- Главная
- Практическое использование притиров для доводки металлических поверхностей
Практическое использование притиров для доводки металлических поверхностей
Доводка металлических поверхностей притирами позволяет достичь высокой точности обработки, снижая шероховатость до Ra 0,01–0,05 мкм. Этот метод применяется при изготовлении прецизионных деталей, таких как клапаны гидравлических систем, измерительные плитки и направляющие станин. Основной принцип заключается во взаимном скольжении двух поверхностей с применением абразивной пасты или суспензии.
Для работы используют чугунные, бронзовые или стальные притиры, твердость которых должна быть на 10–15% ниже обрабатываемого материала. Чугун СЧ20 или СЧ25 подходит для финишной обработки стальных заготовок, а латунь ЛС59-1 – для доводки бронзовых втулок. Геометрия инструмента повторяет форму детали: плоские плиты применяют для плоскостей, а конические или цилиндрические – для отверстий и валов.
Абразивные составы выбирают в зависимости от требуемой чистоты поверхности. Алмазные пасты с зернистостью 1/0, 3/2 или 5/3 мкм дают минимальную шероховатость, а карборундовые суспензии (F600–F1200) подходят для предварительной обработки. В качестве связующего используют олеиновую кислоту, керосин или смесь масла с керосином в пропорции 1:3.
Скорость притирки не должна превышать 0,5–1,5 м/с, чтобы избежать перегрева и появления задиров. Давление на инструмент регулируют в пределах 0,05–0,15 МПа для черновой стадии и 0,01–0,03 МПа для чистовой. При обработке плоских поверхностей применяют восьмеркообразные движения, обеспечивая равномерный износ абразива.
Для контроля качества используют интерферометры или профилометры, замеряя отклонения от плоскостности в пределах 0,5–1 мкм на длине 100 мм. В случае с коническими соединениями проверяют пятно контакта, которое должно составлять не менее 80% площади сопряжения.
При доводке отверстий диаметром до 50 мм применяют разжимные оправки с регулируемым натягом 0,02–0,05 мм. Вращение инструмента выполняют со скоростью 60–100 об/мин, периодически меняя направление для устранения эллипсности.
Твердосплавные детали обрабатывают алмазными притирами с охлаждением эмульсией. Температура в зоне контакта не должна превышать 60–70°C, чтобы избежать термических деформаций. После финишной доводки поверхность промывают в уайт-спирите для удаления остатков абразива.
Для восстановления геометрии изношенных направляющих станков используют притиры с выверенной плоскостностью 0,002 мм/м. Обработку ведут в несколько проходов, постепенно уменьшая размер абразивных зерен.
При работе с жаропрочными сплавами типа ХН77ТЮР применяют пасты на основе кубического нитрида бора. Их эффективность в 2–3 раза выше, чем у карборундовых составов при обработке материалов с твердостью выше 50 HRC.
Доводка зубчатых колес требует использования профилированных притиров, точно повторяющих форму впадин. Угловая скорость вращения не должна превышать 2 м/с, а радиальное биение готовой детали – 0,01–0,02 мм.
Для уменьшения трения в паре "притир-деталь" добавляют противозадирные присадки, такие как дисульфид молибдена или графит. Их концентрация в смазочно-охлаждающей жидкости составляет 3–5% от общего объема.
После 8–10 циклов обработки инструмент необходимо править на точной плите с абразивом более мелкой фракции. Износ рабочей поверхности не должен превышать 0,01 мм по высоте, иначе снизится качество доводки.
Притиры с канавками глубиной 0,3–0,5 мм обеспечивают лучшее удержание абразивной суспензии. Шаг между канавками выбирают равным 8–12 мм для плоских поверхностей и 3–5 мм для цилиндрических.
Для контроля процесса применяют метод цветных отпечатков: тонкий слой краски наносят на эталонную плиту и оценивают равномерность его переноса на деталь. Площадь контакта должна быть не менее 70% для ответственных соединений.
Температурный режим в цехе поддерживают в пределах 20±2°C, так как нагрев на 5°C вызывает расширение стального притира на 0,006 мм на каждые 100 мм длины.
При доводке сферических поверхностей радиус кривизны инструмента делают на 5–10% меньше, чем у детали. Это компенсирует упругие деформации в зоне контакта.
Остаточные напряжения после обработки не должны превышать 50 МПа, что проверяют рентгеноструктурным анализом. Для снятия напряжений применяют низкотемпературный отпуск при 120–150°C в течение 1–2 часов.
Шероховатость контролируют по эталонным образцам или профилографом. Допустимая волнистость для прецизионных направляющих составляет не более 0,003 мм на длине 300 мм.
Для повышения износостойкости чугунные притиры подвергают отжигу при 500–550°C с последующей закалкой ТВЧ до твердости 180–220 HB. Это увеличивает срок службы инструмента в 1,5–2 раза.
При доводке пар трения подбирают материалы с разной структурой: перлитный чугун обрабатывает закаленную сталь, а ферритный – бронзу. Разница в микротвердости должна составлять 15–20%.
Для устранения местного износа применяют притиры с принудительным вращением абразивных сегментов. Частота их обращения – 30–50 об/мин при основном движении 0,8–1,2 м/с.
Обработку ведут до появления матового блеска без отдельных рисок. На финишной стадии используют пасту с размером зерна 0,5–1 мкм, нанесенную слоем 2–3 мкм.
После окончания работ инструмент очищают щетками с латунным ворсом и хранят в масляной бумаге для предотвращения коррозии. Периодичность поверки геометрии – каждые 50–60 циклов использования.
Для повышения стабильности процесса применяют магнитные плиты, фиксирующие деталь с усилием 0,3–0,5 МПа. Это исключает смещение при обработке тонкостенных заготовок.
Оптимальный зазор между притиром и деталью составляет 0,005–0,01 мм. Его регулируют индикаторными скобами с ценой деления 0,001 мм.
При доводке резьбовых поверхностей шаг притира должен соответствовать обрабатываемой резьбе с допуском ±0,002 мм. Осевое усилие ограничивают 50–70 Н для метрических профилей и 20–30 Н для трубных.
Для контроля цилиндричности валов после обработки применяют трехточечные микрометры с точностью 0,001 мм. Допустимое отклонение от круглости – не более 0,003 мм на диаметре до 50 мм.
Износ инструмента компенсируют подшлифовкой на плоскошлифовальном станке с подачей 0,002–0,005 мм за проход. После правки притир выдерживают 24 часа для стабилизации внутренних напряжений.
- На главную
-
Категории
-
Пластины твердосплавные
-
Пластины токарные
-
Пластины для внутреннего и наружного точения
-
Пластины резьбовые
-
Пластины резьбовые ISO
-
Пластины резьбовые трапецеидального профиля, угол 30 град.
-
Пластины резьбовые неполного профиля, угол 55 или 60 град.
-
Пластины резьбовые для нарезания трубной резьбы Whitworth, правые
-
Пластины резьбовые NPT (дюймовая коническая резьба c углом профиля 60 град. и конус 1:16)
-
Пластины резьбовые BSPT (Британский стандарт) полного профиля, угол 55 град.
-
Пластины резьбовые треугольного закругленного профиля
-
Пластины резьбовые UN (Американский стандарт) полного профиля, угол 60 град.
-
-
Пластины отрезные и канавочные
-
TGF32
-
SP
-
MRMN
-
MG...N
- GER-C
- SP для стали
- SP для нержавеющей стали
-
QCMB
-
QPMB
- MGMN для стали
- MGMN для нержавеющей стали
- QPMB для стали
- QPMB для нержавеющей стали
- MRMN для стали
- ZP_S для нержавеющей стали
-
ZP_S
- QCMB для нержавеющей стали
- ZT_D для нержавеющей стали
-
ZT_D
- ZT_D для стали
- QCMB для стали
- TDC для нержавеющей стали
-
TDC
- QC_ для нержавеющей стали
-
QC
- QC_
- ZP_D для нержавеющей стали
-
ZP_D
- ZR_D для нержавеющей стали
-
ZR_D
- ZT_S для нержавеющей стали
-
ZT_S
- ZQMX для стали
-
ZQMX
- CTPA для нержавеющей стали
-
CTPA
- MGMN для чугуна
- MRMN для нержавеющей стали
- MRMN для чугуна
-
GEL-A/B
- GEL-A
-
GEL-A/B-R
-
GEL-C/D/E
- GEL-C
-
GEL-C/D/E-R
-
GER-A/B
- GER-A
-
GER-A/B-R
-
GER-C/D/E
-
GER-C/D/E-R
-
-
-
Пластины фрезерные
-
Пластины для свёрл
-
Лезвия для резьбофрез
-
Пластины со вставками PCBN
-
-
Фрезы
-
Метчики
-
Сверла
-
Ленточные пилы
-
Новое поступление (NEW!)
-
Державки токарные
-
Державки расточные
-
S...-SVJCR/S...-SVJCL
-
S...-DCLNR/S...-DCLNL
-
S...-DDUNR/S...-DDUNL
-
S...-DWLNR/S...-DWLNL
-
S...-MCKNR/S...-MCKNL
-
S...-MCLNR/S...-MCLNL
-
S...-MDQNR/S...-MDQNL
-
S...-MDUNR/S...-MDUNL
-
S...-MSKNR/S-...MSKNL
-
S...-MTJNR/S...-MTJNL
-
S...-MTQNR/S...-MTQNL
-
S...-MTUNR/S...-MTUNL
-
S...-MTFNR/S...-MTFNL
-
S...-MTWNR/S...-MTWNL
-
S...-MVQNR/S-...MVQNL
-
S...-MVUNR/S-...MVUNL
-
S...-MVWNR/S...-MVWNL
-
S...-MVXNR/S...-MVXNL
-
S...-MWLNR/S...-MWLNL
-
S...-PCLNR/S...-PCLNL
-
S...-PDSNR/S...-PDSNL
-
S...-PDUNR/S...-PDUNL
-
S...-PSKNR/S...-PSKNL
-
S...-PWLNR/S...-PWLNL
-
S...-PTFNR/S...-PTFNL
-
S...-SCKCR/S...-SCKCL
-
S...-SCLCR/S...-SCLCL
-
S...-SCLPR/S...-SCLPL
-
S...-SDQCR/S...-SDQCL
-
S...-SDUCR/S...-SDUCL
-
S...-SDZCR/S...-SDZCL
-
S...-SSSCR/S...-SSSCL
-
S...-SSKCR/S...-SSKCL
-
S...-STFCR/S-...STFCL
-
S...-STUCR/S-...STUCL
-
S...-SVUCR/S-...SVUCL
-
S...-SVUBR/S...-SVUBL
-
-
Державки проходные
-
CCLNR/CCLNL
-
CRDNN
-
CSDNN
-
CSKNR/CSKNL
-
CTJNR/CTJNL
-
DCBNR/DCBNL
-
DCKNR/DCKNL
-
DCLNR/DCLNL
-
DCMNN
-
DDJNR/DDJNL
-
DDPNN
-
DSSNR/DSSNL
-
DDQNR/DDQNL
-
DSBNR/DSBNL
-
DSDNN
-
DSKNR/DSKNL
-
DTFNR/DTFNL
-
DTGNR/DTGNL
-
DVJNR/DVJNL
-
DVVNN
-
DWLNR/DWLNL
-
ECLNR/ECLNL
-
EDJNR/EDJNL
-
EVJNR/EVJNL
-
EWLNR/EWLNL
-
MCBNR/MCBNL
-
MCKNR/MCKNL
-
MCLNR/MCLNL
-
MCMNN
-
MDJNR/MDJNL
-
MDPNN
-
MDQNR/MDQNL
-
MRDNN
-
MRGNR/MRGNL
-
MSBNR/MSBNL
-
MSDNN
-
MSKNR/MSKNL
-
MSSNR/MSSNL
-
MTENN
-
MTFNR/MTFNL
-
MTGNR/MTGNL
-
MTJNR/MTJNL
-
MTQNR/MTQNL
-
MVJNR/MVJNL
-
MVQNR/MVQNL
-
MVUNR/MVUNL
-
MVVNN
-
MWLNR/MWLNL
-
PWLNR/PWLNL
-
PCLNR/PCLNL
-
PDJNR/PDJNL
-
PRACR/PRACL
-
PRDCN
-
PCBNR/PCBNL
-
PRGCR/PRGCL
-
PSBNR/PSBNL
-
PSDNN
-
PSSNR/PSSNL
-
PTGNR/PTGNL
-
PTTNR/PTTNL
-
SCLCR/SCLCL
-
SDJCR/SDJCL
-
SDNCN
-
SRACR/SRACL
-
SRDCN
-
SSDCN
-
SSSCR/SSSCL
-
STFCR/STFCL
-
SVACR/SVACL
-
SVJBR/SVJBL
-
SVJCR/SVJCL
-
SVVBN
-
SVVCN
-
WTENN
-
WTJNR/WTJNL
-
WWLNR/WWLNL
-
PDNNR/PDNNL
-
SVHBR/SVHBL
-
PDNNN
-
PTFNR/PTFNL
-
SCACR/SCACL
-
SDACR/SDACL
-
SSBCR/SSBCL
-
SRGCR/SRGCL
-
SSKCR/SSKCL
-
STGCR/STGCL
-
SVABR/SVABL
-
SVQCR/SVQCL
-
SWACR/SWACL
-
WTQNR/WTQNL
-
-
Державки резьбовые
-
Державки отрезные, канавочные
-
Держатели отрезного лезвия
-
Лезвия отрезные
-
Мини-резцы твердосплавные
-
-
Оснастка для фрезерных станков
-
Фрезерные патроны
-
BT
-
BT-ER (для цанг ER)
-
BT-FMB (для насадных фрез)
-
BT-SCA (для дисковых фрез)
-
BT-D (тестовые оправки)
-
BT-SLN Weldon
-
BT-MTA (конус Морзе с лапкой)
-
BT-MTB (конус Морзе с резьбовым отверстием)
-
BT-DC (высокоскоростные патроны для цанг DC)
-
BT-APU
-
BT-SC (для цилиндрических цанг SC)
-
BT-GT (для резьбовых цанг GT12/24/42)
-
BT-TER (патроны с осевой компенсацией по длине для цанг ER)
-
BT-OZ(EOC) (для силовых цанг OZ)
-
BT-PHC (гидропластовые патроны)
-
-
Конус Морзе MTA/MTB
-
HSK
-
Цилиндрический хвостовик
-
NT
-
SK
-
SK-FMB (для насадных фрез)
-
SK-SLN (Weldon)
-
SK-TER (патроны с осевой компенсацией по длине для цанг ER)
-
SK-SC (для цилиндрических цанг SC)
-
SK-MTB (конус Морзе с резьбовым отверстием)
-
SK-MTA (конус Морзе с лапкой)
-
SK-ER (для цанг ER)
-
SK-GT (для резьбовых цанг GT12/24/42)
-
SK-OZ(EOC) (для силовых цанг OZ)
-
SK-APU (сверлильные быстрозажимные патроны)
-
SK-PHC (гидропластовые патроны)
-
-
-
Прихваты, прижимы, упоры
-
Цанги
-
Штревели
-
3D тестеры
-
Тиски станочные
-
Аксессуары и запчасти
- Силовые высокоточные VQC
-
640 Multitasking
-
Трехкулачковые NBK
-
Гидравлические DCV
-
Модульные двойные ZQ83
-
С регулируемым усилием зажима HPAC
-
Самоцентрирующиеся SC-I
-
Модульные GT
-
Глобусные HHY
-
Лекальные QGG
-
Лекальные QKG
-
Модульные составные ZQ84
-
Гидравлические CHV
-
Самоцентрирующиеся двойные SMC
-
-
Кромкоискатели
-
Магнитные плиты
-
Центроискатели
-
Гайки для цанг
-
Ключи гаечные
-
Приспособления для оправок
-
Наборы прижимов
-
Расточные системы
-
Система нулевого базирования
-
Магнитные захваты
-
Поворотные столы
-
Аксессуары для станочной оснастки
-
Привязка по оси Z
-
-
Оснастка для токарных станков
-
Кулачки токарные
- Инструментальные блоки BOT
-
Токарные патроны
-
Центры токарные вращающиеся
- Центры вращающиеся
- Центры вращающиеся усиленные M11
- Центры вращающиеся облегченные
- Центры вращающиеся со сменными вставками
- Центры вращающиеся высокоскоростные
- Центры вращающиеся с твердосплавной вставкой
- Центры вращающиеся с удлиненной вершиной
- Центры вращающиеся усиленные
- Центры вращающиеся высокоточные
- Центры вращающиеся грибковые
-
Держатели осевого инструмента
-
Переходные втулки
-
Приспособления для расточки кулачков
-
Инструментальные блоки BMT
-
Центры токарные упорные
-
Сухари для токарных патронов
-
Инструментальные блоки VDI
-
Патроны цанговые
-
Цанги токарные
-
-
Измерительный инструмент
-
Станки
-
Станки ленточные по металлу
-
Лазерные граверы (маркировщики) по металлу
-
Токарные станки
-
Фрезерные станки
-
Заточные станки
-
Резьбонарезные манипуляторы
-
Электроэрозионные станки
-
Промышленные роботы
-
-
Мерч CNC66
-
Проволока, СОЖ, запчасти для электроэрозионных станков
-
Промышленная мебель
-
Запасные части для державок, резцов и фрез
-
Развертки
-
Упаковка
-
Зенковки
-
Плашки
-
Инструмент для снятия заусенцев
- выгрузка
-
Корзина пуста
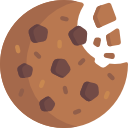
Мы используем файлы cookie для улучшения работы сайта и персонализации. Продолжая использовать сайт, вы соглашаетесь на сбор, обработку cookie-файлов и пользовательских данных с помощью Яндекс.Метрика, в соответствии с нашей Политикой конфиденциальности.