Фрезеровка титана: оптимальные скорости и подачи для разных видов фрез
Титан отличается низкой теплопроводностью и высокой прочностью, что создает сложности при механической обработке. В процессе резания выделяется значительное количество тепла, которое не отводится быстро из зоны контакта, приводя к ускоренному износу инструмента. Для компенсации этого эффекта необходимо правильно подбирать режимы резания и геометрию режущей кромки.
Скорость резания при работе с титановыми сплавами варьируется в пределах 30-70 м/мин в зависимости от марки материала и типа фрезы. Для ВТ6 оптимальным диапазоном будет 40-50 м/мин, тогда как более мягкие сплавы, такие как ВТ1-0, допускают увеличение до 60 м/мин. Подача на зуб обычно составляет 0,03-0,1 мм, но точное значение подбирается исходя из жесткости системы станок-инструмент-деталь.
Твердосплавные фрезы с покрытием TiAlN демонстрируют лучшую стойкость при обработке титана. Угол заострения режущей кромки должен быть в пределах 85-90 градусов, а передний угол — от 5 до 10 градусов для снижения сил резания. Диаметр инструмента влияет на выбор скорости: для фрез 6-10 мм оптимальная частота вращения составит 1500-2500 об/мин, а для инструмента 16-20 мм — 800-1200 об/мин.
Черновое фрезерование требует меньших скоростей, но больших подач. Так, при снятии слоя 2-3 мм за проход подачу можно увеличить до 0,08-0,12 мм на зуб, снизив скорость до 35-45 м/мин. Чистовая обработка, напротив, выполняется на повышенных оборотах (50-70 м/мин) с уменьшенной подачей (0,02-0,05 мм на зуб) для достижения шероховатости Ra 1,6 и ниже.
Конические фрезы с углом конуса 30 градусов применяются для обработки сложных профилей. Их преимущество — плавное врезание и снижение вибраций. Скорость резания для такого инструмента должна быть на 15-20% ниже, чем для цилиндрических аналогов, а подача — в пределах 0,04-0,07 мм на зуб.
Шарошечные фрезы эффективны при обработке глубоких пазов и полостей. Из-за большого контакта с материалом их используют на скоростях 25-40 м/мин с подачей 0,03-0,06 мм на зуб. Охлаждение обязательно — лучше применять СОЖ под высоким давлением (до 70 бар) для эффективного отвода стружки и снижения температуры в зоне резания.
Для торцевого фрезерования подходят инструменты с большим числом зубьев (4-6), что позволяет увеличить подачу на оборот до 0,15-0,25 мм. Однако при этом необходимо снижать скорость до 30-40 м/мин, чтобы избежать перегрева.
Спиральные фрезы с переменным шагом зубьев уменьшают вибрации, что особенно актуально при обработке тонкостенных деталей. Их применяют на скоростях 45-60 м/мин с подачей 0,05-0,09 мм на зуб. Увеличение длины рабочей части инструмента требует пропорционального снижения режимов.
При выборе параметров резания стоит ориентироваться на стойкость инструмента. Для твердосплавных фрез она составляет 60-120 минут в зависимости от интенсивности работы. Если износ наступает быстрее, необходимо скорректировать скорость или подачу.
Оптимальная глубина резания при черновой обработке — 1,5-3 мм, при чистовой — 0,2-0,5 мм. Увеличение этих значений ведет к росту нагрузок и снижению точности. Для достижения стабильного результата рекомендуется использовать станки с ЧПУ, позволяющие точно выдерживать заданные режимы.
Титан склонен к налипанию на режущую кромку, поэтому стоит избегать слишком малых подач. Минимальное значение — 0,02 мм на зуб, иначе стружка не отводится, а приваривается к инструменту.
Для контроля процесса можно использовать формулу расчета мощности резания: P = K × Q, где K — удельная сила резания (для титана около 3000 Н/мм²), Q — объем снимаемого металла в минуту. Это помогает подобрать оборудование с достаточной мощностью привода.
При фрезеровании титана часто возникают вибрации, которые снижают качество поверхности. Для их уменьшения нужно применять инструмент с максимально возможным диаметром хвостовика и минимальным вылетом. Демпфированные оправки также помогают повысить стабильность процесса.
Стружка должна быть мелкой и ломкой — это признак правильно выбранных режимов. Длинная витая стружка указывает на недостаточную подачу или износ фрезы. В таком случае требуется проверить заточку или увеличить подачу на 10-15%.
Для повышения эффективности можно использовать трохоидальные стратегии фрезерования, когда инструмент движется по спиральной траектории с постоянным припуском. Это снижает тепловыделение и увеличивает стойкость фрезы.
При работе с титановыми сплавами важно избегать застоя стружки в зоне резания. Лучше применять сжатый воздух или СОЖ с добавками против налипания.
Геометрия режущей кромки играет решающую роль. Острые кромки склонны к выкрашиванию, поэтому небольшое затупление (радиус 0,03-0,05 мм) повышает стойкость инструмента.
Для достижения высокой точности рекомендуется использовать фрезы с жестким креплением пластин. Быстросменные системы не всегда обеспечивают достаточную стабильность, что приводит к биению и ухудшению качества поверхности.
Титан обладает памятью формы, поэтому после механической обработки возможны небольшие деформации. Чтобы минимизировать этот эффект, следует оставлять припуск 0,1-0,2 мм на финишный проход.
При фрезеровании глубоких полостей стоит применять инструмент с внутренним подводом СОЖ. Это обеспечивает эффективное охлаждение и продлевает срок службы фрезы.
Для контроля качества поверхности можно использовать параметр Ra, который не должен превышать 3,2 мкм после чистовой обработки. Если шероховатость выше, нужно проверить заточку инструмента или снизить подачу.
Твердость титана после обработки может повышаться из-за наклепа. Чтобы избежать этого, следует использовать острые фрезы и не допускать перегрева заготовки.
Соблюдение этих рекомендаций позволяет добиться высокой производительности и качества при фрезеровании титановых деталей. Главное — подбирать режимы индивидуально для каждой задачи и контролировать состояние инструмента.
- На главную
-
Категории
-
Пластины твердосплавные
-
Пластины токарные
-
Пластины для внутреннего и наружного точения
-
Пластины резьбовые
-
Пластины резьбовые ISO
-
Пластины резьбовые трапецеидального профиля, угол 30 град.
-
Пластины резьбовые неполного профиля, угол 55 или 60 град.
-
Пластины резьбовые для нарезания трубной резьбы Whitworth, правые
-
Пластины резьбовые NPT (дюймовая коническая резьба c углом профиля 60 град. и конус 1:16)
-
Пластины резьбовые BSPT (Британский стандарт) полного профиля, угол 55 град.
-
Пластины резьбовые треугольного закругленного профиля
-
Пластины резьбовые UN (Американский стандарт) полного профиля, угол 60 град.
- Пластины резьбовые UN (Американский стандарт) полного профиля, угол 60 град.
- Панцирная трубная резьба Pg 80 град.
- Пластины резьбовые трапецеидального профиля, угол 30 град.
- Пластины резьбовые BSPT (Британский стандарт) полного профиля, угол 55 град.
- Пластины резьбовые NPT (дюймовая коническая резьба c углом профиля 60 град. и конус 1:16)
- Пластины резьбовые неполного профиля, угол 55 или 60 град.
- Упорная резьба SAGE 30 град.
-
-
Пластины отрезные и канавочные
-
TGF32
-
SP
-
MRMN
-
MG...N
- GER-C
- SP для стали
- SP для нержавеющей стали
-
QCMB
-
QPMB
- MGMN для стали
- MGMN для нержавеющей стали
- QPMB для стали
- QPMB для нержавеющей стали
- MRMN для стали
- ZP_S для нержавеющей стали
-
ZP_S
- QCMB для нержавеющей стали
- ZT_D для нержавеющей стали
-
ZT_D
- ZT_D для стали
- QCMB для стали
- TDC для нержавеющей стали
-
TDC
- QC_ для нержавеющей стали
-
QC
- QC_
- ZP_D для нержавеющей стали
-
ZP_D
- ZR_D для нержавеющей стали
-
ZR_D
- ZT_S для нержавеющей стали
-
ZT_S
- ZQMX для стали
-
ZQMX
- CTPA для нержавеющей стали
-
CTPA
- MGMN для чугуна
- MRMN для нержавеющей стали
- MRMN для чугуна
-
GEL-A/B
- GEL-A
-
GEL-A/B-R
-
GEL-C/D/E
- GEL-C
-
GEL-C/D/E-R
-
GER-A/B
- GER-A
-
GER-A/B-R
-
GER-C/D/E
-
GER-C/D/E-R
- MGMN
- MGGN
- MB
- ZTKS
- JRMN
- GK-R
- ZRFD
- KTMD
- KGT
- JSMN
- SPDR
-
-
-
Пластины фрезерные
-
Пластины для сверл
-
Лезвия для резьбофрез
-
Пластины со вставками PCBN
- Пластины для червячного зуба 40°
-
-
Фрезы
-
Фрезы монолитные
-
Концевые
-
HRC72
- HRC45
- HRC55
- HRC60
- HRC65
- HRC66
- HRC70
- HRC45
- HRC55
- HRC60
- HRC65
- HRC66
- HRC70
- HRC45
- HRC55
- HRC60
- HRC65
- HRC66
- HRC70
- HRC45
- HRC55
- HRC60
- HRC65
- HRC66
- HRC70
- HRC45
- HRC55
- HRC60
- HRC65
- HRC66
- HRC70
- HRC45
- HRC55
- HRC60
- HRC65
- HRC66
- HRC70
- HRC45
- HRC55
- HRC60
- HRC65
- HRC66
- HRC70
- HRC55
- HRC65
- HRC70
- HRC60
- HRC45
- HRC66
- HRC45
- HRC55
- HRC60
- HRC65
- HRC66
- HRC70
- HRC45
- HRC55
- HRC60
- HRC65
- HRC66
- HRC70
- HRC45
- HRC55
- HRC60
- HRC65
- HRC66
- HRC70
- HRC45
- HRC55
- HRC60
- HRC65
- HRC66
- HRC70
- HRC45
- HRC55
- HRC60
- HRC65
- HRC66
- HRC70
- HRC45
- HRC55
- HRC60
- HRC65
- HRC66
- HRC70
- HRC45
- HRC55
- HRC60
- HRC65
- HRC66
- HRC70
- HRC45
- HRC55
- HRC60
- HRC65
- HRC66
- HRC70
- HRC45
- HRC55
- HRC60
- HRC65
- HRC66
- HRC70
- HRC45
- HRC55
- HRC60
- HRC65
- HRC66
- HRC70
- HRC45
- HRC55
- HRC60
- HRC65
- HRC66
- HRC70
- HRC45
- HRC55
- HRC60
- HRC65
- HRC66
- HRC70
- HRC45
- HRC55
- HRC60
- HRC65
- HRC66
- HRC70
- HRC45
- HRC55
- HRC60
- HRC65
- HRC66
- HRC70
- HRC45
- HRC55
- HRC60
- HRC65
- HRC66
- HRC70
- HRC45
- HRC55
- HRC60
- HRC65
- HRC66
- HRC70
- HRC45
- HRC55
- HRC60
- HRC65
- HRC66
- HRC70
- HRC45
- HRC55
- HRC60
- HRC65
- HRC66
- HRC70
- HRC45
- HRC55
- HRC60
- HRC65
- HRC66
- HRC70
- HRC45
- HRC55
- HRC60
- HRC65
- HRC66
- HRC70
- HRC45
- HRC55
- HRC60
- HRC65
- HRC66
- HRC70
- HRC45
- HRC55
- HRC60
- HRC65
- HRC66
- HRC70
- HRC45
- HRC55
- HRC60
- HRC65
- HRC66
- HRC70
- HRC45
- HRC55
- HRC60
- HRC65
- HRC66
- HRC70
- HRC45
- HRC55
- HRC60
- HRC65
- HRC66
- HRC70
- HRC45
- HRC55
- HRC60
- HRC65
- HRC66
- HRC70
- HRC45
- HRC55
- HRC60
- HRC65
- HRC66
- HRC70
- HRC45
- HRC55
- HRC60
- HRC65
- HRC66
- HRC70
- HRC45
- HRC55
- HRC60
- HRC65
- HRC66
- HRC70
- HRC45
- HRC55
- HRC60
- HRC65
- HRC66
- HRC70
- HRC45
- HRC55
- HRC60
- HRC65
- HRC66
- HRC70
- HRC45
- HRC55
- HRC60
- HRC65
- HRC66
- HRC70
-
-
Радиусные
-
HRC45
-
HRC60
-
HRC66
-
HRC45
-
HRC55
-
HRC60
-
HRC65
-
HRC70
- HRC55
- HRC65
- HRC70
- HRC55
- HRC65
- HRC70
- HRC55
- HRC65
- HRC70
- HRC55
- HRC65
- HRC70
- HRC55
- HRC65
- HRC70
- HRC55
- HRC65
- HRC70
- HRC55
- HRC65
- HRC70
- HRC70
- HRC55
- HRC65
- HRC55
- HRC65
- HRC70
- HRC55
- HRC65
- HRC70
- HRC55
- HRC65
- HRC70
- HRC55
- HRC65
- HRC70
- HRC55
- HRC65
- HRC70
- HRC55
- HRC65
- HRC70
- HRC55
- HRC65
- HRC70
- HRC55
- HRC65
- HRC70
- HRC55
- HRC65
- HRC70
- HRC55
- HRC65
- HRC70
- HRC55
- HRC65
- HRC70
- HRC55
- HRC65
- HRC70
- HRC55
- HRC65
- HRC70
- HRC55
- HRC65
- HRC70
- HRC55
- HRC65
- HRC70
- HRC55
- HRC65
- HRC70
- HRC55
- HRC65
- HRC70
- HRC55
- HRC65
- HRC70
- HRC55
- HRC65
- HRC70
- HRC55
- HRC65
- HRC70
- HRC55
- HRC65
- HRC70
- HRC55
- HRC65
- HRC70
- HRC55
- HRC65
- HRC70
- HRC55
- HRC65
- HRC70
- HRC55
- HRC65
- HRC70
- HRC55
- HRC65
- HRC70
- HRC55
- HRC65
- HRC70
- HRC55
- HRC65
- HRC70
- HRC55
- HRC65
- HRC70
- HRC55
- HRC65
- HRC70
- HRC55
- HRC65
- HRC70
- HRC55
- HRC65
- HRC70
-
-
Сферические
-
Фасочные
-
Граверы
-
Дисковые
- Резьбофрезы
-
-
Фрезы со сменными пластинами
-
Фрезы дисковые
-
Фрезы концевые
-
ASM
-
BAP
- BMR
-
EMR
-
PE03
-
RB02
-
RB03
-
TEBL
-
ХК01
- ХК02
- SSM390
- EMP01
- AF06
- BAP
- EMR
- EMRW
- EXN03
- PE01
- PE02
- PE05
- R217.96
- RF01
- AF06
- BAP
- EMR
- EMRW
- EXN03
- PE01
- PE02
- PE05
- R217.96
- RF01
- AF06
- BAP
- EMR
- EMRW
- EXN03
- PE01
- PE02
- PE05
- R217.96
- RF01
- AF06
- BAP
- EMR
- EMRW
- EXN03
- PE01
- PE02
- PE05
- R217.96
- RF01
- AF06
- BAP
- EMR
- EMRW
- EXN03
- PE01
- PE02
- PE05
- R217.96
- RF01
- AF06
- BAP
- EMR
- EMRW
- EXN03
- PE01
- PE02
- PE05
- R217.96
- RF01
- AF06
- BAP
- EMR
- EMRW
- EXN03
- PE01
- PE02
- PE05
- R217.96
- RF01
- RF01
- EXN03
- PE02
- AF06
- R217.96
- EMRW
- EMR
- BAP
- PE01
- PE05
- AF06
- BAP
- EMR
- EMRW
- EXN03
- PE01
- PE02
- PE05
- R217.96
- RF01
- AF06
- BAP
- EMR
- EMRW
- EXN03
- PE01
- PE02
- PE05
- R217.96
- RF01
- AF06
- BAP
- EMR
- EMRW
- EXN03
- PE01
- PE02
- PE05
- R217.96
- RF01
- AF06
- BAP
- EMR
- EMRW
- EXN03
- PE01
- PE02
- PE05
- R217.96
- RF01
- AF06
- BAP
- EMR
- EMRW
- EXN03
- PE01
- PE02
- PE05
- R217.96
- RF01
- AF06
- BAP
- EMR
- EMRW
- EXN03
- PE01
- PE02
- PE05
- R217.96
- RF01
- AF06
- BAP
- EMR
- EMRW
- EXN03
- PE01
- PE02
- PE05
- R217.96
- RF01
- AF06
- BAP
- EMR
- EMRW
- EXN03
- PE01
- PE02
- PE05
- R217.96
- RF01
- AF06
- BAP
- EMR
- EMRW
- EXN03
- PE01
- PE02
- PE05
- R217.96
- RF01
- AF06
- BAP
- EMR
- EMRW
- EXN03
- PE01
- PE02
- PE05
- R217.96
- RF01
- AF06
- BAP
- EMR
- EMRW
- EXN03
- PE01
- PE02
- PE05
- R217.96
- RF01
- AF06
- BAP
- EMR
- EMRW
- EXN03
- PE01
- PE02
- PE05
- R217.96
- RF01
- AF06
- BAP
- EMR
- EMRW
- EXN03
- PE01
- PE02
- PE05
- R217.96
- RF01
- AF06
- BAP
- EMR
- EMRW
- EXN03
- PE01
- PE02
- PE05
- R217.96
- RF01
- AF06
- BAP
- EMR
- EMRW
- EXN03
- PE01
- PE02
- PE05
- R217.96
- RF01
- AF06
- BAP
- EMR
- EMRW
- EXN03
- PE01
- PE02
- PE05
- R217.96
- RF01
- AF06
- BAP
- EMR
- EMRW
- EXN03
- PE01
- PE02
- PE05
- R217.96
- RF01
- AF06
- BAP
- EMR
- EMRW
- EXN03
- PE01
- PE02
- PE05
- R217.96
- RF01
- AF06
- BAP
- EMR
- EMRW
- EXN03
- PE01
- PE02
- PE05
- R217.96
- RF01
- AF06
- BAP
- EMR
- EMRW
- EXN03
- PE01
- PE02
- PE05
- R217.96
- RF01
- AF06
- BAP
- EMR
- EMRW
- EXN03
- PE01
- PE02
- PE05
- R217.96
- RF01
- AF06
- BAP
- EMR
- EMRW
- EXN03
- PE01
- PE02
- PE05
- R217.96
- RF01
- AF06
- BAP
- EMR
- EMRW
- EXN03
- PE01
- PE02
- PE05
- R217.96
- RF01
- AF06
- BAP
- EMR
- EMRW
- EXN03
- PE01
- PE02
- PE05
- R217.96
- RF01
- AF06
- BAP
- EMR
- EMRW
- EXN03
- PE01
- PE02
- PE05
- R217.96
- RF01
- AF06
- BAP
- EMR
- EMRW
- EXN03
- PE01
- PE02
- PE05
- R217.96
- RF01
- AF06
- BAP
- EMR
- EMRW
- EXN03
- PE01
- PE02
- PE05
- R217.96
- RF01
- AF06
- BAP
- EMR
- EMRW
- EXN03
- PE01
- PE02
- PE05
- R217.96
- RF01
- AF06
- BAP
- EMR
- EMRW
- EXN03
- PE01
- PE02
- PE05
- R217.96
- RF01
- AF06
- BAP
- EMR
- EMRW
- EXN03
- PE01
- PE02
- PE05
- R217.96
- RF01
- AF06
- BAP
- EMR
- EMRW
- EXN03
- PE01
- PE02
- PE05
- R217.96
- RF01
- AF06
- BAP
- EMR
- EMRW
- EXN03
- PE01
- PE02
- PE05
- R217.96
- RF01
-
-
Фрезы резьбонарезные
-
Фрезы торцевые насадные
-
Фрезы фасочные
-
-
Фрезы со сменными головками
- BNM
-
C-MFL
- R390
-
XCH
- AJX
- BAP
- EMR
- AJX
- BAP
- EMR
- AJX
- BAP
- EMR
- AJX
- BAP
- EMR
- AJX
- BAP
- EMR
- AJX
- BAP
- EMR
- AJX
- BAP
- EMR
- BAP
- EMR
- AJX
- AJX
- BAP
- EMR
- AJX
- BAP
- EMR
- AJX
- BAP
- EMR
- AJX
- BAP
- EMR
- AJX
- BAP
- EMR
- AJX
- BAP
- EMR
- AJX
- BAP
- EMR
- AJX
- BAP
- EMR
- AJX
- BAP
- EMR
- AJX
- BAP
- EMR
- AJX
- BAP
- EMR
- AJX
- BAP
- EMR
- AJX
- BAP
- EMR
- AJX
- BAP
- EMR
- AJX
- BAP
- EMR
- AJX
- BAP
- EMR
- AJX
- BAP
- EMR
- AJX
- BAP
- EMR
- AJX
- BAP
- EMR
- AJX
- BAP
- EMR
- AJX
- BAP
- EMR
- AJX
- BAP
- EMR
- AJX
- BAP
- EMR
- AJX
- BAP
- EMR
- AJX
- BAP
- EMR
- AJX
- BAP
- EMR
- AJX
- BAP
- EMR
- AJX
- BAP
- EMR
- AJX
- BAP
- EMR
- AJX
- BAP
- EMR
- AJX
- BAP
- EMR
- AJX
- BAP
- EMR
-
-
Метчики
-
Сверла
-
Ленточные пилы
-
Новое поступление (NEW!)
-
Державки токарные
-
Державки расточные
-
S...-SVJCR/S...-SVJCL
-
S...-DCLNR/S...-DCLNL
-
S...-DDUNR/S...-DDUNL
-
S...-DWLNR/S...-DWLNL
-
S...-MCKNR/S...-MCKNL
-
S...-MCLNR/S...-MCLNL
-
S...-MDQNR/S...-MDQNL
-
S...-MDUNR/S...-MDUNL
-
S...-MSKNR/S-...MSKNL
-
S...-MTJNR/S...-MTJNL
-
S...-MTQNR/S...-MTQNL
-
S...-MTUNR/S...-MTUNL
-
S...-MTFNR/S...-MTFNL
-
S...-MTWNR/S...-MTWNL
-
S...-MVQNR/S-...MVQNL
-
S...-MVUNR/S-...MVUNL
-
S...-MVWNR/S...-MVWNL
-
S...-MVXNR/S...-MVXNL
-
S...-MWLNR/S...-MWLNL
-
S...-PCLNR/S...-PCLNL
-
S...-PDSNR/S...-PDSNL
-
S...-PDUNR/S...-PDUNL
-
S...-PSKNR/S...-PSKNL
-
S...-PWLNR/S...-PWLNL
-
S...-PTFNR/S...-PTFNL
-
S...-SCKCR/S...-SCKCL
-
S...-SCLCR/S...-SCLCL
-
S...-SCLPR/S...-SCLPL
-
S...-SDQCR/S...-SDQCL
-
S...-SDUCR/S...-SDUCL
-
S...-SDZCR/S...-SDZCL
-
S...-SSSCR/S...-SSSCL
-
S...-SSKCR/S...-SSKCL
-
S...-STFCR/S-...STFCL
-
S...-STUCR/S-...STUCL
-
S...-SVUCR/S-...SVUCL
-
S...-SVUBR/S...-SVUBL
-
-
Державки проходные
-
CCLNR/CCLNL
-
CRDNN
-
CSDNN
-
CSKNR/CSKNL
-
CTJNR/CTJNL
-
DCBNR/DCBNL
-
DCKNR/DCKNL
-
DCLNR/DCLNL
-
DCMNN
-
DDJNR/DDJNL
-
DDPNN
-
DSSNR/DSSNL
-
DDQNR/DDQNL
-
DSBNR/DSBNL
-
DSDNN
-
DSKNR/DSKNL
-
DTFNR/DTFNL
-
DTGNR/DTGNL
-
DVJNR/DVJNL
-
DVVNN
-
DWLNR/DWLNL
-
ECLNR/ECLNL
-
EDJNR/EDJNL
-
EVJNR/EVJNL
-
EWLNR/EWLNL
-
MCBNR/MCBNL
-
MCKNR/MCKNL
-
MCLNR/MCLNL
-
MCMNN
-
MDJNR/MDJNL
-
MDPNN
-
MDQNR/MDQNL
-
MRDNN
-
MRGNR/MRGNL
-
MSBNR/MSBNL
-
MSDNN
-
MSKNR/MSKNL
-
MSSNR/MSSNL
-
MTENN
-
MTFNR/MTFNL
-
MTGNR/MTGNL
-
MTJNR/MTJNL
-
MTQNR/MTQNL
-
MVJNR/MVJNL
-
MVQNR/MVQNL
-
MVUNR/MVUNL
-
MVVNN
-
MWLNR/MWLNL
-
PWLNR/PWLNL
-
PCLNR/PCLNL
-
PDJNR/PDJNL
-
PRACR/PRACL
-
PRDCN
-
PCBNR/PCBNL
-
PRGCR/PRGCL
-
PSBNR/PSBNL
-
PSDNN
-
PSSNR/PSSNL
-
PTGNR/PTGNL
-
PTTNR/PTTNL
-
SCLCR/SCLCL
-
SDJCR/SDJCL
-
SDNCN
-
SRACR/SRACL
-
SRDCN
-
SSDCN
-
SSSCR/SSSCL
-
STFCR/STFCL
-
SVACR/SVACL
-
SVJBR/SVJBL
-
SVJCR/SVJCL
-
SVVBN
-
SVVCN
-
WTENN
-
WTJNR/WTJNL
-
WWLNR/WWLNL
-
PDNNR/PDNNL
-
SVHBR/SVHBL
-
PDNNN
-
PTFNR/PTFNL
-
SCACR/SCACL
-
SDACR/SDACL
-
SSBCR/SSBCL
-
SRGCR/SRGCL
-
SSKCR/SSKCL
-
STGCR/STGCL
-
SVABR/SVABL
-
SVQCR/SVQCL
-
SWACR/SWACL
-
WTQNR/WTQNL
-
-
Державки резьбовые
-
Державки отрезные, канавочные
-
Держатели отрезного лезвия
-
Лезвия отрезные
-
Мини-резцы твердосплавные
-
-
Оснастка для фрезерных станков
-
Фрезерные патроны
-
BT
-
BT-ER (для цанг ER)
-
BT-FMB (для насадных фрез)
-
BT-SCA (для дисковых фрез)
-
BT-D (тестовые оправки)
-
BT-SLN Weldon
-
BT-MTA (конус Морзе с лапкой)
-
BT-MTB (конус Морзе с резьбовым отверстием)
-
BT-DC (высокоскоростные патроны для цанг DC)
-
BT-APU
-
BT-SC (для цилиндрических цанг SC)
-
BT-GT (для резьбовых цанг GT12/24/42)
-
BT-TER (патроны с осевой компенсацией по длине для цанг ER)
-
BT-OZ(EOC) (для силовых цанг OZ)
-
BT-PHC (гидропластовые патроны)
-
-
Конус Морзе MTA/MTB
-
HSK
-
Цилиндрический хвостовик
-
NT
-
SK
-
SK-FMB (для насадных фрез)
-
SK-SLN (Weldon)
-
SK-TER (патроны с осевой компенсацией по длине для цанг ER)
-
SK-SC (для цилиндрических цанг SC)
-
SK-MTB (конус Морзе с резьбовым отверстием)
-
SK-MTA (конус Морзе с лапкой)
-
SK-ER (для цанг ER)
-
SK-GT (для резьбовых цанг GT12/24/42)
-
SK-OZ(EOC) (для силовых цанг OZ)
-
SK-APU (сверлильные быстрозажимные патроны)
-
SK-PHC (гидропластовые патроны)
-
-
-
Прихваты, прижимы, упоры
-
Цанги
-
Штревели
-
3D тестеры
-
Тиски станочные
-
Аксессуары и запчасти
- Силовые высокоточные VQC
-
640 Multitasking
-
Трехкулачковые NBK
-
Гидравлические DCV
-
Модульные двойные ZQ83
-
С регулируемым усилием зажима HPAC
-
Самоцентрирующиеся SC-I
-
Модульные GT
-
Глобусные HHY
-
Лекальные QGG
-
Лекальные QKG
-
Модульные составные ZQ84
-
Гидравлические CHV
-
Самоцентрирующиеся двойные SMC
-
-
Кромкоискатели
-
Магнитные плиты
-
Центроискатели
-
Гайки для цанг
-
Ключи гаечные
-
Приспособления для оправок
-
Наборы прижимов
-
Расточные системы
-
Система нулевого базирования
-
Магнитные захваты
-
Поворотные столы
-
Аксессуары для станочной оснастки
-
Привязка по оси Z
-
Защитные вставки
-
-
Оснастка для токарных станков
-
Кулачки токарные
- Инструментальные блоки BOT
-
Токарные патроны
-
Центры токарные вращающиеся
- Центры вращающиеся
- Центры вращающиеся усиленные M11
- Центры вращающиеся облегченные
- Центры вращающиеся со сменными вставками
- Центры вращающиеся высокоскоростные
- Центры вращающиеся с твердосплавной вставкой
- Центры вращающиеся с удлиненной вершиной
- Центры вращающиеся усиленные
- Центры вращающиеся высокоточные
- Центры вращающиеся грибковые
-
Держатели осевого инструмента
-
Переходные втулки
-
Приспособления для расточки кулачков
-
Инструментальные блоки BMT
-
Центры токарные упорные
-
Сухари для токарных патронов
-
Инструментальные блоки VDI
-
Патроны цанговые
-
Цанги токарные
-
-
Измерительный инструмент
-
Станки
-
Станки ленточные по металлу
-
Лазерные граверы (маркировщики) по металлу
-
Токарные станки
-
Фрезерные станки
-
Заточные станки
-
Резьбонарезные манипуляторы
-
Электроэрозионные станки
-
Промышленные роботы
-
-
Мерч CNC66
-
Проволока, СОЖ, запчасти для электроэрозионных станков
-
Промышленная мебель
-
Запасные части для державок, резцов и фрез
-
Развертки
-
Упаковка
-
Зенковки
-
Плашки
-
Инструмент для снятия заусенцев
-
Корзина пуста
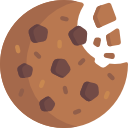
Мы используем файлы cookie для улучшения работы сайта и персонализации. Продолжая использовать сайт, вы соглашаетесь на сбор, обработку cookie-файлов и пользовательских данных с помощью Яндекс.Метрика, в соответствии с нашей Политикой конфиденциальности.