американский стандарт) полного профиля, угол 60 град.
-
-
Пластины отрезные и канавочные
-
TGF32
-
SP
-
MRMN
-
MG...N
- GER-C
- SP для стали
- SP для нержавеющей стали
-
QCMB
-
QPMB
- MGMN для стали
- MGMN для нержавеющей стали
- QPMB для стали
- QPMB для нержавеющей стали
- MRMN для стали
- ZP_S для нержавеющей стали
-
ZP_S
- QCMB для нержавеющей стали
- ZT_D для нержавеющей стали
-
ZT_D
- ZT_D для стали
- QCMB для стали
- TDC для нержавеющей стали
-
TDC
- QC_ для нержавеющей стали
-
QC
- QC_
- ZP_D для нержавеющей стали
-
ZP_D
- ZR_D для нержавеющей стали
-
ZR_D
- ZT_S для нержавеющей стали
-
ZT_S
- ZQMX для стали
-
ZQMX
- CTPA для нержавеющей стали
-
CTPA
- MGMN для чугуна
- MRMN для нержавеющей стали
- MRMN для чугуна
-
GEL-A/B
- GEL-A
-
GEL-A/B-R
-
GEL-C/D/E
- GEL-C
-
GEL-C/D/E-R
-
GER-A/B
- GER-A
-
GER-A/B-R
-
GER-C/D/E
-
GER-C/D/E-R
-
-
-
Пластины фрезерные
-
Пластины для свёрл
-
Лезвия для резьбофрез
-
Пластины со вставками PCBN
-
-
Фрезы
-
Метчики
-
Сверла
-
Ленточные пилы
-
Новое поступление (NEW!)
-
Державки токарные
-
Державки расточные
-
S...-SVJCR/S...-SVJCL
-
S...-DCLNR/S...-DCLNL
-
S...-DDUNR/S...-DDUNL
-
S...-DWLNR/S...-DWLNL
-
S...-MCKNR/S...-MCKNL
-
S...-MCLNR/S...-MCLNL
-
S...-MDQNR/S...-MDQNL
-
S...-MDUNR/S...-MDUNL
-
S...-MSKNR/S-...MSKNL
-
S...-MTJNR/S...-MTJNL
-
S...-MTQNR/S...-MTQNL
-
S...-MTUNR/S...-MTUNL
-
S...-MTFNR/S...-MTFNL
-
S...-MTWNR/S...-MTWNL
-
S...-MVQNR/S-...MVQNL
-
S...-MVUNR/S-...MVUNL
-
S...-MVWNR/S...-MVWNL
-
S...-MVXNR/S...-MVXNL
-
S...-MWLNR/S...-MWLNL
-
S...-PCLNR/S...-PCLNL
-
S...-PDSNR/S...-PDSNL
-
S...-PDUNR/S...-PDUNL
-
S...-PSKNR/S...-PSKNL
-
S...-PWLNR/S...-PWLNL
-
S...-PTFNR/S...-PTFNL
-
S...-SCKCR/S...-SCKCL
-
S...-SCLCR/S...-SCLCL
-
S...-SCLPR/S...-SCLPL
-
S...-SDQCR/S...-SDQCL
-
S...-SDUCR/S...-SDUCL
-
S...-SDZCR/S...-SDZCL
-
S...-SSSCR/S...-SSSCL
-
S...-SSKCR/S...-SSKCL
-
S...-STFCR/S-...STFCL
-
S...-STUCR/S-...STUCL
-
S...-SVUCR/S-...SVUCL
-
S...-SVUBR/S...-SVUBL
-
-
Державки проходные
-
CCLNR/CCLNL
-
CRDNN
-
CSDNN
-
CSKNR/CSKNL
-
CTJNR/CTJNL
-
DCBNR/DCBNL
-
DCKNR/DCKNL
-
DCLNR/DCLNL
-
DCMNN
-
DDJNR/DDJNL
-
DDPNN
-
DSSNR/DSSNL
-
DDQNR/DDQNL
-
DSBNR/DSBNL
-
DSDNN
-
DSKNR/DSKNL
-
DTFNR/DTFNL
-
DTGNR/DTGNL
-
DVJNR/DVJNL
-
DVVNN
-
DWLNR/DWLNL
-
ECLNR/ECLNL
-
EDJNR/EDJNL
-
EVJNR/EVJNL
-
EWLNR/EWLNL
-
MCBNR/MCBNL
-
MCKNR/MCKNL
-
MCLNR/MCLNL
-
MCMNN
-
MDJNR/MDJNL
-
MDPNN
-
MDQNR/MDQNL
-
MRDNN
-
MRGNR/MRGNL
-
MSBNR/MSBNL
-
MSDNN
-
MSKNR/MSKNL
-
MSSNR/MSSNL
-
MTENN
-
MTFNR/MTFNL
-
MTGNR/MTGNL
-
MTJNR/MTJNL
-
MTQNR/MTQNL
-
MVJNR/MVJNL
-
MVQNR/MVQNL
-
MVUNR/MVUNL
-
MVVNN
-
MWLNR/MWLNL
-
PWLNR/PWLNL
-
PCLNR/PCLNL
-
PDJNR/PDJNL
-
PRACR/PRACL
-
PRDCN
-
PCBNR/PCBNL
-
PRGCR/PRGCL
-
PSBNR/PSBNL
-
PSDNN
-
PSSNR/PSSNL
-
PTGNR/PTGNL
-
PTTNR/PTTNL
-
SCLCR/SCLCL
-
SDJCR/SDJCL
-
SDNCN
-
SRACR/SRACL
-
SRDCN
-
SSDCN
-
SSSCR/SSSCL
-
STFCR/STFCL
-
SVACR/SVACL
-
SVJBR/SVJBL
-
SVJCR/SVJCL
-
SVVBN
-
SVVCN
-
WTENN
-
WTJNR/WTJNL
-
WWLNR/WWLNL
-
PDNNR/PDNNL
-
SVHBR/SVHBL
-
PDNNN
-
PTFNR/PTFNL
-
SCACR/SCACL
-
SDACR/SDACL
-
SSBCR/SSBCL
-
SRGCR/SRGCL
-
SSKCR/SSKCL
-
STGCR/STGCL
-
SVABR/SVABL
-
SVQCR/SVQCL
-
SWACR/SWACL
-
WTQNR/WTQNL
-
-
Державки резьбовые
-
Державки отрезные, канавочные
-
Держатели отрезного лезвия
-
Лезвия отрезные
-
Мини-резцы твердосплавные
-
-
Оснастка для фрезерных станков
-
Фрезерные патроны
-
BT
-
BT-ER (для цанг ER)
-
BT-FMB (для насадных фрез)
-
BT-SCA (для дисковых фрез)
-
BT-D (тестовые оправки)
-
BT-SLN Weldon
-
BT-MTA (конус Морзе с лапкой)
-
BT-MTB (конус Морзе с резьбовым отверстием)
-
BT-DC (высокоскоростные патроны для цанг DC)
-
BT-APU
-
BT-SC (для цилиндрических цанг SC)
-
BT-GT (для резьбовых цанг GT12/24/42)
-
BT-TER (патроны с осевой компенсацией по длине для цанг ER)
-
BT-OZ(EOC) (для силовых цанг OZ)
-
BT-PHC (гидропластовые патроны)
-
-
Конус Морзе MTA/MTB
-
HSK
-
Цилиндрический хвостовик
-
NT
-
SK
-
SK-FMB (для насадных фрез)
-
SK-SLN (Weldon)
-
SK-TER (патроны с осевой компенсацией по длине для цанг ER)
-
SK-SC (для цилиндрических цанг SC)
-
SK-MTB (конус Морзе с резьбовым отверстием)
-
SK-MTA (конус Морзе с лапкой)
-
SK-ER (для цанг ER)
-
SK-GT (для резьбовых цанг GT12/24/42)
-
SK-OZ(EOC) (для силовых цанг OZ)
-
SK-APU (сверлильные быстрозажимные патроны)
-
SK-PHC (гидропластовые патроны)
-
-
-
Прихваты, прижимы, упоры
-
Цанги
-
Штревели
-
3D тестеры
-
Тиски станочные
-
Аксессуары и запчасти
- Силовые высокоточные VQC
-
640 Multitasking
-
Трехкулачковые NBK
-
Гидравлические DCV
-
Модульные двойные ZQ83
-
С регулируемым усилием зажима HPAC
-
Самоцентрирующиеся SC-I
-
Модульные GT
-
Глобусные HHY
-
Лекальные QGG
-
Лекальные QKG
-
Модульные составные ZQ84
-
Гидравлические CHV
-
Самоцентрирующиеся двойные SMC
-
-
Кромкоискатели
-
Магнитные плиты
-
Центроискатели
-
Гайки для цанг
-
Ключи гаечные
-
Приспособления для оправок
-
Наборы прижимов
-
Расточные системы
-
Система нулевого базирования
-
Магнитные захваты
-
Поворотные столы
-
Аксессуары для станочной оснастки
-
Привязка по оси Z
-
-
Оснастка для токарных станков
-
Кулачки токарные
- Инструментальные блоки BOT
-
Токарные патроны
-
Центры токарные вращающиеся
- Центры вращающиеся
- Центры вращающиеся усиленные M11
- Центры вращающиеся облегченные
- Центры вращающиеся со сменными вставками
- Центры вращающиеся высокоскоростные
- Центры вращающиеся с твердосплавной вставкой
- Центры вращающиеся с удлиненной вершиной
- Центры вращающиеся усиленные
- Центры вращающиеся высокоточные
- Центры вращающиеся грибковые
-
Держатели осевого инструмента
-
Переходные втулки
-
Приспособления для расточки кулачков
-
Инструментальные блоки BMT
-
Центры токарные упорные
-
Сухари для токарных патронов
-
Инструментальные блоки VDI
-
Патроны цанговые
-
Цанги токарные
-
-
Измерительный инструмент
-
Станки
-
Станки ленточные по металлу
-
Лазерные граверы (маркировщики) по металлу
-
Токарные станки
-
Фрезерные станки
-
Заточные станки
-
Резьбонарезные манипуляторы
-
Электроэрозионные станки
-
Промышленные роботы
-
-
Мерч CNC66
-
Проволока, СОЖ, запчасти для электроэрозионных станков
-
Промышленная мебель
-
Запасные части для державок, резцов и фрез
-
Развертки
-
Упаковка
-
Зенковки
-
Плашки
-
Инструмент для снятия заусенцев
- выгрузка
-
Корзина пуста
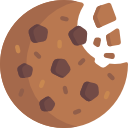
Мы используем файлы cookie для улучшения работы сайта и персонализации. Продолжая использовать сайт, вы соглашаетесь на сбор, обработку cookie-файлов и пользовательских данных с помощью Яндекс.Метрика, в соответствии с нашей Политикой конфиденциальности.